Cleaning in production plants
The cleaning tasks in industrial production settings are as varied as the products themselves. Clean facilities and a well-maintained environment are always a prerequisite for smooth-running processes, safety and product quality. Cleaning floors with scrubber dryers can play a part in achieving this, as can the extraction of fine dust to prevent explosion risks. In some cases, it even comes down to customised solutions – for example, using extraction systems to remove wood chips from pallets or bits of film wrap from transport belts.
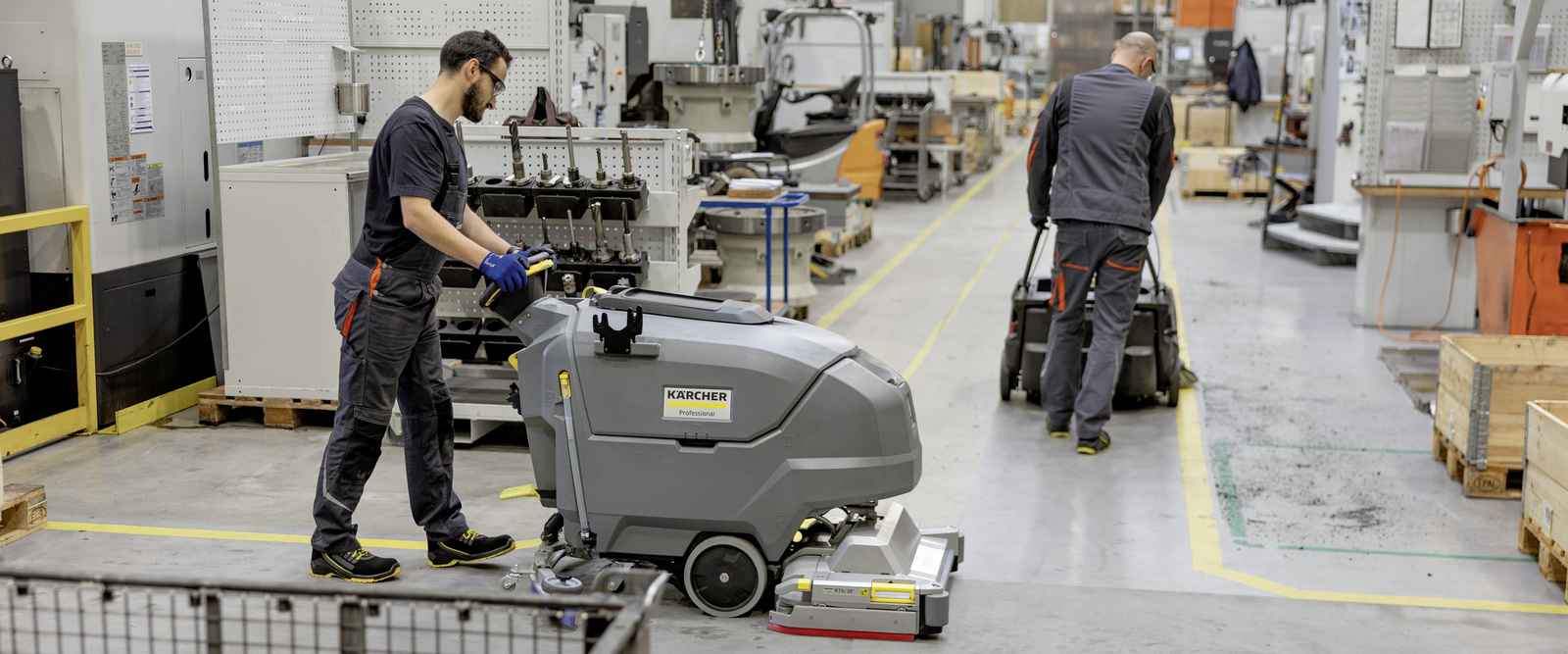
Stopping the spread of dirt with floor cleaning
In modern production environments, autonomous forklift trucks ensure a smooth flow of materials between logistics and production. In order for them to navigate reliably using sensors, the floors need to have a particular defined texture. Dirt or spills are an obstacle to this and also pose a risk of accidents for employees. Plus, this dirt gets spread around and can find its way into production. Regular use of vacuum sweepers and scrubber dryers in harmonised rotation counteracts these problems and ensures safe processes.
Preventing malfunctions: surface cleaning
Many production facilities are highly automated and equipped with sensitive sensors and robotics. To prevent faults from arising, parameters such as temperature, humidity etc. are kept constant and controlled by means of remote monitoring. A major factor in the defined environment, however, is cleanliness, because dirty sensors do not work. Regular surface cleaning using the preconditioning or spray method is recommended, especially where highly sensitive sensors are in operation.
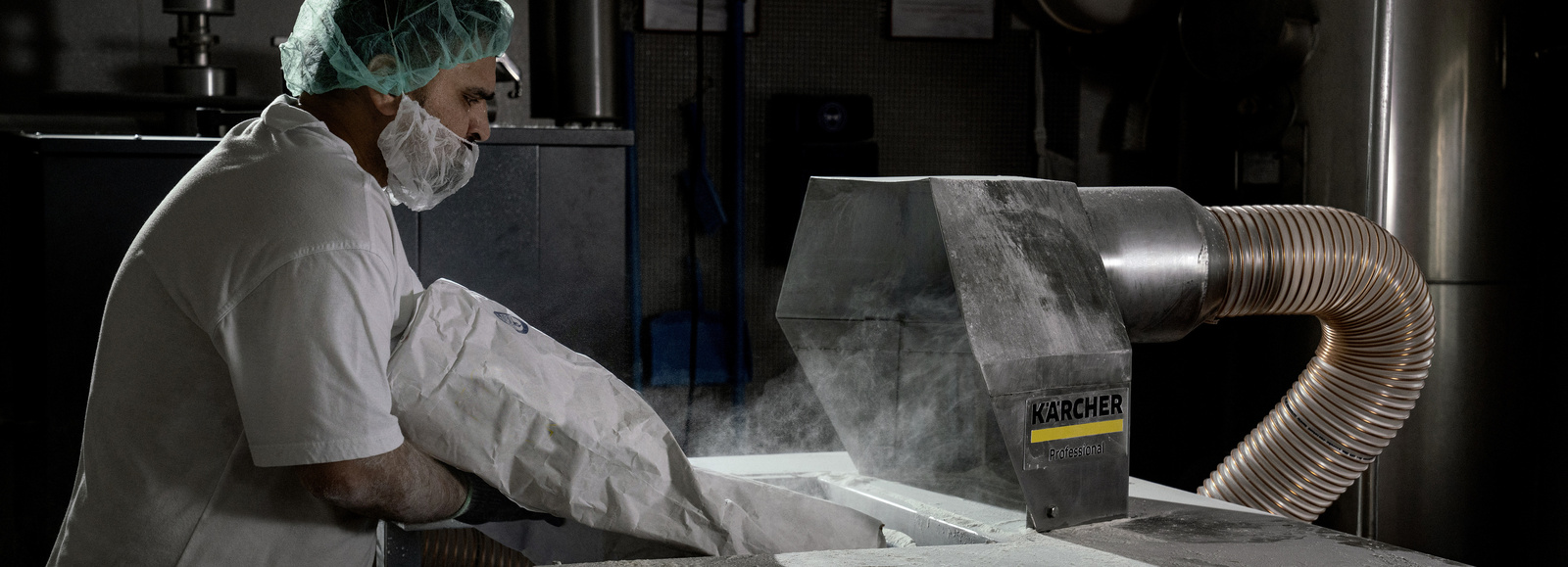
From flour dust to cooling lubricants: everything must be cleaned off
Dirt can appear as a result of an accident or it may be an unavoidable part of the manufacturing process. While loose dirt, such as residues from punching metal blanks or dust from polishing, is commonplace in the automotive industry, many food-processing companies have to deal with fine dusts. In metal processing, however, greasy dirt is often produced by cooling lubricant bonding with metal shavings. There is the right cleaning solution for every type of dirt, whereby permanently installed extraction systems or mobile industrial vacuum cleaners can ensure high efficiency depending on the circumstances. Use of ATEX industrial vacuum cleaners to remove fine dust is mandatory if there is an explosion risk as per the ATEX (Atmosphères Explosibles) definition.
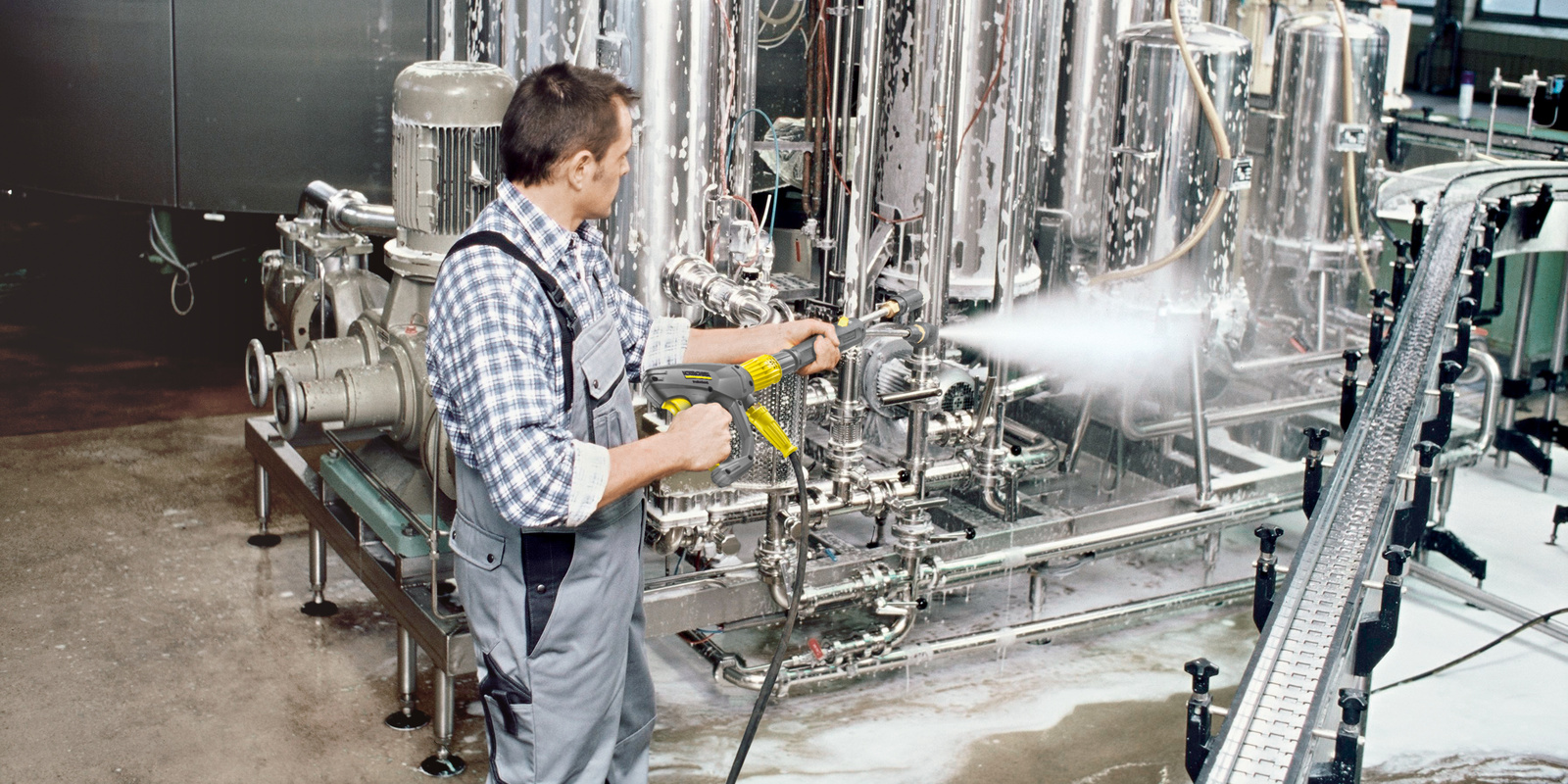
Special case: cleaning transport belts
When transport belts and conveyor belts stop, the entire production and logistics chains are immediately blocked. It is therefore very important to ensure cleanliness – both in the event of unforeseen contamination or contamination that is inherent in the process. Extraction systems, for example, can pick up loose labels to make sure that these do not disrupt production. Dry ice blasters, meanwhile, can be used as a gentle method to fully remove sticky, adhesive dirt without having to dismantle parts. Belts that transport primary products are often cleaned with a high-pressure cleaner.
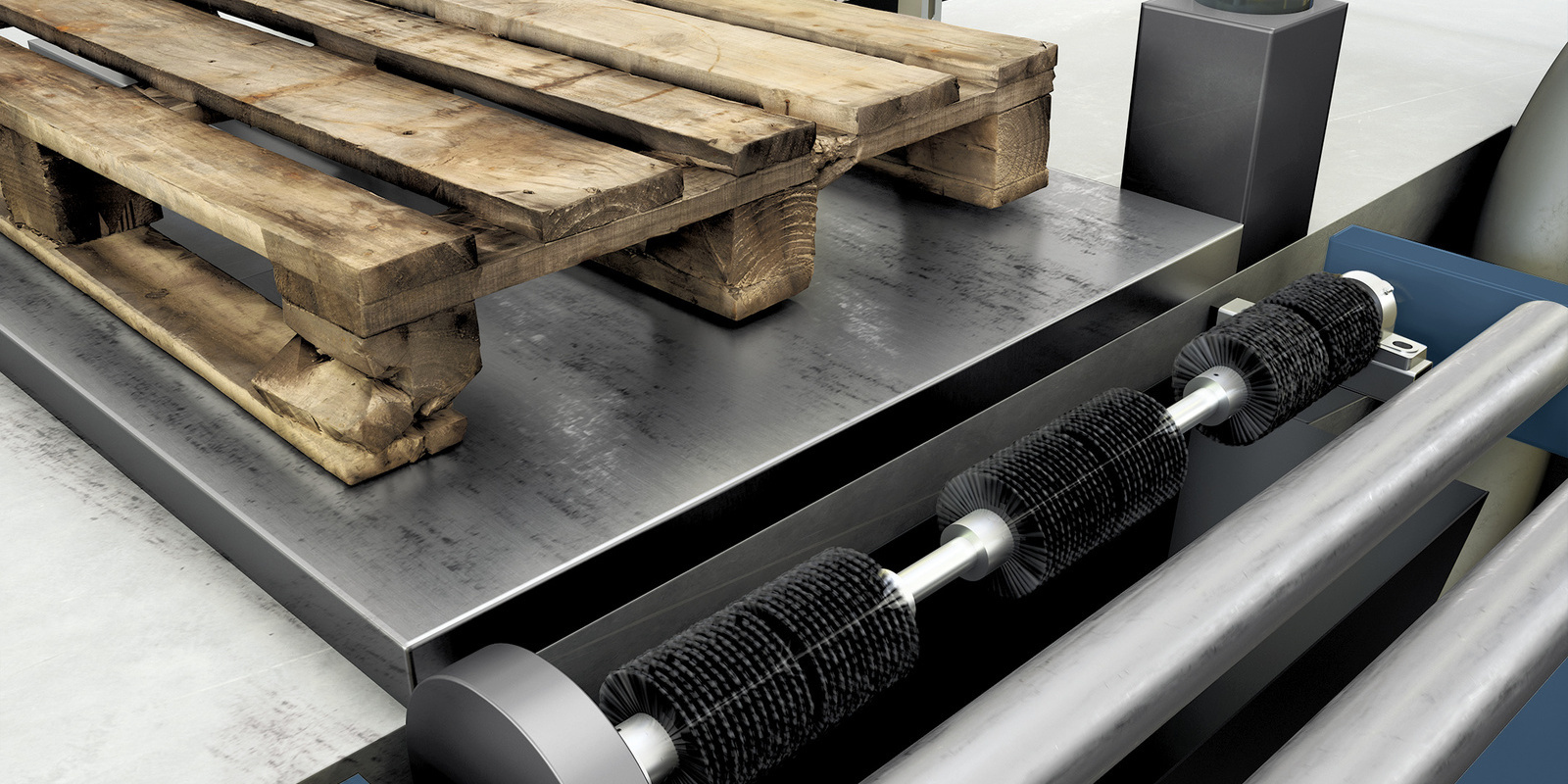
Special case of pallet cleaning
Wooden pallets and plastic pallets are indispensable when handling materials and goods. At the same time, they do bring with them dust, wood chips and other dirt into warehouses and, in turn, into production processes. They also often contaminate the highly sensitive light barriers in automated warehouse systems, causing faults. Automatic pallet cleaning systems can be installed on site to prevent production downtime and to improve product quality.