HD 8/18-4 St, HD 8/18-4 St HHD 10/21-4 St, HD 10/19-4 St HHD 13/18-4 StHD 17/15-4 St, HD 17/12-4 St H
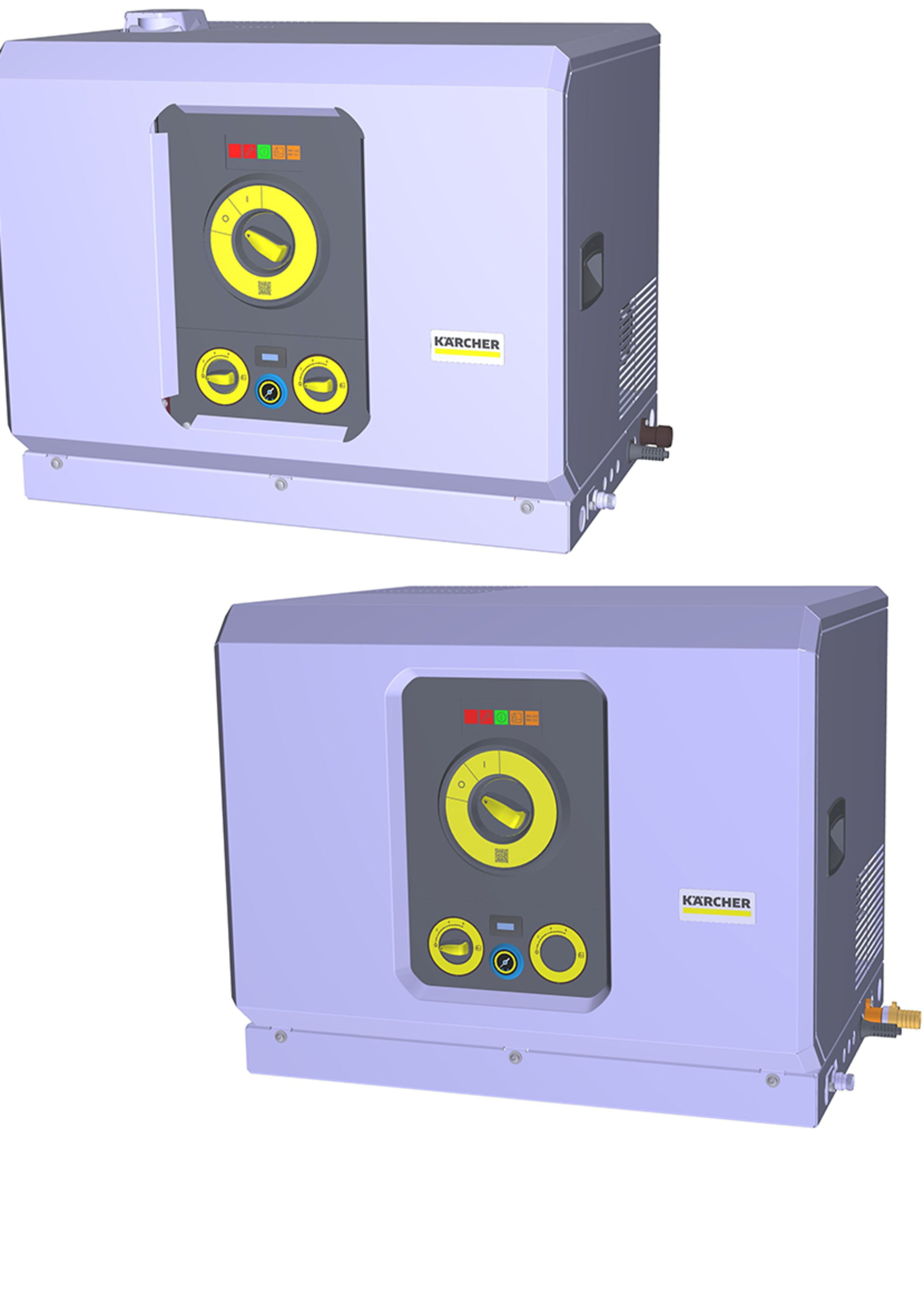
59802420 (10/24)
59802420 (10/24)
Read these original operating instructions and the enclosed safety instructions before using the device for the first time. Proceed accordingly.
Keep both books for future reference or for future owners.
No changes may be made to the device.
For safety reasons we recommend operating the device only via a fault current protection switch (maximum 30 mA).
Children must not operate the device.
Only people who have been instructed on how to use the device, or have proven their ability to operate it, and have been explicitly instructed to use it, must use the device.
Only connect the device to an electrical connection which has been set up by a qualified electrician as per IEC 60364‑1.
Observe the respectively applicable national regulations for liquid jet cleaners.
Observe the legislature’s national accident prevention regulations. Liquid jet cleaners must be tested regularly and the results of the test recorded in writing.
Observe the safety instructions of the used the detergents.
The mains plug and socket must be freely accessible even after installation.
![]() | Do not point the high-pressure jet at people, animals, live electrical equipment or at the device itself. Protect the device from frost. |
![]() | Danger of injury from electrical voltage. Only qualified electricians or authorised and qualified technical specialists are permitted to work on the electrical systems. |
![]() | According to applicable regulations, the device must never be used with the drinking water network without a system separator. Ensure that the connection to your house water system, with which the high-pressure cleaner is operated, is equipped with a system separator according to EN 12729 type BA. Water that has flowed through a system separator is classified as undrinkable. Always connect the system separator to the water supply and never directly to the device. |
![]() | Risk of burns from hot surfaces. |
The system is switched on and off on the device. The detergent dosage can also be set and error messages can be viewed.
Depending on the system design, further workstations are located at the accessory devices (spraying devices), which are connected to the tapping points. Remote controls can optionally be installed at these workstations.
Risk of injury due to missing or modified safety devices!
Safety devices are provided for your own protection.
Do not bypass, remove or render ineffective any safety devices.The safety devices are set and sealed by the manufacturer. Adjustments are performed only by customer service.
The power switch prevents the device from starting up unintentionally. Turn the power switch to 0/OFF during work breaks or when finishing work.
The safety catch on the high-pressure gun prevents the device from being switched on inadvertently.
When the water quantity is reduced via the pressure/quantity control on the trigger gun, the overflow valve opens and part of the water flows back to the suction side of the pump.
When the trigger on the high-pressure gun is release, the pressure switch switches off the high-pressure pump and the high-pressure jet stops.
The pump switches on again when the trigger is pulled.
If the device is not used for 30 minutes, the device switches off. The readiness time can be activated and deactivated by customer service via the service menu.
The motor circuit breaker shuts off the device if power consumption it too high.
The winding protection contact switches the device off in the event of thermal overload.If there are leaks in the high-pressure system, the device is switched off.
The water shortage safeguard prevents the high-pressure pump from switching on when there is a lack of water.
After switching off the device via the high-pressure gun, a solenoid valve located in the high-pressure system opens after the operating standby time has elapsed. This reduces the pressure built up in the high-pressure system.
The packing materials can be recycled. Please dispose of packaging in accordance with the environmental regulations.
Electrical and electronic devices contain valuable, recyclable materials and often components such as batteries, rechargeable batteries or oil, which - if handled or disposed of incorrectly - can pose a potential danger to human health and the environment. However, these components are required for the correct operation of the device. Devices marked by this symbol are not allowed to be disposed of together with the household rubbish.
Current information on content materials can be found at: www.kaercher.de/REACH
The system delivers water at high pressure to a downstream high-pressure cleaning system. If necessary, detergent is sucked in and added to the water.
The system is permanently installed in a dry, frost-free room. The high-pressure water is distributed by a permanently installed piping network. Alternatively, a high-pressure gun with a high-pressure hose can be connected directly to the high-pressure outlet of the device.
The system can be mounted on a wall or installed on a frame (attachment kit, optional).
The system must be installed so that the rear opening is closed, for example by a wall.
Only clean water may be used as a high-pressure medium. Contamination leads to premature wear and tear or deposits in the device.
Measures to reduce hardness may be necessary above 3 °dH.
The use of recycled water must be agreed with Kärcher in advance.
Use at petrol stations or other hazard zones
Risk of injury
Adhere to the respective safety regulations.Do not allow waste water containing mineral oil to penetrate soil, waterways or the sewage system. Only wash the motor or the undercarriage in suitable places with an oil separator.
Dirty water
Premature wear and tear or deposits in the device
Supply the device using only clean water, or recycled water that does not exceed the specified limit values.The following limit values apply to the water supply:
pH value: 6.5-9.5
Electrical conductivity: Conductivity of fresh water + 1200 µS/cm, maximum conductivity 2000 µS/cm
Settleable particles (sample volume 1 l, settling time 30 minutes): < 0.5 mg/l
Filterable particles: < 50 mg/l, no abrasive substances
Hydrocarbons: < 20 mg/l
Chloride: < 300 mg/l
Sulphate: < 240 mg/l
Calcium: < 200 mg/l
Total hardness: < 28 °dH, < 50° TH, < 500 ppm (mg CaCO3/l)
Iron: < 0.5 mg/l
Manganese: < 0.05 mg/l
Copper: < 2 mg/l
Active chloride: < 0.3 mg/l
Free of unpleasant odours
Only use original accessories and original spare parts. They ensure that the appliance will run fault-free and safely.
Information on accessories and spare parts can be found at www.kaercher.com.
Detergents make cleaning tasks easier and a selection of detergents is shown in the table. The instructions on the packaging must be observed before using the detergents.
The following types of detergent are not permitted as they will damage the device:
Detergents containing nitric acid
Detergents containing active chlorine
Area of application | Target group | Detergent | Description | Dosing |
---|---|---|---|---|
Foaming | Food industry / cutting plants | Disinfection cleaning | RM 732 | 1-3% |
Disinfectant | RM 735 | 1,5-2 % | ||
Beverage/winery businesses | Foam cleaner, alkaline | RM 58* | 1-2% | |
Foam cleaner, acidic | RM 59* | 1-2% | ||
Municipality | Foam cleaner, neutral | RM 57* | 1-2% | |
Disinfection cleaning | RM 732 | 1-3% | ||
Agriculture (only for food industry,e.g. Dairy kitchen. Not for areas close to animals) | Disinfection cleaning | RM 732 | 1-3% | |
Disinfectant | RM 735 | 1,5-2% | ||
High-pressure cleaning | Beverage/winery businesses | Active cleaner, neutral | RM 55* | 0,5-8% |
Municipality | Active cleaner, alkaline | RM 81* | 0,25-1,25% | |
Agriculture | Active cleaner, alkaline | RM 31* | 0,375-2,5% | |
Active cleaner, alkaline | RM 81* | 0,25-1,25% | ||
Natural active cleaner, alkaline | RM 82N | |||
Marine equipment | Active cleaner, alkaline | RM 81* | 0,25-1.25% | |
Car/truck workshop | Active cleaner, alkaline (motor/parts) | RM 31* | 0,375-2,5% | |
Active cleaner, alkaline (vehicle upper/underbody) | RM 81* | 0,25-1.25% | ||
Floor cleaning | Food industry/ cutting plants | Intensive deep cleaner | RM 750* | 0,25-1,25 % |
Industrial cleaner | RM 69* | 0,5-3% | ||
Beverage/winery businesses, municipality | Intensive deep cleaner | RM 750 | 0,25-1,25 % | |
Industrial cleaner | RM 69* | 0,5-3% | ||
Car/truck workshop | Intensive deep cleaner | RM 750* | 0,25-1,25 % | |
Industrial cleaner | RM 69* | 0,5-3% | ||
Marine equipment | Intensive deep cleaner | RM 750* | 0,25-1,25 % | |
Industrial cleaner | RM 69* | 0,5-3% | ||
Washing brush | Municipality | Active cleaner, alkaline | RM 81* | 0,25-1.25% |
Active cleaner, neutral | RM 55* | 0,5-8% | ||
Car/truck workshop | Active cleaner, alkaline (vehicle upper/underbody) | RM 81* | 0,25-1.25% | |
Marine equipment | Active cleaner, alkaline | RM 81* | 0,25-1.25% |
* Separator-friendly
For all cleaning work with detergents other than floor cleaning, the surface to be cleaned should be rinsed. In food processing areas, rinsing with drinking water is required.
During unpacking, check the contents for completeness. In the event of shipping damage, please notify your dealer.
No accessories are included in the scope of delivery.
The following attachment kits are available separately:
Remote control (not shown)
Pressure relief (not shown)
Second detergent + dosing valve
Floor structure (steel or stainless steel) (not shown)
Water inlet solenoid valve (not shown)
Operating hours counter + pressure gauge
LED | Blink code | Meaning |
---|---|---|
Service menu LED (red) | - | Direction of rotation (wrong rotating field) |
Service LED (red) | lights up | Carry out service/maintenance after 600 h pump operation |
flashes 1x | Leakage on the device or water shortage (dry running) The device switches off. | |
flashes 2x | Current/voltage fault:
The device switches off. | |
flashes 3x | Winding protection contact fault The device switches off. | |
flashes 8x | Communication fault The device switches off. | |
Operation LED (green) | lights up | Normal operation without faults |
flashes 1x | Pump has been running continuously for 30 minutes | |
flashes 2x | Pump has been continuously inactive for 30 minutes | |
Detergent LED (orange) | lights up | Detergent 1 empty |
flashes 1x | Detergent 2 empty | |
System care LED (orange) | lights up | System care empty (only HD St...H) |
No accessories are included in the scope of delivery.
When the entire water volume is removed, the water flows via the water inlet, float container, advance pressure pump hot water and high-pressure pump to the high-pressure outlet.
Partial withdrawalIf only part of the water output delivered by the pump is required, the residual amount flows back to the suction side of the high-pressure pump via the flow control.
DetergentDetergent is sucked in from up to 2 detergent containers and added using the detergent dosing valves. To activate the detergent, turn the twist grip to the right. No detergent is drawn in at position 0 and the maximum amount is drawn in at position 6.
Automatic pump start and stopIf the system pressure drops during the standby time due to the opening of a consumer, the pressure switch switches on the high-pressure pump. If the consumer is closed again, the pump switches off automatically.
System care (only for HD St...H)Adding RM 110 system care prevents the formation of lime deposits when operating with hot water. St H devices are suitable for hot water operation up to 85°C, St devices up to 60° water inlet temperature. Depending on the water hardness, the dosing can be adjusted by customer service as required.
* Flow chart with 1 detergent without remote control (delivery status)
** Flow chart with 2 detergents and remote control (optional)
*** Flow chart with 1 detergent and remote control (optional)
* Flow chart with 1 detergent without remote control (delivery status)
** Flow chart with 2 detergents and remote control (optional)
*** Flow chart with 1 detergent and remote control (optional)
Installation may only be carried out by authorised specialist personnel!
The water connection, the high-pressure network and the electrical connection may only be carried out by authorised specialist personnel in compliance with local regulations.
The system should be installed in a dry, non-explosive environment.
The device should be installed on a firm and level surface.
The system should be easily accessible for maintenance work.
The system can be mounted on the wall or with the floor structure attachment kit (optional)
Check the load capacity of the wall before installation. Use suitable plugs and screws for concrete, cavity block, brick and aerated concrete walls,e.g. an injection anchor.
The device must not be rigidly connected to the water supply or high-pressure pipework. The connecting hoses must always be fitted.
Provide a stopcock between the water pipe network and the connecting hose.
Switch-on procedures will generate short-term voltage drops. Unfavourable mains conditions may cause other devices to be impaired.
Exceeding the grid impedance
Electrical shock in the event of a short-circuit
The maximum permissible mains grid impedance at the electrical connection point (see Technical data) must not be exceeded.Contact your electricity supplier in the case of any uncertainties regarding the mains grid impedance at your electrical connection point.For connected loads, see technical data and type plate.
The electrical connection must be carried out by an electrician and comply with IEC 60364-1.
All live parts, cables and devices in the work area must be in proper condition and be protected against water jets.
Danger of death from electric shock.
If the device is operated at a socket without an error current circuit breaker or without a protective contact (earthing), there is a danger of death from electric shock in the event of a fault!
Only operate the device at sockets with an earthing contact and with an error current circuit breaker with a nominal fault current of max. 30 mA.Design the water inlet for continuous operation.
Fit the water supply line with a shut-off valve and connect it to the high-pressure unit via a flexible pressure hose.
If the line cross-section is too small or the inlet pressure is too low, the result is a water shortage.
If the inlet pressure is too high or there are pressure peaks in the line system, always connect a pressure reducer upstream. A water drain must be available at the installation site.
If the "Solenoid valve water inlet" attachment kit is installed, the valve blocks the water inlet until the device is switched on.
Observe the relevant national regulations when installing the high-pressure lines.
The connection between the permanently installed pipework and the device must be a high-pressure hose line.
Lay the permanently installed pipework as straight as possible. Lay high-pressure pipelines in accordance with regulations, taking into account length changes due to heat and pressure effects, using dampened sliding and fixed clamps.
In order to minimise pressure losses in the high-pressure lines, the following recommendations should be observed:
Pipelines: Nominal width DN 15 Hose lines: Nominal width DN 8hose lines HD 17-15 St (H): DN 10For the above-mentioned guide values, the pipework length and the number of changes of direction and fittings must also be taken into account.
Device with ANTI!Twist: Attach the yellow high-pressure hose connection to the high-pressure gun.
The EASY!Lock system connects components quickly and safely via a single turn of the quick-release thread.
Connect the spray lance to the high-pressure gun and hand-tighten (EASY!Lock).
Plug the high-pressure nozzle onto the spray lance.
Fit the union nut and hand-tighten (EASY!Lock).
Device without a hose reel: Connect the high-pressure hose to the high-pressure gun and high-pressure connection of the device and tighten hand-tight (EASY!Lock).
Device with a hose reel: Connect the high-pressure hose to the high-pressure gun and hand-tighten (EASY!Lock).
Rolled-up high-pressure hose
Risk of damage
Fully unroll the high-pressure hose before starting operation.Set up the containers so that the lower level of the detergent is not more than 1.5 m below the base of the device and the upper level is not above the base of the device.
Remote controls can be connected between the device and the tapping points. These allow the device to be operated directly at the tapping point.
Various mounting kits for remote controls are available depending on the application.
Function | Description | |
---|---|---|
![]() | Reset | After the standby time has elapsed, the device can be restarted directly at the tapping point. |
![]() | Emergency off | |
![]() | On/Off + detergent (turn switch) Single workstation | Switching the device on and off at the tapping point. Selection of whether detergent should be added: No admixture, admixture RM 1 or admixture RM 2, as set on the device. |
![]() | On/Off + detergent (push buttons) up to 5 spots | Switching the device on and off at the tapping point. Selection of whether detergent should be added: No admixture, admixture RM 1 or admixture RM 2 (option), as set on the device. |
Risk of injury
Damaged components can lead to injuries when operating the device.
Check that the device, accessories, supply lines and connections are in perfect condition. Do not use the device if it is not in perfect condition.Ensure the water inlet is OK.
Remove the detergent suction from the device.
Ensure the power supply is OK.
For connected loads, see technical data and type plate.
The electrical connection must be carried out by an electrician and comply with IEC 60364-1.
The system care tank is only available with the HD St... H is present.
RM 110 prevents calcification of the device and pipelines in the presence of hard water.
Water hardness (°dH) | Scale on the turn switch (1-10) | System care products to be used |
3...7 | 1 | RM 110 |
7...14 | 2 | RM 110 |
14...21 | 3 | RM 110 |
>21 | 4 | RM 110 |
Determine the local water hardness via the local supply company or with a hardness tester.
Remove the cover and set the system care using the turn switch on the control panel.
The system care is a highly effective agent for preventing calcification of the water lines when operating with calcareous tap water. This is drip-fed dosed into the float container.
The dosage is set to medium water hardness at the factory and can be adjusted to the water hardness on site if necessary.
Refill the system care.
Risk of injury
Risk of injury from escaping, possibly hot water stream!
Check the device for damage each time before use.Check the high-pressure hose, the pipework, the fittings and the spray lance for damage before each use.
Replace leaking components immediately and seal leaking joints.
Check the hose coupling for tight fit and leaks.
Check the filling level of the detergent container and top up with detergent if necessary.
Check the filling level of the system care and top up if necessary.
Actuate the safety lever and trigger.
The high-pressure gun opens.
Release the safety lever and trigger.
The high-pressure gun closes.
The device is equipped with a pressure switch. The motor only starts up when the high-pressure gun is open.
Open the water inlet.
Connect the mains plug.
Set the power switch to "I".
Unlock the high-pressure gun by pushing the high-pressure gun safety latch to the rear.
Open the high-pressure gun.
Risk of injury
The water jet coming out of the pressure control/flow control can cause injuries.
Make sure that the connection between the pressure control/flow control and the steel pipe does not come loose.Set the working pressure and water quantity by turning the pressure control/flow control.
At the lowest flow rate, the waste heat from the motor heats the water to approx. 15 °C.
Risk of damage as a result of incorrect nozzle
Vehicle tyres can be damaged when cleaning with a round jet.
Always clean vehicle tyres with a flat jet nozzle (25°) and a spray distance of at least 30 cm.We recommend the following nozzles, depending on the device and the cleaning task:
Nozzle | Spray angle | Pressure (MPa) |
---|---|---|
HD 8/18-4 St (H) | ||
045 | 40° | 17 |
043 | 25° | 18 |
045 | 0° | 17 |
HD 10/21-4 St | ||
050 | 40° | 21 |
050 | 25° | 21 |
050 | 0° | 21 |
HD 10/19-4 St H | ||
045 | 40° | 17 |
043 | 25° | 18 |
045 | 0° | 17 |
HD 13/18-4 St | ||
075 | 40° | 16 |
070/072 | 25° | 17-18 |
075 | 0° | 16 |
HDS 17/15-4 St | ||
105 | 25° | 15 |
110 | 0° | 13 |
HDS 17/12-4 St (H) | ||
115 | 25° | 12 |
125 | 25° | 10 |
Risk of injury from detergent
Serious damage to health due to improper use of detergents.
Observe the detergent manufacturer's safety data sheet.Wear the prescribed personal protective gear.KÄRCHER detergents ensure fault-free operation. Ask us for advice, request our catalog or our detergent information sheets.
Hang the detergent suction hose in a container with detergent.
Set the detergent dosing valve to the desired dosage. The dosage is set in stages from 0 (no detergent) to 6 (highest dosage).
Spray the detergent sparingly on the dry surface and let it work for a while (do not let it dry).
Rinse off the loosened dirt with the high-pressure jet.
The cup foam lance must be flushed after use to prevent the formation of detergent deposits.
Unscrew the container.
Pour the remaining detergent back into the original packaging.
Fill the container with clear water.
Screw the container onto the cup foam lance nozzle.
Operate the cup foam lance for approx. 1 minute to flush the detergent residue.
Empty the container.
Immerse the filter in clear water.
Turn the dosing valve to the highest detergent concentration.
Start the device and rinse clear for one minute.
As an alternative to dosing detergent at the device, detergent can also be added directly at the dispensing points.
Various options are available for this, e.g.a cup foam lance.
Risk of injury from detergent
Health risk due to incorrect handling of detergents.
Adhere to the safety instructions stated on the detergent packaging.Risk of damage from unsuitable detergents
Using unsuitable detergents may damage the device and the item being cleaned.
Use only detergents approved by KÄRCHER.Observe the dosing recommendations and notes provided with the detergent.Use detergents sparingly to help conserve the environment.KÄRCHER detergents ensure fault-free operation. Ask us for a consultation, request our catalogue or our detergent information sheets.
Unscrew the container.
Plug the desired gate into the suction hose.
Fill the detergent into the container.
Screw the container onto the foam nozzle.
Disconnect the spray lance from the high-pressure gun.
Connect the cup foam lance to the high-pressure gun and hand-tighten.
Start up the high-pressure cleaner.
Release the trigger.
The device switches off.
Push the safety latch forwards.
The high-pressure gun is secured.
After the interruption
Push the safety latch backwards.
The high-pressure gun is unlocked.
Open the high-pressure gun.
The device switches itself on again.
Readiness time
The operational readiness period starts when the high-pressure gun is closed. The device can no longer be started by opening the high-pressure gun if this operational readiness period (30 minutes) expires. The indicator light flashes green.
To restart, briefly turn the device switch to "0" and then back to "I".
The standby time can be set by Customer Service.
Restart standby time
Set the power switch to "0".
Wait for a short time.
Set the power switch to "I".
Close the water inlet.
Open the high-pressure gun.
Switch on the pump with the power switch and let it run for 5-10 seconds.
Close the high-pressure gun.
Set the trigger to "0/OFF".
Close the stopcock on the water inlet and, if necessary, also close other stopcocks at the tapping points
Remove the water connection.
Actuate the high-pressure guns at the tapping points until the system is depressurised.
Lock the high-pressure guns by pushing the safety latch forwards.
Risk of damage!
Damage to the device and accessories due to freezing water.
Completely empty the device and accessories after each use.Protect the device and accessories from temperatures below or equal to 0 °C (32 °F).Disconnect the water supply from the device.
Remove the high-pressure hose from the device.
Switch the device on ("I/ON").
Wait for a maximum of 1 minute until no more water escapes from the high-pressure connection.
Switch off the device ("0/OFF").
Store the device and accessories in a frost-protected room.
Observe the handling instructions of the anti-freeze manufacturer.
Fill commonly available antifreeze all the way to the top of the float container.
Place a catch pan under the high-pressure outlet.
Switch on the device and allow it to run until the float container water shortage safeguard activates and the device switches off.
This also provides a certain degree of corrosion protection.
Turn the main switch to position “0”.
Close the water inlet.
Actuate the high-pressure gun until the device is completely depressurised.
Risk of injury, risk of damage
Be aware of the weight of the device during transportation.When transporting in vehicles, secure the device against slipping and tipping over according to the applicable guidelines.
Risk of injury or damage due to non-observance of the weight
Be aware of the weight of the device during storage.Operator: Work labelled with "Operator" may only be performed by instructed persons capable of operating and maintaining high-pressure systems.
Customer Service: Work labelled with "Customer service" may only be performed by KÄRCHER customer service technicians or KÄRCHER-authorised technicians.
We recommend that you choose a service contract to ensure reliable operation of the device. Please contact your KÄRCHER customer service department responsible.
Check the high-pressure gun.
Check the mains cable.
Check the filling level of the detergent containers.
Check the filling level of the system care.
Check the high-pressure hoses.
Risk of damage due to milky oil
Operation with milky oil can lead to damage to the device.
If the oil is milky, inform the authorised Customer Service immediately.Check the system for leaks.
Check the appearance and level of the pump oil.
Check the vibration dampener.
Clean the fresh water filter.
Check the float valve.
Check the automatic switch-on.
Re-tighten the hose clips.
Check the system for limescale.
Change the oil.
Carry out a safety inspection.
Switch the device on "I/ON".
Unlock the lever of the high-pressure gun.
Press the lever of the high-pressure gun.
The device switches on.
Allow the device for run a maximum of 2 minutes until the water escaping from the high-pressure gun is free of air bubbles.
Release the lever of the high-pressure gun.
Lock the lever of the high-pressure gun.
Deposits accumulating in the pipelines increase the flow resistance and the motor load becomes too high.
Flammable gases
Risk of explosion
Do not smoke during the descaling process.Ensure good ventilation.Acids
Risk of acid burns
Wear safety goggles and protective gloves.According to legal regulations, only approved boiler solvents with a test certificate may be used for descaling.
RM 101
Descaling the float container
Close the water inlet.
Remove the float container lid.
Detach the hose from the suction side of the pump to the float container on the pump side.
Close the free end of the hose.
Fill a 7-percent descaling solution.
After descaling, remove all residues from the container.
Descaling the high-pressure system
Disconnect the high-pressure hose at the piping network supply point and hang it in the float container.
Operate for a short time in recirculation mode with the descaling acid mixture prepared in the container, allow to take effect, rinse.
For the purposes of corrosion protection and neutralising acid residues, we recommend then pumping an alkaline solution (e.g. RM 81) through the device.
Close the water inlet.
Release the screws of the cover and remove the cover.
Unscrew the filter casing in front of the pump and remove the water filter.
Clean the filter and replace if necessary
Mount the device in reverse order.
Inadvertently starting up device, touching live components
Risk of injury, electric shock
Switch off the device before performing any work on the device.Remove the mains plug.Have all checks and work on electrical parts performed by a qualified electrician.In case of any malfunctions not mentioned in this chapter, contact the authorised Customer Service.Operator: Work labelled with "Operator" may only be performed by instructed persons capable of operating and maintaining high-pressure systems.
Qualified electrician: Work labelled with "Electrician" may only be performed by qualified electricians.
Customer Service: Work labelled with "Customer service" may only be performed by KÄRCHER customer service technicians or KÄRCHER-authorised technicians.
Cause:
Nozzle is clogged.
Remedy:
Operator
Clean the nozzle.
Cause:
Water supply volume too low.
Remedy:
Operator
Check the water inlet.
Cause:
Dosage set too low.
Remedy:
Operator
Increase the dosage.
Cause:
Suction filter in the detergent container is dirty.
Remedy:
Operator
Clean the suction filter.
Cause:
The detergent suction hose is leaking.
Remedy:
Customer Service department
Replace the suction hose.
Cause:
Manual detergent dosing valve blocked or defective.
Remedy:
Customer Service department
Check valve, clean, replace if necessary.
Cause:
Wrong nozzle.
Remedy:
Operator
Change the nozzle.
Cause:
Air in high-pressure pump.
Remedy:
Operator
Vent the device.
Cause:
Suction pipeline system leaking.
Remedy:
Operator
Check the screw connections and hoses.
Cause:
Not enough water.
Remedy:
Operator
Ensure for sufficient water supply.
Cause:
Fresh water filter contaminated.
Remedy:
Operator
Clean the fresh water filter.
Cause:
High-pressure hose is leaking.
Remedy:
Customer Service department
Replacing the high-pressure hose.
Cause:
Pipeline system is leaking.
Remedy:
Customer Service department
Repair the pipeline system.
Cause:
Quantity control faulty.
Remedy:
Customer Service department
Check and repair volume control.
Cause:
Valve in the pump is defective.
Remedy:
Customer Service department
Replace valve.
Cause:
Vibration dampener is defective.
Remedy:
Customer Service department
Replace the vibration dampener.
Cause:
High-pressure pump draws in a small amount of air.
Remedy:
Customer Service department
Check the suction system and eliminate any leaks.
Cause:
Detergent container empty and detergent dosing activated.
Remedy:
Operator
Top up detergent or set detergent dosage to 0.
Cause:
Water supply temperature too high.
Remedy:
Operator
Lower the water temperature.
Cause:
Not enough water, water inlet/fresh water filter blocked.
Remedy:
Operator
Check the water inlet.
Clean the fresh water filter.
Cause:
Valve head or valve springs faulty.
Remedy:
Customer Service department
Replace the parts.
Cause:
Advance pressure pump scaled or faulty (only for HD St...H)
Remedy:
Operator
Check the advance pressure pump.
Cause:
Power switch is turned off
Remedy:
Operator
Switch on the power switch.
Cause:
On-site power supply is interrupted.
Remedy:
Operator
Restore the power supply.
Cause:
Pressure switch defective
Remedy:
Operator
Replace the pressure switch.
Cause:
The motor circuit breaker has tripped due to overcurrent or failure of one phase of the mains supply.
Remedy:
Qualified electrician/customer service
Check the voltage of the 3 phases.
Cause:
The motor circuit breaker is set incorrectly.
Remedy:
Qualified electrician/customer service
Set the motor circuit breaker according to the circuit diagram.
Cause:
Motor circuit breaker for controller and advance pressure pump has tripped.
Remedy:
Qualified electrician/customer service
Check the motor circuit breaker.
Cause:
Control fuse on transformer is defective.
Remedy:
Qualified electrician/customer service
Check cause, replace control fuse.
Cause:
Control board is faulty.
Remedy:
Customer Service department
Check control board, replace if necessary.
Cause:
Pressure switch or cable to pressure switch is defective.
Remedy:
Customer Service department
Replace the pressure switch or cable.
Cause:
The pump is drawing air through the emptied detergent container.
Remedy:
Operator
Refill detergent container, vent suction line.
Cause:
Pressure switch faulty.
Remedy:
Qualified electrician/customer service
Replace the pressure switch.
Service indicator light flashes 1x
Cause:
Leak in the high-pressure system / water shortage.
Remedy:
Operator
Check the high-pressure system and the connections for leaks.
Service indicator light flashes 2x
Cause:
Fault in the voltage supply or current consumption of the motor too high.
Remedy:
Operator
Check the power supply and the mains power supply circuit breaker.
Contact Customer Service.
Service indicator light flashes 3x
Cause:
Motor overloaded or overheated.
Remedy:
Operator
Set the power switch to "0".
Allow the device to cool down.
Switch the device on.
Cause:
Malfunction occurs repeatedly.
Remedy:
Customer Service
Contact Customer Service.
Service indicator light flashes 8x
Cause:
Communication fault.
Remedy:
Customer Service
Contact Customer Service.
Service indicator light lights up
Cause:
Maintenance required.
The device continues running.Remedy:
Customer Service department
Contact Customer Service.
Cause:
Nozzle is clogged.
Remedy:
Operator
Clean the nozzle.
Cause:
Water supply volume too low.
Remedy:
Operator
Check the water inlet.
Cause:
Dosage set too low.
Remedy:
Operator
Increase the dosage.
Cause:
Suction filter in the detergent container is dirty.
Remedy:
Operator
Clean the suction filter.
Cause:
The detergent suction hose is leaking.
Remedy:
Customer Service department
Replace the suction hose.
Cause:
Manual detergent dosing valve blocked or defective.
Remedy:
Customer Service department
Check valve, clean, replace if necessary.
Cause:
Wrong nozzle.
Remedy:
Operator
Change the nozzle.
Cause:
Air in high-pressure pump.
Remedy:
Operator
Vent the device.
Cause:
Suction pipeline system leaking.
Remedy:
Operator
Check the screw connections and hoses.
Cause:
Not enough water.
Remedy:
Operator
Ensure for sufficient water supply.
Cause:
Fresh water filter contaminated.
Remedy:
Operator
Clean the fresh water filter.
Cause:
High-pressure hose is leaking.
Remedy:
Customer Service department
Replacing the high-pressure hose.
Cause:
Pipeline system is leaking.
Remedy:
Customer Service department
Repair the pipeline system.
Cause:
Quantity control faulty.
Remedy:
Customer Service department
Check and repair volume control.
Cause:
Valve in the pump is defective.
Remedy:
Customer Service department
Replace valve.
Cause:
Vibration dampener is defective.
Remedy:
Customer Service department
Replace the vibration dampener.
Cause:
High-pressure pump draws in a small amount of air.
Remedy:
Customer Service department
Check the suction system and eliminate any leaks.
Cause:
Detergent container empty and detergent dosing activated.
Remedy:
Operator
Top up detergent or set detergent dosage to 0.
Cause:
Water supply temperature too high.
Remedy:
Operator
Lower the water temperature.
Cause:
Not enough water, water inlet/fresh water filter blocked.
Remedy:
Operator
Check the water inlet.
Clean the fresh water filter.
Cause:
Valve head or valve springs faulty.
Remedy:
Customer Service department
Replace the parts.
Cause:
Advance pressure pump scaled or faulty (only for HD St...H)
Remedy:
Operator
Check the advance pressure pump.
Cause:
Power switch is turned off
Remedy:
Operator
Switch on the power switch.
Cause:
On-site power supply is interrupted.
Remedy:
Operator
Restore the power supply.
Cause:
Pressure switch defective
Remedy:
Operator
Replace the pressure switch.
Cause:
The motor circuit breaker has tripped due to overcurrent or failure of one phase of the mains supply.
Remedy:
Qualified electrician/customer service
Check the voltage of the 3 phases.
Cause:
The motor circuit breaker is set incorrectly.
Remedy:
Qualified electrician/customer service
Set the motor circuit breaker according to the circuit diagram.
Cause:
Motor circuit breaker for controller and advance pressure pump has tripped.
Remedy:
Qualified electrician/customer service
Check the motor circuit breaker.
Cause:
Control fuse on transformer is defective.
Remedy:
Qualified electrician/customer service
Check cause, replace control fuse.
Cause:
Control board is faulty.
Remedy:
Customer Service department
Check control board, replace if necessary.
Cause:
Pressure switch or cable to pressure switch is defective.
Remedy:
Customer Service department
Replace the pressure switch or cable.
Cause:
The pump is drawing air through the emptied detergent container.
Remedy:
Operator
Refill detergent container, vent suction line.
Cause:
Pressure switch faulty.
Remedy:
Qualified electrician/customer service
Replace the pressure switch.
Service indicator light flashes 1x
Cause:
Leak in the high-pressure system / water shortage.
Remedy:
Operator
Check the high-pressure system and the connections for leaks.
Service indicator light flashes 2x
Cause:
Fault in the voltage supply or current consumption of the motor too high.
Remedy:
Operator
Check the power supply and the mains power supply circuit breaker.
Contact Customer Service.
Service indicator light flashes 3x
Cause:
Motor overloaded or overheated.
Remedy:
Operator
Set the power switch to "0".
Allow the device to cool down.
Switch the device on.
Cause:
Malfunction occurs repeatedly.
Remedy:
Customer Service
Contact Customer Service.
Service indicator light flashes 8x
Cause:
Communication fault.
Remedy:
Customer Service
Contact Customer Service.
Service indicator light lights up
Cause:
Maintenance required.
The device continues running.Remedy:
Customer Service department
Contact Customer Service.
The warranty conditions issued by our relevant sales company apply in all countries. We shall remedy possible malfunctions on your appliance within the warranty period free of cost, provided that a material or manufacturing flaw is the cause. In a warranty case, please contact your dealer (with the purchase receipt) or the next authorised customer service site.
Further information can be found at: www.kaercher.com/dealersearch
Further warranty information (if available) can be found in the service area of your local Kärcher website under "Downloads".
EU Declaration of Conformity |
We hereby declare that the product named below complies with the relevant provisions of the directives and regulations listed. This declaration is invalidated by any changes made to the product that are not approved by us.
Product: High-pressure cleaner ST
Type: 1.698-xxx
Type: 1.699-xxx
Directives and Regulations2006/42/EC (+2009/127/EC)
2014/30/EU
2014/68/EU
2011/65/EU
2009/125/EC
(EU) 2019/1781
Harmonised standards usedEN 60335-1
EN 60335-2-79
EN 55014-1: 2017 + A11: 2020
EN 55014-2: 1997 + A1: 2001 + A2: 2008
EN 61000-3-2: 2014
EN IEC 63000: 2018
HDS 8/18-4 ST; HDS 10/21-4 ST
EN 61000-3-3: 2013
HDS 13/20-4 ST
EN 61000-3-11: 2000
Name and addressDocumentation supervisor:
S. Reiser
Alfred Kärcher SE & Co. KG
Alfred-Kärcher-Str. 28 - 40
71364 Winnenden (Germany)
Tel.: +49 7195 14-0
Fax: +49 7195 14-2212
Winnenden, 2024/09/01
The undersigned act on behalf of and with the authority of the Board of Directors.
Alfred Kärcher SE & Co. KG
Alfred-Kärcher-Str. 28 - 40
71364 Winnenden (Germany)
Ph.: +49 7195 14-0
Fax: +49 7195 14-2212
Declaration of Conformity (UK) |
We hereby declare that the product named below complies with the relevant provisions of the directives and regulations listed. This declaration is invalidated by any changes made to the product that are not approved by us.
Product: High-pressure cleaner ST
Type: 1.698-xxx
Type: 1.699-xxx
Directives and RegulationsS.I. 2008/1597 (as amended)
S.I. 2016/1091 (as amended)
S.I. 2016/1105 (as amended)
S.I. 2012/3032 (as amended)
S.I. 2010/2617 (as amended)
(EU) 2019/1781
Designated standards usedEN 60335-1
EN 60335-2-79
EN 55014-1: 2017 + A11: 2020
EN 55014-2: 1997 + A1: 2001 + A2: 2008
EN 61000-3-2: 2014
EN IEC 63000: 2018
HDS 8/18-4 ST; HDS 10/21-4 ST
EN 61000-3-3: 2013
HDS 13/20-4 ST
EN 61000-3-11: 2000
Name and addressDocumentation supervisor:
S. Reiser
Alfred Kärcher SE & Co. KG
Alfred-Kärcher-Str. 28 - 40
71364 Winnenden (Germany)
Tel.: +49 7195 14-0
Fax: +49 7195 14-2212
Winnenden, 2024/09/01
The undersigned act on behalf of and with the authority of the Board of Directors.
Alfred Kärcher SE & Co. KG
Alfred-Kärcher-Str. 28 - 40
71364 Winnenden (Germany)
Ph.: +49 7195 14-0
Fax: +49 7195 14-2212
Electrical connection | |
Voltage | 400 V |
Phase | 3 ~ |
Frequency | 50 Hz |
Power rating | 5,5 kW |
Power protection (slow-blow, char. C) | 16 A |
Degree of protection | IPX5 |
Protection class | I |
Maximum permissible mains grid impedance | - Ω |
Water connection | |
Input amount (min.) | 1000 (16,7) l/h (l/min) |
Feed pressure (max.) | 1 (10) MPa (bar) |
Input temperature (max.) | 60 °C |
Device performance data | |
Water flow rate | 800 (13,3) l/h (l/min) |
Water operating pressure with standard nozzle | 18 (180) MPa (bar) |
Operating pressure (max.) | 24 (240) MPa (bar) |
Detergent flow rate | 45 (0,75) l/h (l/min) |
High-pressure gun recoil force | 42 N |
Nozzle size of standard nozzle | 43 |
Dimensions and weights | |
Typical operating weight | 74 kg |
Length | 856 mm |
Width | 605 mm |
Height | 649 mm |
High-pressure pump | |
Filling quantity | 0,5 l |
Oil type | 15W40 |
Determined values in acc. with EN 60335-2-79 | |
Sound pressure level LpA | 76 dB(A) |
Uncertainty KpA | 3 dB(A) |
Sound power level LWA + uncertainty KWA | 92 dB(A) |
Hand-arm vibration value | 3,2 m/s2 |
Uncertainty K | 0,8 m/s2 |
Electrical connection | |
Voltage | 400 V |
Phase | 3 ~ |
Frequency | 50 Hz |
Power rating | 5,5 kW |
Power protection (slow-blow, char. C) | 16 A |
Degree of protection | IPX5 |
Protection class | I |
Maximum permissible mains grid impedance | - Ω |
Water connection | |
Input amount (min.) | 1000 (16,7) l/h (l/min) |
Feed pressure (max.) | 1 (10) MPa (bar) |
Input temperature (max.) | 85 °C |
Device performance data | |
Water flow rate | 800 (13,3) l/h (l/min) |
Water operating pressure with standard nozzle | 18 (180) MPa (bar) |
Operating pressure (max.) | 24 (240) MPa (bar) |
Detergent flow rate | 50 (0,83) l/h (l/min) |
High-pressure gun recoil force | 42 N |
Nozzle size of standard nozzle | 43 |
Dimensions and weights | |
Typical operating weight | 81 kg |
Length | 857 mm |
Width | 605 mm |
Height | 677 mm |
High-pressure pump | |
Filling quantity | 0,5 l |
Oil type | 15W40 |
Determined values in acc. with EN 60335-2-79 | |
Sound pressure level LpA | 76 dB(A) |
Uncertainty KpA | 3 dB(A) |
Sound power level LWA + uncertainty KWA | 92 dB(A) |
Hand-arm vibration value | 3,2 m/s2 |
Uncertainty K | 0,8 m/s2 |
Electrical connection | |
Voltage | 400 V |
Phase | 3 ~ |
Frequency | 50 Hz |
Power rating | 7,5 kW |
Power protection (slow-blow, char. C) | 16 A |
Degree of protection | IPX5 |
Protection class | I |
Maximum permissible mains grid impedance | - Ω |
Water connection | |
Input amount (min.) | 1300 (21,7) l/h (l/min) |
Feed pressure (max.) | 1 (10) MPa (bar) |
Input temperature (max.) | 60 °C |
Device performance data | |
Water flow rate | 1000 (16,7) l/h (l/min) |
Water operating pressure with standard nozzle | 21 (210) MPa (bar) |
Operating pressure (max.) | 27 (270) MPa (bar) |
Detergent flow rate | 58 (0,97) l/h (l/min) |
High-pressure gun recoil force | 57 N |
Nozzle size of standard nozzle | 50 |
Dimensions and weights | |
Typical operating weight | 80 kg |
Length | 856 mm |
Width | 605 mm |
Height | 649 mm |
High-pressure pump | |
Filling quantity | 0,65 l |
Oil type | 15W40 |
Determined values in acc. with EN 60335-2-79 | |
Sound pressure level LpA | 76 dB(A) |
Uncertainty KpA | 3 dB(A) |
Sound power level LWA + uncertainty KWA | 92 dB(A) |
Hand-arm vibration value | 3,8 m/s2 |
Uncertainty K | 1,3 m/s2 |
Electrical connection | |
Voltage | 400 V |
Phase | 3 ~ |
Frequency | 50 Hz |
Power rating | 7 kW |
Power protection (slow-blow, char. C) | 16 A |
Degree of protection | IPX5 |
Protection class | I |
Maximum permissible mains grid impedance | 0.0452 + j0.0283 Ω |
Water connection | |
Input amount (min.) | 1300 (21,7) l/h (l/min) |
Feed pressure (max.) | 1 (10) MPa (bar) |
Input temperature (max.) | 85 °C |
Device performance data | |
Water flow rate | 1000 (16,7) l/h (l/min) |
Water operating pressure with standard nozzle | 19 (190) MPa (bar) |
Operating pressure (max.) | 25 (250) MPa (bar) |
Detergent flow rate | 40 (0,66) l/h (l/min) |
High-pressure gun recoil force | 54 N |
Nozzle size of standard nozzle | 54 |
Dimensions and weights | |
Typical operating weight | 95 kg |
Length | 857 mm |
Width | 605 mm |
Height | 677 mm |
High-pressure pump | |
Filling quantity | 0,65 l |
Oil type | 15W40 |
Determined values in acc. with EN 60335-2-79 | |
Sound pressure level LpA | 76 dB(A) |
Uncertainty KpA | 3 dB(A) |
Sound power level LWA + uncertainty KWA | 92 dB(A) |
Hand-arm vibration value | 5 m/s2 |
Uncertainty K | 1,9 m/s2 |
Electrical connection | |
Voltage | 400 V |
Phase | 3 ~ |
Frequency | 50 Hz |
Power rating | 8,8 kW |
Power protection (slow-blow, char. C) | 16 A |
Degree of protection | IPX5 |
Protection class | I |
Maximum permissible mains grid impedance | 0.0452 + j0.0283 Ω |
Water connection | |
Input amount (min.) | 1500 (25) l/h (l/min) |
Feed pressure (max.) | 1 (10) MPa (bar) |
Input temperature (max.) | 60 °C |
Device performance data | |
Water flow rate | 1300 (21,7) l/h (l/min) |
Water operating pressure with standard nozzle | 18 (180) MPa (bar) |
Operating pressure (max.) | 24 (240) MPa (bar) |
Detergent flow rate | 45 (0,75) l/h (l/min) |
High-pressure gun recoil force | 69 N |
Nozzle size of standard nozzle | 72 |
Dimensions and weights | |
Typical operating weight | 87 kg |
Length | 856 mm |
Width | 605 mm |
Height | 649 mm |
High-pressure pump | |
Filling quantity | 0,65 l |
Oil type | 15W40 |
Determined values in acc. with EN 60335-2-79 | |
Sound pressure level LpA | 76 dB(A) |
Uncertainty KpA | 3 dB(A) |
Sound power level LWA + uncertainty KWA | 92 dB(A) |
Hand-arm vibration value | 5,7 m/s2 |
Uncertainty K | 1,5 m/s2 |
Electrical connection | |
Voltage | 400 V |
Phase | 3 ~ |
Frequency | 50 Hz |
Power rating | 9 kW |
Power protection (slow-blow, char. C) | 16 A |
Degree of protection | IPX5 |
Protection class | I |
Maximum permissible mains grid impedance | 0.0452 + j0.0283 Ω |
Water connection | |
Input amount (min.) | 2000 (30,3) l/h (l/min) |
Feed pressure (max.) | 1 (10) MPa (bar) |
Input temperature (max.) | 60 °C |
Device performance data | |
Water flow rate | 1700 (28,3) l/h (l/min) |
Water operating pressure with standard nozzle | 15 (150) MPa (bar) |
Operating pressure (max.) | 21 (210) MPa (bar) |
Detergent flow rate | 43 (0,71) l/h (l/min) |
High-pressure gun recoil force | 82 N |
Nozzle size of standard nozzle | 105 |
Dimensions and weights | |
Typical operating weight | 90 kg |
Length | 856 mm |
Width | 605 mm |
Height | 649 mm |
High-pressure pump | |
Filling quantity | 1,2 l |
Oil type | 15W40 |
Determined values in acc. with EN 60335-2-79 | |
Sound pressure level LpA | 76 dB(A) |
Uncertainty KpA | 3 dB(A) |
Sound power level LWA + uncertainty KWA | 92 dB(A) |
Hand-arm vibration value | 5,2 m/s2 |
Uncertainty K | 1 m/s2 |
Electrical connection | |
Voltage | 400 V |
Phase | 3 ~ |
Frequency | 50 Hz |
Power rating | 7 kW |
Power protection (slow-blow, char. C) | 16 A |
Degree of protection | IPX5 |
Protection class | I |
Maximum permissible mains grid impedance | 0.0452 + j0.0283 Ω |
Water connection | |
Input amount (min.) | 2000 (30,3) l/h (l/min) |
Feed pressure (max.) | 1 (10) MPa (bar) |
Input temperature (max.) | 85 °C |
Device performance data | |
Water flow rate | 1700 (28,3) l/h (l/min) |
Water operating pressure with standard nozzle | 12 (120) MPa (bar) |
Operating pressure (max.) | 18 (180) MPa (bar) |
Detergent flow rate | 15 (0,25) l/h (l/min) |
High-pressure gun recoil force | 73 N |
Nozzle size of standard nozzle | 125 |
Dimensions and weights | |
Typical operating weight | 97 kg |
Length | 857 mm |
Width | 605 mm |
Height | 677 mm |
High-pressure pump | |
Filling quantity | 1,2 l |
Oil type | 15W40 |
Determined values in acc. with EN 60335-2-79 | |
Sound pressure level LpA | 76 dB(A) |
Uncertainty KpA | 3 dB(A) |
Sound power level LWA + uncertainty KWA | 92 dB(A) |
Hand-arm vibration value | 6,2 m/s2 |
Uncertainty K | 1,1 m/s2 |
System type: | Manufacturer no: | Initial startup on: |
Test performed on: | ||
Findings: | ||
Signature | ||
Test performed on: | ||
Findings: | ||
Signature | ||
Test performed on: | ||
Findings: | ||
Signature | ||
Test performed on: | ||
Findings: | ||
Signature |
2-2-NN-A4-GS-20906