Cleaning in the chemical industry
The chemical industry is under increasing cost pressure, primarily due to fluctuating energy prices. Furthermore, very strict standards and regulations must be adhered to in order to avert risks in the process that could endanger employees, the environment or the general public. In light of this, cleaning is ultimately a driving force behind efficiency, safety and quality, because cleanliness ensures smooth processes, reduces downtimes and assures product quality. Occupational safety can also be better guaranteed in a clean environment, since leaks, for example, can be resolved fast.
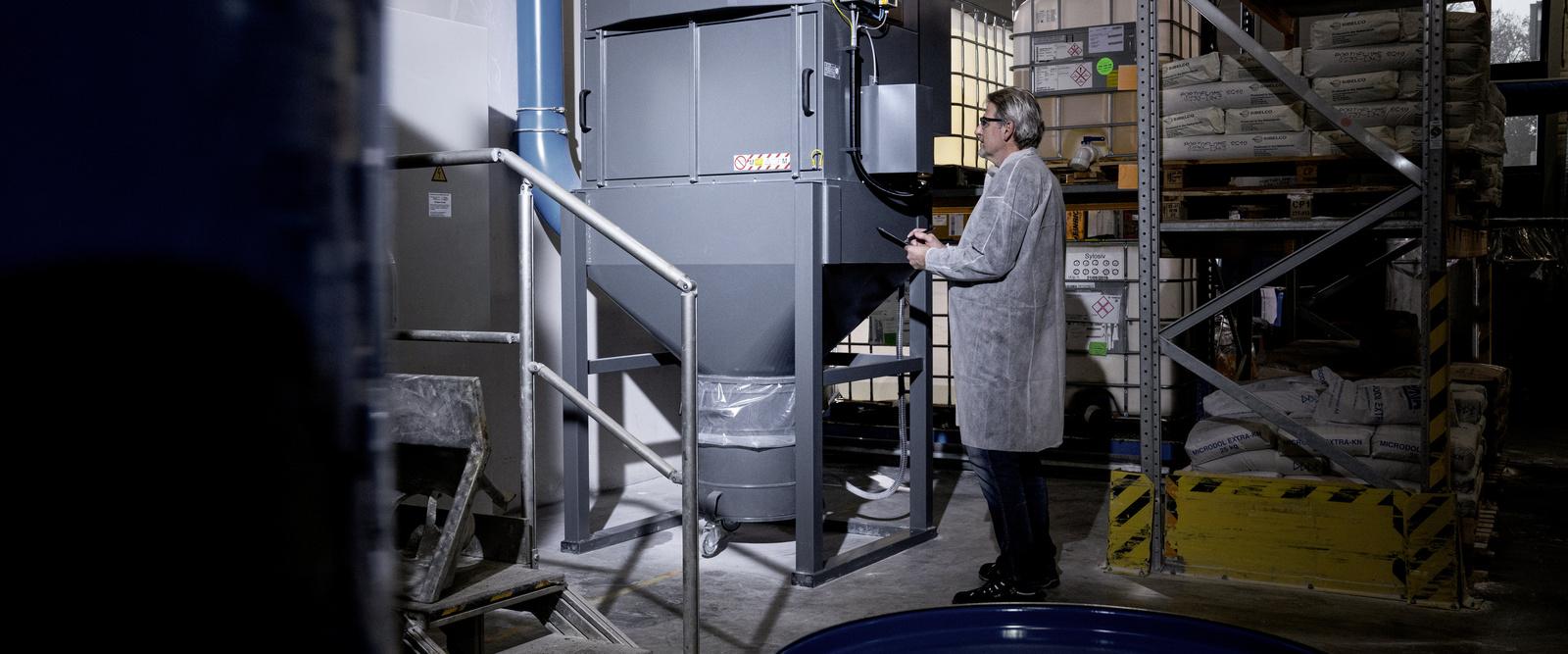
Complex processes call for complex cleaning tasks
In the chemical industry, petroleum-based products are often manufactured using highly complex formulations and processes that require systems consisting of pipelines, various temperature stages, intermediate storage tanks, tube convectors or heat exchangers. A product is manufactured in batches from various raw materials, which must be clearly documented for traceability. If a batch change takes place, the product change-over affects the process steps required. This situation gives rise to numerous different cleaning tasks, and often even the water required for cleaning has to be collected and kept in a separate circuit to ensure groundwater protection requirements are met.
Cleaning in place and ATEX equipment
In order to achieve the required standards in terms of plant cleanliness, cleaning-in-place systems are often used. These are integrated into the production processes and automatically take over certain tasks, such as cleaning the pipelines. Production halls often contain ATEX zones, i.e. hazardous zones as per the European ATEX Directive 2014/34/EU (Atmosphères Explosibles) with exact specifications for the technology to be used there. For example, there are vacuum cleaners that comply with the requirements ex works, or scrubber dryers that can be fitted with ATEX conversions upon request in order to carry out floor cleaning efficiently and safely.
(Ultra-)high-pressure and the fixation on dust
Mobile or stationary high-pressure cleaners with compatible accessories are often used to clean vessels between successive batches. Ultra-high pressure cleaners operating at 500 to 1,000 bar can help to remove very stubborn residues from vessels or floors.
In addition to all production-related cleaning tasks, it is important to consider the processes before and after production, too. Dust is a major issue both in the delivery zones and in the areas where raw materials enter production, as well as in the packing area and goods out area of logistics. Regular sweeping and vacuuming is essential to ensure cleanliness and safety.