Automating pallet cleaning
In the field of logistics, wooden and plastic pallets not only bring goods into the company, they also bring dirt into the warehouses. This, in turn, increases the cleaning effort. Automated warehousing systems also use sensors such as light barriers, which can become dirty, disrupting processes in warehouse systems. Systems installed upstream of the incoming goods area are designed to automatically extract dirt and debris from pallets, significantly reducing the amount of dirt and helping to minimise technical problems. How does this work and how else can companies benefit from it?
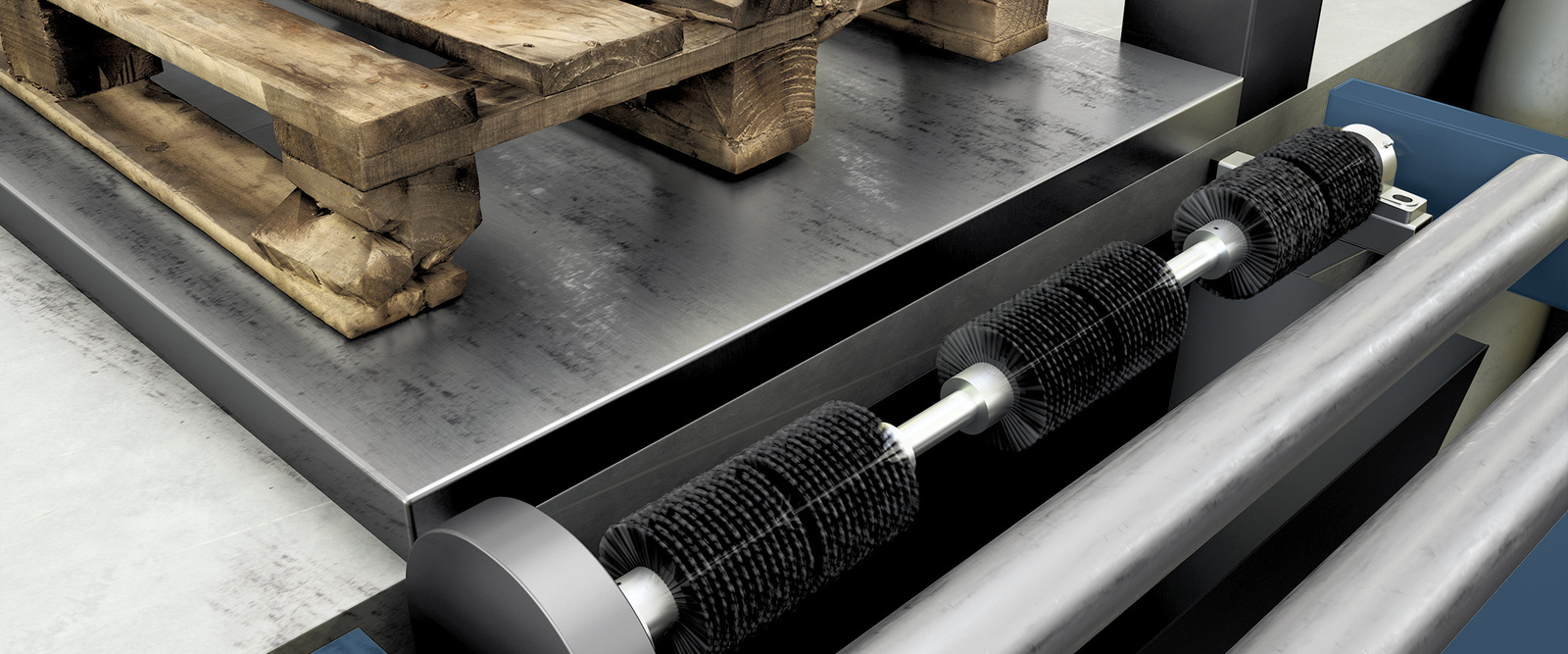
Cleaning in logistics: recognising problems, finding solutions
To ensure logistics run smoothly, it is important to recognise problems and find suitable cleaning solutions to those problems.
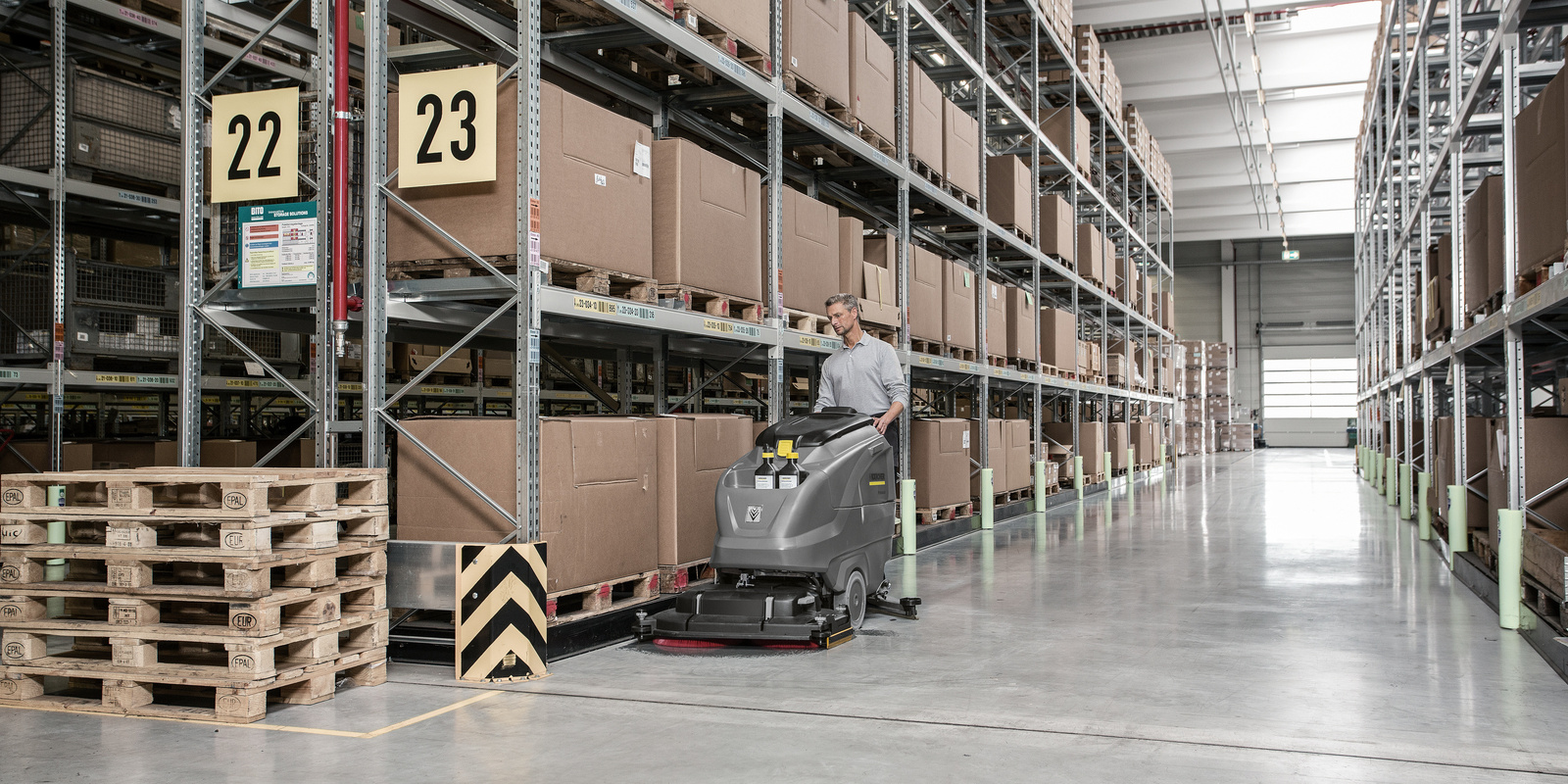
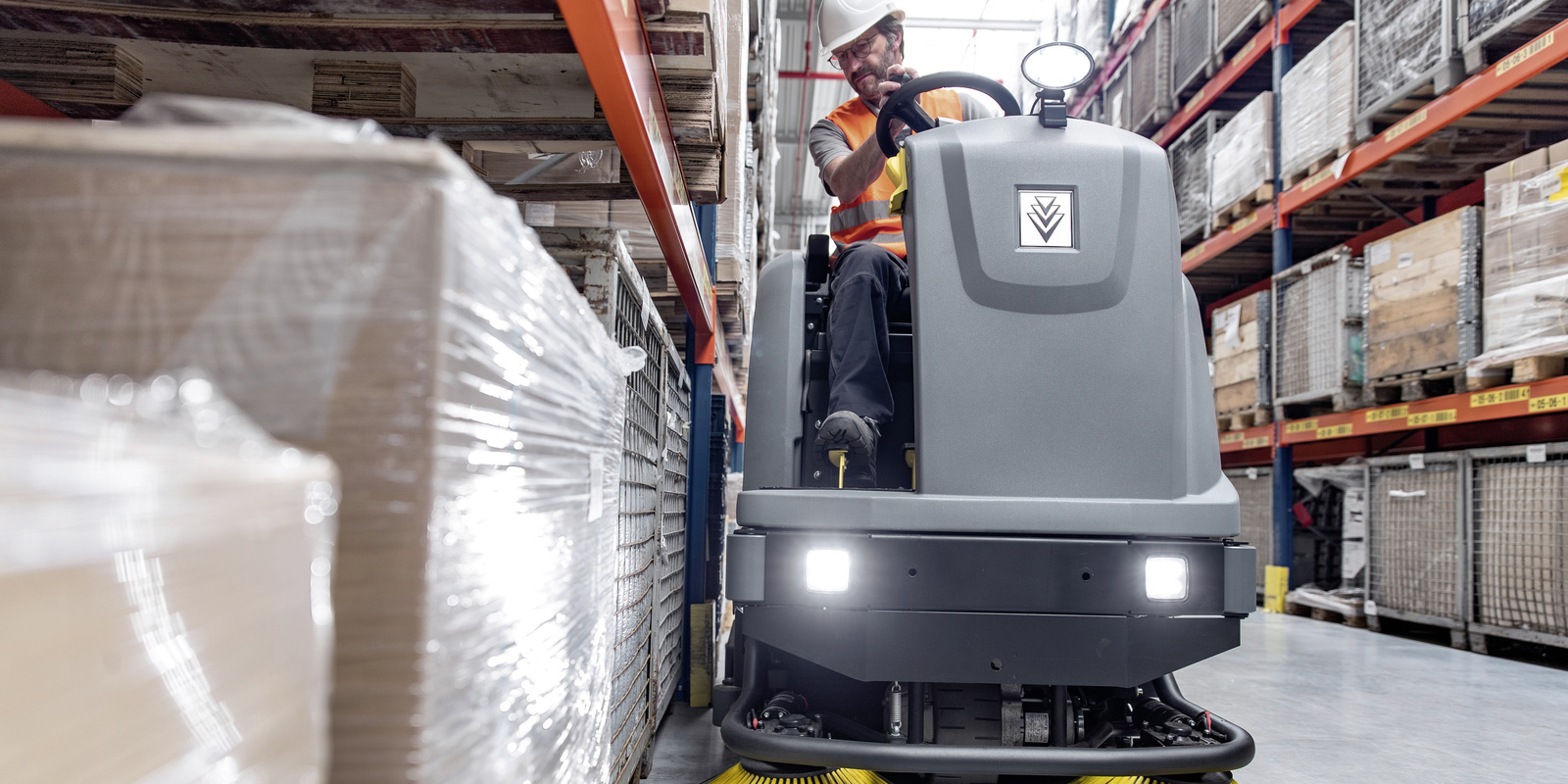
The beating heart of any company: without logistics, everything stops
Internal logistics plays a central role in every company. It ensures that raw materials are inspected and enter production, and it makes sure that end products leave the plant and reach the customer on schedule. If these processes do not run smoothly, it results in workflow delays, production downtime and, in the worst case, dissatisfied customers. Product quality can also suffer from the introduction of non-production-related substances. Potential consequences include a drop in order numbers or damaged company image.
Recognising problems: accident risk and standstill
To avoid these risks, it is important to pay attention to every detail. The wooden or plastic pallets used throughout industry can also create problems, as they bring coarse dirt and, depending on the design, wood chips and dust into the warehouses. The dirt poses a safety risk for employees, as it can create a slip hazard or a tripping hazard. Automatic warehouse systems also work with highly sensitive light barriers. If these get dirty, their function is impaired or they can even fail completely. Appropriate cleaning solutions help to solve these problems.
Tip:
If the company is experiencing an increase in operational process disruptions, the reasons must be discovered and remedied. Extraction technology can help to effectively remove the harmful foreign particles from the process and eliminate the associated problems.
Benefits of automatic pallet cleaning systems
Carefully considered solutions such as the automatic cleaning of pallets not only keep warehouses clean, but also bring further benefits to the logistics department and the company as a whole.
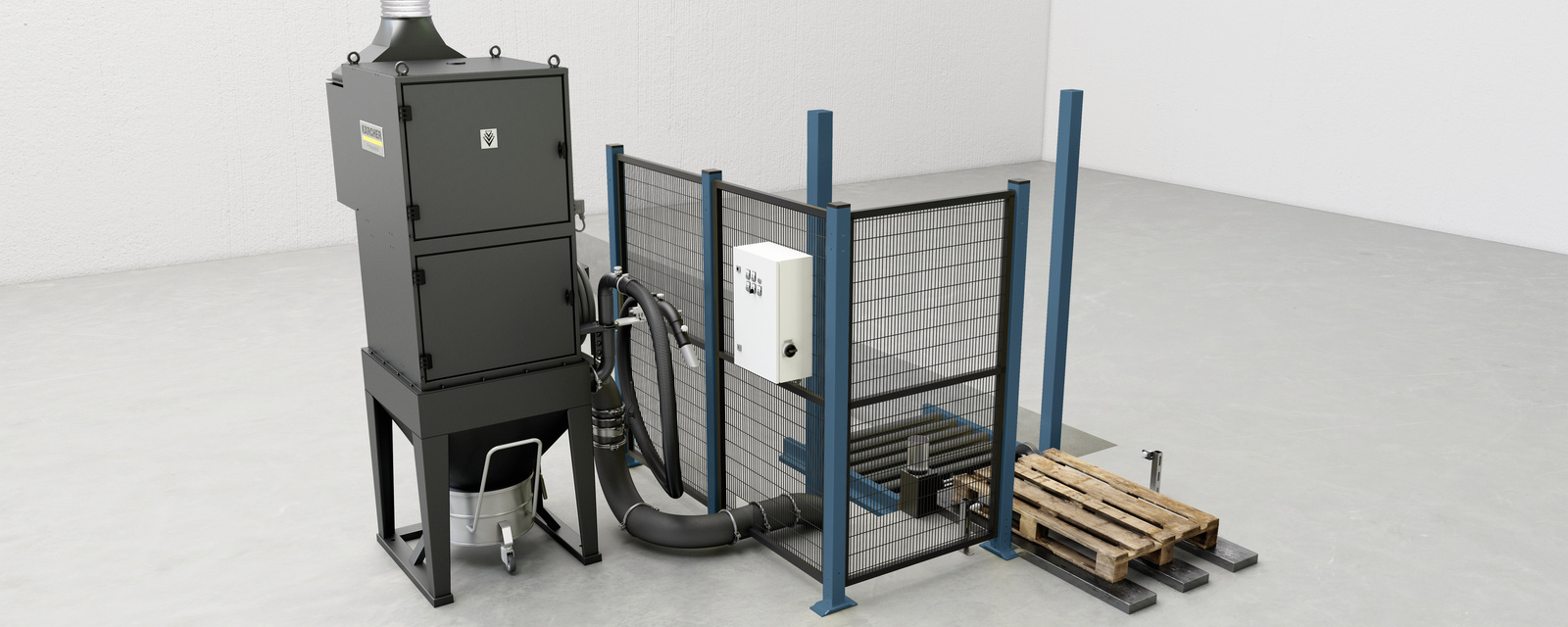
Automatic pallet cleaning: fewer production losses, more product quality
The use of pallet cleaning systems significantly reduces the cost and effort of maintenance cleaning in logistics. It reduces the workload for cleaning staff, and minimises damage to sweepers that is caused by coarse dirt and debris. Since clean conditions keep data light barriers working, production downtimes are therefore reduced to a minimum. It also reduces the risk of contamination, since the pallets would otherwise carry dirt into logistics together with the raw goods, which can subsequently work its way into the production line. If this is prevented, the result is increased product quality. Pallet cleaning can also be a sensible measure for outgoing goods, to ensure these arrive with retailers and, ultimately, end customers perfectly clean.
Tip:
The cost of installing an automated pallet cleaning system is amortised within a year, on average.
How pallet cleaning systems work and what they have to offer
Automatic pallet cleaning systems work relatively simply: for example, the pallets enter the warehouse via conveyor belts at goods-in. Pallet cleaning can be set up between two sections in a conveyor belt. It consists of a wide brush that removes coarse dirt, such as wood splinters, and a rotating combi brush to pick up finer particles. The extracted dust and dirt is transported away by pipes. The extraction itself is carried out by a stationary extraction system with powerful turbines and a collecting container. Controlled by sensors, the cleaning process starts automatically as soon as a lifting unit loads a pallet onto the conveyor belts. A major advantage of this solution is that it can be integrated into the conveyor infrastructure without taking up too much space, and it can easily be adapted to site conditions, because the standard systems used can be modified to suit the customer's specific requirements.
Could it get any better? How systems can be expanded
The system can be scaled as required to suit the size of the company. In the event of extensive logistics with many branches, it may be preferable to plan in multiple cleaning stations at relevant points ahead of goods in/out or before pallets are transferred to production. The system also offers the flexibility to adjust the power in response to the conditions and hygiene requirements. Manual extraction points can be installed for additional manual cleaning. For this purpose, hoses are attached in suitable locations, which automatically start extracting when picked up, making work easier for the user. With a conventional manual cleaning system, dry vacuum cleaners must first be retrieved from storage, plugged in (depending on the model), switched on then put away again after use.
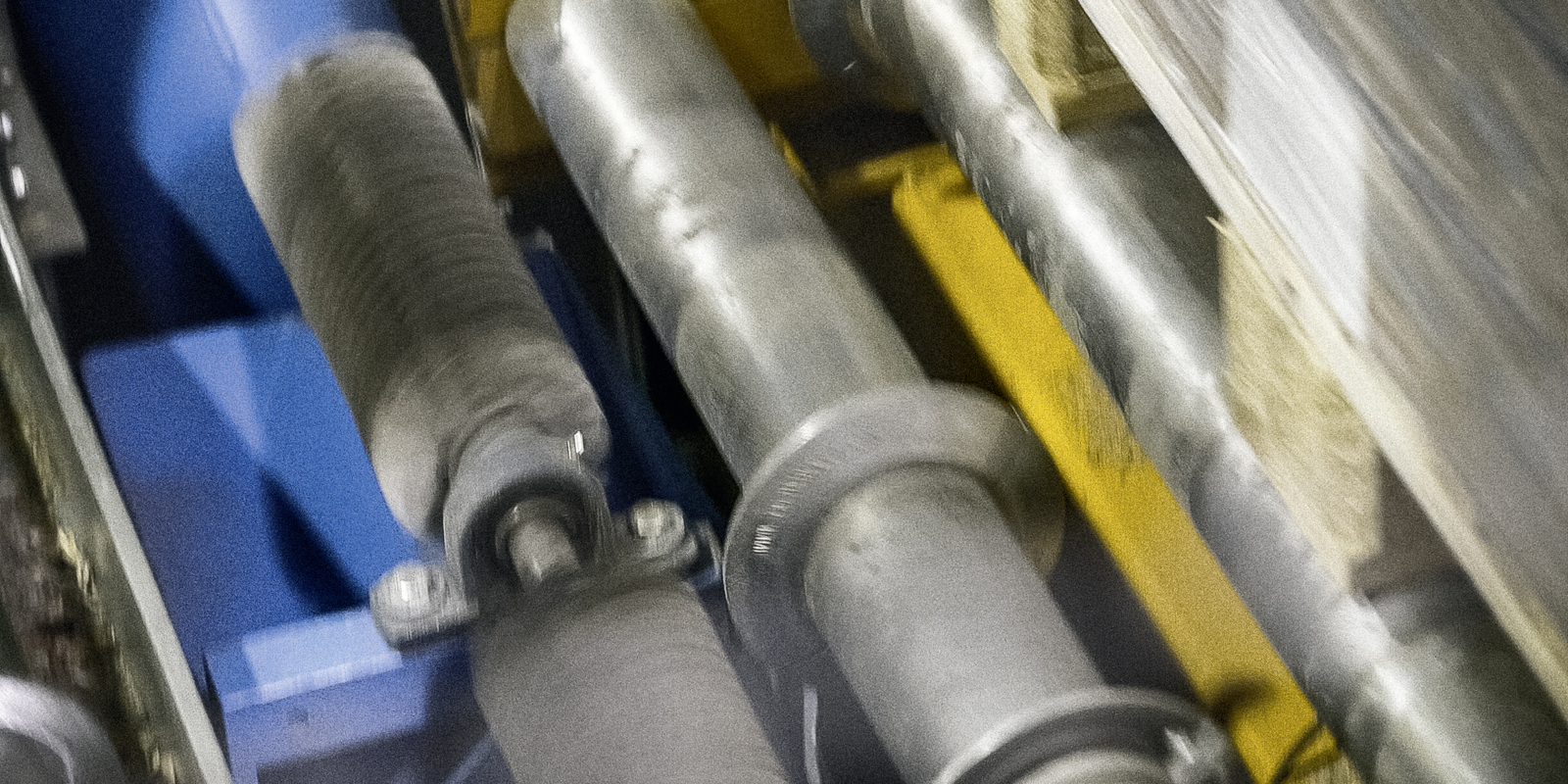
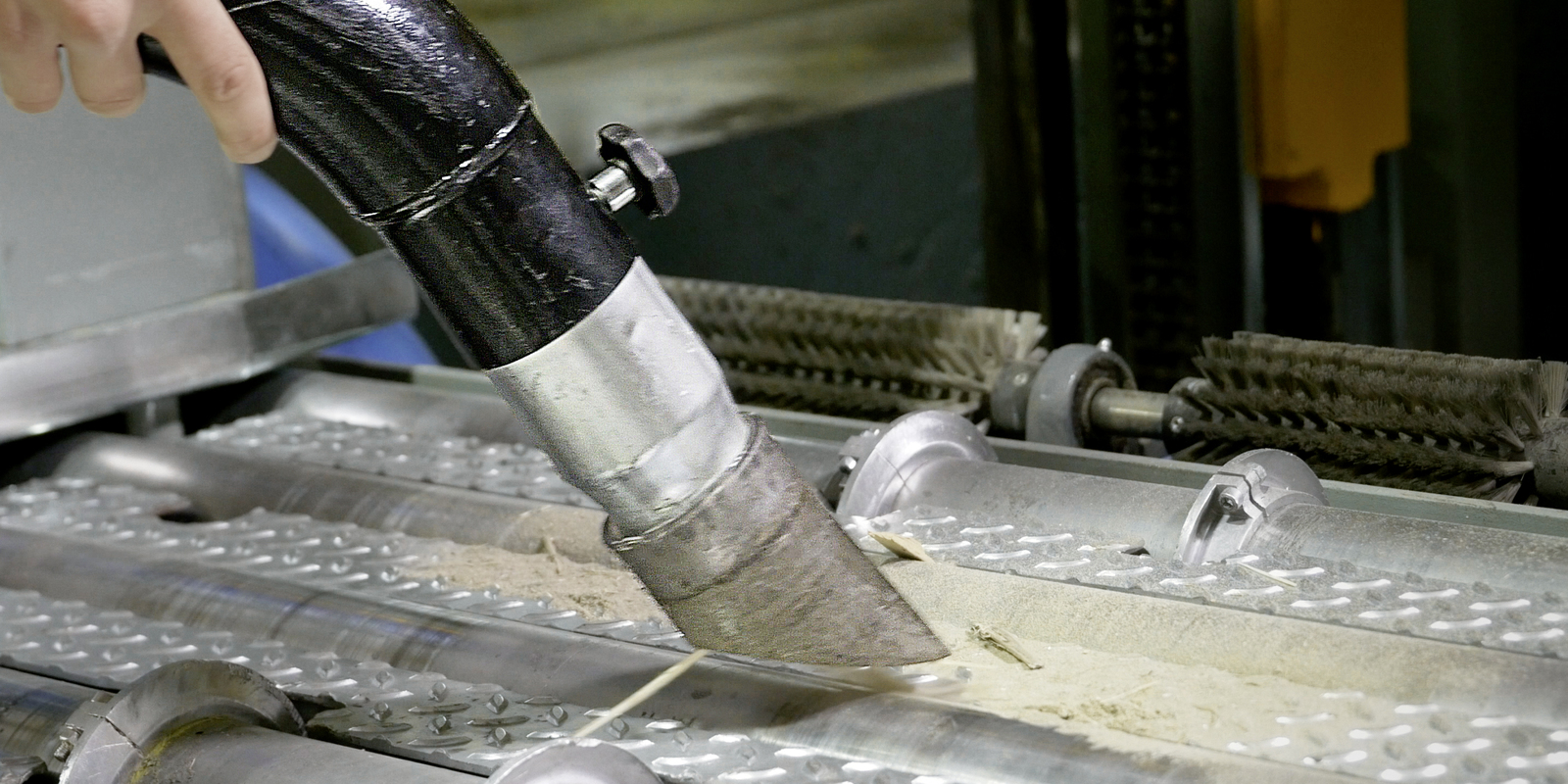
Tip:
A system for automatic pallet cleaning can also be adapted to different pallet sizes. To do this, only the width of the brushes used and the power of the stationary extraction system need to be adjusted.
Other solutions for a clean production environment
It is not just logistics processes that benefit from pallet cleaning; production also sees the benefit of increased cleanliness.
Learning from logistics: potential solution for production
Many companies work with Kanban systems to flexibly control production. First developed in Japan, this method organises the flow of materials and work processes using visual signals (known as Kanban cards). This often involves the use of plastic pallets and crates, which pass through the entire production process. Another potential area of application for automatic extraction is in the automatic and efficient cleaning of containers and pallets in buffer stations or return stations. This could increase cleanliness throughout the entire production process. A clean production environment improves the quality of the manufactured products and increases the safety of employees.
Warehouse cleaning
It is certainly advantageous to have your material warehouse looking spick and span. This is not only true of very small storage rooms, such as those in workshops, but also applies to very large warehouses. However, occupational health and safety and the protection of warehouse material are always key issues. In particular, the floors must be clean and safe to walk on to prevent the risk of accidents caused by inadequate cleaning. Such cleaning can be carried out efficiently using individually configurable (vacuum) sweepers and scrubber dryers.
Suitable products for your area of application
Find a wide range of technology at lightning speed – with the Kärcher Professional product finder
In no time at all, we'll show you the exact Kärcher Professional machine that best suits your specific cleaning task.