CW 3 / CW 5 (CWB 3)
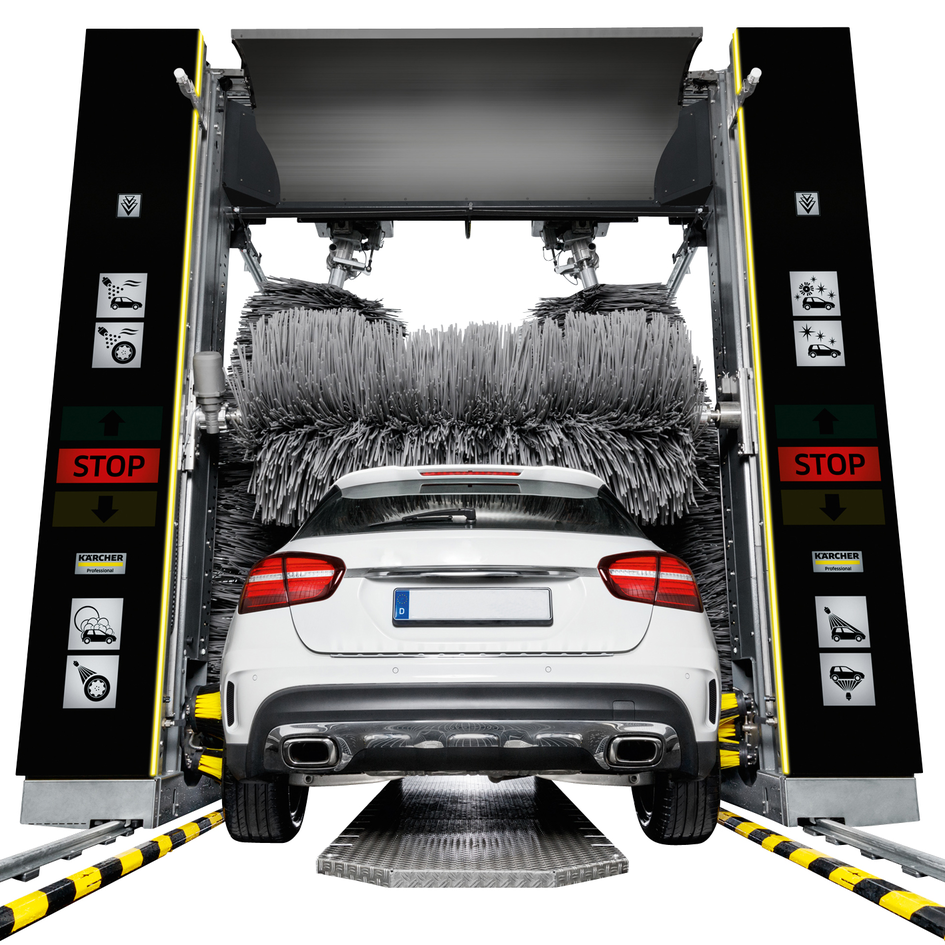
59687360 (12/22)
59687360 (12/22)
Read these original operating instructions and the safety instructions chapter before using the device for the first time. Act in accordance with them.
Keep them safe for future reference or for future owners.
The packing materials can be recycled. Please dispose of packaging in accordance with the environmental regulations.
Electrical and electronic devices contain valuable, recyclable materials and often components such as batteries, rechargeable batteries or oil, which - if handled or disposed of incorrectly - can pose a potential danger to human health and the environment. However, these components are required for the correct operation of the device. Devices marked by this symbol are not allowed to be disposed of together with the household rubbish.
Current information on content materials can be found at: www.kaercher.de/REACH
Dangers can be presented to the operator and other persons if the device is incorrectly operated or misused:
High water pressure
High electrical voltage
Compressed air
Detergent
To avoid danger to persons, animals and property, read the following documents before operating the system:
The operating instructions, including all safety instructions
The respectively applicable national regulations
The safety instructions provided with the detergent used
Ensure the following:
That you have understood all notes and instructions
That all users of the system are notified of the instructions and have understood them
All persons working on the erection, commissioning and operation of the system must:
Be appropriately qualified
Know and adhere to the operating instructions
Know and adhere to the applicable regulations
In self-service operation, ensure that clearly visible notices are present informing all users with regard to:
Potential dangers
Safety devices
Operating the system
The owner/operator of the washing bay is to create work instructions based on these operating instructions, the local conditions and the personnel conditions. The operating instructions are to be made available by providing copies or hanging signs with corresponding content in the workplace.
Indication of an imminent threat of danger that will lead to severe injuries or even death.
Indication of a potentially dangerous situation that may lead to severe injuries or even death.
Indication of a potentially dangerous situation that may lead to minor injuries.
Indication of a potentially dangerous situation that may lead to damage to property.
In the Federal Republic of Germany, the following regulations and guidelines apply to the operation of this system (available from Carl Heymanns Verlag KG, Luxemburger Straße 449, 50939 Cologne):
Accident prevention regulations "General regulations" BGV A1
Vehicle washing plant safety EN 17281
German work safety directive (BetrSichV)
Only persons familiar with the work, the operating instructions and the dangers associated with the system are permitted to operate, monitor, care for and inspect car wash systems.
Environmental pollution through vehicles
Escaping oils.
Protect the ground and dispose of old oil in an environmentally-friendly manner.
Do not allow gear oil and waste water containing mineral oil to enter the soil or waterways.
Treat the waste water before channelling it into the sewage system.
Observe the locally applicable statutory regulations and waste water treatment regulations.
In self-service systems, a person must always be available during operating periods, who is familiar with the washing bay and can take or initiate the measures necessary for preventing potential dangers in the case of a system malfunction.
Clearly visible instructions on the operation and intended use of the washing system must be provided at the washing bay for the users of the washing system.
The washing bay must always be shut down when performing maintenance and servicing work.
Risk of injury from machine movements
Switch the system off before performing maintenance and servicing work.
Secure the main switch with a padlock to prevent it from being switched on again.
Danger from substances in detergents that present a hazard to health
Observe the safety data sheets for the detergents used.
Adhere to the prescribed safety measures.
Wear the prescribed protective clothing such as safety goggles and protective gloves.
Increased risk of corrosion through the use of unsuitable cleaning agents
Do not use the following cleaning agents in the system:
Detergents intended for cleaning the washing hall.
Detergents intended for externally cleaning the washing bay.
Acidic cleaning agents.
Cleaning agents applied to the vehicle using a separate device (e.g. wheel cleaner).
Water treatment agents.
Danger through entering the portal washing station
Prohibit unauthorised persons from entering the portal washing station.
Erect suitable permanent signage indicating prohibited entry.
Risk of slipping on wet surfaces
Wear suitable shoes when entering the system and exercise care when walking.
Erect suitable permanent signage informing customers of the danger of slipping.
Danger through incorrect operation
Persons operating the system must:
Be instructed in the correct handling of the system,
Have provided verification of their ability to operate the system,
Be explicitly nominated to operate the system.
The operating instructions must be accessible to all operators.
The system may not be operated by persons under 18 years of age. This does not included supervised trainees of 16 years of age or more.
Risk of tripping over objects or supply lines lying on the ground
Remove all objects lying in the washing station before starting the system.
Risk of injury or damage due to the formation of ice in the system
Drain all water from the system if there is a danger of frost.
Keep all footpaths slip-free (e.g. floor heating, gravel).
The system is started via the control panel or via a wash card/code reader.
The occupants must leave the vehicle before washing.
Entering the system before washing has finished is prohibited.
Risk of injury from escaping compressed air, high-pressure water at nozzle outlets and propelled dirt particles or similar in the vicinity of the rotating brushes!
Dirt particles or loose objects can injure persons or animals when propelled off the vehicle.
Compressed air or high-pressure water can remain pressurised even when the system is switched off.
Keep the hall floor free of loose lying objects.
Exercise care when operating the compressed air system and the high-pressure system.
Wear suitable safety goggles when performing maintenance work.
Risk of explosion
Do not operate the system in the vicinity of potentially explosive spaces. Systems specifically designed for this, and labelled accordingly, are exempt from this stipulation
Do not use explosive or poisonous substances as cleaning agents, e.g.:
Petrol
Heating oil or diesel fuel
Solvents
Liquids containing solvents
Acids
Acetone
Contact the manufacturer if you are unsure.
The noises emitted by the system are not hazardous for the washing customers due to the short exposure time.
The sound level at the entry side during dry operation is 91 dB(A).
Risk of hearing damage to the operating personnel during drying mode
Hearing damage due to high volume in the machine room
Wear hearing protection during drying mode.
Wear suitable hearing protection when staying in the machine room.
Danger of electric shock
Never touch electrical components and cables with wet hands.
Ensure that the electrical connection cables or extension cable are not damaged by being driven over, crushed, yanked or similar.
Protect the cables from heat, oil and sharp edges.
Never point a water jet at electrical devices or systems.
Protect all live components in the work area from water jets.
Connect the system only to correctly earthed power sources.
Allow only qualified electricians to work on electrical components of the system.
Danger due to harmful substances
Be sure to observe the information and notes provided with the detergent.
Never drink water expelled from the system! The water is not of drinking water quality due to the added cleaning agents.
Observe the anti-bacterial regulations of the treatment system manufacturer when using processed water for operating the system.
Ensure that materials not normally present during exterior cleaning of vehicles (e.g. heavy metals, pesticide, radioactive materials, faeces or infectious materials) do not enter the washing bay.
Design measures are to be taken to ensure that uncontrolled restarting of the system after a power failure is impossible.
Observe the local waste water disposal regulations.
The corresponding instructions must be followed to ensure safe operation of the system and avoid dangers during maintenance, monitoring and inspection.
Maintenance work must be performed as specified by the manufacturer by a technically qualified person at the specified regular intervals. Observe the applicable regulations and safety requirement. Allow only qualified electricians to work on the electrical system.
Risk of injury from machine movements
Switch the system off before performing maintenance and servicing work.
Secure the main switch with a padlock to prevent it from being switched on again.
Risk of injury from pressurised compressed air reservoirs and lines after the system has been switched off
Depressurise the system before performing any work on the system.
Check the pressure gauge at the maintenance unit to ensure that the system is depressurised.
Risk of injury from the high-pressure system after the system has been switched off
Depressurise the high-pressure system before performing any work on the system.
This washing bay must be inspected by a technically qualified person to ensure a safe condition before initial commissioning and then at half-yearly intervals at the very least.
This inspection includes especially:
A visual inspection for all externally visible signs of wear and tear or damage
Function test
The completeness and effectiveness of all safety devices at self-service stations must be checked daily before the start or operations, or as required on monitored systems but always at least once a month.
Use only original manufacturer spare parts or parts recommended by the original manufacturer, otherwise all warranty claims will be invalidated.
Adhere to all safety instructions and application instructions provided with these parts.
This applies to:
Spare parts and wearing parts
Accessories
Operating materials
Detergent
The high-pressure pumps for the supply of the underbody washing unit and the high-pressure wash have the following safety devices.
The safety valve opens when the permissible operating pressure is exceeded and the water flows into the open.
This washing bay is exclusively intended for external cleaning of passenger vehicles with standard equipment and closed delivery vehicles.
Adherence to the intended use also includes:
Adherence to all information provided in these operating instructions.
Adherence to the inspection and maintenance instructions.
Risk of damage to vehicles when using the CareTouch brushes
Equip the system with a high pressure attachment kit or pre-wash the vehicles when using the CareTouch brushes.
To prevent damage to vehicles and the washing bay, only passenger vehicles and closed delivery vehicles conforming to the specified dimensional limits may be cleaned, see chapter Technical data.
A category 5 mains isolation must be installed between the system and the drinking water network to protect the drinking water network according to EN 1717.
The system must be erected by qualified technical personnel. The locally applicable safety regulations (e.g. clearances between the system and buildings) must be adhered to during erection.
Any type of improper use is prohibited.
The operating personnel are liable for hazards resulting from incorrect use. Usage for other purposes than those described in this documentation is prohibited.
Material damage to vehicles and the system if the vehicle dimensional limits are not adhered to
Adhere to the specified vehicle dimensional limits, see chapter Technical data.
The portal washing station is not suitable for cleaning:
Special passenger vehicles, e.g. vehicles with roof and alcove attachments projecting above the windscreen at the front or above the rear window at the rear
Construction machines
Vehicles with trailers
Two-wheel and three-wheel vehicles
Vehicles with double tyres / twin tyres
Pick-ups (optional)
Convertibles with an open roof
Convertibles with a closed roof but without manufacturer verification of washing system suitability
If these instructions are not followed, the system manufacturer accepts no liability for any resulting
personal injury,
material damage,
injuries to animals.
Increased risk of corrosion through the use of unsuitable cleaning agents
The following cleaning agents may not be used in the system:
Detergents intended for cleaning the washing hall.
Detergents intended for externally cleaning the washing bay.
Acidic cleaning agents.
Cleaning agents applied to the vehicle using a separate device (e.g. wheel cleaner).
Water treatment agents.
Only use original accessories and original spare parts. They ensure that the appliance will run fault-free and safely.
Information on accessories and spare parts can be found at www.kaercher.com.
The rotating side brushes clean the vehicle at the sides, front and rear.
The rotating roof brush removes dirt from the top of the vehicle.
The washing bay is equipped with two wheel washing units for thorough wheel cleaning. The position of the wheels is determined by a light sensor.
The rotating brushes are pressed against the wheel rim by pneumatic cylinders.
The brushes are watered by a nozzle mounted in the centre of each brush.
An optional height-adjustable wheel washing unit is available.
Processed water and fresh water is sprayed onto the vehicle by nozzles and spray arches.
Cleaning agents and care agents are mixed into the water according to the washing program.
A1 = Fresh water, chemical drying aid (CTH), wax
A2 = Processed water, shampoo
A3 = Polishing (optional, instead of C3)
B1 = Processed water, shampoo
B2 = Foam, insects, intensive Basic
C1 = Processed water, shampoo
C2 = Fresh water, chemical drying aid (CTH), wax
C3 = Polishing
G = Prespray wheel rims
L = Tar remover
K = Wheel gloss
H 2 = High pressure wheel wash
H 3 = High-pressure side nozzles
H4 = High-pressure roof nozzles
The cleaning agent for pre-cleaning is applied as a foam to extend the contact time.
The dirt traps retain particles that might clog the nozzles.
The dosing pumps mix cleaning and care agents into the water.
The air required for blowing the sides of the vehicle dry flows out of the drier nozzles.
The drier blower bars are moved along the contour of the vehicle. The air flow required for drying the vehicle is generated by integrated fans.
The positioning light has the following functions:
For positioning the vehicle before washing.
For indicating the exit direction after washing.
For indicating faults.
The light sensors provide the following information:
The position and contours of the vehicle.
The position of the vehicle wheels.
The cleaning and care agent canisters and dosing pumps are located in pillar 2.
A maximum of 8 canisters can be installed in pillar 2.
The supply can be optionally provided from the technical room if more canisters are required.
The suction hoses, canisters and dosing pumps are all labelled with the same colour Labelling of the dosing pumps.
Name | Description | Consumption | Order no. |
---|---|---|---|
RM 896 | Vehicle Pro Klear! RIM* | 15-25ml | 6.296-077.0 |
RM 890 | Vehicle Pro Klear! Prewash* | 10-14ml | 6.296-003.0 |
RM 891 | Vehicle Pro Klear! Brush* | 7-10ml | 6.295-995.0 |
RM 892 | Vehicle Pro Klear! Foam* | 8-10ml | 6.295-998.0 |
RM 893 | Vehicle Pro Klear! Dry* | 8-12ml | 6.296-001.0 |
RM 894 | Vehicle Pro Klear! Glow* | 10-15ml | 6.295-993.0 |
RM 837 | Vehicle Pro Klear! Plus** | 15ml | 6.295-779.0 |
* Container capacity 10 litres
* Container capacity 20 litres
The major device information is specified on the type plate.
The system control cabinet is located at the main supply distributor.
The main switch for the system is located on the main supply distributor.
The main supply distributor is located outside the washing bay, in the technical room or at suitable location in the vicinity of the washing bay.
0 = System off
1 = Operation via wash card reader
2 = Operation via wash card reader and control panel (display)
In the event of danger to persons, equipment or animals, the system must be switched off immediately by pressing the "EMERGENCY OFF" button.
"EMERGENCY OFF" buttons are located:
On the wash card/code reader.
On the control panel.
Optionally at the washing hall entrance if the control panel or wash card/code reader are not located at the entrance.
The washing bay is supplied with:
A control panel with display
A wash card/code reader (optional)
A mechanical retainer keeps the system on the guide rails, even in the case of incorrect behaviour by the washing customer.
A wash card reader or code reader is used for operating the washing bay in self-service mode.
The wash cards/codes required for operating the system are programmed on the respective system.
The process water connection allows rain water or recycled water to be used as a partial replacement for fresh water.
The planet wheel washing unit is equipped with 3 brushes instead of a circular broom.
The wheel washing units can be additionally equipped with a height adjustment mechanism.
The wheel wells and sills of the vehicle are cleaned by water jets from 2 additional nozzles per washing direction.
The vehicle underside can be washed with the underbody washing unit. For this, water is sprayed at high pressure over the entire underbody via two pivoting nozzle pipes.
Foam is applied to the front half of the vehicle by the prespraying nozzles. The foam is generated from water, prespraying agent and compressed air.
Pre-cleaning chemicals are applied to the vehicle by stationary nozzles.
The foam is generated from water, prespraying agent and compressed air.
Compressed air is used to spray a water-cleaning agent mixture onto the wheel rims via 2 stationary foam nozzles.
The high-pressure wash removes coarse dirt from the surface of the vehicle. High-pressure cleaning minimises the danger of scratching from sand grains or similar abrasives and makes a significant contribution to preserving the paintwork during cleaning.
Various different versions are available:
Working pressure 16 bar (1.6 MPa)
Working pressure 60 bar (6 MPa)
Working pressure 70 bar (7 MPa), on-board high-pressure pump (in the portal)
Foam wax is applied to the vehicle by the drying aid nozzles before the drying process.
Water mixed with wax is sprayed onto the vehicle via the cold wax nozzles. Two different types of cold wax (wax 1 and wax 2) can be selected.
The cleaning agent heater is located in the cleaning agent supply in pillar 2.
The washing bay can be equipped with a frost protection device:
If there is a danger of frost, the water is blown out of the piping system automatically.
This blowing process is controlled by a thermostat.
Demineralised water (from an on-site system or optionally available reverse osmosis system) or fresh water dosed with drying aid is sprayed onto the vehicle via the drying aid nozzles.
A compressed air foamed mixture of water and cleaning agent is sprayed onto the vehicle via 2 stationary nozzles. This is followed by a polishing procedure with the washing brushes.
Safety switches are required if the required safety clearances between the washing bay and permanent fixtures (e.g. walls, pillars, sinks) cannot be maintained. The safety switches prevent persons from being crushed between the system and the wall.
The washing bay stops immediately if a safety switch touches an obstacle.
If the system is stopped by a safety switch, determine the cause if this hand have the safety switch reset by an authorised technical specialist.
The splash guard protects the areas adjacent to the washing station from sprayed dirt and splash water emitted by the rotating side brushes.
The splash guard is attached to the outer surfaces of the chassis and suspension as well as the pillars.
The purpose of the bollard protection is to ensure central alignment of the vehicle. They prevent the vehicle from being parked too far away from the centre.
The Reset function allows the wash gantry to be moved to the iniial position remotely with a command via an interface. The function can be enabled via a separate parameter in the system control.
This function must only be enabled in countries or at locations where this function is permitted.
Video surveillance must be installed on site, covering the entire area of the washing hall or the entire travel path of the system, and any regulations applicable in the country/municipality where the system is installed must be applied.
The person who performs the remote reset must first ensure via the video surveillance that there are no persons in the travel path of the system. If a person then requests the command, that person must confirm that the system and its travel path are completely free by acknowledging a safety notice (e.g. pop-up window).
The person who integrates the system into his system, e.g. via the Internet, is responsible for the required security or cybersecurity and a risk assessment must be carried out on the system.
The on-site gate control is actuated by the passenger vehicle portal controller with the correct signals according to the washing sequence.
A distinction is made between summer gate control and winter gate control.
The gates are open before washing starts.
The vehicle can drive in.
The gates are closed when washing starts.
The gates are opened when washing ends and remain open.
The entry gate is closed before washing starts and must be opened to allow the vehicle to drive in. This is done by e.g. inserting a wash card into the wash card reader.
The gates are closed when washing starts (e.g. by pressing the "Start" button on the wash card reader).
The gates are opened when washing ends and are closed again after the vehicle has exited.
In the event of danger to persons, equipment or animals, the system must be switched off immediately by pressing the "EMERGENCY OFF" button.
"EMERGENCY OFF" buttons are located:
On the wash card/code reader.
On the control panel.
Optionally at the washing hall entrance if the control panel or wash card/code reader are not located at the entrance.
The main switch is located at the main supply distributor.
Set the main switch to "1" to switch the system on.
At the key switch on the main supply distributor, see Supply distributorcan be used for selecting the operating stations from which washing programs can be started.
Position 0: Programme start not possible
Position 1: Programme start possible at the wash card/code reader
Position 2: Programme start possible at the wash card/code reader and at the control panel
Depending on the version of the Wash card/code reader, the washing program can be selected as follows:
Entry via a keypad.
The program specified on the wash card.
Entry of a code number.
Further information is provided in the separate operating instructions for the wash card/code reader.
The cleaning and care agents are added to the water by the dosing pumps located in pillar 2.
The assignment of the dosing pumps is by way of example only. Dosing pumps 1-4 are assigned as shown in a standard system.
7 different cleaning and care agents can be selected for dosing pumps 5-8.
The dosing pumps add cleaning and care agents to the washing water according to the washing program and the equipment in the system.
The dosing quantities are adjusted optimally by the installation technician during initial commissioning. Changes to these settings are not usually necessary.
The positioning of the dosing pumps is system-dependent.
Dosing pump | Cleaning and care agents |
---|---|
![]() | Drying aid |
![]() | Shampoo |
![]() | Active foam |
![]() | Wax 1 |
![]() | Polish 1 |
![]() | Wheel cleaning |
![]() | Wax 2 |
![]() | Tyre gloss |
![]() | Insect pre-cleaning |
![]() | Polish 2 |
![]() | Intensive Basic |
Damage to the dosing pump due to dry running
Only adjust the dosing amount when the dosing pump is running.
Pull out the dosing amount adjustment knob.
Alternately press and release the ventilation button while turning the adjustment knob to the desired setting.
Release the ventilation button.
Press in the dosing amount adjustment knob.
The system compressed air supply must be in operation.
Turn the venting lever anticlockwise as far as it will go.
Set the dosing amount to 100%.
Press the ventilation button repeatedly until the detergent comes out of the venting line on the underside of the dosing pump without bubbles.
To set the dosing amount back to the desired value, see Adjusting the dosing amount.
Turn the venting lever clockwise as far as it will go.
The language is set during initial commissioning and can be changed via the Settings / General menu.
The display can be used for e.g. making system settings, making settings for the display and displaying system information.
The following symbols are shown on the display, depending on the current menu or status of the system
![]() | System ready for operation |
![]() | System malfunction |
![]() | Home button The Home button us used to navigate back to the previous menu from a submenu. |
![]() | Logged in with normal User access rights |
![]() | Logged in with Cleaning agent supplier access rights |
![]() | Logged in with Operator access rights |
![]() | Logged in with Service access rights |
![]() | Spring seasonal washing program set |
![]() | Summer seasonal washing program set |
![]() | Autumn seasonal washing program set |
![]() | Winter seasonal washing program set |
The Washing menu is used for selecting and starting programs and additional programs.
The currently running program can be interrupted and the progress in percent can be displayed.
Start washing program, see Start the program on the display.
The Service menu allows manual functions to be executed and the manual frost protection device to be started.
The Service menu contains the following submenus:
Manual mode (portal manual functions, manual starting of the frost protection device, manual water system functions)
Diagnostics (Operators and Service personnel only)
This calls up self-test functions for the system
The Settings menu contains the user management functions and allows system settings to be made.
The Settings menu contains the following submenus:
User administration
Wash program settings (pre-cleaning portal speed, brushes, care and drying, seasonal settings)
System (cleaning agent, water supply, gate operation, customer text priority display)
General (set date, time and opening times, select language, display system information)
This menu can be used for displaying system reports and showing the current filling levels of the cleaning agents.
The General Info menu contains the following submenus:
Wash counter (Operators only) - display of the completed and interrupted washes
Operating hours
Maintenance diagnostics - interval to the next servicing, system information, error memory, event memory
Cleaning agent filling levels - percentage filling levels of the cleaning agents (option)
The following push messages can be shown on the display when the system is in operation.
Danger from a critical fault
Switch the system off and notify the Service department.
Critical faults may only be corrected by persons trained in the system servicing tasks.
If multiple errors are present, these are displayed one after another.
You can switch between the displays using the arrow keys.
Malfunctions are errors occurring during the washing program. The washing program is interrupted and can be resumed after elimination of the malfunction.
If multiple malfunctions are present, these are displayed one after another.
You can switch between the displays using the arrow keys.
A detailed description of troubleshooting is provided in chapter Troubleshooting guide.
An event is an error occurring when no washing program is active.
If multiple events are present, these are displayed one after another.
You can switch between the displays using the arrow keys.
A detailed description of troubleshooting is provided in chapter Troubleshooting guide.
This message appears when one or more power units are not in their respective initial position.
Press and hold the button (> 2 seconds) or press and hold the blue button (> 2 seconds) to move the system to the initial position.
This message appears when a service date is due.
Contact the Service to arrange a servicing appointment.
Open the stop valves for water and compressed air.
Set the main switch at the main supply distributor to "1".
Press the blue control voltage/initial position button on the control panel.
System ready for operation. The vehicle to be washed can now be driven in.
Danger from moving system components
Switch the system off immediately using the emergency off button in the case of danger to persons, property or animals.
Risk of damage to the vehicles through inadequately removed cleaning agent
If a malfunction occurs in the washing bay after application of the cleaning agent, you must remove the cleaning agents by spraying thoroughly with water after switching off the system to prevent paint damage due to an excessively long cleaning agent exposure time.
In self-service systems, a person must always be available during operating periods who is familiar with the washing system and can take or initiate the measures necessary for preventing potential dangers.
Correct the reason for actuating the emergency off button before switching the system on again.
Persons or animals must not be present in the work area. Any vehicles present must be driven out of the system.
Unlock the emergency off button by pulling it.
Press the blue control voltage/initial position button on the control panel.
In the initial position, the upper green "Forwards" lamp on the positioning light lights up. The system is now ready for operation, the vehicle to be washed can now be driven in.
Select Settings/User Administration in the main menu.
The available users are displayed.
Select the desired user.
The dialogue for entering the code opens.
Enter and confirm the code.
The symbol for the currently logged-in user is displayed in the top line.
The user level switches automatically back to the normal User level after 30 minutes of inactivity.
Damage to the system and the vehicle
To prevent damage to the vehicle, take care to ensure that the following measures are taken before starting the system.
Close all windows, doors and sunroofs.
Push in the antennas, fold them in towards the rear or remove them.
Fold in any large or wide projecting mirrors.
Check the vehicle for any loose vehicle parts and remove these, e.g.:
Trim strips
Spoiler
Bumpers
Door handles
Exhaust pipes
Wind deflectors
Tarpaulin ropes
Rubber seals
Externally mounted sun visors
Luggage racks
The positioning light assists the customer in positioning the vehicle correctly.
Position the vehicle straight ahead and centrally between the guide rails.
Shut down the engine.
Engage one gear.
With an automatic transmission, select "P".
Apply the handbrake.
Check that all instructions from Preparing the vehicle have been followed.
Exit the vehicle (all persons).
Start the washing programme depending on the start type.
Operation with a wash card/code reader is described in the separate operating instructions for the wash card/code reader.
Press the "Wash" button.
Select the desired washing program.
Select the desired options and confirm with "OK".
Start the washing program.
The following manual functions can be executed via the display while a washing program is running:
Lock/raise dryer
Lock/raise roof brush
Lock/outwards movement of the side brushes
Stop the wheel brushes
Press the "Information" button to show the program progress display.
Press the "Stop" button.
The program is interrupted.
Press the "Start" button to resume the program.
After the programme has finished, the positioning light indicates whether the vehicle should be driven forwards or backwards out of the system.
Drive the vehicle out of the system.
Manual functions can be performed with the following assemblies:
Portal - move
Roof brush - raise and lower, switch on and off
Side brushes - move in and out, switch on and off
Dryer - raise and lower, switch on and off
Wheel brushes - move in and out, switch on and off
Select Service / Manual mode / Manual portal in the main menu.
The menu with executable manual functions opens.
Select the desired assembly.
The executable manual functions are shown in yellow.
Start the manual function.
The selected assembly must be deselected before selecting another assembly.
Danger due to chemicals
Observe the safety data sheets for the cleaning and care agents used.
Press the "General Infos" and "Cleaning agent filling levels" buttons on the display to display the filling levels", see General Infos.
The filling level display is an optional extra.
Screw the refill canister onto the overflow pipe.
Open the corresponding cleaning or care agent container.
Fill the reservoir and close it again.
End a currently running washing programme.
Leave the main switch set to "1" so that the optional frost protection device can remain activated.
End a currently running washing programme.
Drain all water lines if frost is to be expected during the shutdown period.
Set the main switch to "0".
Close the water supply line.
Close the compressed-air supply line.
Remove the detergent and care agents.
Damage to the system if the frost protection device is not switched on
If frost is to be expected, take care to ensure that the main power switch is switched on and no emergency stop buttons are actuated.
The following steps are performed automatically when the temperature falls below the minimum temperature:
The currently running washing program is executed until finished.
After the washing program has finished, the hoses and nozzle pipes of the portal are blown out with compressed air.
Starting of further washing programs is locked out.
The system is automatically ready for operation after the danger of frost has passed
Damage to the system through temperatures below zero
Execute the frost protection process for the system.
In systems with an automatic frost protection unit, the frost protection starts as soon as the preset temperature is reached.
Select Service / Manual mode in the main menu.
Press the "Manual frost protection" button to start the frost protection process.
The frost protection process starts and the time remaining is shown in the display.
Regular maintenance according to the following maintenance plan is fundamental for a safely operating system.
Risk of injury from machine movements
Switch the system off before performing maintenance and servicing work.
Secure the main switch with a padlock to prevent it from being switched on again.
Risk of injury from pressurised compressed air reservoirs and lines after the system has been switched off
Depressurise the system before performing any work on the system.
Check the pressure gauge at the maintenance unit to ensure that the system is depressurised.
Risk of injury from the high-pressure system after the system has been switched off
Depressurise the high-pressure system before performing any work on the system.
Risk of injury from escaping compressed air, high-pressure water at nozzle outlets and propelled dirt particles or similar in the vicinity of the rotating brushes!
Dirt particles or loose objects can injure persons or animals when propelled off the vehicle.
Compressed air or high-pressure water can remain pressurised even when the system is switched off.
Keep the hall floor free of loose lying objects.
Exercise care when operating the compressed air system and the high-pressure system.
Wear suitable safety goggles when performing maintenance work.
Who is permitted to perform inspection, maintenance and servicing work?
Work labelled with "Operator" may only be performed by instructed persons who are capable of safely operating and maintaining the system.
Work labelled with "Customer service" may only be performed by Kärcher customer service technicians or Kärcher-authorised installation technicians.
We recommend that you close a service contract to ensure reliable operation of the system. Please contact your KÄRCHER customer service department responsible.
For you own safety and the safety of others, the system should be switched off when performing maintenance and servicing work. Since not all system components requiring maintenance are freely accessible, some system components must be moved during maintenance and servicing work. The "Manual mode" operating mode is provided for this.
The manual mode is executed on the display.
Risk of injury
Take care to ensure that you perform the following work steps only in the specified sequence.
Risk of damage due to Manual mode
Do not use the Manual mode for washing vehicles.
Drive any vehicle present out of the system.
Ensure that no persons or animals are present in the system.
Switch on the system.
Select manual mode on the display.
Move the system components.
Switch off the system and secure it against being switched on again.
Perform the maintenance and servicing work.
Assembly | Activity | Performed | Target group |
---|---|---|---|
Emergency off button Safety switch | Check | Start the washing program, actuate an emergency-off button or safety switch, the system must stop immediately, then switch the system on again, see chapter “Switching on again after an emergency off”. | Operator |
Signs with operating instructions and intended use | Check the instructions for self-service customers (self-service systems only) | Check all signs for completeness and legibility. Replace any damaged signs. | Operator |
Cleaning and care agent reservoirs | Check the filling level | Refill or replace as necessary. | Operator |
High-pressure hoses from the high-pressure pump to the washing bay | Check | Check the hoses for damage. Replace faulty hoses immediately. Danger of accident. | Operator |
Spray nozzles/sieves | Checking for clogging | Visual inspection (assess the spray pattern), clean if necessary. | Operator |
Eliminate clogging | Warning, do not swap over the nozzles. Unscrew nozzles individually to avoid mixing them up. Clean with compressed air or insert in a detergent solution and then clean with a brush or needle. Screw in the nozzles again. | Operator | |
Light sensors | Check for soiling, clean if necessary | For light soiling, wipe the light sensors with a damp cloth without detergent under light pressure. In the event of heavy soiling, spray the cloth with a gentle detergent. | Operator |
Limits switches | Visual inspection | Check for mechanical damage and firm seating. | Operator |
Side brushes, roof brush, wheel brushes | Check for foreign bodies | Visual inspection, remove any foreign bodies, clean dirty brushes with a high-pressure cleaner. | Operator |
Rinsing and spray circuits | Check the water supply | In washing mode, check that sufficient water for vehicle washing is available. Too little water of no water can damage the vehicle being washed. | Operator |
Positioning light | Function test | Interrupt the “Position 1” and “Position 2” light sensors, for the position of the light sensors see chapter “Front maintenance overview”. The positioning light must display corresponding signals. | Operator |
Assembly | Activity | Rectification | Target group |
---|---|---|---|
Roof brush rollers Side brush rollers | Visual inspection | Check the true running of the brush shaft. Check the brushes for tight seating. Check the brush for wear and tear. Minimum bristle length = as-new length minus 50 mm Replace the brushes if necessary. | Operator |
Supply line hoses and pipeline | Visual inspection | Check for leaks. | Operator Customer Service |
High-pressure pump(s) | Checking for leaks | Check pump and line system for leaks. Notify Customer Service if you lose oil or if there is a leak of more than 10 drops of water per minute. | Operator |
Checking the oil level | Target level in the middle of the oil level indicator. Top up with oil if necessary (order no. 6.288-020.0) and inform Customer Service immediately. | Operator | |
Check pressure tank | If there is increased vibration in the high-pressure pump, the pressure tank is defective. Contact Customer Service. | Operator Customer Service | |
Fresh water tank | Check the float switch | Check the function of the float valve (see "Maintenance work"). | Operator |
Operating station with display | Cleaning/Care | Wipe the surface with a damp cloth, spray the cloth with a detergent and clean it if heavily soiled | Operator |
Panel/glass front system | Cleaning | Spray the surface with an acidic cleaner and clean with a soft pad, then rinse with clean water and remove with a squeegee | Operator |
Assembly | Activity | Performed | Target group |
---|---|---|---|
Check the running rollers of the side brush rollers | Visual inspection | Check the play by moving the side brushes. Contact Customer Service in the case of excessive play between the carriage and guide. | Operator Customer Service |
Screws on the guide rails for the roof brush and roof drier | Re-tighten | Check for tight seating of the screws and tighten if necessary. Tightening torque 25 Nm | Operator Customer Service |
Assembly | Activity | Rectification | Target group |
---|---|---|---|
Maintenance unit | Cleaning the filter | Shut off the compressed air supply and then extend and retract the wheel washing unit in manual mode until the system is depressurised. Check the pressure gauge to ensure that the system is completely depressurised. Unscrew the filter housing, remove the filter insert, clean the filter with compressed air, fit the filter, screw the cover on again. | Operator |
Processed water and fresh water dirt trap | Cleaning | Shut off the water supply, unscrew the cover of the dirt trap, remove the filter, flush the filter with water, fit the filter again, screw on the cover. | Operator |
Pressure reducer | Cleaning the sieve | See "Maintenance work". | Operator |
Roof brush and roof drier | Visual inspection of the drive belts | Check the condition of the drive belts and replace if necessary. | Customer Service |
All limit switches | Check the fasteners and clearances4 | Check the clearance between the limit switch and switching vane using a feeler gauge. If necessary, adjust the limit switches by adjusting the plastic nuts. Limit switch clearances:
| Customer Service |
Washing hall | Cleaning | Spray the surfaces such as floor, walls and tiles with an acidic detergent, allow to take effect, clean off the detergent with a soft pad (white) | Operator |
Assembly | Activity | Rectification | Target group |
---|---|---|---|
Cables and hoses for:
| Visual inspection | Condition of the hoses and cables. Check the hoses and connecting elements for leaks. | Operator |
Side brushes, roof brush, wheel brushes | Basic cleaning | Spray the brushes with a detergent (pre-cleaner or hall cleaner), allow to act and rinse thoroughly with high-pressure cleaner and warm water at max. 40 °C | Operator |
Assembly | Activity | Rectification | Target group |
---|---|---|---|
Self-service gantry | Check the toothed rack for wear and tear | Operator Customer Service | |
Wheel washing brushes | Visual inspection | Replace the brushes after approx. 15000 washes. Replacing the wheel washing brushes: Remove the screws inside the brush ring, remove the wheel washing brush, fit the new wheel washing brush and fasten in place with the screws. | Operator Customer Service |
High-pressure unit | Safety check | Carry out a safety check according to the guidelines for liquid emitters. | Expert customer service |
Close the water inlet.
Unscrew the cover.
Take out the strainer and rinse it with water.
Insert the sieve into the pressure reducer. Ensure that the seals are seated properly.
Screw in and tighten the cover.
Check whether water comes out from the overflow opening.
Remove the fresh water tank cap.
Check whether the float valve closes completely when the fresh water is full.
When the float valve is completely closed, no water comes out of the outlet.
Replace the cover.
Risk of injury from machine movements
Switch the system off before performing maintenance and servicing work.
Secure the main switch with a padlock to prevent it from being switched on again.
Risk of injury from pressurised compressed air reservoirs and lines after the system has been switched off
Depressurise the system before performing any work on the system.
Check the pressure gauge at the maintenance unit to ensure that the system is depressurised.
Risk of injury from the high-pressure system after the system has been switched off
Depressurise the high-pressure system before performing any work on the system.
Who is permitted to eliminate faults?
Work labelled with "Operator" may only be performed by instructed persons who are capable of safely operating and maintaining the system.
Qualified electricians are persons with professional electrotechnical training and qualifications.
Work labelled with "Customer service" may only be performed by Kärcher customer service technicians or Kärcher-authorised installation technicians.
The faults, causes and remedies are shown in plain text on the display.
Eliminate the malfunction according to the message on the display and then acknowledge via the OK button.
Inadequate cleaning efficiency
Cause:
No cleaning agent or insufficient cleaning agent
Cause:
No air pressure or insufficient air pressure in the supply line
Cause:
Worn brushes
Remedy:
Operator
Check the cleaning agent filling level and refill if necessary, vent the dosing pump.
Check the air pressure and adjust if necessary (0.6 MPa (6 bar) at the maintenance unit pressure gauge).
Clean the cleaning agent intake filter, check the cleaning agent pipes for damage.
Check the brushes and replace if necessary.
High-pressure pump does not reach pressure
Cause:
Suction-side pipeline system leaking.
Cause:
Water shortage
Remedy:
Operator, Customer Service
Check the screw connections and hoses.
Eliminate water shortage.
The pressure gauge pointer of the high-pressure pump vibrates strongly
Cause:
Pump sucking air
Cause:
Pressure tank defective
Remedy:
Customer Service
Check suction line.
Replace pressure tank.
The high-pressure pump safety valve opens
Cause:
Clogged washing bay nozzles
Remedy:
Operator
Check, clean, replace nozzles.
Cause:
Hose or high-pressure valves clogged
Remedy:
Customer Service
Remove clog.
Too little water or no water coming out of the nozzles
Cause:
Dirt trap clogged
Cause:
Insufficient water pressure
Cause:
Nozzle clogged
Cause:
Air in the centrifugal pump
Cause:
Solenoid valve or supply line clogged
Remedy:
Operator
Clean the dirt trap
Check the water supply pressure and pumps
Clean the nozzles with compressed air
Venting the centrifugal pump by loosening the bleed screw
Check the solenoid valves and supply lines (water and electricity) and repair if necessary
Water continues coming out of the nozzles after washing
Cause:
Dirty solenoid valve
Remedy:
Customer Service
Clean the solenoid valves
Inadequate drying
Cause:
Too little or too much drying aid
Cause:
Incorrect drying aid
Cause:
No air pressure or inadequate air pressure
Remedy:
Operator
Increase or reduce the dosage
Check the cleaning agent filling level
Clean the intake filter
Vent the dosing pump
Use original drying aid from Kärcher
Check that the drying blower is working correctly
The wheel washing brush does not rotate
Cause:
The motor circuit breaker in the control cabinet has triggered
Cause:
Contact pressure too high
Remedy:
Operator
Check the motor circuit breaker in the control cabinet
Reduce the contact pressure at the wheel wash pressure reducer
The wheel washing brush extends slowly or not at all
Cause:
No air pressure or inadequate air pressure
Remedy:
Operator, Customer Service
Check the air pressure and adjust if necessary
Increase the contact pressure at the wheel wash pressure reducer
The wheel washing brush extends at the wrong position
Cause:
Dirty light sensors
Remedy:
Operator
Clean the light sensors and check the settings if necessary
The brushes become dirty quickly
Cause:
Shampoo dosage too low
Remedy:
Operator
Adjust the shampoo dosage
Check the water volume and adjust if necessary
The undercarriage wash nozzle pipes pivot too slowly/too quickly or not at all
Cause:
No air pressure or inadequate air pressure
Cause:
Pivoting unit heavily soiled
Cause:
Chokes incorrectly adjusted
Remedy:
Operator, Customer Service
Check the air pressure in the supply line and adjust if necessary
Clean the pivoting unit
Re-adjust the chokes
The system cannot be switched on
Cause:
Power supply fault
Remedy:
Operator, qualified electrician
Ensure a fault-free power supply as specified in the connection values
Display | Blink code | Cause | Remedy |
---|---|---|---|
![]() | Blinking alternately | Manual mode active | Message |
![]() | lights up | Washing is running | Message |
![]() | lights up | Washing stopped | Message |
![]() | Blinking alternately | Error active | Correct the error |
![]() | Blinking briefly | Emergency-off active | Determine the cause and unlock the emergency-off button |
![]() | lights up | Move into position | Drive the vehicle into position |
![]() | lights up | Stop positioning | Stop the vehicle |
![]() | lights up | Reverse the positioning | Reverse the vehicle |
![]() | Blinking | Washing finished | Drive the vehicle out forwards |
![]() | Blinking | Washing finished | Drive the vehicle out backwards |
Inadequate cleaning efficiency
Cause:
No cleaning agent or insufficient cleaning agent
Cause:
No air pressure or insufficient air pressure in the supply line
Cause:
Worn brushes
Remedy:
Operator
Check the cleaning agent filling level and refill if necessary, vent the dosing pump.
Check the air pressure and adjust if necessary (0.6 MPa (6 bar) at the maintenance unit pressure gauge).
Clean the cleaning agent intake filter, check the cleaning agent pipes for damage.
Check the brushes and replace if necessary.
High-pressure pump does not reach pressure
Cause:
Suction-side pipeline system leaking.
Cause:
Water shortage
Remedy:
Operator, Customer Service
Check the screw connections and hoses.
Eliminate water shortage.
The pressure gauge pointer of the high-pressure pump vibrates strongly
Cause:
Pump sucking air
Cause:
Pressure tank defective
Remedy:
Customer Service
Check suction line.
Replace pressure tank.
The high-pressure pump safety valve opens
Cause:
Clogged washing bay nozzles
Remedy:
Operator
Check, clean, replace nozzles.
Cause:
Hose or high-pressure valves clogged
Remedy:
Customer Service
Remove clog.
Too little water or no water coming out of the nozzles
Cause:
Dirt trap clogged
Cause:
Insufficient water pressure
Cause:
Nozzle clogged
Cause:
Air in the centrifugal pump
Cause:
Solenoid valve or supply line clogged
Remedy:
Operator
Clean the dirt trap
Check the water supply pressure and pumps
Clean the nozzles with compressed air
Venting the centrifugal pump by loosening the bleed screw
Check the solenoid valves and supply lines (water and electricity) and repair if necessary
Water continues coming out of the nozzles after washing
Cause:
Dirty solenoid valve
Remedy:
Customer Service
Clean the solenoid valves
Inadequate drying
Cause:
Too little or too much drying aid
Cause:
Incorrect drying aid
Cause:
No air pressure or inadequate air pressure
Remedy:
Operator
Increase or reduce the dosage
Check the cleaning agent filling level
Clean the intake filter
Vent the dosing pump
Use original drying aid from Kärcher
Check that the drying blower is working correctly
The wheel washing brush does not rotate
Cause:
The motor circuit breaker in the control cabinet has triggered
Cause:
Contact pressure too high
Remedy:
Operator
Check the motor circuit breaker in the control cabinet
Reduce the contact pressure at the wheel wash pressure reducer
The wheel washing brush extends slowly or not at all
Cause:
No air pressure or inadequate air pressure
Remedy:
Operator, Customer Service
Check the air pressure and adjust if necessary
Increase the contact pressure at the wheel wash pressure reducer
The wheel washing brush extends at the wrong position
Cause:
Dirty light sensors
Remedy:
Operator
Clean the light sensors and check the settings if necessary
The brushes become dirty quickly
Cause:
Shampoo dosage too low
Remedy:
Operator
Adjust the shampoo dosage
Check the water volume and adjust if necessary
The undercarriage wash nozzle pipes pivot too slowly/too quickly or not at all
Cause:
No air pressure or inadequate air pressure
Cause:
Pivoting unit heavily soiled
Cause:
Chokes incorrectly adjusted
Remedy:
Operator, Customer Service
Check the air pressure in the supply line and adjust if necessary
Clean the pivoting unit
Re-adjust the chokes
The system cannot be switched on
Cause:
Power supply fault
Remedy:
Operator, qualified electrician
Ensure a fault-free power supply as specified in the connection values
Inadequate cleaning efficiency
Cause:
No cleaning agent or insufficient cleaning agent
Cause:
No air pressure or insufficient air pressure in the supply line
Cause:
Worn brushes
Remedy:
Operator
Check the cleaning agent filling level and refill if necessary, vent the dosing pump.
Check the air pressure and adjust if necessary (0.6 MPa (6 bar) at the maintenance unit pressure gauge).
Clean the cleaning agent intake filter, check the cleaning agent pipes for damage.
Check the brushes and replace if necessary.
High-pressure pump does not reach pressure
Cause:
Suction-side pipeline system leaking.
Cause:
Water shortage
Remedy:
Operator, Customer Service
Check the screw connections and hoses.
Eliminate water shortage.
The pressure gauge pointer of the high-pressure pump vibrates strongly
Cause:
Pump sucking air
Cause:
Pressure tank defective
Remedy:
Customer Service
Check suction line.
Replace pressure tank.
The high-pressure pump safety valve opens
Cause:
Clogged washing bay nozzles
Remedy:
Operator
Check, clean, replace nozzles.
Cause:
Hose or high-pressure valves clogged
Remedy:
Customer Service
Remove clog.
Too little water or no water coming out of the nozzles
Cause:
Dirt trap clogged
Cause:
Insufficient water pressure
Cause:
Nozzle clogged
Cause:
Air in the centrifugal pump
Cause:
Solenoid valve or supply line clogged
Remedy:
Operator
Clean the dirt trap
Check the water supply pressure and pumps
Clean the nozzles with compressed air
Venting the centrifugal pump by loosening the bleed screw
Check the solenoid valves and supply lines (water and electricity) and repair if necessary
Water continues coming out of the nozzles after washing
Cause:
Dirty solenoid valve
Remedy:
Customer Service
Clean the solenoid valves
Inadequate drying
Cause:
Too little or too much drying aid
Cause:
Incorrect drying aid
Cause:
No air pressure or inadequate air pressure
Remedy:
Operator
Increase or reduce the dosage
Check the cleaning agent filling level
Clean the intake filter
Vent the dosing pump
Use original drying aid from Kärcher
Check that the drying blower is working correctly
The wheel washing brush does not rotate
Cause:
The motor circuit breaker in the control cabinet has triggered
Cause:
Contact pressure too high
Remedy:
Operator
Check the motor circuit breaker in the control cabinet
Reduce the contact pressure at the wheel wash pressure reducer
The wheel washing brush extends slowly or not at all
Cause:
No air pressure or inadequate air pressure
Remedy:
Operator, Customer Service
Check the air pressure and adjust if necessary
Increase the contact pressure at the wheel wash pressure reducer
The wheel washing brush extends at the wrong position
Cause:
Dirty light sensors
Remedy:
Operator
Clean the light sensors and check the settings if necessary
The brushes become dirty quickly
Cause:
Shampoo dosage too low
Remedy:
Operator
Adjust the shampoo dosage
Check the water volume and adjust if necessary
The undercarriage wash nozzle pipes pivot too slowly/too quickly or not at all
Cause:
No air pressure or inadequate air pressure
Cause:
Pivoting unit heavily soiled
Cause:
Chokes incorrectly adjusted
Remedy:
Operator, Customer Service
Check the air pressure in the supply line and adjust if necessary
Clean the pivoting unit
Re-adjust the chokes
The system cannot be switched on
Cause:
Power supply fault
Remedy:
Operator, qualified electrician
Ensure a fault-free power supply as specified in the connection values
Loosen the bleed screw.
If water comes out, screw the bleed screw in again.
The warranty conditions issued by our sales company responsible apply in all countries. We shall remedy possible malfunctions on your device within the warranty period free of cost, provided that a material or manufacturing defect is the cause. In a warranty case, please contact your dealer (with the purchase receipt) or the next authorised customer service site.
You can find more detailed information at: www.kaercher.com/dealersearch
Plant dimensions | |
Washing height | 2100, 2200, 2300 mm |
Frame height | 2900 mm |
Total height | 2930, 3030, 3130 mm |
Frame width | 3500 mm |
Total width of side brushes | 4040 mm |
Total width of splash guard | 4060 mm |
Frame depth/depth with rotating brushes | 1600 / 2170 mm |
Total length of short hall | 2070 mm |
System width at mirror height | 2450 mm |
System width in the wheel wash region | 2100 mm |
Track width of guide rails | 2550, 2700, 2800 mm |
Hall width with safety clearance | 4500 mm |
Washing brushes | |
Side brush diameter | 975 mm |
Side brush rotary speed | 107 1/min |
Roof brush diameter | 975 mm |
Roof brush rotary speed | 127 1/min |
Portal speed | 0 - 24 m/min |
Electrical connection | |
Mains voltage | 400 V |
Frequency | 50 Hz |
Power rating | 10-16 kW |
Controller maximum supply fuse | 35-50 A |
Water connection | |
Nominal width | 1 Inches |
Flow pressure as per DIN 1988 (at 100 l/min) | 0,4 - 0,6 MPa |
Max. temperature | 50 °C |
Compressed air connection | |
Nominal width | 1/2 Inches |
Pressure | 0,6 - 0,8 MPa |
Consumption/washing (without frost protection device, program-dependent at a vehicle length of 4.5 m) | 50 l |
Consumption with without frost protection, approx. | 700 l |
Determined values in acc. with EN 60335-2-79 | |
Sound level, washing process with drying | 87 dB(A) |
Sound level, drying mode only | 91 dB(A) |
Sound level, high pressure module | 86 dB(A) |
Sound power, washing process with drying | 101 dB(A) |
Sound power, drying mode only | 105 dB(A) |
Sound power, high-pressure module | 101 dB(A) |
Uncertainty | 3 dB(A) |
Plant dimensions | |
Washing height | 2400, 2500, 2600 mm |
Frame height | 3200 mm |
Total height | 3230, 3330, 3430 mm |
Frame width | 3500 mm |
Total width of side brushes | 4040 mm |
Total width of splash guard | 4060 mm |
Frame depth/depth with rotating brushes | 1600 / 2170 mm |
Total length of short hall | 2070 mm |
System width at mirror height | 2450 mm |
System width in the wheel wash region | 2100 mm |
Track width of guide rails | 2550, 2700, 2800 mm |
Hall width with safety clearance | 4500 mm |
Washing brushes | |
Side brush diameter | 975 mm |
Side brush rotary speed | 107 1/min |
Roof brush diameter | 975 mm |
Roof brush rotary speed | 127 1/min |
Portal speed | 0 - 24 m/min |
Electrical connection | |
Mains voltage | 400 V |
Frequency | 50 Hz |
Power rating | 10-16 kW |
Controller maximum supply fuse | 35-50 A |
Water connection | |
Nominal width | 1 Inches |
Flow pressure as per DIN 1988 (at 100 l/min) | 0,4 - 0,6 MPa |
Max. temperature | 50 °C |
Compressed air connection | |
Nominal width | 1/2 Inches |
Pressure | 0,6 - 0,8 MPa |
Consumption/washing (without frost protection device, program-dependent at a vehicle length of 4.5 m) | 50 l |
Consumption with without frost protection, approx. | 700 l |
Determined values in acc. with EN 60335-2-79 | |
Sound level, washing process with drying | 87 dB(A) |
Sound level, drying mode only | 91 dB(A) |
Sound level, high pressure module | 86 dB(A) |
Sound power, washing process with drying | 101 dB(A) |
Sound power, drying mode only | 105 dB(A) |
Sound power, high-pressure module | 101 dB(A) |
Uncertainty | 3 dB(A) |
Plant dimensions | |
Washing height | 2700, 2800, 2900 mm |
Frame height | 3500 mm |
Total height | 3530, 3630, 3730 mm |
Frame width | 3500 mm |
Total width of side brushes | 4040 mm |
Total width of splash guard | 4060 mm |
Frame depth/depth with rotating brushes | 1600 / 2170 mm |
Total length of short hall | 2070 mm |
System width at mirror height | 2450 mm |
System width in the wheel wash region | 2100 mm |
Track width of guide rails | 2550, 2700, 2800 mm |
Hall width with safety clearance | 4500 mm |
Washing brushes | |
Side brush diameter | 975 mm |
Side brush rotary speed | 107 1/min |
Roof brush diameter | 975 mm |
Roof brush rotary speed | 127 1/min |
Portal speed | 0 - 24 m/min |
Electrical connection | |
Mains voltage | 400 V |
Frequency | 50 Hz |
Power rating | 10-16 kW |
Controller maximum supply fuse | 35-50 A |
Water connection | |
Nominal width | 1 Inches |
Flow pressure as per DIN 1988 (at 100 l/min) | 0,4 - 0,6 MPa |
Max. temperature | 50 °C |
Compressed air connection | |
Nominal width | 1/2 Inches |
Pressure | 0,6 - 0,8 MPa |
Consumption/washing (without frost protection device, program-dependent at a vehicle length of 4.5 m) | 50 l |
Consumption with without frost protection, approx. | 700 l |
Determined values in acc. with EN 60335-2-79 | |
Sound level, washing process with drying | 87 dB(A) |
Sound level, drying mode only | 91 dB(A) |
Sound level, high pressure module | 86 dB(A) |
Sound power, washing process with drying | 101 dB(A) |
Sound power, drying mode only | 105 dB(A) |
Sound power, high-pressure module | 101 dB(A) |
Uncertainty | 3 dB(A) |
The water consumption depends on the vehicle length, system equipment and washing program.
The specified values are by way of example for the consumption per vehicle wash.
Boundary conditions:
Vehicle length 4.5 m
We hereby declare that the machine described below complies with the relevant basic safety and health requirements in the EU Directives, both in its basic design and construction as well as in the version placed in circulation by us. This declaration is invalidated by any changes made to the machine that are not approved by us.
Product: Washing bay
Type: 1.534-xxx
Currently applicable EU Directives2006/42/EC (+2009/127/EC)
2014/30/EU
2009/125/EC + 2009/1781
Harmonised standards usedEN ISO 12100
EN 17281
EN 60204-1
EN 61000-6-2: 2005 + AC: 2005
EN 61000-6-4: 2007 + A1: 2001
The signatories act on behalf of and with the authority of the company management.
Documentation supervisor:
S. Reiser
Alfred Kärcher SE & Co. KG
Alfred-Kärcher-Str. 28 - 40
71364 Winnenden (Germany)
Ph.: +49 7195 14-0
Fax: +49 7195 14-2212
Winnenden, 2022/11/01