Cleaning a biogas plant
Agricultural substrates from grass, grain or maize silage, slurry or solid manure. Biogas plants enable farmers to make good use of products from their farm. This is a good source of renewable energy which is even used by grid operators as a buffer for the power supply when several biogas plants are interconnected. Efficient heat recovery is also possible. Properly cleaning an anaerobic digestion plant is important for smooth operation and to retain the plant's value. This involves cleaning the storage facilities for the substrate, the fermenter, the secondary fermenter and the periphery. It also helps keep realisable yields more stable.
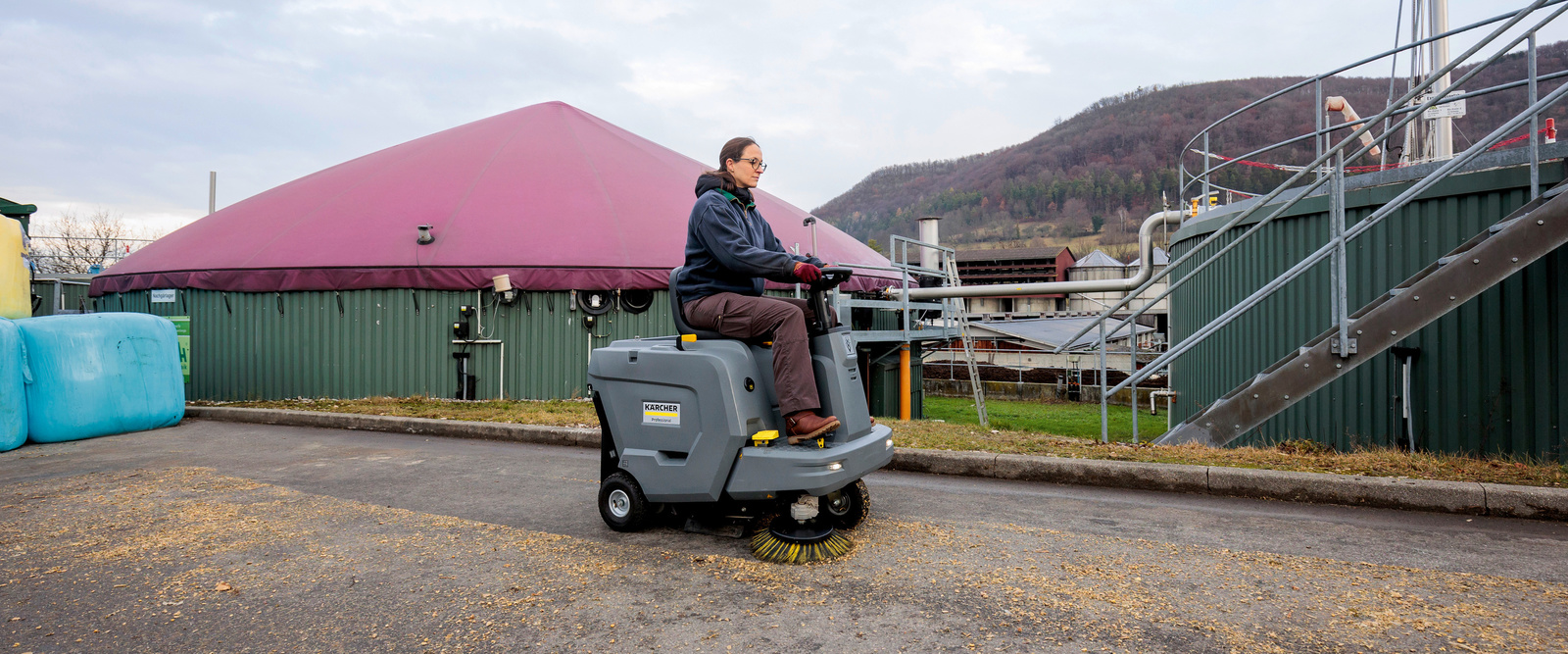
Biogas facilities: A short overview of the makeup and environment
An essential component of a biogas plant is the fermenter. Substrate made from agricultural products such as liquid manure, maize, grain or grass silage is fermented by bacterial cultures inside the fermenter. The biogas produced in this process consists mainly of methane (50-65 %) and carbon dioxide (35-50 %). One or more generators produce electricity from this, which is fed into the grid, or heats the farm itself.
Alternatively, farmers can refine the gas through a biogas upgrading plant and feed it directly into the natural gas grid. However, this is only worthwhile for large plants. The substrate left over from fermentation goes into the secondary fermenter or the secondary fermentation tank, where it is reintroduced into the agricultural cycle as fertiliser.
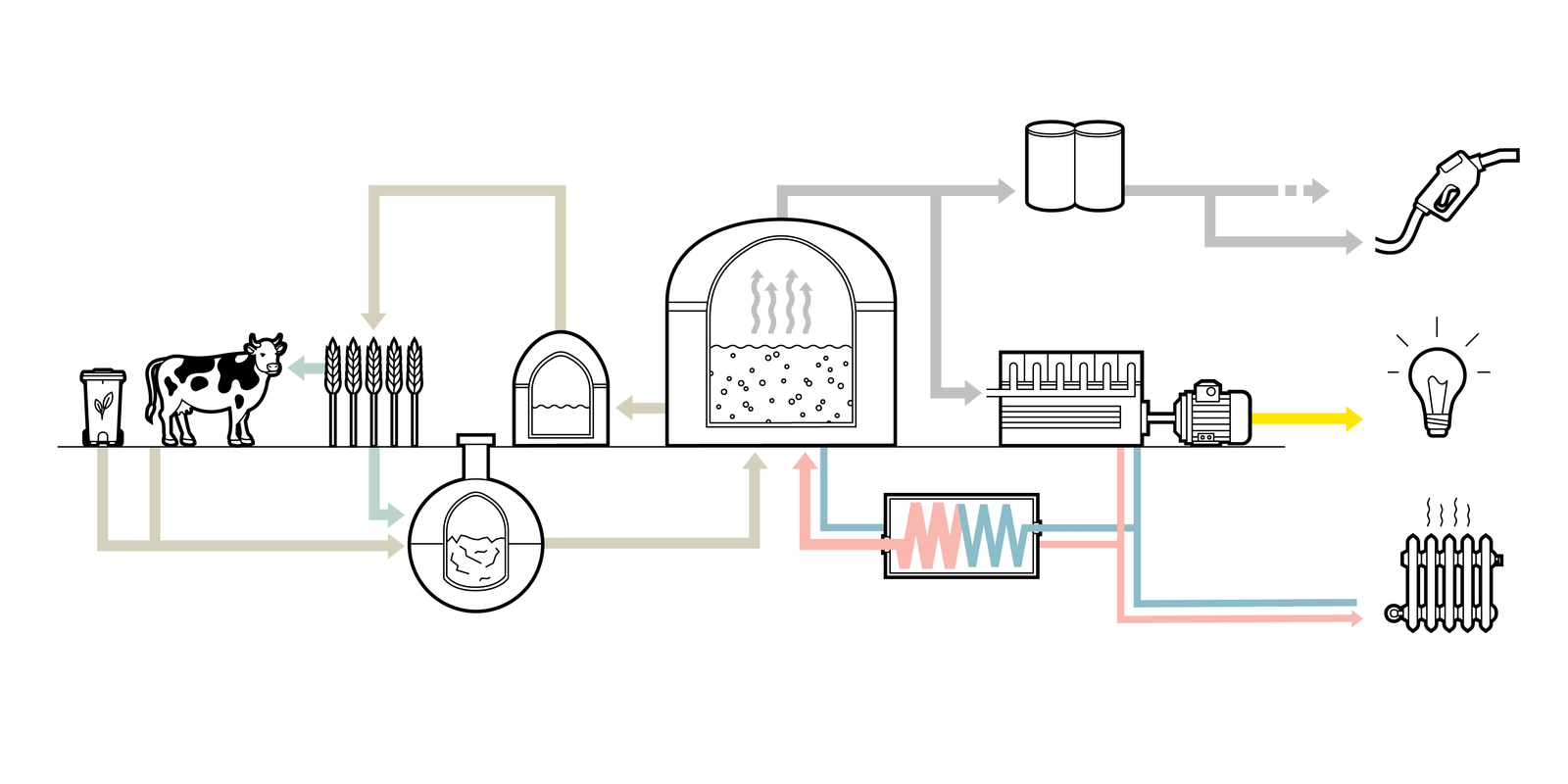
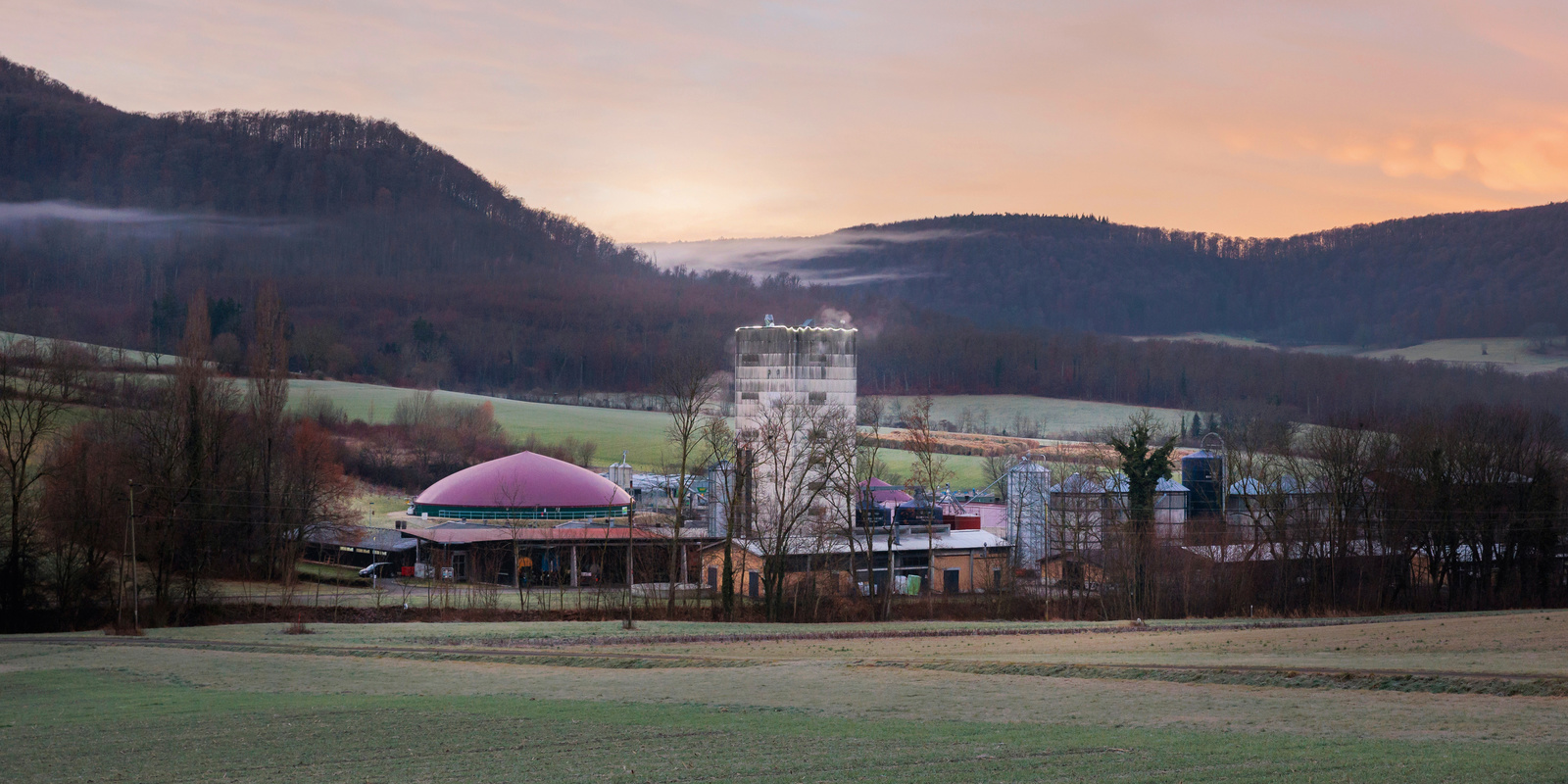
Cleaning an anaerobic digestion plant at a glance
In order to carry out the necessary cleaning work correctly, you should think about all elements of the system. This includes the storage facilities for the substrate, the fermenter, the generator and control rooms. The auxiliary equipment includes the machines that are in use around the biogas plant and, depending on the conditions on site, systems that use the waste heat from the gas engines for heating circuits.
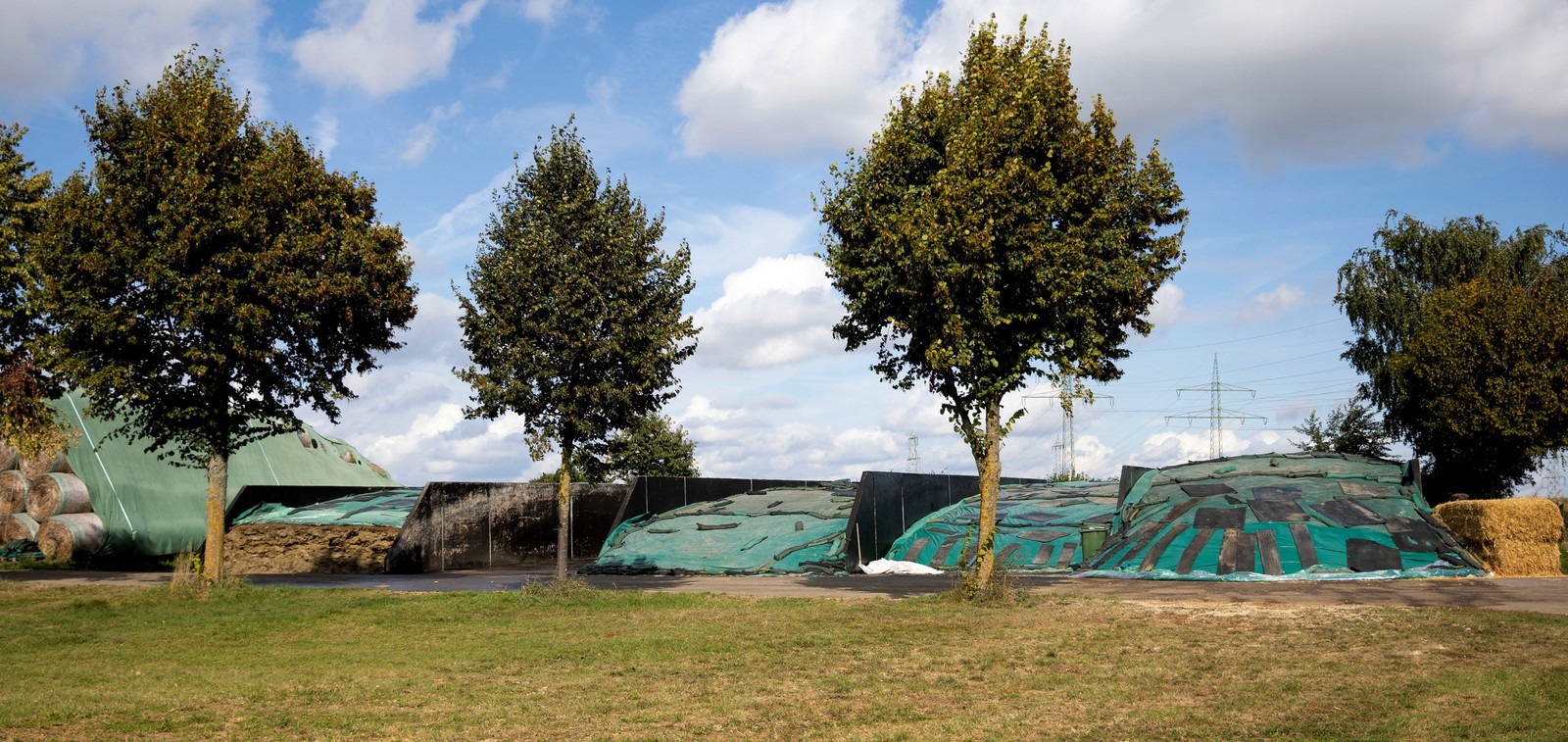
Cleaning the substrate storage facilities
A sufficient amount of substrate is needed to ensure a continuous supply. The amount depends on the size and type of operation, as well as the size of the biogas plant. Storage facilities for the substrate are usually constructed in a similar way to mobile or flat silos so that cleaning requirements and procedures are also similar. The surfaces of the storage facilities are coated to withstand seepage and mechanical stress. But over time, external influences cause porous spots to form. Substrate residues adhere very well to these, making an ideal environment for germs and moulds.
The cleaning process
A pressure washer with a pressure of up to 250 bar and water volumes of up to 2,500 litres is suitable for cleaning a substrate store. The high cleaning and flushing capacity efficiently remove and transport stubborn dirt away. Accessories recommended are a dirt blaster, also known as a rotary nozzle, and, for storage facilities with high walls, long lances with an articulated joint, telescopic lances or, depending on the space available, a surface cleaner. The best results are achieved at a working distance of about 40 centimetres, cleaning the floor before and afterwards.
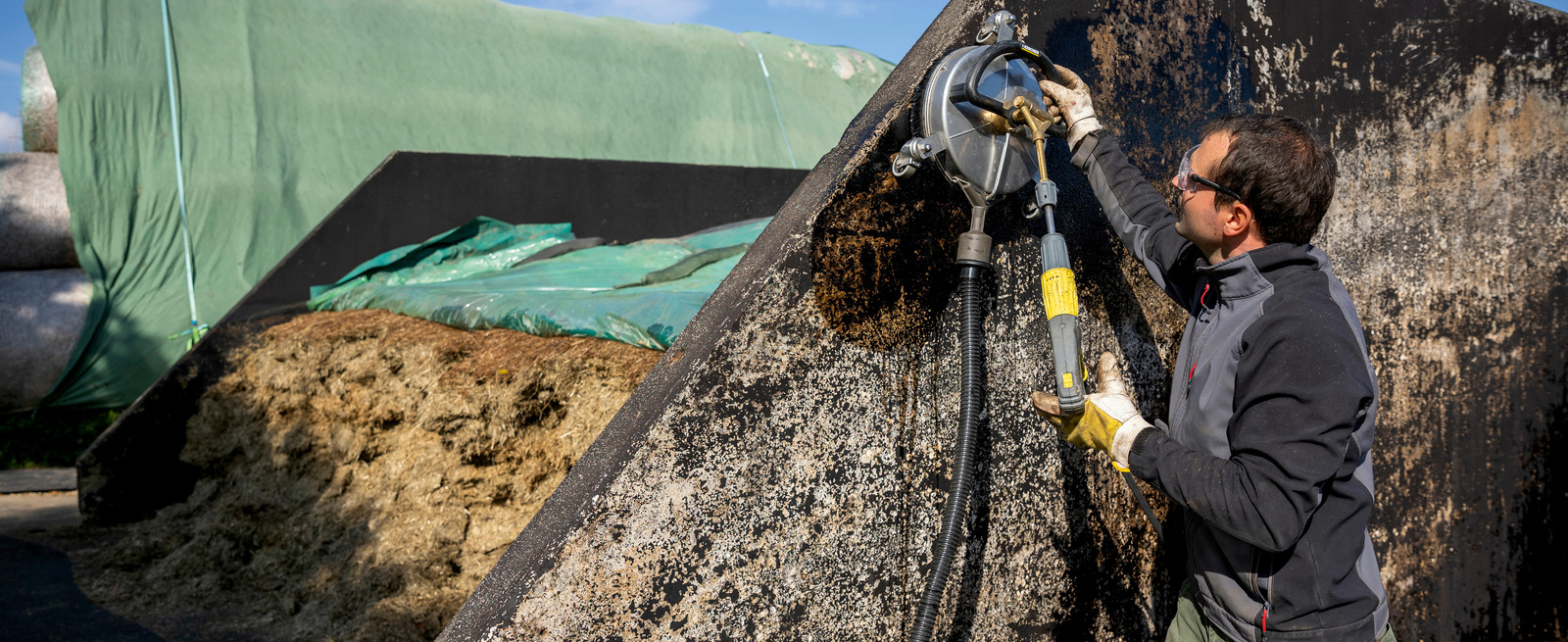
Tip 1: Required Personal Protective Equipment
.
Tip 2: The right cleaning rota
Cleaning should be done annually for agricultural substrates such as grass or maize, just before refilling. If slurry or solid manure is used as part of the substrate, cleaning takes place without a fixed cycle, when maintenance or repairs are due. In general, repairing damage or renewing the coating is only possible with a cleaned storage facility.
Cleaning the fermenter and secondary fermenter tanks in biogas plants and increasing yields
There are various recommendations regarding the cleaning cycle for the fermenter in a biogas plant. Usually, cleaning is due every five to eight years, as more and more solids settle at the bottom over time. This reduces the volume and the gas yield of the digester, which makes it much more difficult to use the plant effectively and economically. Another reason for cleaning the fermenter is the need to carry out repairs to the facilities in the lower area of the tank or to rehabilitate the concrete.
With heavy equipment and high pressure
First, the remaining substrate is pumped out as far as possible and the container is ventilated for at least 24 hours. After that, the deposits have to be removed with heavy equipment. This work with excavators or trucks with extraction systems is usually carried out by specialised service providers. When entering the container, a gas detector, breathing apparatus, rope protection and safety harness are part of the recommended PPE.
The final cleaning is done by a pressure washer, which should have a flushing capacity of 2,000 to 3,000 litres. Extension hoses are laid from the high-pressure generator, which is located outside the fermenter, to the work site. A longer lance offers better protection from flying dirt and also provides a comfortable working distance. The dirty water produced during cleaning can be channelled into the secondary fermenter, remaining in the process.
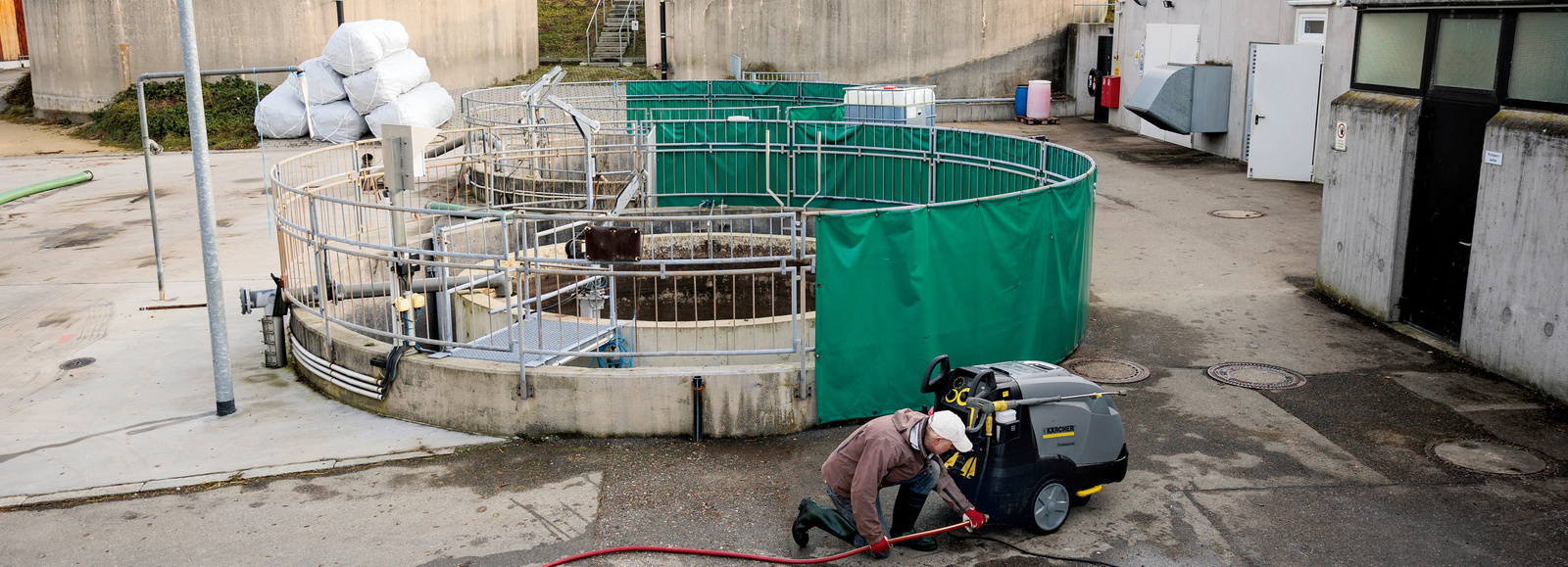
–Tip 1: Detailed cleaning with a wet and dry vacuum cleaner
If the fermenter equipment is to be repaired after cleaning, we recommend detailed cleaning with a wet and dry vacuum cleaner.
Tip 2: Wet clean the secondary fermenters
The secondary fermenter should also be wet cleaned if necessary. This task is usually also carried out by specialists who have climbing training and the necessary equipment.
Cleaning biogas plants: removing dirt and maintaining functionality in the generator and control rooms
The parameters for the fermenter, i.e. filling level, temperature, gas quality and other aspects, are monitored in the control room of the plant. It is usually located in the same building as the generator room. The rooms are soundproofed so that the noise of the large engines with several 100 kWh does not penetrate to the outside.
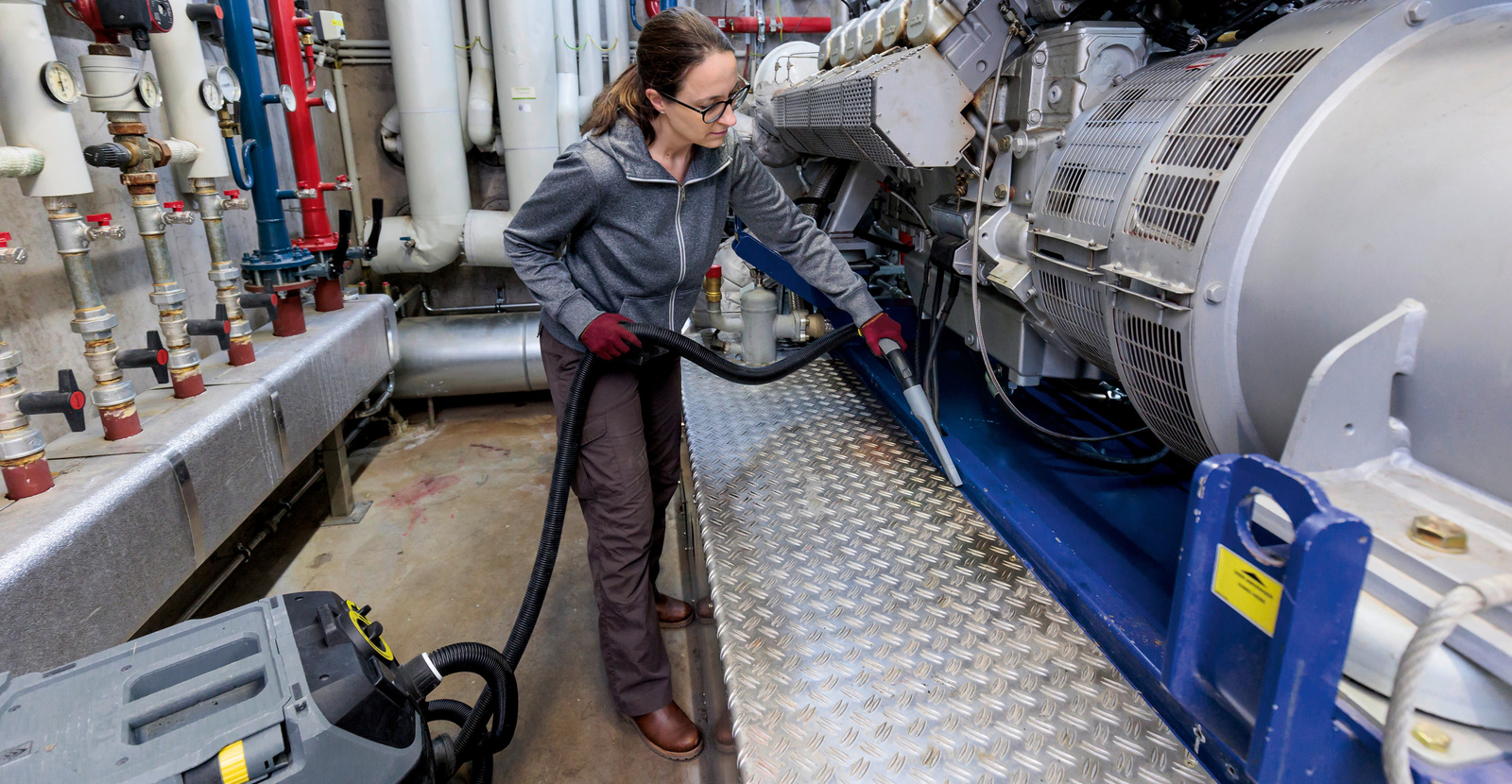
Remove dust, soot and residues
Although all systems are tested for impermeability, there is always a small degree of permeability. Over time, dust, soot and other residues accumulate everywhere in the generator room. Depending on the respective system, it is recommended to remove the dirt regularly by means of maintenance cleaning and to maintain functionality. A wet and dry vacuum cleaner is used for this purpose. This is also suitable for cleaning after maintenance work and can, for example, pick up oil that has dripped down. Any remaining dirt can then be washed off with a pressure washer or wiped out with a damp cloth.
Tip: Cleaning the floor in the control room
Regular room cleaning is also recommended for the control room. This includes vacuuming or dust mopping, surface cleaning and damp mopping as required.

Additional Info 1
Auxiliary machines around the biogas plant
Professional cleaning has a lot to do with maintaining value, and not only in agriculture. Both the biogas plant and the machines used within the transport chain represent high investment factors that need to be protected. Damage to regularly cleaned machines can be detected immediately, so that they are always ready for use and high repair costs resulting from defects can be avoided. Also, dirt cannot accumulate in sensitive areas and cause damage there itself. The following are suitable for cleaning machines around the biogas plant:
- a cold water pressure washer, if necessary in combination with a suitable cleaning agent,
- a hot water pressure washer achieves better results faster and reduces water consumption thanks to its high temperature. Drying is also faster.
- the pressure and amount of water depend on the object and degree of soiling, the working distance should be 20 to 30 centimetres from the surface.
Additional info 2
Use the waste heat for other purposes.
Generators produce electricity from biogas as well as waste heat, which can be used productively. You can dry wood and heat stables or residential buildings with it. In some cases, the waste heat is even fed into a local heating network, powering nearby residential or industrial areas. There is no special cleaning requirement for the systems of the local heating network itself, only the heated premises have to be cleaned if necessary. Depending on the circumstances, vacuum cleaners and/or pressure washers are used for this purpose.