HDS 9/20-4 M/MXAHDS 10/21-4 M/MXAHDS 12/18-4 S/SXAHDS 13/20-4 S/SXA
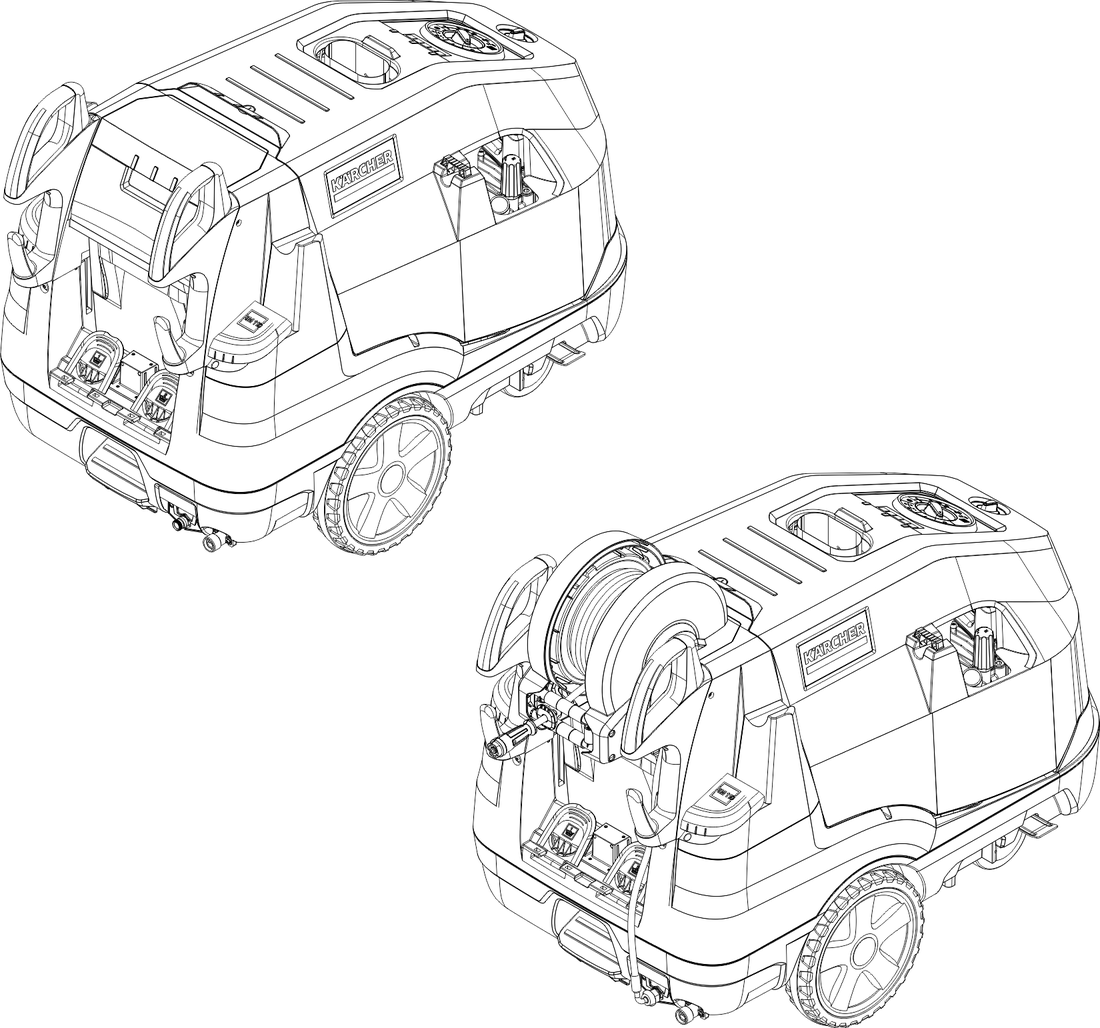
59794160 (01/24)
59794160 (01/24)
Read these original instructions and the enclosed safety instructions before using the device for the first time. Act in accordance with them.
Keep both books for future reference or for future owners.
If the operating instructions and safety instructions are not observed, the device can be damaged and dangers could arise for users and other persons.
Notify the dealer immediately in the case of shipping damage.
Check the package contents when unpacking for missing accessories or for damage. Scope of delivery see illustration A.
At operating elevations of approx. 800 m above sea level or higher, please contact your dealer to have the burner setting adjusted to the elevation and reduced oxygen content.
The packing materials can be recycled. Please dispose of packaging in accordance with the environmental regulations.
Electrical and electronic devices contain valuable, recyclable materials and often components such as batteries, rechargeable batteries or oil, which - if handled or disposed of incorrectly - can pose a potential danger to human health and the environment. However, these components are required for the correct operation of the device. Devices marked by this symbol are not allowed to be disposed of together with the household rubbish.
Current information on content materials can be found at: www.kaercher.de/REACH
Please do not allow engine oil, heating oil, diesel and petrol to enter the environment. Please protect the ground and dispose of old oil in an environmentally friendly manner.
0 = off
Control elements for the cleaning process are yellow.
Control elements for maintenance and servicing are light grey.
![]() | Do not aim the high-pressure jet may at persons, animals, live electrical equipment or the device itself. Protect the device against frost. |
![]() | Danger of injury from electrical voltage. Only qualified electricians or authorised and qualified technical specialists are permitted to work on the electrical systems. |
![]() | Health risk from poisonous exhaust gases. Never inhale the exhaust gases. |
![]() | Risk of burns from hot surfaces. |
![]() | Risk of injury! Do not reach in. |
![]() | QR code for information |
Only use the device for cleaning, e.g. machines, vehicles, buildings, tools, façades, terraces and garden equipment.
Use at petrol stations or other hazard zones
Risk of injury
Adhere to the respective safety regulations.
Do not allow waste water containing mineral oil to penetrate soil, waterways or the sewage system. Only wash the motor or the undercarriage in suitable places with an oil separator.
Dirty water
Premature wear and tear or deposits in the device
Supply the device using only clean water, or recycled water that does not exceed the specified limit values.
The following limit values apply to the water supply:
pH value: 6.5-9.5
Electrical conductivity: Conductivity of fresh water + 1200 µS/cm, maximum conductivity 2000 µS/cm
Settleable particles (sample volume 1 l, settling time 30 minutes): < 0.5 mg/l
Filterable particles: < 50 mg/l, no abrasive substances
Hydrocarbons: < 20 mg/l
Chloride: < 300 mg/l
Sulphate: < 240 mg/l
Calcium: < 200 mg/l
Total hardness: < 28 °dH, < 50° TH, < 500 ppm (mg CaCO3/l)
Iron: < 0.5 mg/l
Manganese: < 0.05 mg/l
Copper: < 2 mg/l
Active chloride: < 0.3 mg/l
Free of unpleasant odours
The following safety instructions apply to the device:
Observe the respectively applicable national regulations for liquid jet cleaners.
Observe the respectively applicable national accident prevention regulations. Liquid jet cleaners must be tested regularly and the results of the test recorded in writing.
Note that the heating system in the device is classified as a furnace. Furnaces must be inspected regularly according to the applicable national regulations.
According to the application national regulations, this device must be initially commissioned by a qualified person when used commercially. KÄRCHER has already performed and documented this initial commissioning for you. You can request the documentation for this from your KÄRCHER partner. Please provide the part number and works number of the device when requesting documentation.
We explicitly state that the application national regulations require that this device must be inspected regularly by a qualified person. Please contact your KÄRCHER partner for this.
No modifications may be made to the device or accessories.
Safety devices protect the user and may not be disabled or functionally circumvented.
When reducing the water volume at the pump head or with the pressure/quantity regulator on the high-pressure gun, the overflow valve opens and part of the water flows back to the pump suction side.
If the high-pressure gun is closed so that all the water flows back to the pump suction side, the pressure switch on the overflow valve switches off the pump.
If the high-pressure gun is opened again, the pressure switch on the cylinder head switches the pump on again.
The overflow valve is set and sealed at the factory. The adjustment is performed only by customer service.
The safety valve opens if the overflow valve or pressure switch is faulty.
The safety valve is adjusted and sealed at the factory. The adjustment is performed only by customer service.
The water shortage safeguard prevents the burner from switching on when there is a lack of water.
The exhaust gas thermostat switches the device off when the emission temperature is too high.
Damaged components
Risk of injury
Check that the device, accessories, supply lines and connections are in perfect condition. If the condition is not perfect, you may not use the device.
Apply the parking brake.
Danger from improper installation
Risk of damage
When hooking the electric supply cable into the cable guide of the right handle bracket, make sure that the cable does not get damaged.
Mount the handlebar, observing the tightening torque of the screws (6.5-7.0 Nm).
Fasten the hubcaps.
Fold the lid of the storage compartment vertically upwards and remove it.
Fold out the folding compartment.
Unlock the storage compartment from below using the 2 latches and pull it out upwards.
Close the folding compartment.
Insert the hose reel into the two guide rails, let it slide down slowly and lock into place.
Fit the hose reel connection hose to the high-pressure connection of the device.
Device with ANTI!Twist: Attach the yellow high-pressure hose connection to the high-pressure gun.
The EASY!Lock system connects components quickly and safely via a single turn of the quick-release thread.
Connect the spray lance to the high-pressure gun and hand-tighten (EASY!Lock).
Plug the high-pressure nozzle onto the spray lance.
Fit the union nut and hand-tighten (EASY!Lock).
Device without a hose reel: Connect the high-pressure hose to the high-pressure gun and high-pressure connection of the device and tighten hand-tight (EASY!Lock).
Device with a hose reel: Connect the high-pressure hose to the high-pressure gun and hand-tighten (EASY!Lock).
Rolled-up high-pressure hose
Risk of damage
Fully unroll the high-pressure hose before starting operation.
RM 110 prevents calcification of the heating coil in the presence of hard water.
RM 111 prevents the formation of black water and cares for the pump in the presence of soft water.
Water hardness (°dH) | System care products to be used |
<3 | RM 111 |
>3 | RM 110 |
Determine the local water hardness via the local supply company or with a hardness tester (order number 6.768-004.0).
A test container of system care is included in the scope of delivery.
System care is a highly effective agent for preventing calcification of the pump when operating with calcareous tap water. This is drip-fed dosed into the float tank.
The dosage is set to medium water hardness at the factory.
Fill up the system care.
Unsuitable fuel
Risk of explosion
Only use diesel fuel or light heating oil. Unsuitable fuels, such as petrol, must not be used.
Operation with an empty fuel tank
Destruction of the fuel pump
Never operate the device with an empty fuel tank.
Open the tank cap.
Refill the fuel.
Close the tank cap.
Wipe up the spilt fuel.
Unsuitable detergents
Risk of injury
Use only KÄRCHER products.
Never fill with solvents (e.g. petrol, acetone, thinners).
Avoid contact with eyes and skin.
Observe the safety and handling instructions of the detergent manufacturer.
Kärcher offers an individual range of cleaning and care products. Your dealer will be happy to advise you.
Fill with detergent.
See the "Technical data" for the connected loads.
The supply hose is not included in the scope of delivery.
Connect the supply hose (minimum length 7.5 m, minimum diameter 3/4") to the water connection of the device and to the water inlet (e.g. tap) using the water connection adapter.
Open the water inlet.
Suction of fluids containing solvents or drinking water
Risk of injury and damage, contamination of drinking water
Never extract fluids containing solvents such as paint thinner, petrol, oil or unfiltered water. The seals in the device are not resistant to solvents. The spray mist of solvents is highly flammable, explosive and poisonous.
Never extract water from drinking water tanks.
If the device is to draw water from an external container, the following modification is required:
Open the filling hole for system care.
Unscrew and remove the system care cover.
Remove the water connection on the fine filter.
Unscrew the fine filter on the pump head.
Remove the system care container.
Unscrew the upper supply hose to the float tank.
Connect the upper supply hose to the pump head.
Plug the flushing line of the detergent dosing valve onto the blind plug.
Connect the suction hose (diameter at least 3/4") with filter (accessory) to the water connection.
Hang the suction hose in an external water source.
Maximum suction height: 0.5 m
Until the pump draws in water: Set the pressure/quantity regulator of the pump unit to the maximum value and close the detergent dosing valve.
Reinstall in the in the reverse order. Make sure that the solenoid valve cable is not pinched on the system care container.
Unsuitable electrical extension cables
Electric shock
Only use approved and appropriately marked electrical extension cables with a sufficient line cross section for outdoors.
Make sure that the plug and coupling of an extension cable used are watertight.
Always unroll extension cables completely.
Exceeding the grid impedance
Electrical shock in the event of a short-circuit
The maximum permissible mains grid impedance at the electrical connection point (see Technical data) must not be exceeded.
Contact your electricity supplier in the case of any uncertainties regarding the mains grid impedance at your electrical connection point.
For connected loads, see technical data and type plate.
The electrical connection must be carried out by an electrician and comply with IEC 60364-1.
Flammable fluids
Risk of explosion
Do not spray inflammable liquids.
Operation without spray lance
Risk of injury
Never operate the device without the spray lance installed.
Before each use, check that the spray lance is firmly seated. The screw connection of the spray lance must be tightened hand tight.
High-pressure water jet
Danger of injury
Never fasten the trigger and safety lever in the actuated position.
Do not use the high-pressure gun when the safety lever is damaged.
Push the safety latch of the high-pressure gun forwards every time before starting work with the device.
Hold the high-pressure gun and spray lance with both hands.
Operation with an empty fuel tank
Destruction of the fuel pump
Never operate the device with an empty fuel tank.
Opening the high-pressure gun: Actuate the safety lever and trigger.
Closing the high-pressure gun: Release the safety lever and trigger.
Switch off the device and operate the high-pressure gun until the device is depressurized.
Lock the high-pressure gun by pushing the safety latch forwards.
Change the nozzle.
Set the trigger to the operating mode. The standby mode indicator light lights up. The device starts up briefly and switches off as soon as the working pressure is reached.
If the direction of rotation indicator light lights up during operation, switch off the device immediately and rectify the fault, see "Troubleshooting".
Unlock the high-pressure gun by pushing the safety latch to the rear. When the high-pressure gun is actuated, the device switches on again.
If no water comes out of the high-pressure nozzle, bleed the pump. See help in the event of malfunctions – device does not build up pressure.
30 °C to 98 °C: Clean with hot water.
100 °C to 150 °C: Clean with steam.
Set the power switch to the desired temperature.
During steam operation: Replace the high-pressure nozzle (stainless steel) with the steam nozzle (brass) (see Operation with steam).
Turn the regulating spindle clockwise: Increase the working pressure (MAX).
Turn the regulating spindle anticlockwise: Reduce the working pressure (MIN).
Danger of a loose spray lance
Risk of injury
Take care to ensure that the spray lance screw connection does not release when adjusting the pressure/quantity control.
If you want to work with reduced pressure over the long term, set the pressure on the pressure/quantity regulator of the pump unit.
Set the power switch to max. 98 °C.
Set the working pressure on the pressure/quantity regulator of the pump unit to the maximum value.
Adjust the working pressure and flow rate by turning (variable) the pressure/quantity regulator on the high-pressure gun (+/-).
Use detergents sparingly to conserve the environment.
The detergent must be suitable for the surface to be cleaned.
The guide values on the control panel refer to the maximum working pressure.
If detergent is to be sucked in from an external container, route the detergent suction hose through the recess to the outside.
Set the concentration of the detergent via the detergent dosing valve according to the manufacturer's instructions.
Always initially direct the high-pressure jet at the object to be cleaned from a distance to avoid damage due to excessive pressure.
Set the working pressure, the cleaning temperature and the detergent concentration according to the surface to be cleaned.
Loosen dirt: Spray the detergent sparingly and let it take effect for 1... 5 minutes, but do not let it dry.
Remove dirt: Rinse off the loosened dirt with the high-pressure jet.
For removing light contamination and for rinsing, e.g. garden machines, terrace, tools.
Adjust the working pressure as required.
The device works in the most economical temperature range (max. 60 °C).
30-50 °C: Light soiling
Max. 60 °C: Soiling containing protein, e.g. in the food industry
60-90 °C: Car cleaning, machine cleaning
100-110 °C: Preservative removal, very greasy soiling
Up to 140 °C: Thawing aggregates, façade cleaning in some cases
Hot water
Risk of scalding
Avoid contact with hot water.
Set the power switch to the desired temperature.
Hot steam
Risk of scalding
At work temperatures above 98 °C, the working pressure must not exceed 3.2 MPa (32 bar).
It is therefore essential that the following measures are carried out:
Replace the high-pressure nozzle (stainless steel) with the steam nozzle (brass, part no. see Technical Data).
Completely open the pressure/quantity regulator on the high-pressure gun, towards + as far as it will go.
Set the working pressure on the pressure/quantity regulator of the pump unit to the minimum value.
Set the power switch to min. 100 °C.
Lock the high-pressure gun by pushing the safety latch forwards.
Set the detergent dosing valve to "0".
Set the power switch to level 1 (operation with cold water).
Flush the device clean for at least 1 minute with the high-pressure gun open.
Risk of injury from hot water or steam
Risk of scalding
After operation with hot water or steam, the device must be operated with the gun opened with cold water for at least two minutes to cool it down.
Close the water inlet.
Open the high-pressure gun.
Switch on the pump with the power switch and let it run for 5-10 seconds.
Close the high-pressure gun.
Set the power switch to "0".
Only pull the mains plug out of the socket only when your hands are dry.
Remove the water connection.
Actuate the high-pressure gun until the device is completely depressurised.
Lock the high-pressure gun by pushing the safety latch forwards.
Do not kink the high-pressure hose or the electrical line.
Snap the spray lance into the holder on the device cover.
Roll up the high-pressure hose and the electrical line and hang them on the supports.
Device with a hose reel: Stretch out the high-pressure hose before winding it up.
Device with a hose reel: Unlock the hose reel by pulling on the high-pressure hose and let the high-pressure hose slowly roll up. Control the reeling speed by holding the hose.
Frost hazard
Destruction of the device through freezing water
Store the device that has not been completely drained of water in a frost-free place.
In the case of devices that are connected to a chimney, the ingress of cold air must be taken into account.
Cold air entering through the chimney
Risk of damage
When the exterior temperatures are below 0 °C, disconnect the device from the chimney.
Shut down the device if frost-free storage is not possible.
For longer breaks in operation or when frost-free storage is not possible:
Drain the detergent tank.
Drain the water.
Flush the device with antifreeze.
Unscrew the water supply hose and the high-pressure hose.
Unscrew the supply line at the boiler base and allow the heating coil to drain.
Allow the device for run for a maximum of 1 minute until the pump and lines are empty.
Observe the handling instructions of the anti-freeze manufacturer.
Pour a commercially available antifreeze into the float tank.
Switch on the device (without burner) and allow it to run until the device is completely flushed.
This also provides a certain degree of corrosion protection.
Improper transport with a factory truck
Risk of damage
Pay attention to the orientation of the device when transporting it with a factory truck.
Improper transportation
Risk of damage
Protect the trigger of the high-pressure gun from damage.
Failure to observe the weight
Risk of injury and damage
Be aware of the weight of the device during transportation.
When transporting the device in vehicles, secure it to prevent it from slipping or overturning in accordance with the respectively applicable guidelines.
Failure to observe the weight
Risk of injury and damage
Be aware of the weight of the device during storage.
Inadvertently starting up device, touching live components
Risk of injury, electric shock
Switch off the device before performing any work on the device.
Remove the mains plug.
Close the water inlet.
Open the high-pressure gun.
Switch on the pump with the power switch and let it run for 5-10 seconds.
Close the high-pressure gun.
Set the power switch to "0".
Only pull the mains plug out of the socket only when your hands are dry.
Remove the water connection.
Actuate the high-pressure gun until the device is completely depressurised.
Lock the high-pressure gun by pushing the safety latch forwards.
Allow the device to cool down.
You can agree on regular safety inspections or close a maintenance contract with your dealer. Please seek advice on this.
Milky oil
Device damage
If the oil is milky, inform authorized Customer Service immediately.
Clean the sieve in the water connection.
Clean the fine filter.
Clean the fuel strainer.
Check the oil level.
Clean the filter on the detergent suction hose.
Change the oil.
Have the device maintained by Customer Service.
Perform a pressure test according to the manufacturer's specifications.
Risk of injury
The hose reel may turn very fast unexpectedly if it is released.
Carefully follow the steps below and secure the hose reel as described.
Only high-pressure hoses in the "Ultra Guard" version are suitable for this device.
Lift off the cover on the hose reel with a flat head screwdriver.
Completely unroll the high-pressure hose from the hose reel.
Insert a 10 mm Allen key through the hexagonal opening in the casing. Insert the key until the hose reel is blocked.
Unscrew the 2 screws.
Remove the hose stopper from the high-pressure hose.
Pull out the locking hook.
Pull the high-pressure hose out of the hose connection.
Insert the new high-pressure hose through the hose guide rollers and insert it into the hose connection. Observe the direction of rotation of the hose reel.
Insert the locking hook into the hose connection.
Check that all washers are behind the locking hook.
Fit the hose stopper to the other end of the high-pressure hose. Distance to the end of the hose about 1 m (to the high-pressure gun).
Connect the device to the water supply and power supply, put it into operation and check the connection for leaks.
Tension the hose and keep it tensioned. Pull out the Allen key while the hose is taut.
Unlock the hose reel by pulling on the high-pressure hose and let the high-pressure hose slowly roll up. Control the reeling speed by holding the hose.
Replace the cover.
Remove the sieve.
Clean the sieve in water.
Install the sieve again.
Depressurise the device.
Unscrew the fine filter on the pump head.
Dismantle the fine filter and take out the filter inlay.
Clean the filter inlay with clean water or compressed air.
Assemble in the reverse order.
Knock out the fuel sieve. Do not allow fuel to enter the environment.
Pull out the detergent suction hose port.
Clean the filter in water.
Fit the filter again.
See the "Technical data" section for the oil filling quantity and type.
Provide a catch pan for approx. 1 litre of oil.
Lever out the safety clip with a flat-blade screwdriver and pull out the oil drain plug.
Drain the oil into the catch pan.
Dispose of the old oil in an environmentally friendly manner or hand it over to an authorised collection point.
Push the oil drain plug back in and secure it with the safety clip.
Slowly fill with new oil until the MAX marking on the oil tank. The air bubbles must be able to escape.
Inadvertently starting up device, touching live components
Risk of injury, electric shock
Switch off the device before performing any work on the device.
Remove the mains plug.
The rotation direction indicator light lights up
Remedy:
Swap the pins on the power plug.
The standby mode indicator light goes out or the device does not run
Cause:
No mains voltage
Remedy:
Check the power supply and the supply line.
Service indicator light flashes 1x
Cause:
Water shortage
Remedy:
Check the water connection and the supply lines.
Cause:
Leak in the high-pressure system
Remedy:
Check the high-pressure system and the connections for leaks.
Service indicator light flashes 2x
Cause:
Fault in the voltage supply or current consumption of the motor too high
Remedy:
Check the power supply and the mains power supply circuit breaker.
Contact Customer Service.
The service indicator light flashes 3x
Cause:
Motor overloaded/overheated
Remedy:
Set the power switch to "0".
Allow the device to cool down.
Switch the device on.
Cause:
Malfunction occurs repeatedly
Remedy:
Contact Customer Service.
The service indicator light flashes 4x
Cause:
Exhaust gas thermostat has triggered
Remedy:
Set the power switch to "0".
Allow the device to cool down.
Switch the device on.
Cause:
Malfunction occurs repeatedly
Remedy:
Contact Customer Service.
Service indicator light flashes 5x
Cause:
Reed switch stuck in the water shortage safeguard or magnetic piston stuck
Remedy:
Contact Customer Service.
The service indicator light flashes 6x
Cause:
Flame sensor has switched off the burner
Remedy:
Contact Customer Service.
The fuel indicator light lights up
Cause:
Fuel tank is empty
Remedy:
Refill the fuel.
System care indicator light lights up
Cause:
System care container is empty
Remedy:
Fill up the system care.
Device not building up pressure
Cause:
Air in the system
Remedy:
Venting the pump:
Set the detergent dosing valve to "0".
With the high-pressure gun open, switch the device on and off several times via the power switch.
Open and close the pressure/quantity regulator of the pump unit with the high-pressure gun open.
The venting process is accelerated by removing the high-pressure hose from the high-pressure connection.
Top up the detergent if necessary.
Check connections and lines.
Cause:
Pressure is set to MIN
Remedy:
Set the pressure to "MAX".
Cause:
Sieve in the water connection/fine filter is dirty
Remedy:
Clean the sieve.
Clean the fine filter, replace if necessary.
Cause:
Water supply volume too low
Remedy:
Check the water supply volume (see "Technical data").
Device is leaking, water is dripping from the bottom of the device
Cause:
Pump leaking
Remedy:
If there is a significant leak, have the device checked by Customer Service.
3 drops/minute are permitted.
The device switches on and off continuously when the high-pressure gun is locked
Cause:
Leak in the high-pressure system
Remedy:
Check the high-pressure system and the connections for leaks.
The device does not suck in any detergent
Remedy:
Let the device run with the detergent dosing valve open and the water inlet closed until the float tank has been sucked empty and the pressure drops to “0”.
Open the water inlet again.
Cause:
If the pump still does not suck in detergent, this can be due to the following reasons:
The filter in the detergent suction hose is dirty
Remedy:
Clean the filter.
Cause:
Check valve is stuck
Remedy:
Pull off the detergent hose and free up the check valve with a blunt object.
Burner not igniting
Cause:
Fuel tank is empty
Remedy:
Refill the fuel.
Cause:
Water shortage
Remedy:
Check the water connection and the supply lines.
Cause:
Fuel filter dirty
Remedy:
Change the fuel filter.
Cause:
No ignition spark
Remedy:
If no ignition spark is visible through the sight glass during operation, have the device checked by Customer Service.
The set temperature is not reached when operating with hot water
Cause:
Working pressure/flow rate too high
Remedy:
Reduce the working pressure/flow rate via the pressure/quantity regulator of the pump unit.
Cause:
Sooty heating coil
Remedy:
Have the soot removed from the device by Customer Service.
If the malfunction cannot be corrected, the device must be checked by the Customer Service department.
The rotation direction indicator light lights up
Remedy:
Swap the pins on the power plug.
The standby mode indicator light goes out or the device does not run
Cause:
No mains voltage
Remedy:
Check the power supply and the supply line.
Service indicator light flashes 1x
Cause:
Water shortage
Remedy:
Check the water connection and the supply lines.
Cause:
Leak in the high-pressure system
Remedy:
Check the high-pressure system and the connections for leaks.
Service indicator light flashes 2x
Cause:
Fault in the voltage supply or current consumption of the motor too high
Remedy:
Check the power supply and the mains power supply circuit breaker.
Contact Customer Service.
The service indicator light flashes 3x
Cause:
Motor overloaded/overheated
Remedy:
Set the power switch to "0".
Allow the device to cool down.
Switch the device on.
Cause:
Malfunction occurs repeatedly
Remedy:
Contact Customer Service.
The service indicator light flashes 4x
Cause:
Exhaust gas thermostat has triggered
Remedy:
Set the power switch to "0".
Allow the device to cool down.
Switch the device on.
Cause:
Malfunction occurs repeatedly
Remedy:
Contact Customer Service.
Service indicator light flashes 5x
Cause:
Reed switch stuck in the water shortage safeguard or magnetic piston stuck
Remedy:
Contact Customer Service.
The service indicator light flashes 6x
Cause:
Flame sensor has switched off the burner
Remedy:
Contact Customer Service.
The fuel indicator light lights up
Cause:
Fuel tank is empty
Remedy:
Refill the fuel.
System care indicator light lights up
Cause:
System care container is empty
Remedy:
Fill up the system care.
Device not building up pressure
Cause:
Air in the system
Remedy:
Venting the pump:
Set the detergent dosing valve to "0".
With the high-pressure gun open, switch the device on and off several times via the power switch.
Open and close the pressure/quantity regulator of the pump unit with the high-pressure gun open.
The venting process is accelerated by removing the high-pressure hose from the high-pressure connection.
Top up the detergent if necessary.
Check connections and lines.
Cause:
Pressure is set to MIN
Remedy:
Set the pressure to "MAX".
Cause:
Sieve in the water connection/fine filter is dirty
Remedy:
Clean the sieve.
Clean the fine filter, replace if necessary.
Cause:
Water supply volume too low
Remedy:
Check the water supply volume (see "Technical data").
Device is leaking, water is dripping from the bottom of the device
Cause:
Pump leaking
Remedy:
If there is a significant leak, have the device checked by Customer Service.
3 drops/minute are permitted.
The device switches on and off continuously when the high-pressure gun is locked
Cause:
Leak in the high-pressure system
Remedy:
Check the high-pressure system and the connections for leaks.
The device does not suck in any detergent
Remedy:
Let the device run with the detergent dosing valve open and the water inlet closed until the float tank has been sucked empty and the pressure drops to “0”.
Open the water inlet again.
Cause:
If the pump still does not suck in detergent, this can be due to the following reasons:
The filter in the detergent suction hose is dirty
Remedy:
Clean the filter.
Cause:
Check valve is stuck
Remedy:
Pull off the detergent hose and free up the check valve with a blunt object.
Burner not igniting
Cause:
Fuel tank is empty
Remedy:
Refill the fuel.
Cause:
Water shortage
Remedy:
Check the water connection and the supply lines.
Cause:
Fuel filter dirty
Remedy:
Change the fuel filter.
Cause:
No ignition spark
Remedy:
If no ignition spark is visible through the sight glass during operation, have the device checked by Customer Service.
The set temperature is not reached when operating with hot water
Cause:
Working pressure/flow rate too high
Remedy:
Reduce the working pressure/flow rate via the pressure/quantity regulator of the pump unit.
Cause:
Sooty heating coil
Remedy:
Have the soot removed from the device by Customer Service.
The warranty conditions issued by our sales company responsible apply in all countries. We shall remedy possible malfunctions on your device within the warranty period free of cost, provided that a material or manufacturing defect is the cause. In a warranty case, please contact your dealer (with the purchase receipt) or the next authorised customer service site.
You can find more detailed information at: www.kaercher.com/dealersearch
If the device is connected to a chimney or if the device cannot be seen, we recommend installing a flame monitor (option).
Only use original accessories and original spare parts. They ensure that the appliance will run safely and fault-free.
Information on accessories and spare parts can be found at www.kaercher.com.
EU Declaration of Conformity |
We hereby declare that the machine described below complies with the relevant basic safety and health requirements in the EU Directives, both in its basic design and construction as well as in the version placed in circulation by us. This declaration is invalidated by any changes made to the machine that are not approved by us.
Product: High-pressure cleaner
Type: 1.071-xxx
Currently applicable EU Directives2000/14/EC
2006/42/EC (+2009/127/EC)
2009/125/EC
2011/65/EU
2014/30/EU
2014/53/EU
2014/68/EU
Category of the assemblyII
Conformity processModule H
Heating coilModule H conformity evaluation
Control blockModule H conformity evaluation
Various pipelinesConformity evaluation Art. 4 Para. 3
Harmonised standards usedEN IEC 63000: 2018
EN 55014-1: 2017 + A11: 2020
EN 55014-2: 2015
EN 60335-1
EN 60335-2-79
EN 61000-3-2: 2014
EN 62233: 2008
HDS 9/20-4, HDS 10/21-4, HDS 12/18-4:
EN 61000-3-3: 2013
HDS 13/20-4:
EN 61000-3-11: 2000
Commission Regulation(s)(EU) 2019/1781
Applied specifications:AD 2000 based on
TRD 801 based on
Name of stated position:For 2014/68/EUTÜV Rheinland Industrie Service GmbH
Am Grauen Stein
51105 Köln
ID no. 0035
Certificate No .:01 202 111/Q-08 0003
Conformity evaluation procedure used2000/14/EC: Annex V
Sound power level dB(A)HDS 9/20-4
Measured: 74
Guaranteed: 93
HDS 10/21-4
Measured: 74
Guaranteed: 93
HDS 12/18-4
Measured: 74
Guaranteed: 93
HDS 13/20-4
Measured: 74
Guaranteed: 93
The signatories act on behalf of and with the authority of the company management.
Documentation supervisor:
S. Reiser
Alfred Kärcher SE & Co. KG
Alfred-Kärcher-Str. 28 - 40
71364 Winnenden (Germany)
Ph.: +49 7195 14-0
Fax: +49 7195 14-2212
Winnenden, 2022/10/01
Declaration of Conformity (UK) |
We hereby declare that the product described below complies with the relevant provisions of the following UK Regulations, both in its basic design and construction as well as in the version put into circulation by us. This declaration shall cease to be valid if the product is modified without our prior approval.
Product: High-pressure cleaner
Type: 1.071-xxx
Currently applicable UK RegulationsS.I. 2001/1701 (as amended)
S.I. 2008/1597 (as amended)
S.I. 2010/2617 (as amended)
S.I. 2012/3032 (as amended)
S.I. 2016/1091 (as amended)
S.I. 2017/1206 (as amended)
2014/68/EU
Category of the assemblyII
Conformity processModule H
Heating coilModule H conformity evaluation
Control blockModule H conformity evaluation
Various pipelinesConformity evaluation Art. 4 Para. 3
Designated standards usedEN IEC 63000: 2018
EN 55014-1: 2017 + A11: 2020
EN 55014-2: 2015
EN 60335-1
EN 60335-2-79
EN 61000-3-2: 2014
EN 62233: 2008
HDS 9/20-4, HDS 10/21-4, HDS 12/18-4:
EN 61000-3-3: 2013
HDS 13/20-4:
EN 61000-3-11: 2000
Commission Regulation(s)(EU) 2019/1781
Applied specifications:AD 2000 based on
TRD 801 based on
Name of stated position:For 2014/68/EUTÜV Rheinland Industrie Service GmbH
Am Grauen Stein
51105 Köln
ID no. 0035
Certificate No .:01 202 111/Q-08 0003
Conformity assessment procedure usedS.I. 2001/1701 (as amended): Schedule 8
Sound power level dB(A)HDS 9/20-4
Measured: 74
Guaranteed: 93
HDS 10/21-4
Measured: 74
Guaranteed: 93
HDS 12/18-4
Measured: 74
Guaranteed: 93
HDS 13/20-4
Measured: 74
Guaranteed: 93
The signatories act on behalf of and with the authority of the company management.
Documentation supervisor:
S. Reiser
Alfred Kärcher SE & Co. KG
Alfred-Kärcher-Str. 28 - 40
71364 Winnenden (Germany)
Ph.: +49 7195 14-0
Fax: +49 7195 14-2212
Winnenden, 2022/10/01
Electrical connection | |
Mains voltage | 400 V |
Phase | 3 ~ |
Power frequency | 50 Hz |
Degree of protection | IPX5 |
Protection class | I |
Power rating | 7,0 kW |
Power protection (C-type, gL/gG) | 16 A |
Water connection | |
Feed pressure (max.) | 1,0 (10) MPa (bar) |
Input temperature (max.) | 30 °C |
Input amount (min.) | 1200 (20) l/h (l/min) |
Suction height (max.) | 0,5 m |
Device performance data | |
Water flow rate | 450-900 (7,5-15) l/h (l/min) |
Water operating pressure with standard nozzle | 3-20 (30-200) MPa (bar) |
Excess operating pressure safety valve (maximum) | 24 (240) MPa (bar) |
Steam operation flow rate | 350-420 (5,8-7,0) l/h (l/min) |
Steam operation operating pressure with steam nozzle (max.) | 3,2 (32) MPa (bar) |
Part no. of steam nozzle | 2.114-004.0 (40060) |
Hot water operating temperature (maximum) | 98 °C |
Steam operation working temperature | 155 °C |
Detergent flow rate | 0-54 (0-0,9) l/h (l/min) |
Burner output | 75 kW |
Heating oil consumption (max.) | 6,5 kg/h |
High-pressure gun recoil force | 50 N |
Nozzle size of standard nozzle | 047 |
Dimensions and weights | |
Typical operating weight (M/S) | 177 kg |
Typical operating weight (MXA/SXA) | 189 kg |
Length x width x height | 1330 x 750 x 1060 mm |
Fuel tank | 25 l |
Detergent tank | 20+10 l |
High-pressure pump | |
Oil volume | 1,0 l |
Oil type | SAE 90 |
Burner | |
Fuel | EL heating oil or diesel |
Determined values in acc. with EN 60335-2-79 | |
Sound pressure level LpA | 75 dB(A) |
Uncertainty KpA | 3 dB(A) |
Sound power level LWA + uncertainty KWA | 93 dB(A) |
Hand-arm vibration value | 3,7 m/s2 |
Uncertainty K | 0,3 m/s2 |
Electrical connection | |
Mains voltage | 400 V |
Phase | 3 ~ |
Power frequency | 50 Hz |
Degree of protection | IPX5 |
Protection class | I |
Power rating | 8,0 kW |
Power protection (C-type, gL/gG) | 16 A |
Water connection | |
Feed pressure (max.) | 1,0 (10) MPa (bar) |
Input temperature (max.) | 30 °C |
Input amount (min.) | 1300 (21,7) l/h (l/min) |
Suction height (max.) | 0,5 m |
Device performance data | |
Water flow rate | 500-1000 (8,3-16,7) l/h (l/min) |
Water operating pressure with standard nozzle | 3-21 (30-210) MPa (bar) |
Excess operating pressure safety valve (maximum) | 24 (240) MPa (bar) |
Steam operation flow rate | 380-480 (6,3-8,0) l/h (l/min) |
Steam operation operating pressure with steam nozzle (max.) | 3,2 (32) MPa (bar) |
Part no. of steam nozzle | 2.114-006.0 (40070) |
Hot water operating temperature (maximum) | 98 °C |
Steam operation working temperature | 155 °C |
Detergent flow rate | 0-54 (0-0,9) l/h (l/min) |
Burner output | 83 kW |
Heating oil consumption (max.) | 7,3 kg/h |
High-pressure gun recoil force | 57 N |
Nozzle size of standard nozzle | 052 |
Dimensions and weights | |
Typical operating weight (M/S) | 183 kg |
Typical operating weight (MXA/SXA) | 195 kg |
Length x width x height | 1330 x 750 x 1060 mm |
Fuel tank | 25 l |
Detergent tank | 20+10 l |
High-pressure pump | |
Oil volume | 1,0 l |
Oil type | SAE 90 |
Burner | |
Fuel | EL heating oil or diesel |
Determined values in acc. with EN 60335-2-79 | |
Sound pressure level LpA | 75 dB(A) |
Uncertainty KpA | 3 dB(A) |
Sound power level LWA + uncertainty KWA | 93 dB(A) |
Hand-arm vibration value | 4,6 m/s2 |
Uncertainty K | 0,3 m/s2 |
Electrical connection | |
Mains voltage | 400 V |
Phase | 3 ~ |
Power frequency | 50 Hz |
Degree of protection | IPX5 |
Protection class | I |
Power rating | 8,0 kW |
Power protection (C-type, gL/gG) | 16 A |
Water connection | |
Feed pressure (max.) | 1,0 (10) MPa (bar) |
Input temperature (max.) | 30 °C |
Input amount (min.) | 1400 (23,3) l/h (l/min) |
Suction height (max.) | 0,5 m |
Device performance data | |
Water flow rate | 500-1200 (8,3-20) l/h (l/min) |
Water operating pressure with standard nozzle | 3-18 (30-180) MPa (bar) |
Excess operating pressure safety valve (maximum) | 24 (240) MPa (bar) |
Steam operation flow rate | 430-500 (7,2-8,3) l/h (l/min) |
Steam operation operating pressure with steam nozzle (max.) | 3,2 (32) MPa (bar) |
Part no. of steam nozzle | 2.114-010.0 (40090) |
Hot water operating temperature (maximum) | 98 °C |
Steam operation working temperature | 155 °C |
Detergent flow rate | 0-54 (0-0,9) l/h (l/min) |
Burner output | 100 kW |
Heating oil consumption (max.) | 7,7 kg/h |
High-pressure gun recoil force | 63 N |
Nozzle size of standard nozzle | S: 065, SXA: 068 |
Dimensions and weights | |
Typical operating weight (M/S) | 202 kg |
Typical operating weight (MXA/SXA) | 214 kg |
Length x width x height | 1330 x 750 x 1060 mm |
Fuel tank | 25 l |
Detergent tank | 20+10 l |
High-pressure pump | |
Oil volume | 1,0 l |
Oil type | SAE 90 |
Burner | |
Fuel | EL heating oil or diesel |
Determined values in acc. with EN 60335-2-79 | |
Sound pressure level LpA | 75 dB(A) |
Uncertainty KpA | 3 dB(A) |
Sound power level LWA + uncertainty KWA | 93 dB(A) |
Hand-arm vibration value | 4,6 m/s2 |
Uncertainty K | 0,3 m/s2 |
Electrical connection | |
Mains voltage | 400 V |
Phase | 3 ~ |
Power frequency | 50 Hz |
Degree of protection | IPX5 |
Protection class | I |
Power rating | 9,5 kW |
Power protection (C-type, gL/gG) | 25 A |
Maximum permissible mains grid impedance | 0.402 Ω |
Water connection | |
Feed pressure (max.) | 1,0 (10) MPa (bar) |
Input temperature (max.) | 30 °C |
Input amount (min.) | 1500 (25) l/h (l/min) |
Suction height (max.) | 0,5 m |
Device performance data | |
Water flow rate | 600-1300 (10-21,7) l/h (l/min) |
Water operating pressure with standard nozzle | 3-20 (30-200) MPa (bar) |
Excess operating pressure safety valve (maximum) | 24 (240) MPa (bar) |
Steam operation flow rate | 485-648 (8,1-10,8) l/h (l/min) |
Steam operation operating pressure with steam nozzle (max.) | 3,2 (32) MPa (bar) |
Part no. of steam nozzle | 2.114-011.0 (40100) |
Hot water operating temperature (maximum) | 98 °C |
Steam operation working temperature | 155 °C |
Detergent flow rate | 0-54 (0-0,9) l/h (l/min) |
Burner output | 108 kW |
Heating oil consumption (max.) | 9,5 kg/h |
High-pressure gun recoil force | 72 N |
Nozzle size of standard nozzle | S: 068, SXA: 070 |
Dimensions and weights | |
Typical operating weight (M/S) | 206 kg |
Typical operating weight (MXA/SXA) | 218 kg |
Length x width x height | 1330 x 750 x 1060 mm |
Fuel tank | 25 l |
Detergent tank | 20+10 l |
High-pressure pump | |
Oil volume | 1,0 l |
Oil type | SAE 90 |
Burner | |
Fuel | EL heating oil or diesel |
Determined values in acc. with EN 60335-2-79 | |
Sound pressure level LpA | 75 dB(A) |
Uncertainty KpA | 3 dB(A) |
Sound power level LWA + uncertainty KWA | 93 dB(A) |
Hand-arm vibration value | 4,6 m/s2 |
Uncertainty K | 0,3 m/s2 |