Cleaning paint shops
Where a thorough approach really matters: cleaning paint shops is no walk in the park. Not only because every paint shop has its own unique setup, but also (and especially) because the smallest impurities in the painting process can often lead to imperfections in products. In light of this, it is imperative that the particular conditions are taken into account while also cleaning as efficiently and thoroughly as possible.
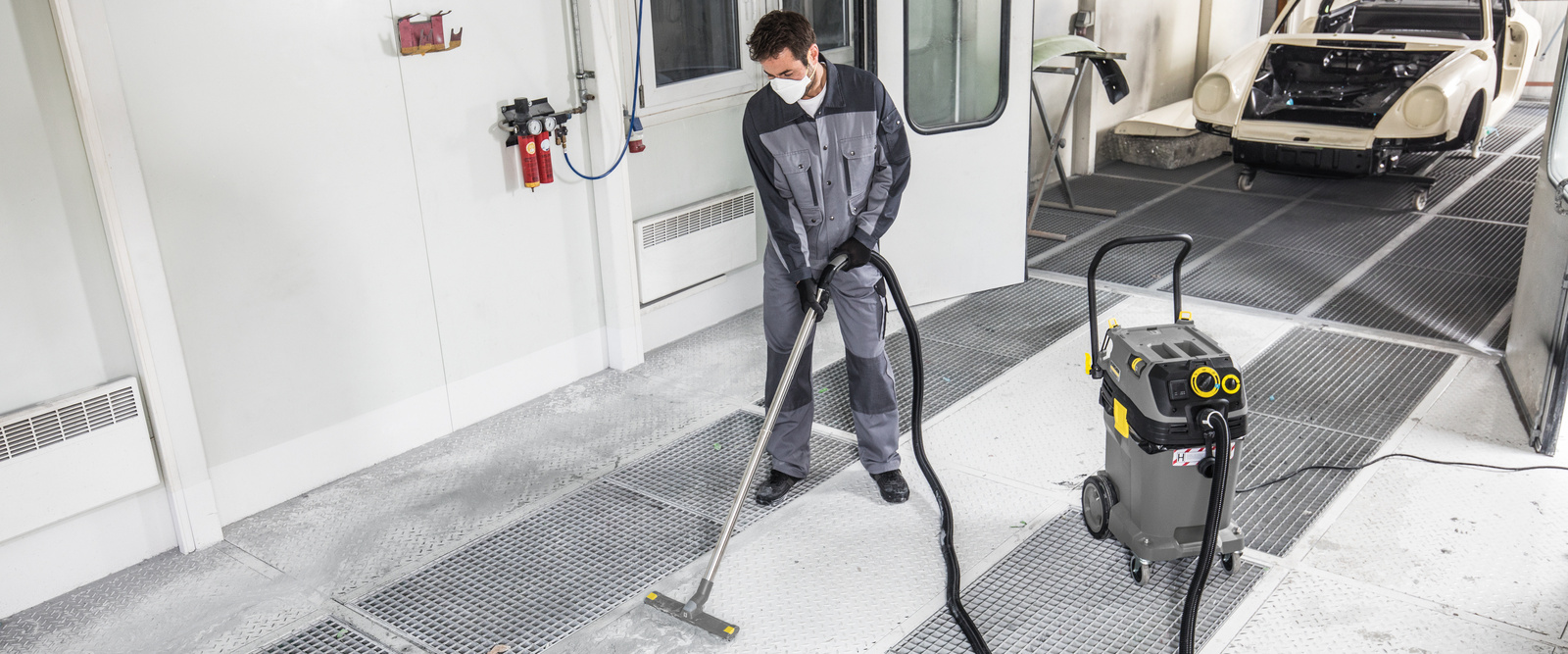
Cleanliness as the starting basis for immaculate results
Whether it's a smooth, flawless painted surface for a premium-quality end product or a simple coating for corrosion protection, the range of coatings applied in paint booths is wide, and the reasons for their application are diverse. While some processes do not require such precision, elsewhere even so much as a speck of dust in the wrong place can impair the finished article – all of which means that extreme care must be taken in the maintenance and cleaning of the paint shop. Nevertheless, cleaning processes in the context of a paint shop are always far from simple. After all, the applied coatings – whether paint, adhesive or something else – are generally designed to be hard-wearing and durable. Consequently, once they have dried, removing them is no easy matter and requires extensive expertise and customised cleaning solutions. However, cleaning is not just about achieving the best possible end result – the process must also account for other considerations, such as health. The efficiency of cleaning is also a key factor, since downtime during operational hours is best avoided.
Challenge accepted: how do you remove something that's designed to be permanent?
Cleaning paint shops brings with it its very own complexity. Soiling is particularly stubborn; over time, it becomes caked on and difficult to remove. What's more, paint shops can vary greatly in design.
No two paint shops are the same
If a professional is asked how to clean a paint shop, they will often answer with another question: what kind of paint shop exactly? After all, there are as many different types of paint shop as there are paint shops themselves, and the specific conditions are critical to how they are best cleaned. The first thing to do is to differentiate between the overall types of paint shop. For instance, is it a top coat or clear coat spraying system? Or perhaps only primer coat is applied there? A distinction must also be made between paint booths and dip tanks, and between wet and powder coating systems. All these different types bring with them different challenges. In addition to this fundamental distinction, it must also be considered that every paint shop has its own unique setup and, within this setup, its own unique complexity – depending on the industry in question and the intended purpose of the product once painted.
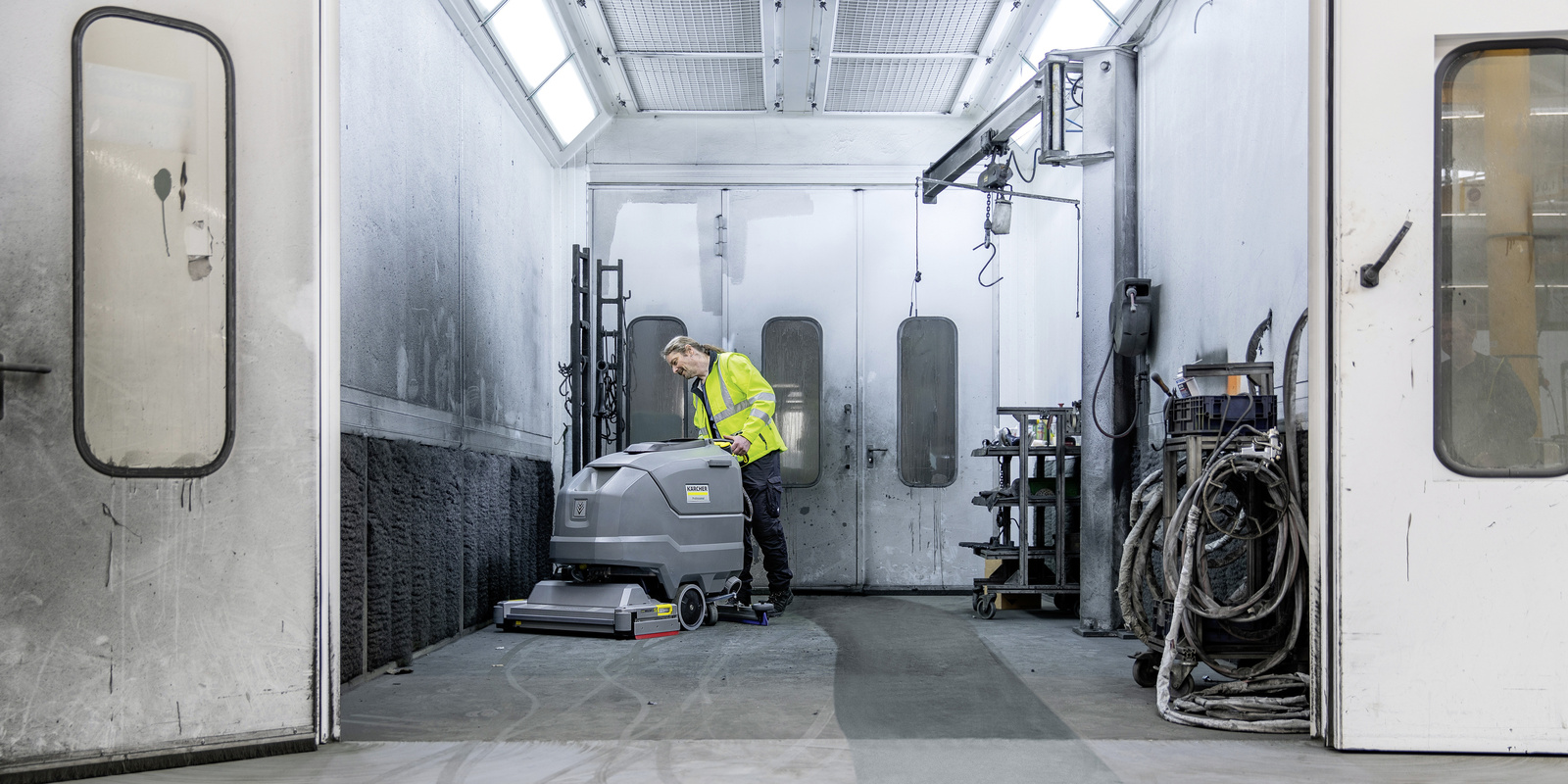
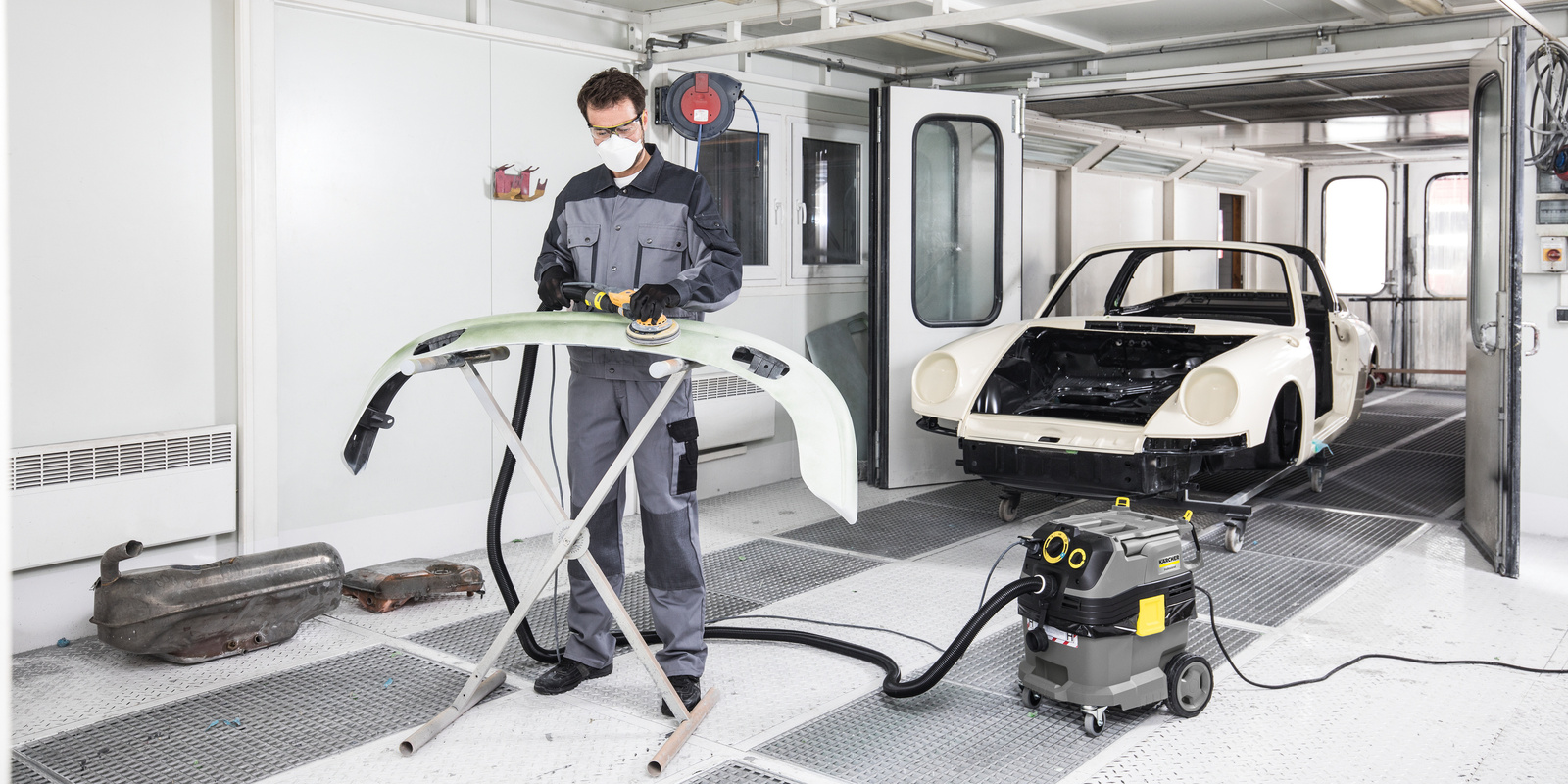
Different elements or facilities can play a role in the cleaning process. This includes everything that can be attributed to preparation and preparatory cleaning. Of central importance are the facilities in which the painting itself is carried out and the corresponding technology – for example, painting booths or painting rooms, dip tanks, application technology, conveyor technology, gratings, etc. In addition, facilities for drying and evaporation naturally also play a role. These are key to the overall process, since they are used, among other things, to extract the solvent that vaporises after the painting process. A basic distinction must be made between cleaning processes that have to be completed during the painting process – such as the extraction of dust – and periodic cleaning during downtime or
outside the painting process, for example to remove dried paint residues from machinery. For the latter, the cleaning intervals are generally based on external circumstances, such as plant holidays, batch changes or maintenance shutdowns.
As a general rule, due consideration should be given to personal protective equipment before cleaning operations commence. The equipment needed depends on the type of work being carried out – safety goggles, safety shoes (usually S2 or above), protective gloves and a respiratory mask with a filter for dust and paint mist are usually relevant for cleaning in paint shops. When using certain solvents, a sealed, forced-air respirator hood with oxygen supply may be necessary.
Many methods, one goal: flawless cleaning results
Various cleaning solutions are available to efficiently overcome the various challenges involved in cleaning paint shops with thorough results. For small elements, such as nozzles, which need to be cleaned straight after the painting process, chemical cleaning is a suitable method, whereby entire parts are individually immersed in chemical detergents. For more extensive cleaning processes in the booth and the drying room, however, the following solutions are particularly suitable:
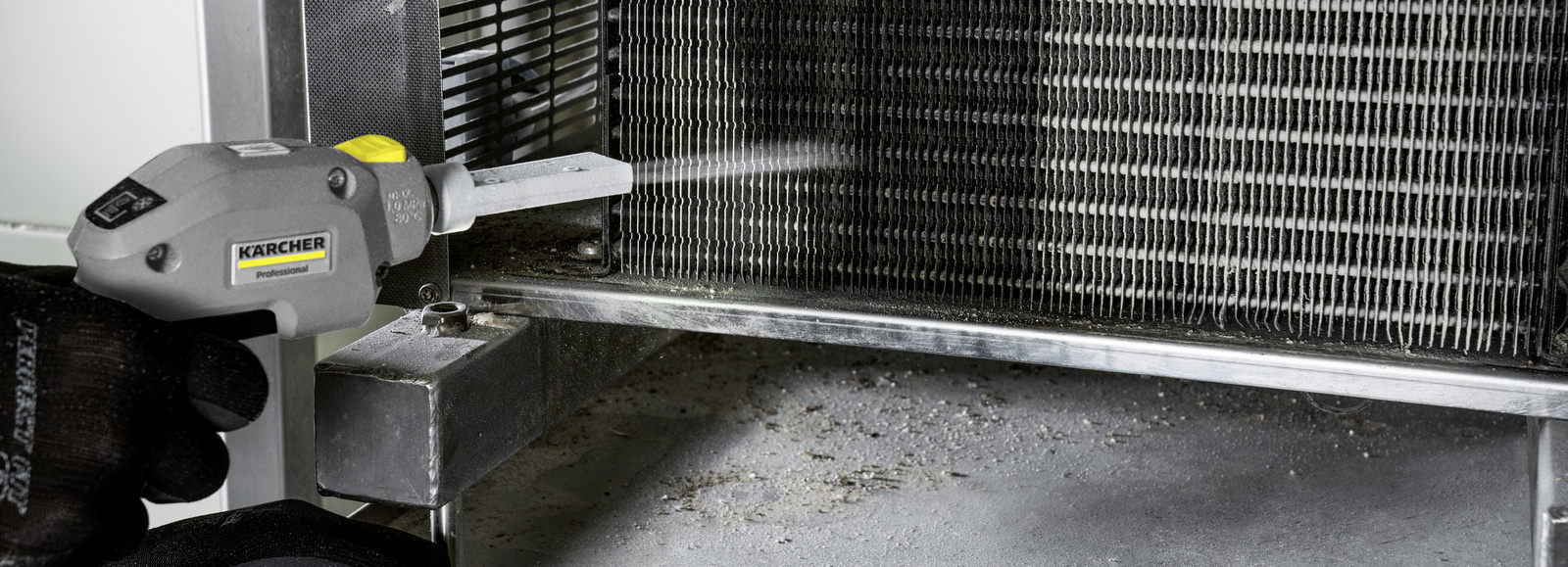
Gentle cleaning of delicate surfaces: dry ice cleaning
Suitable for:
✓ Gentle cleaning of sensitive electronics, such as painting robots
✓ Spot cleaning of delicate surfaces
✓ Cleaning of moderate to heavy soiling
Dry ice is very well suited for cleaning paint shops. Not only does this method benefit from a wide range of possible applications beneficial, but also the fact that neither abrasive residues nor residues of dirty water are left behind after the cleaning process is complete – the cleaned areas are not even damp afterwards. Because of this, dry ice is also an ideal option for cleaning areas where water must not be used.
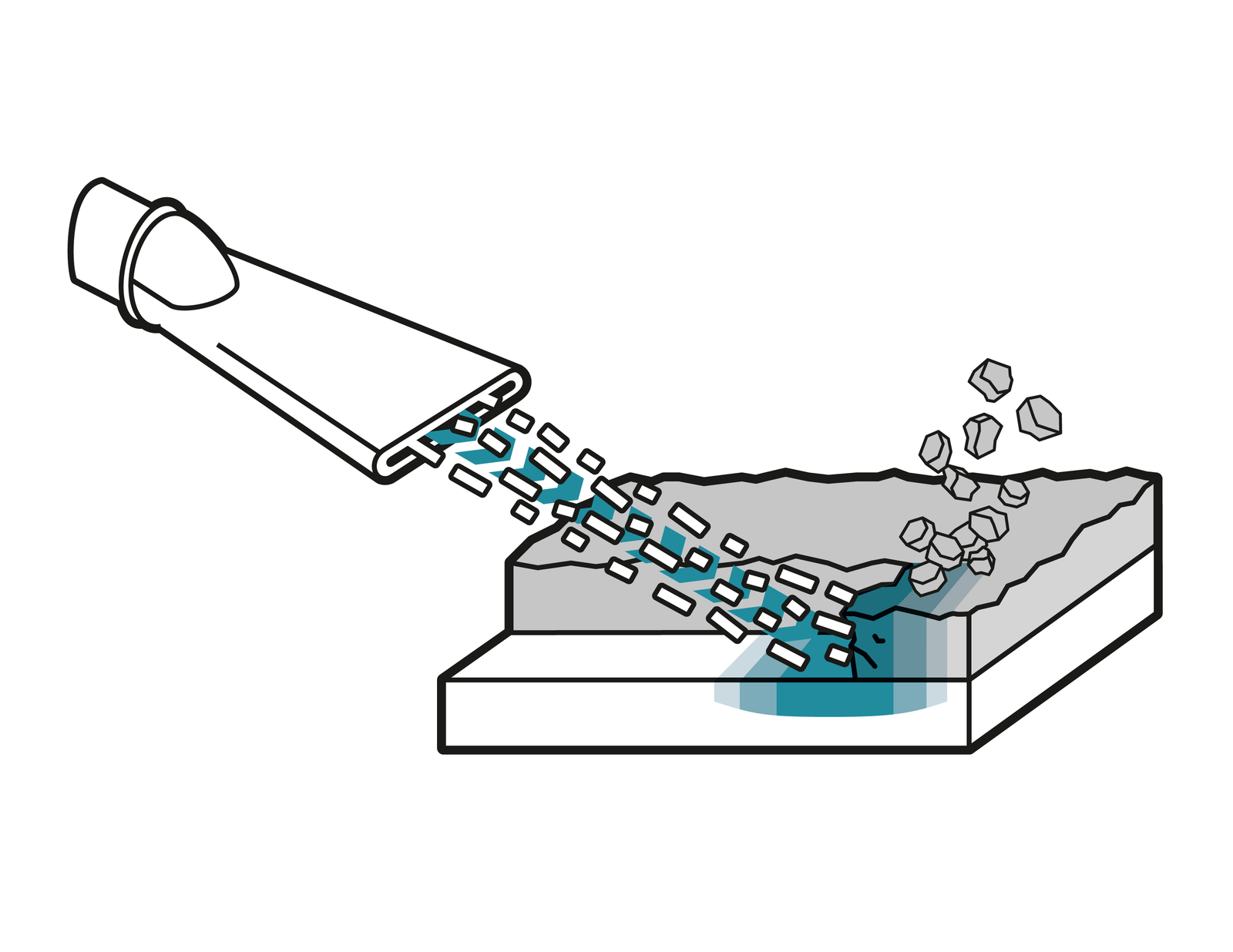
A fundamental property of dry ice cleaning is that it is not abrasive; it removes only the dirt, nothing else. There is no mechanical erosion or damage to the material surface. It is therefore suitable for cleaning delicate surfaces – however, it should be noted that the surface in question must be resistant to extremely low temperatures; otherwise, it will not be damaged by the cleaning itself, but it may instead be damaged by the temperature.
Dry ice blasting is a particle blasting method, whereby CO2 pellets measuring 0.5–3 millimetres are used as a spray agent. The dry ice pellets – at a temperature of -79 °C – hit the surface at a speed in excess of 150 m/s and transfer their kinetic energy in the process. The cold temperatures also cause the dirt to become brittle and fragile, which makes it come away more easily. Only the blasted substances remain. Depending on the quantity and composition, these are then either blown off with the compressed air available or, ideally, sucked up using a suitable vacuum cleaner.
As a rule, dry ice tends to be used in small areas and in places where no other form of cleaning is possible or practical – for example, in those places where water cannot be used. Areas of application may include glass surfaces, paint spray guns, and the metal and plastic casings of painting robots.
Tip:
For extra flexibility when cleaning, machines that actually produce the dry ice themselves are ideal – this means there is no lead time prior to use.
Health and safety comes first
Particular care must be taken to protect the user's hearing during use. The sound pressure of a dry ice blaster is between 75 dB(A) and 125 dB(A), depending on various operating parameters. Hearing protection must therefore usually be worn, and is mandatory from 80/95 dB(A). To protect against cold burns, personal protective equipment (PPE) should also include overalls, safety goggles with helmets and gloves. Depending on the application, a protective (dust) mask is also recommended.
Air quality is of particular importance when working with dry ice. The threshold limit value (TLV) for CO2 in the workplace is limited to 0.5 percent by volume. In a large factory hall, this is rarely a problem – in small, enclosed spaces or blast cabinets, however, a ventilation system is required.
If this is not possible, the user must have an oxygen supply. A CO2 measuring instrument at the workplace ensures that the air's composition is acceptable.
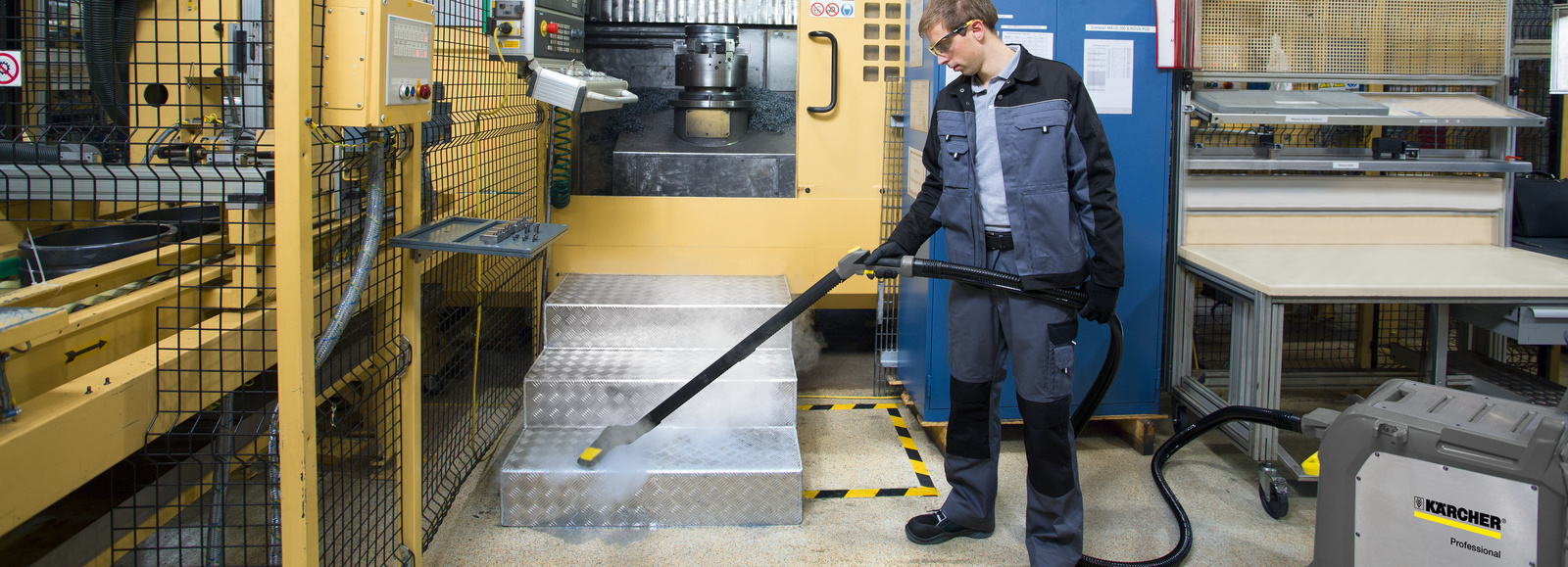
Tackle even adhesives with steam cleaning
Suitable for:
✓ Places where large water volumes are to be avoided
✓ Detailed cleaning of angled surfaces
✓ Removing adhesives
The power of steam cleaning comes from the combined effect of the jet of steam and the temperature of the steam. Water is heated in the steam cleaner's self-contained tank until it reaches boiling point and produces steam. Depending on the machine type, this hot steam emerges from the nozzle in very fine droplets at a temperature of approx. 100 °C and a pressure of up to 8 bar. The pressure propels tiny vapour particles, which strike the surfaces at speeds of up to 170 km/h, even getting into hard-to-reach areas and tight angles.
Steam cleaning is ideal for small and medium-sized surfaces and is particularly suitable for places where large volumes of water must not be allowed to enter and where chemicals are not permitted for use. Steam cleaners are ideal for cleaning facilities in which adhesive is applied, because steam can remove adhesive residues with ease. The heat of the vapour is key to its effectiveness in this regard. However, care should always be taken to identify the type of adhesive and whether any harmful aerosols could be released upon heating. In such cases, personal protective equipment must be worn.
The surfaces must also be tested in advance to establish whether they are too sensitive to the high temperatures and moisture. If the surfaces are compatible with the cleaning process, the adhesive residues are treated with steam until they can be seen to come away. The loosened residues are then scraped off. A steam scraper is ideal for smaller areas, while a steam vacuum cleaner with a hand nozzle is advisable for larger areas. It can be used to treat the adhesive residues with steam in an initial step, then further loosened with a scraper if necessary before being vacuumed off.
Ideal for textured surfaces: high-pressure cleaning
Suitable for
✓ Ingrained, heavy or stubborn soiling
✓ Textured surfaces
✓ Removable parts, as well as paint booth walls, for example
High-pressure cleaning is particularly suitable for removing stubborn dirt. It can be used for cleaning the walls of paint booths, for example, and especially in situations where parts can be disassembled and cleaned separately, as is the case with gratings, for instance. However, when cleaning with high pressure, the quality of the surface coating applied in the booth must be taken into account. This determines whether or not cleaning with high pressure is possible. Industrial coatings, for example, are compatible with high-pressure cleaning. In this case, the exhaust air and supply air ducts are of a robust and simple design, so that nothing stands in the way of the use of high pressure.
In combination with dirt-dissolving detergents, pressures in excess of 180 bar and water flow rates of approx. 1,000 l/h are used for efficient cleaning. If, on the other hand, the paintwork in question is a premium finish, it is difficult or impossible to use high pressure. In this case, the walls as well as the exhaust air and supply air ducts have a very complex design in order to create an ideal, draught-free environment and stable temperature for even painting results.
Due to the good air supply and ventilation and the high air exchange rates, paint mist gets trapped in the filter fleece of the extraction system; only the floor is exposed to larger mists, making cleaning necessary. As such, the parts needing to be cleaned, such as floor gratings, are taken to a wash booth or outside area so that the thick paint residues can be removed there using high pressure. If appropriate and available, this cleaning process can be done with hot water. The paint shop can be kept running during the cleaning process by installing replacement grates or it can be shut down during this time. As soon as the cleaned grids are completely dry, they are ready for use again.
Tip:
Take care to choose the right nozzle. The working efficiency can be significantly improved by using a nozzle with a larger spray angle, which increases the area performance. For very stubborn dirt, choosing a rotary nozzle (also known as a Dirt Blaster) significantly increases cleaning performance compared with a normal power nozzle. Before use, check to make sure the surface structure is not damaged by the use of the nozzle.
Advantages of hot water high-pressure cleaning
Used with hot water, high-pressure cleaners clean even better at a constant pressure. Alongside improved results and faster cleaning and drying times, hot water high-pressure cleaners also have a measurable germ-reducing effect. When the steam stage is used, even delicate surfaces can be gently cleaned with temperatures of up to 155 °C. Furthermore, the machines allow for a reduction in the working pressure, the time required and the volume of detergent that is used. This means that cleaning with hot water offers a number of advantages and various possibilities for optimising the cleaning process.
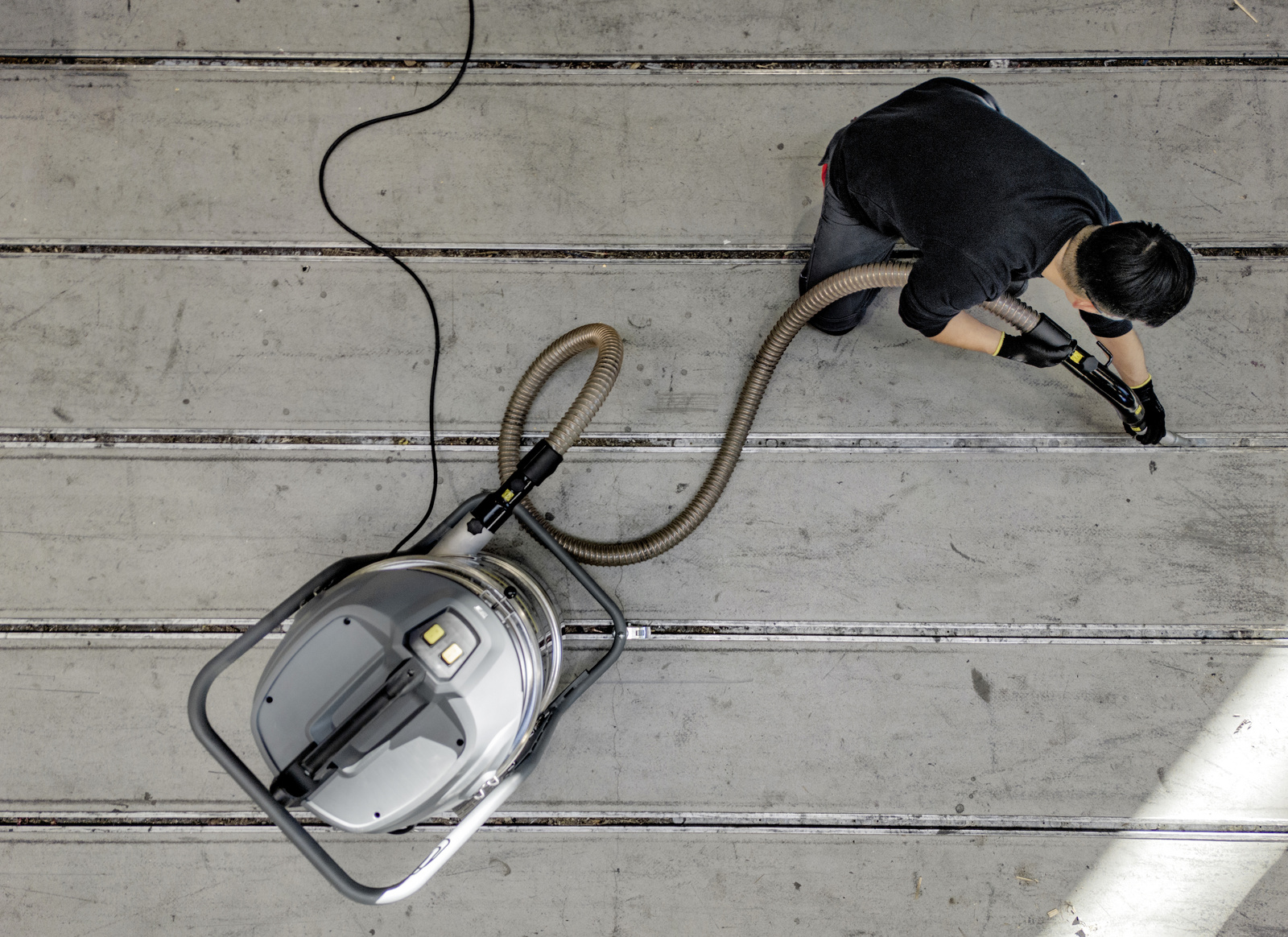
Don't just loosen it, remove it: cleaning with an industrial vacuum cleaner
Suitable for
✓ Removing loosened paint particles
✓ Use in paint booths, drying facilities and related areas
Industrial vacuums are particularly suitable for removing dust from paint booths and drying rooms, as well as in adjacent areas. After all, when paint mist sticks to surfaces and is subsequently loosened using dry ice, for example, the dried particles fall to the ground without actually being removed from the process. This is where an industrial vacuum comes in: the vacuum cleaner, usually a mobile design, safely collects up the dust, ensuring that it cannot impair further operational processes.
It is also very important for occupational safety that these residues are extracted, since most of these dusts are not only harmful to health, but also combustible and hang in the air in finely dispersed form.
It is therefore essential to use specially adapted equipment: the vacuum cleaner used must be capable of picking up combustible dusts and must be fitted with the appropriate filters. Class M filters are generally used as a minimum. In the case of toxic substances, class H filters are used and a respiratory mask must be worn when working with the vacuum cleaner.
How the dirt is contained also depends on whether it is harmful to health or not. If the dirt is harmless, it is sufficient to collect it in the vacuum cleaner's container without a disposal bag. However, toxic residues must be collected in a safety filter bag. It must then be ensured that the collected dirt is disposed of in line with the applicable regulations.
It should be noted that use of the vacuum cleaner should not be limited to the paint booth alone, but should also include the drying rooms and any transport routes between the painting facilities and drying facilities. Regular cleaning can significantly reduce the amount of paint transferred into other areas of the plant.
Suitable products for your area of application
Find a wide range of technology at lightning speed – with the Kärcher Professional product finder
In no time at all, we'll show you the exact Kärcher Professional machine that best suits your specific cleaning task.