Cleaning heat exchangers
Heat exchangers are used in many different sectors, whether food production, metal processing or glass production. They are particularly helpful in times of rising energy prices, since they save costs through heat recovery. In order to function perfectly, however, they must be professionally cleaned and maintained on a regular basis. The thermal exchange processes in heat exchangers often cause stubborn deposits to build, which makes cleaning particularly challenging.
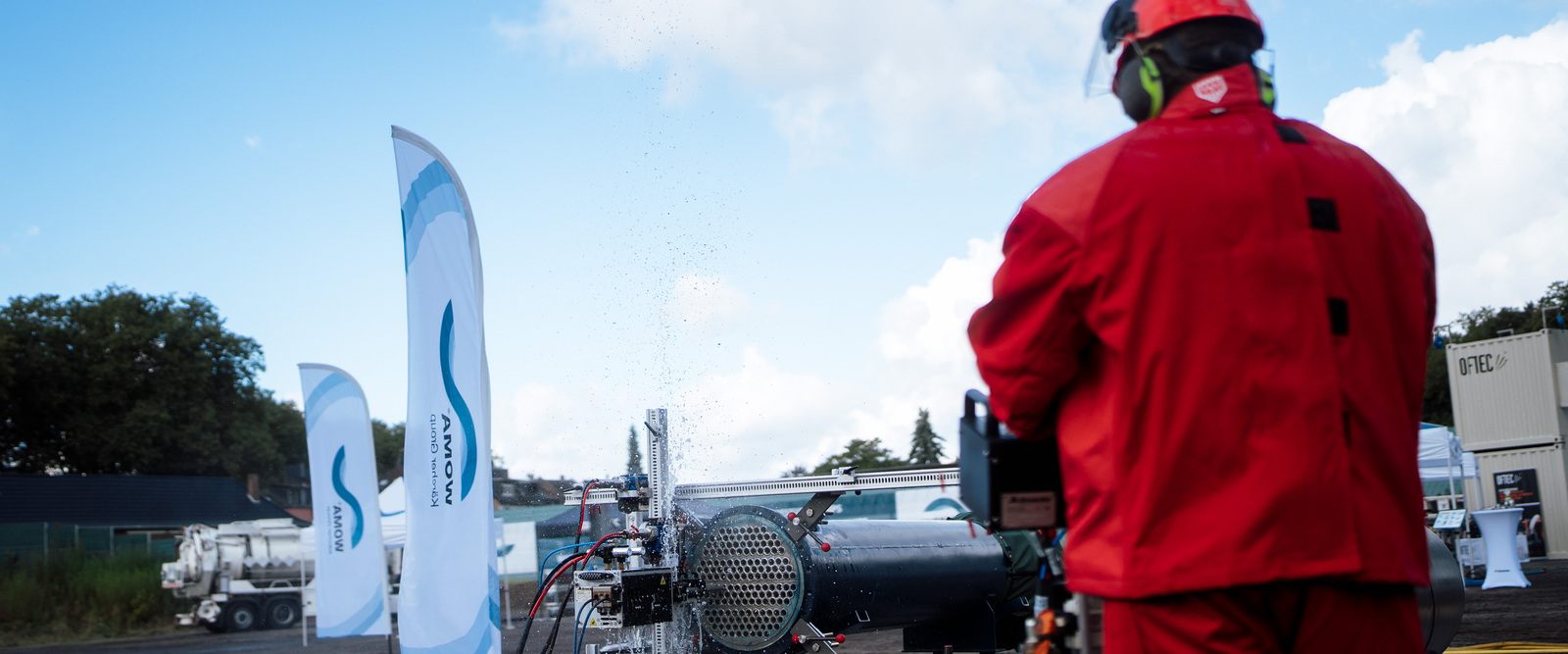
Spotlight on heat exchangers
The principle of the heat exchanger is widespread and can be found in various forms. From coffee machines to domestic central heating and even vast cooling towers in power plants – the basic principle is always the same: a heat exchanger is a machine designed to efficiently transfer heat from one medium to another. The media may be separated from each other so that they do not mix, but they can also be in direct contact with each other without a separating layer.
The most common field of application for heat exchangers is domestic heating systems. However, heat exchangers are also found in industrial settings and are often used in oil refineries, the chemical industry and the energy sector.
Professional and regular cleaning and maintenance is extremely important to keep heat exchangers running efficiently. The challenges involved in cleaning depend not only on the media used, but also to a large extent on the nature or type of heat exchanger.
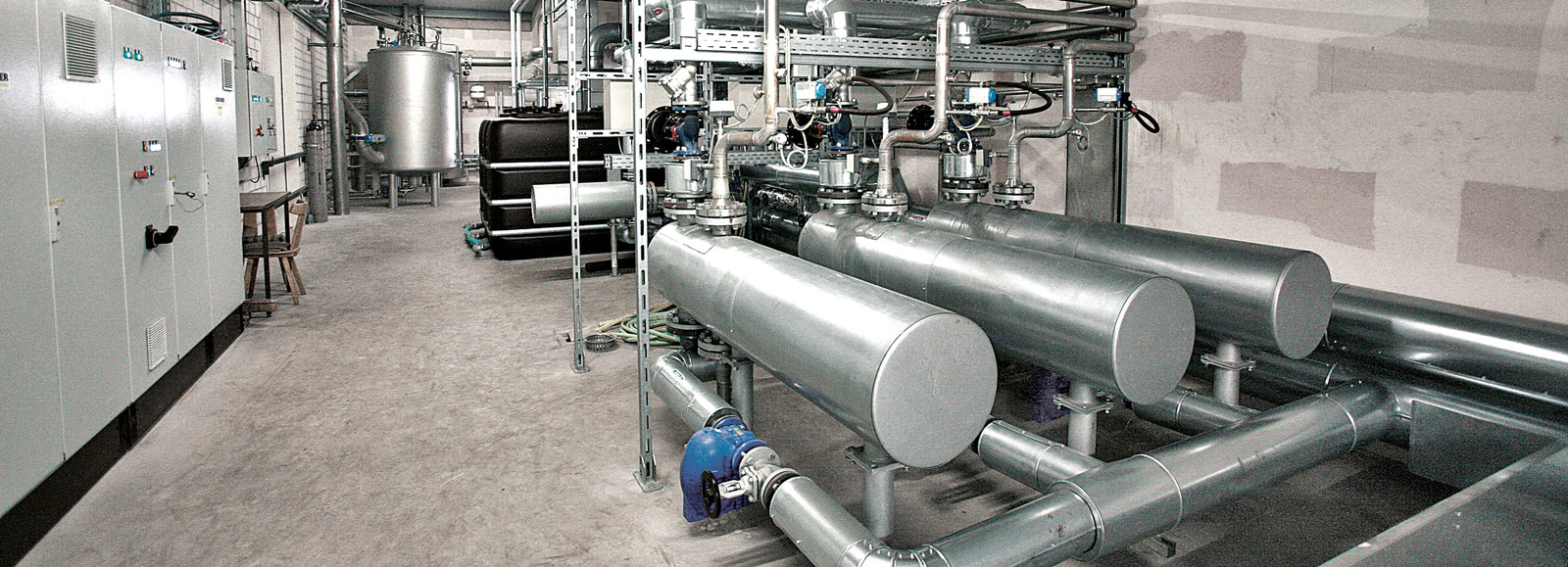
Heat exchangers: cleaning as an investment in the future
Maximising the surface area is fundamental to the performance of a heat exchanger, and the heat transfer rate of the material used is also an important factor. However, one other point is also important to performance – namely the condition of those surfaces. If they are dirty, performance is drastically impaired – it is therefore important that they are professionally cleaned and with consideration for the circumstances of their use.
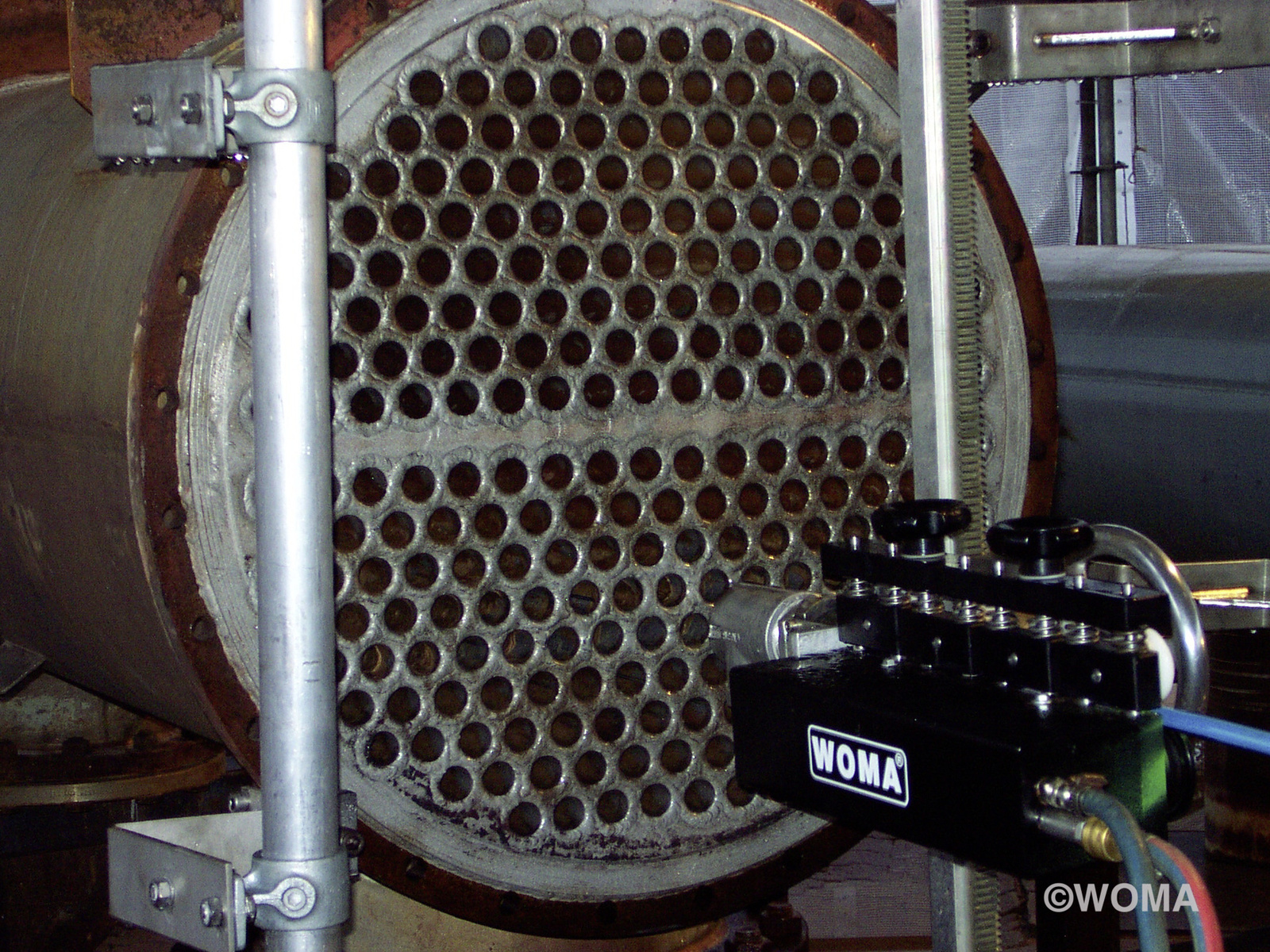
The task of cleaning and its challenges
The challenges involved in cleaning heat exchangers are varied and complex. The geometry and sometimes the long length of the tubes in particular can make cleaning a challenging endeavour. The tubes are often routed in bends with tight radii, and U-bends are also commonplace. Plus, the diameter of some tubes is as little as 12 millimetres. Circumstances such as these make it difficult to access the inside of the tube, making it necessary to use highly specialised cleaning machines. The nature of the soiling is also often challenging in itself. Depending which medium is flowing through the tubes, residue may build up on the inside. Liquid media in particular often contain dirt and solid matter that will bake on, such as carbonates and oxides.
In some circumstances, the incrustation on the tubes can be harder than the coating, which adds to the complexity of the cleaning process. Regular cleaning can stop incrustations from forming in the first place. Without regular cleaning, the crust grows from the inside and forms what is effectively an insulating layer, which then reduces the efficiency of the system. In the worst case scenario, the tubes can become completely blocked.
Nevertheless, downtimes need to be kept to a minimum, so a balance must be found here. In principle, the cleaning intervals vary according to the media flowing through the tubes and the overall size of the system. Cleaning often takes place when media is being changed or during planned shutdowns.
A complex cleaning task – the answer lies in high pressure
Various cleaning methods can be considered that are up to the task of cleaning heat exchangers. However, very few can be rated positively in terms of their implementation and results. In particular, chemical washing, i.e. cleaning in acid baths, is not especially practical as it requires huge tubs. Ultrasonic cleaning, meanwhile, is very time-consuming and does not achieve convincing results because it struggles to reach recesses. Cleaning with sandblasting brings with it the undeniable drawbacks that it is an abrasive and costly method, and ultimately produces large quantities of contaminated sand that need to be disposed of. Mechanical drilling, on the other hand, reaches its limits if the tubes in question do not run straight.
High-pressure cleaning, on the other hand, is very well suited to cleaning heat exchangers. There are no high material costs or disposal costs, and it does not require the use of chemical detergents – a fact that benefits both the environment and budgeting. Plus, this method generally uses cold water, which saves energy costs.
High pressure can also be used to remove stubborn deposits; this is usually done at 1,000 bar, or in some cases even 2,500 to 3,000 bar. Applications above 1,000 bar are referred to as cleaning with ultra-high pressure. This cleaning procedure can be used to clean both the inside and outside of the tubes and is also suitable for complicated geometries and tubes with a particularly small diameter.
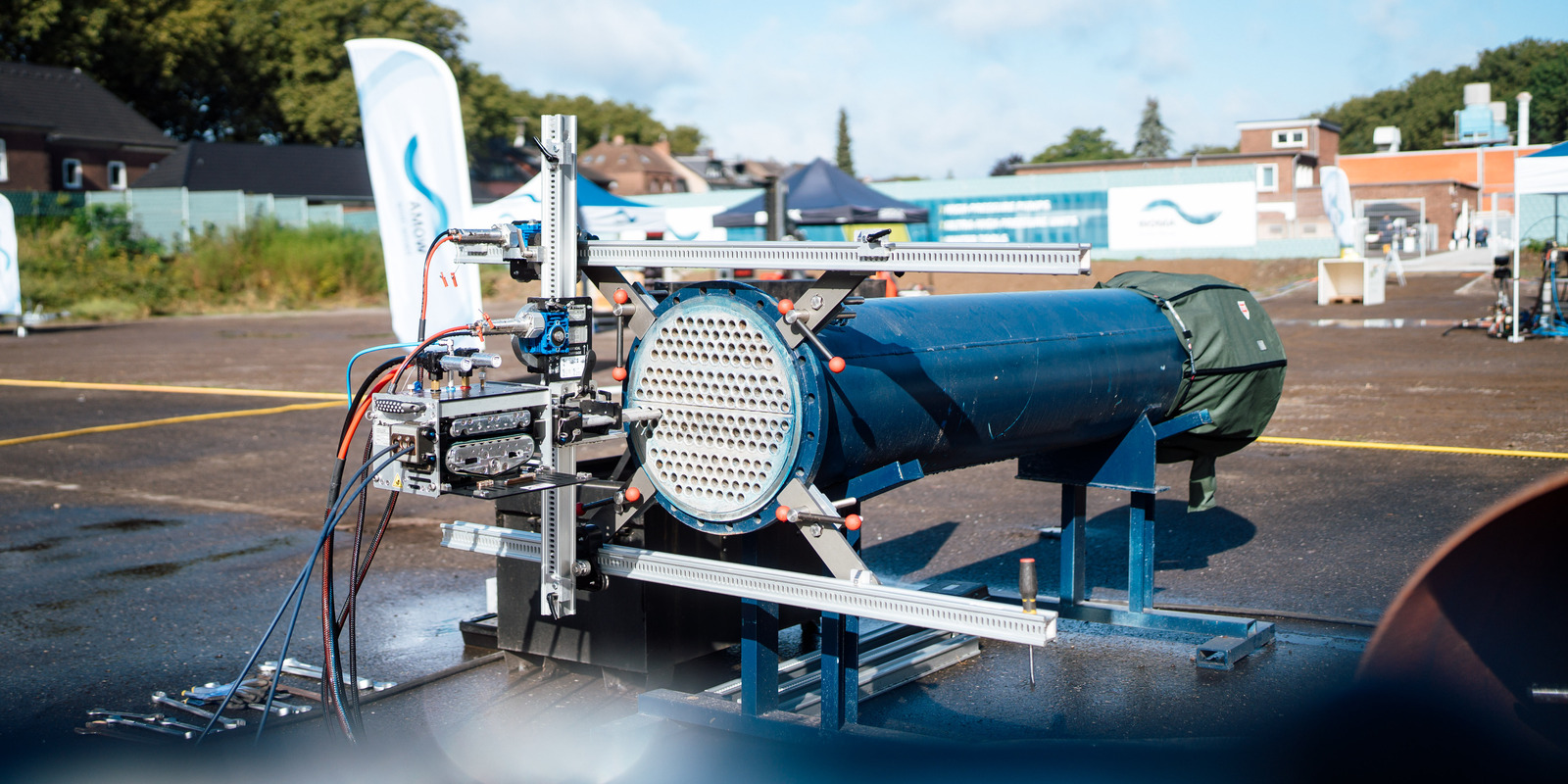
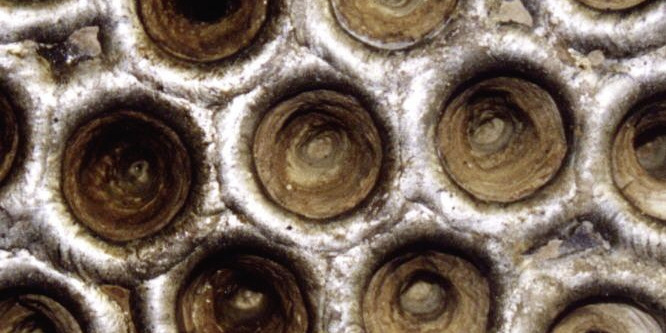
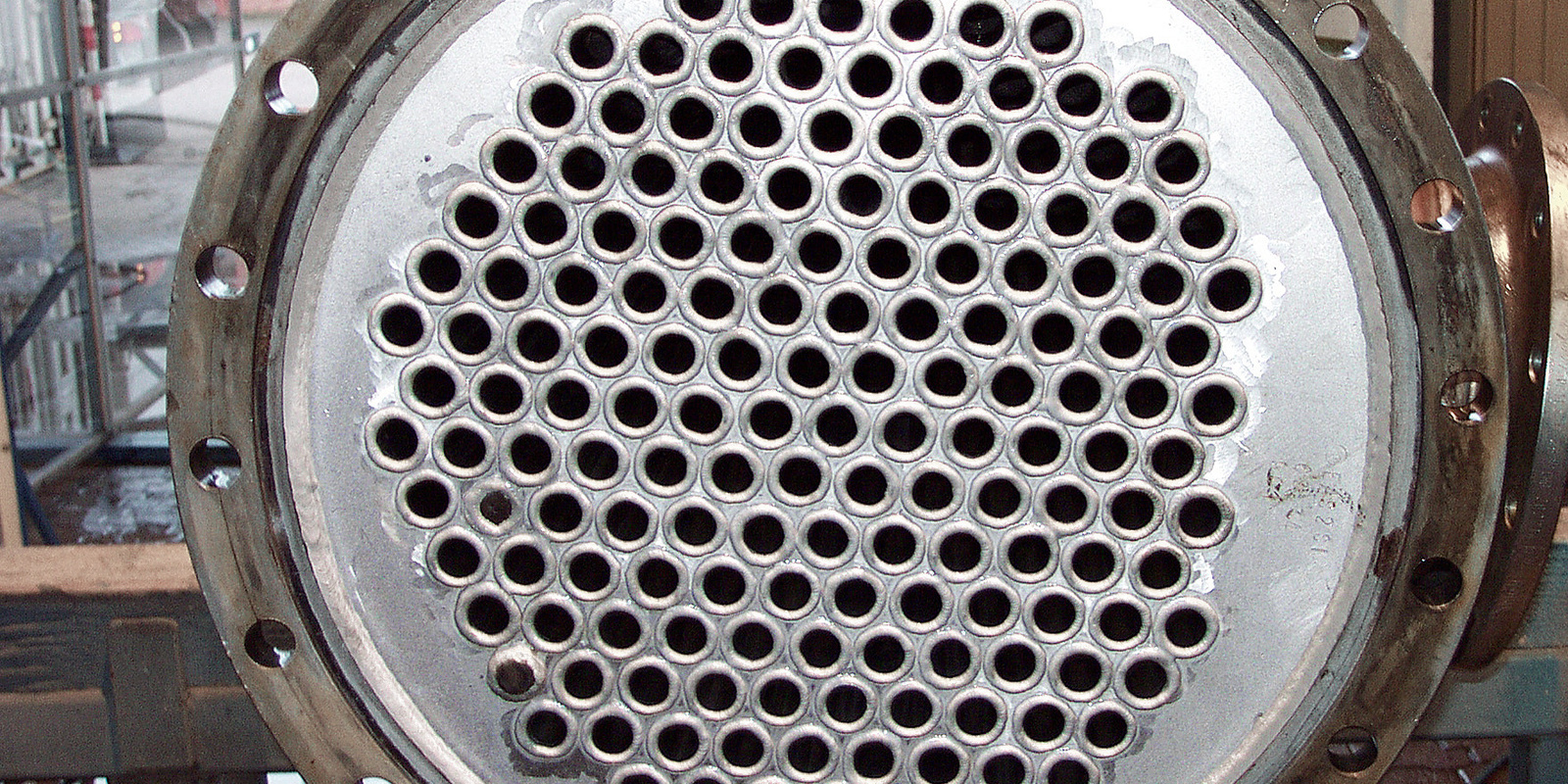
The cleaning process in practice
The cleaning procedure can be differentiated on the basis of two criteria: firstly, a distinction is made between cleaning out of place (COP) and cleaning in place (CIP). And secondly, manual cleaning can be differentiated from semi-automated cleaning. Depending on these categorisations, the equipment must be adapted to the respective conditions using specialised accessories.
Tip – High-pressure cleaning needs the right type of lance:
Choosing the right cleaning lance can make the cleaning process more efficient. Flexible – in the physical sense of bendable – lances are easier to use, more adaptable, more economical and particularly suitable when space around the heat exchanger is limited. However, they are also more delicate and get bent out of shape easily. Rigid lances are stable and available for every pressure range. However, they are difficult to handle from a length of around 6,000 millimetres, since handling them requires a lot of space and care due to their lack of flexibility.
Suitable products for your area of application
Find a wide range of technology at lightning speed – with the Kärcher Professional product finder
In no time at all, we'll show you the exact Kärcher Professional machine that best suits your specific cleaning task.