Cleaning production facilities
Clean production facilities and surrounding areas are fundamental to smooth processes, safety and product quality. Consequently, keeping production plants clean is a key to success for any company, whether it is in the automotive, food industry, metal or chemical industry. Each and every industry struggles with specific types of dirt that require custom cleaning solutions. Soiling occurs either as a by-product of the production process or as a result of unforeseen incidents, such as leaks. The various types and origins of dirt give rise to different ways of efficiently integrating cleaning tasks into everyday production.
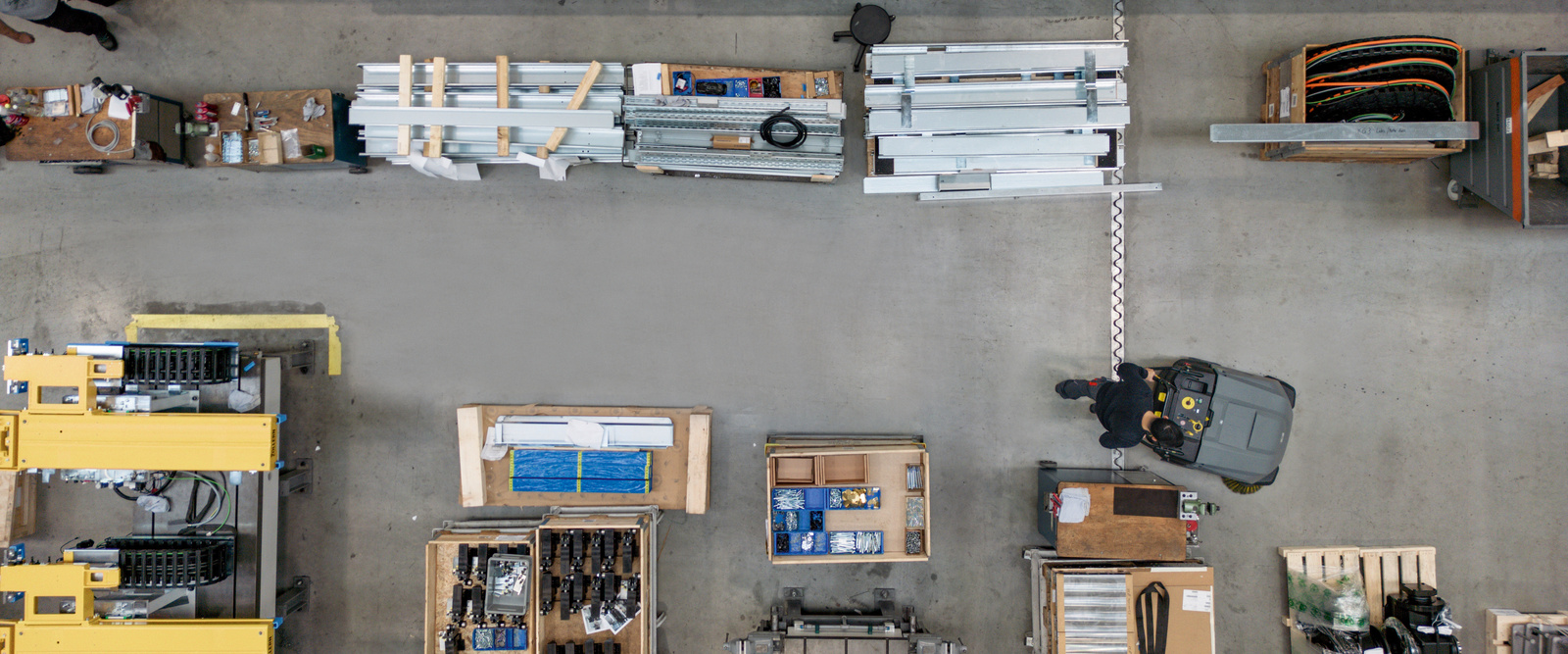
Floor cleaning: stopping the spread of dirt
Large halls, long aisles – keeping floors clean is hugely important to production. It is the first step to minimising the amount of dirt found in the production environment, for keeping automated processes running smoothly and for keeping production facilities clean.
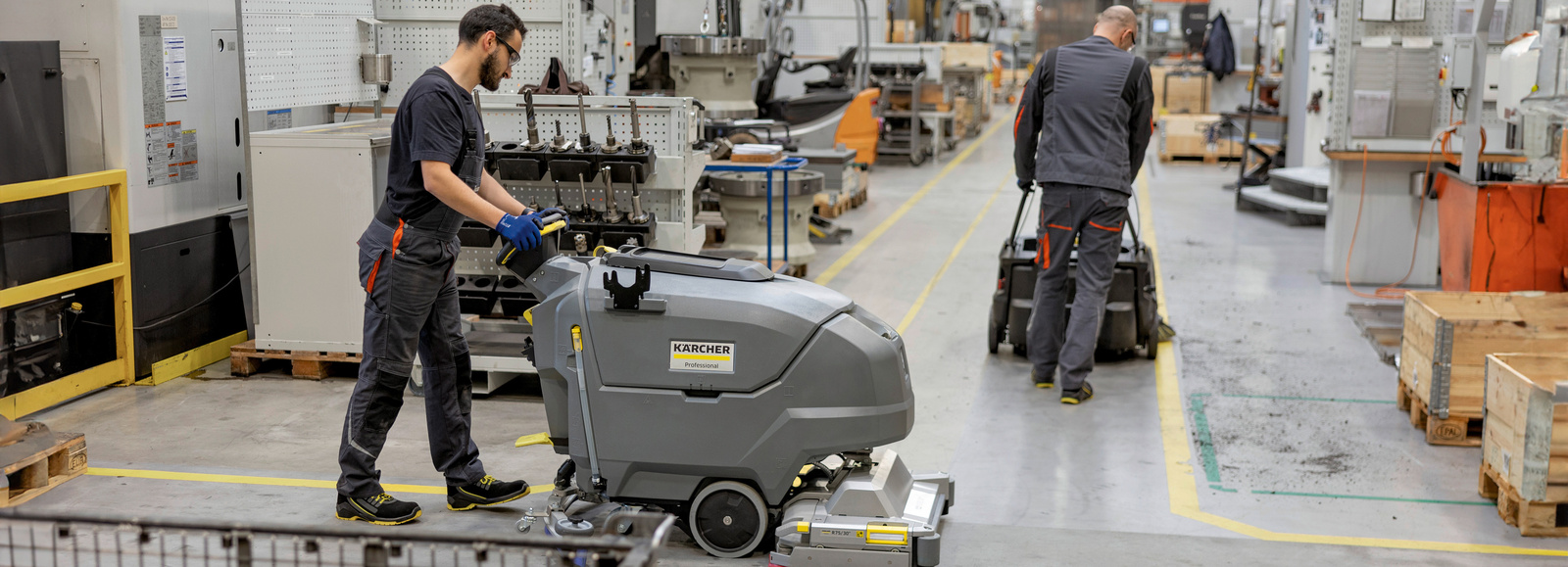
Automation demands cleanliness
In modern production plants, autonomous forklift trucks are essential for maintaining the flow of materials between logistics and production. In order for these vehicles to navigate safely using sensors, the texture of the floor must meet the defined value. If dirt, spillages or similar are found anywhere, there is a risk of accidents – for employees, as well as for autonomous forklift trucks. By cleaning regularly, incidents and inefficiencies in the process chain can be avoided.
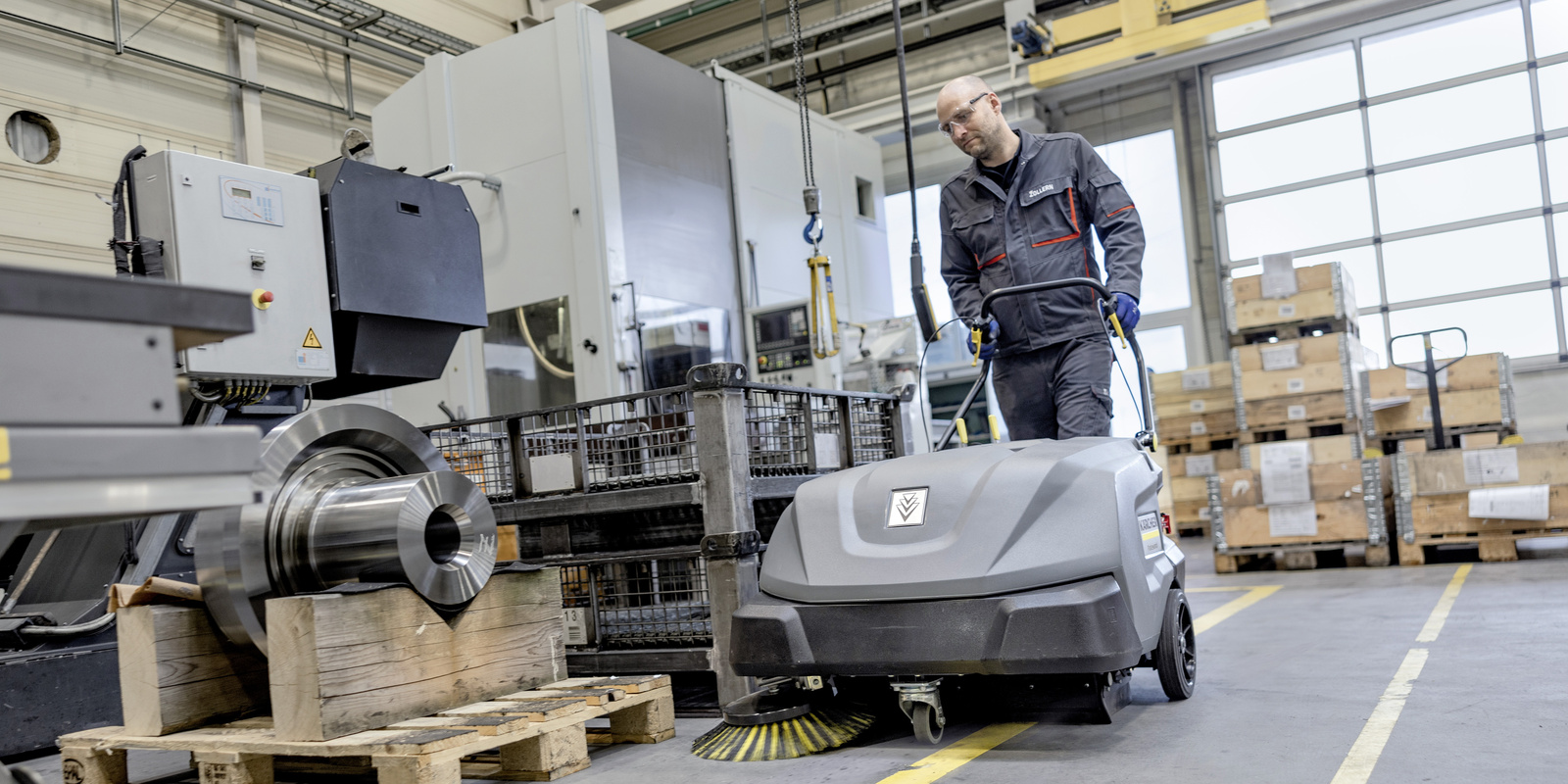
Sweeping and scrub vacuuming on rotation
Depending on the focus of production and the types of dirt present, it is advisable to alternate between sweeping and scrub vacuuming. In normal operations, for example, sweeping alone is sufficient for four to five consecutive days before then carrying out a thorough clean using a scrubber dryer. Sweepers should be selected in the appropriate design and have a coarse dirt flap to pick up larger debris.
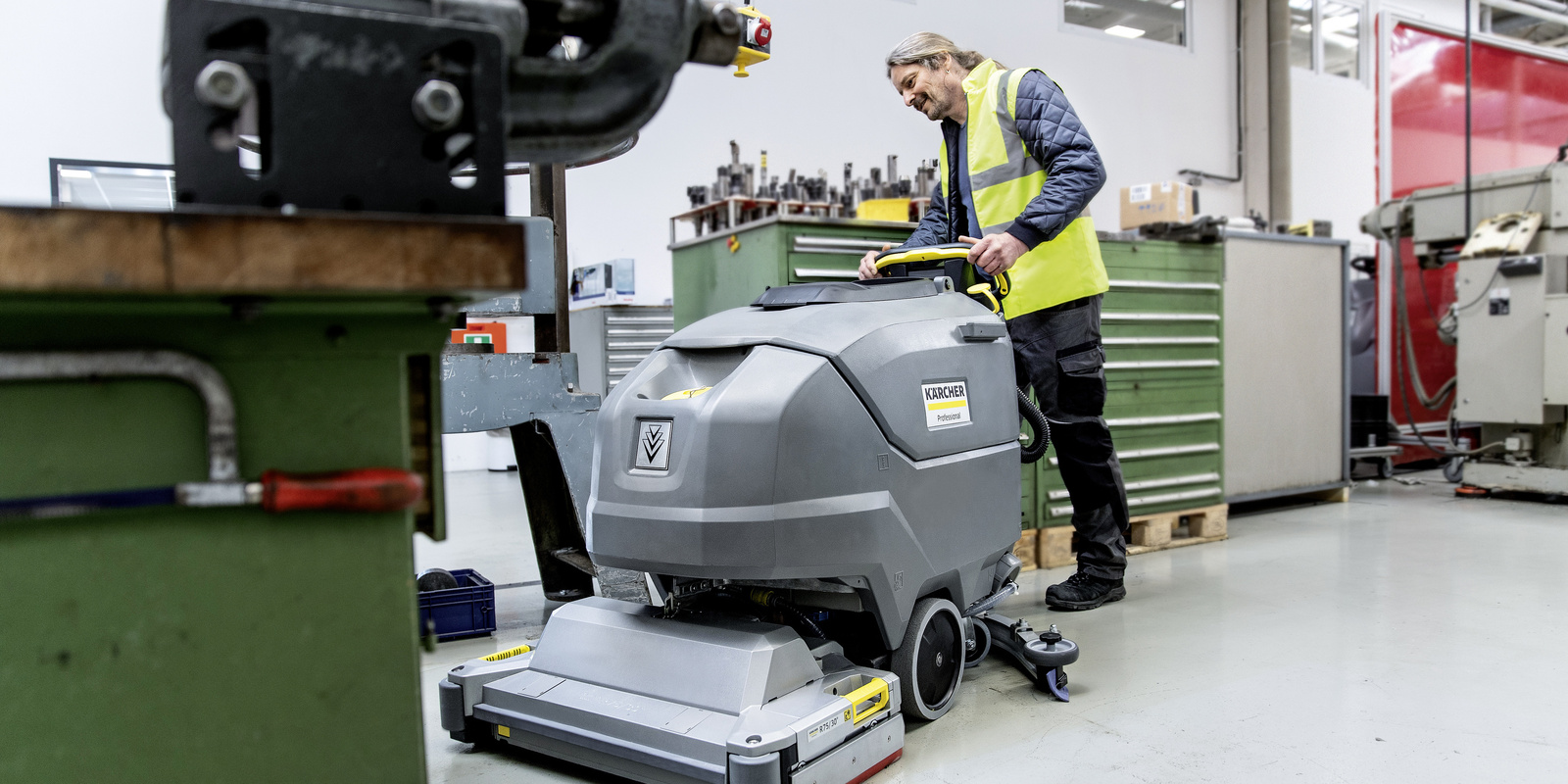
Ride-on models are the right choice for scrub vacuuming large open expanses of flooring. By assigning scrubber dryer robots to suitable areas, the workload can be can reduced further. Tighter spaces, such as those around pick stations, can be cleaned effectively with push machines. The one-step method, which combines scrubbing and vacuuming in a single work step, is used for maintenance cleaning. Meanwhile, the two-step method, which involves scrubbing with detergent first and then vacuuming after a suitable contact time, is more commonly used for deep cleans.
Tip 1 – Scrubber dryers with roller brushes for uneven floor surfaces:
Industrial floors are often plastic-coated and smooth – the material properties determine how rough or smooth the floor texture is. Nevertheless, there are often still uneven areas, created by walkways and transit routes that are more effectively cleaned using scrubber dryers with roller brushes than using disc machines.
Tip 2 – Alternate between alkaline and acidic detergents:
Organic soiling can be removed with alkaline detergents, and mineral soiling with acidic detergents. Used in an alternating 4:1 cycle, these ensure hygienic cleaning results.
Cleaning industrial floors
Industrial floors require particular care and attention – both during manufacture and in terms of their coating, cleaning and maintenance. This is because they not only have to withstand a considerable amount of strain, but they also need to meet occupational safety standards at the same time. Which cleaning method to use depends largely on the texture of the floor.
Surface cleaning for smooth processes
Endless surfaces: automation, sensor technology and robotics ensure higher cycle times and often help to ease the ever-present shortage of skilled labour. Smooth-running processes are essential too, so it is becoming increasingly important to clean the surfaces of intricate systems in order to prevent malfunctions.
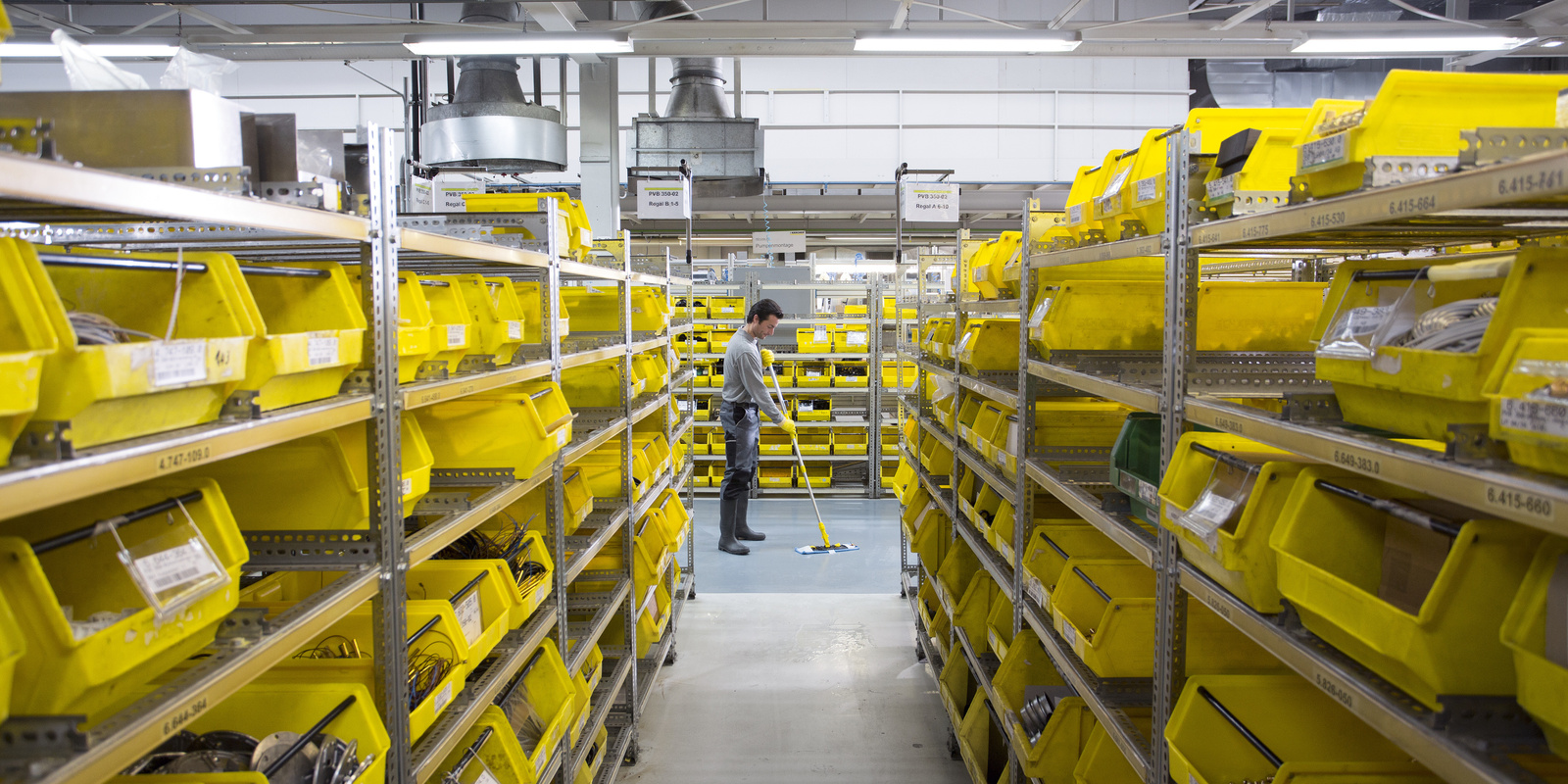
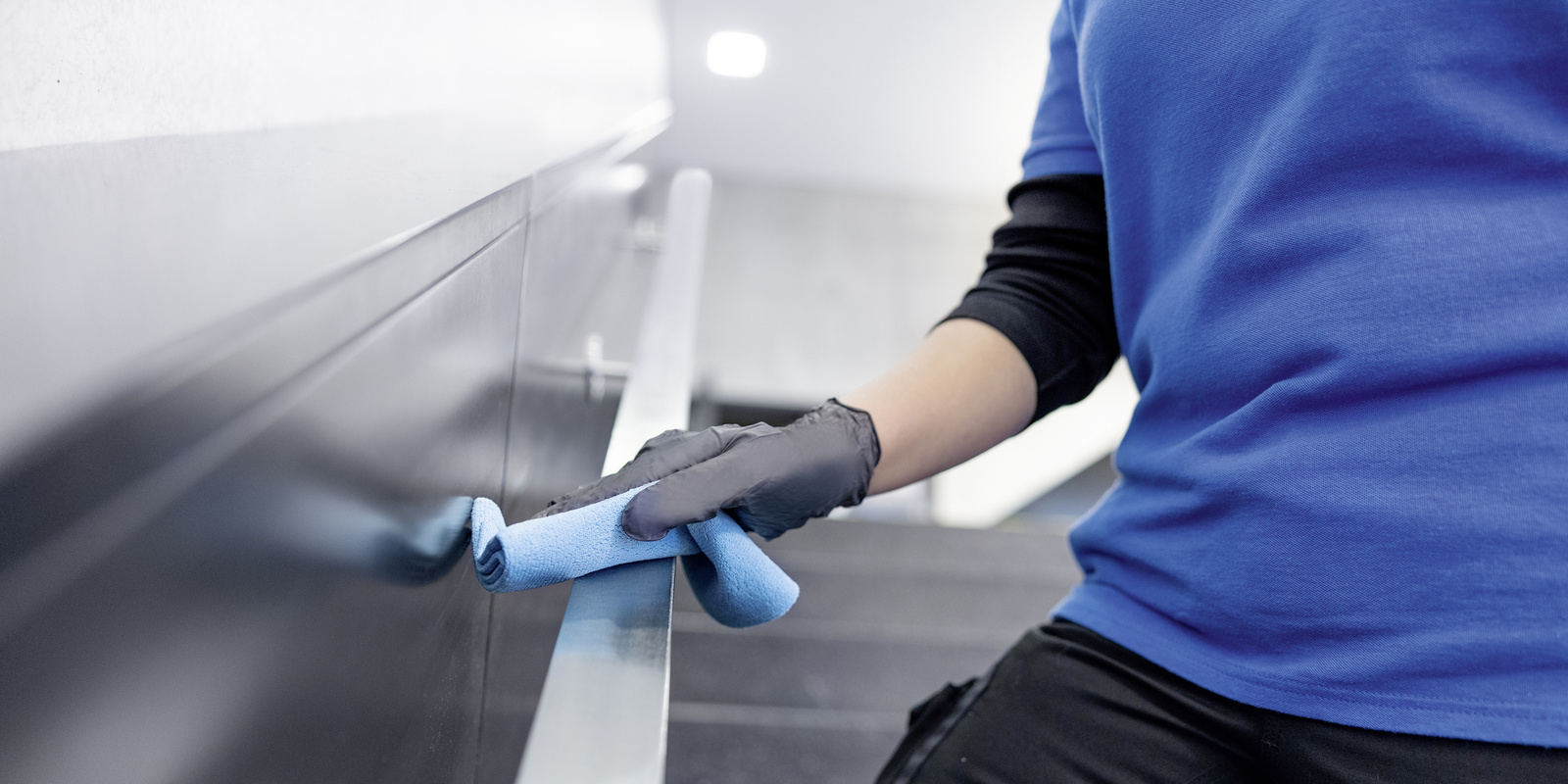
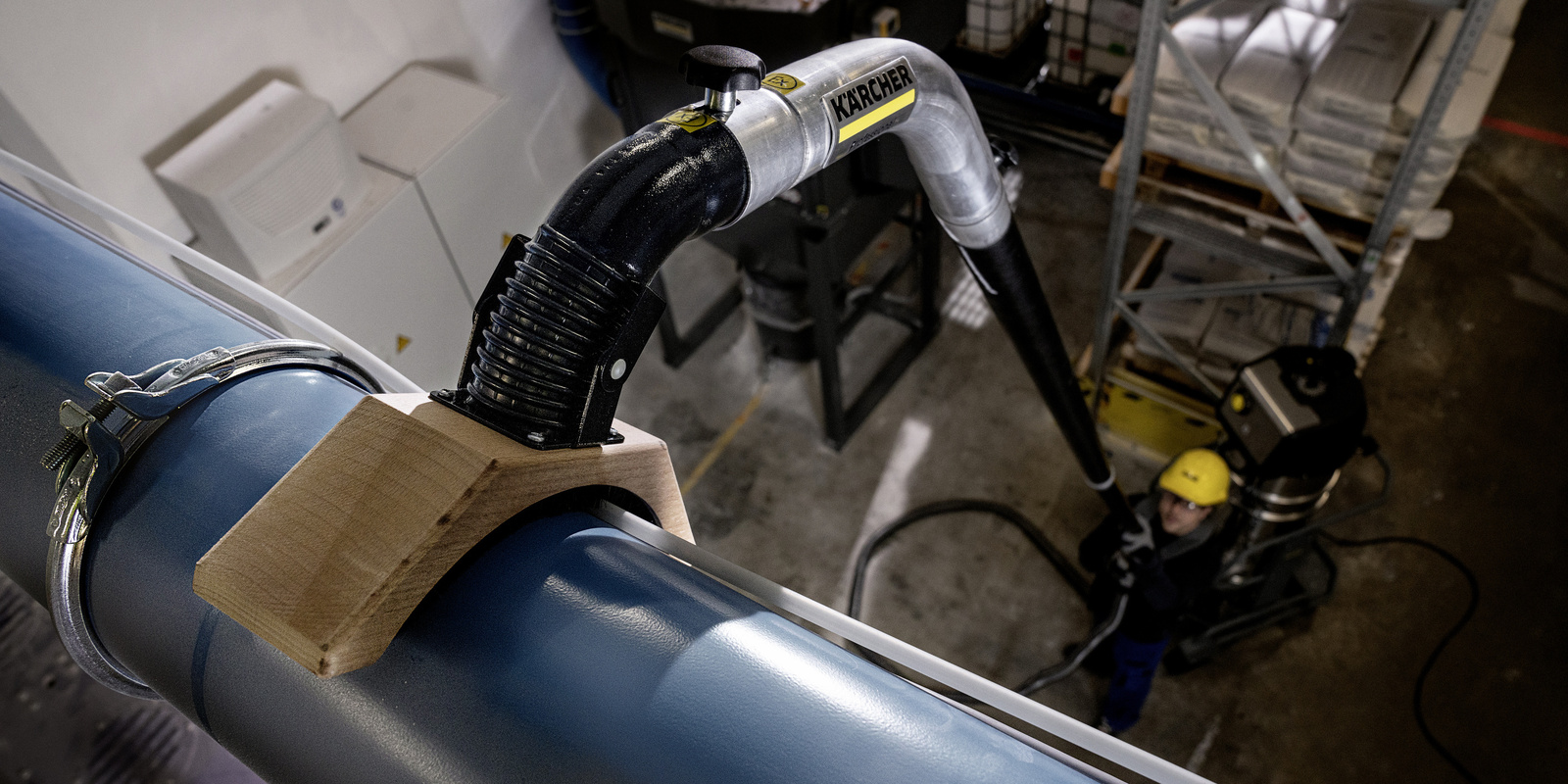
Creating solid framework conditions
Efficiency is the main driving force behind industrial companies. The aim is to increase output while minimising input and, ideally, to improve quality in the process. Automated production processes are designed to do precisely that, though these need a very specific environment if there are to be no malfunctions. Relevant parameters, such as temperature, humidity etc., are kept constant and controlled by means of remote monitoring. Cleanliness is also a parameter in the defined environment, because sensors do not work when dirty. Therefore, on the one hand it is necessary to reduce the ingress of dirt as much as possible or even prevent it completely. On the other hand, surfaces in the production environment must be cleaned thoroughly on a regular basis, especially where highly sensitive sensors are used.
Manual cleaning between production shifts
This is a task that can only be carried out manually before, after or between production shifts. In order to work quickly and efficiently, it is advisable to use a modular cleaning trolley, stocked with the necessary manual equipment. Pretreated or spraying methods are advisable for these tasks. For the former, employees use microfibre cloths that have already been double-folded and soaked with the specified amount of detergent. Alternatively, a spray bottle of detergent can be used to wet the cloth at point of use.
Tip – Surface cleaning as required:
Surfaces on control cabinets, equipment or machinery are cleaned when dirt has built up. Regular cleaning is not necessary.
Where does dirt in the production environment come from
In production, a distinction is made between two sources of dirt: the dirt is either an integral element of the production process or a consequence of unplanned events.
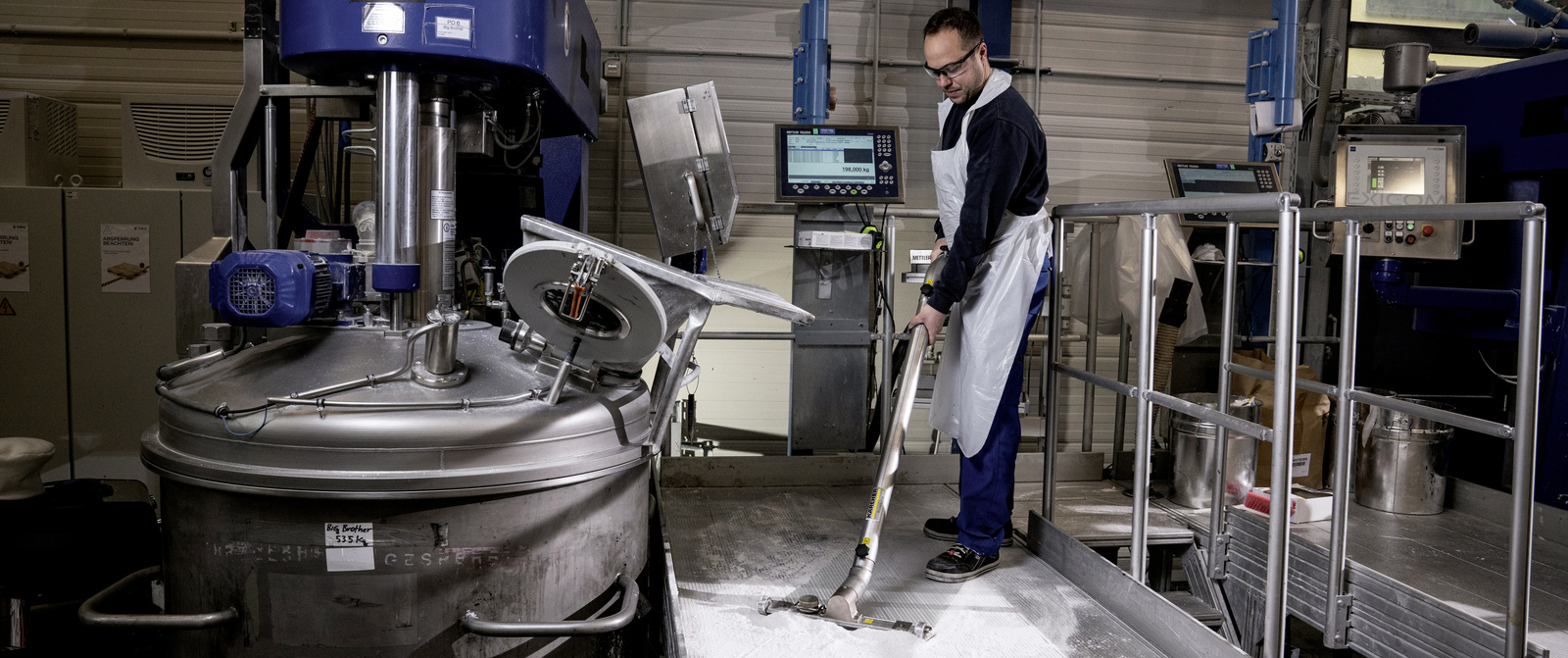
Dirt as 'part of the process'
You can't make an omelette without breaking eggs – and you can't machine wood without making sawdust. Dirt created by the production process is a side effect in many production environments. To keep this dirt under control at all times, solutions can be integrated into the process, including film extraction systems or pallet cleaning systems, stationary extraction systems for dust, swarf, etc. and stationary high-pressure units. These solutions play an important role in maintaining a clean production environment. Dirt particles are removed during operation, ensuring high product quality and the smoothest possible processes.
Cleaning pallets
In the field of logistics, wooden and plastic pallets not only bring goods into the company, they also bring dirt into the warehouses. This, in turn, increases the cleaning effort. Automated warehousing systems also use sensors such as light barriers, which can become dirty, disrupting processes in warehouse systems. Systems installed upstream of the incoming goods area are designed to automatically extract dirt and debris from pallets, significantly reducing the amount of dirt and helping to minimise technical problems. How does this work and how else can companies benefit from it?
Dirt as a result of accidents
Dirt that arises as a result of malfunctions in the operating process, such as leaks or application errors, poses a particular challenge. It is important to make the necessary equipment, such as industrial vacuums, sweepers or scrubber dryers, available to deal with any unforeseen incidents quickly and efficiently. Regular visual inspections help to recognise potential hazards, for example leaking fluids, before accidents happen. This also helps to reduce the cleaning workload: if, for example, a spilled bag of flour in a large bakery is discovered quickly, the flour can simply be vacuumed up. This prevents the flour from being trodden around and exposed to moisture to form a sticky dough that is far more difficult to clean. This example relates to the food industry, but each industry is faced with different challenges from different types of dirt and so, their main cleaning focus varies depending on their branch of industry.
Cleaning transport belts
Transport belts and conveyor belts are an indispensable part of everyday life in most companies – it is therefore important to maintain them carefully and to clean them regularly. Depending on the specific circumstances of the site, different cleaning solutions are available for this.
Example: loose dirt in the automotive industry
In the automotive industry, dirt is not attributable to one specific material; here, dirt includes metal, plastic, wood and inorganic materials such as binding agents or sand. Loose dirt and debris, such as residues from punching metal blanks or polishing dust, are an ever-present by-product of production. Depending on the quantity and conditions, industrial vacuums, sweepers and extraction systems could be potential solutions.

Adapting extraction equipment to production volume
It is necessary to decide which extraction solution is most suitable, depending on the scale of production and the amount of dust and swarf produced. Fully automated stationary systems are only worthwhile where large quantities of dirt build up and where cycle times and large volumes are crucial. The investment soon pays for itself, as there is no need to manually empty the swarf containers. Where smaller quantities are involved – under 100 litres of swarf per day – mobile extraction units are the right option.
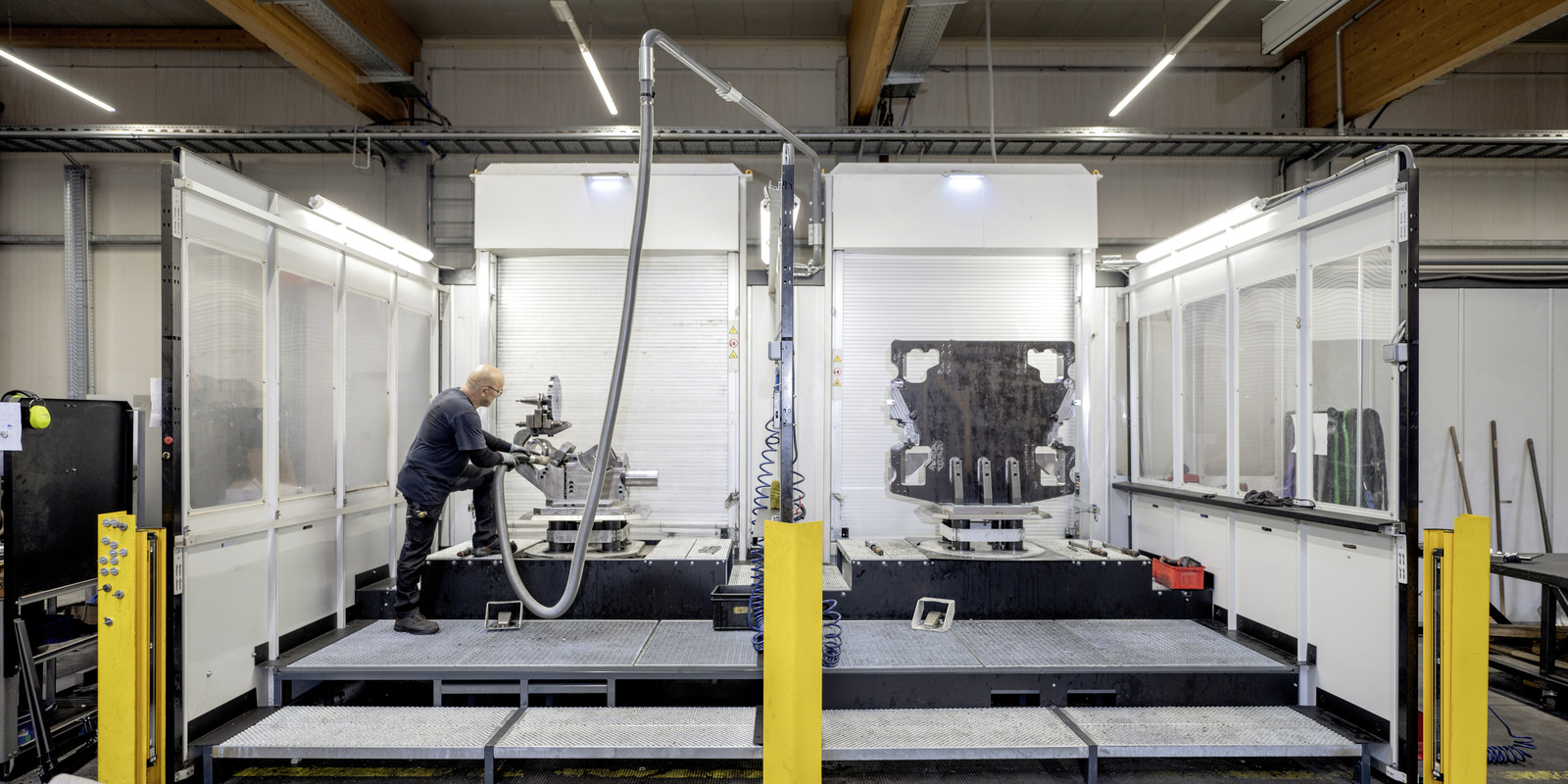
Performance and flexibility of mobile extraction units
Mobile extraction units can be made available at every workstation or used flexibly across several workstations, depending on how the processes are organised. Especially if production is frequently restructured or a relocated, mobile units are a good choice. They reliably remove swarf and fine dust from workpieces and machines. They can also be used to remove floating, lightweight swarf and general dirt from cooling lubricants.
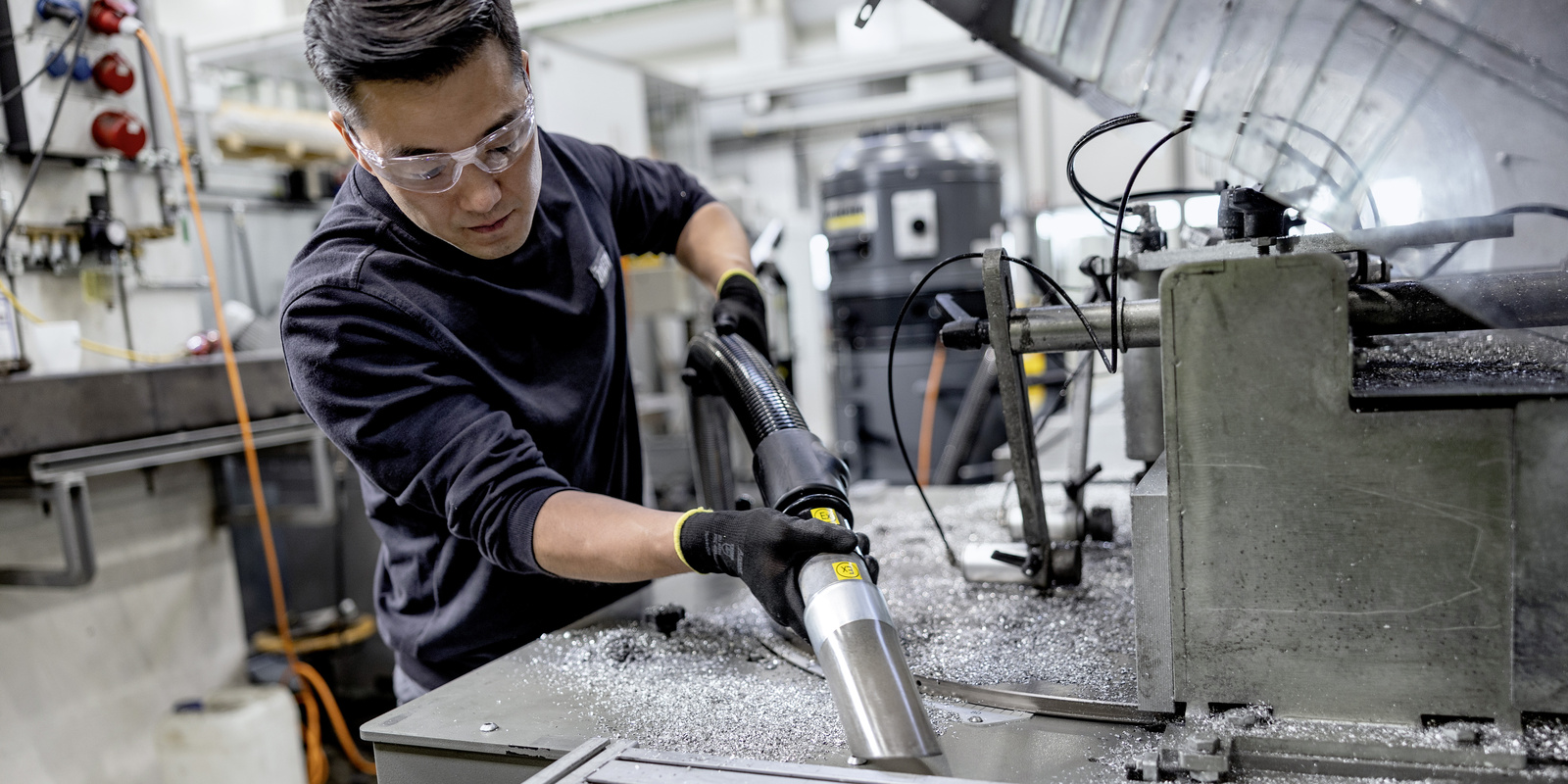
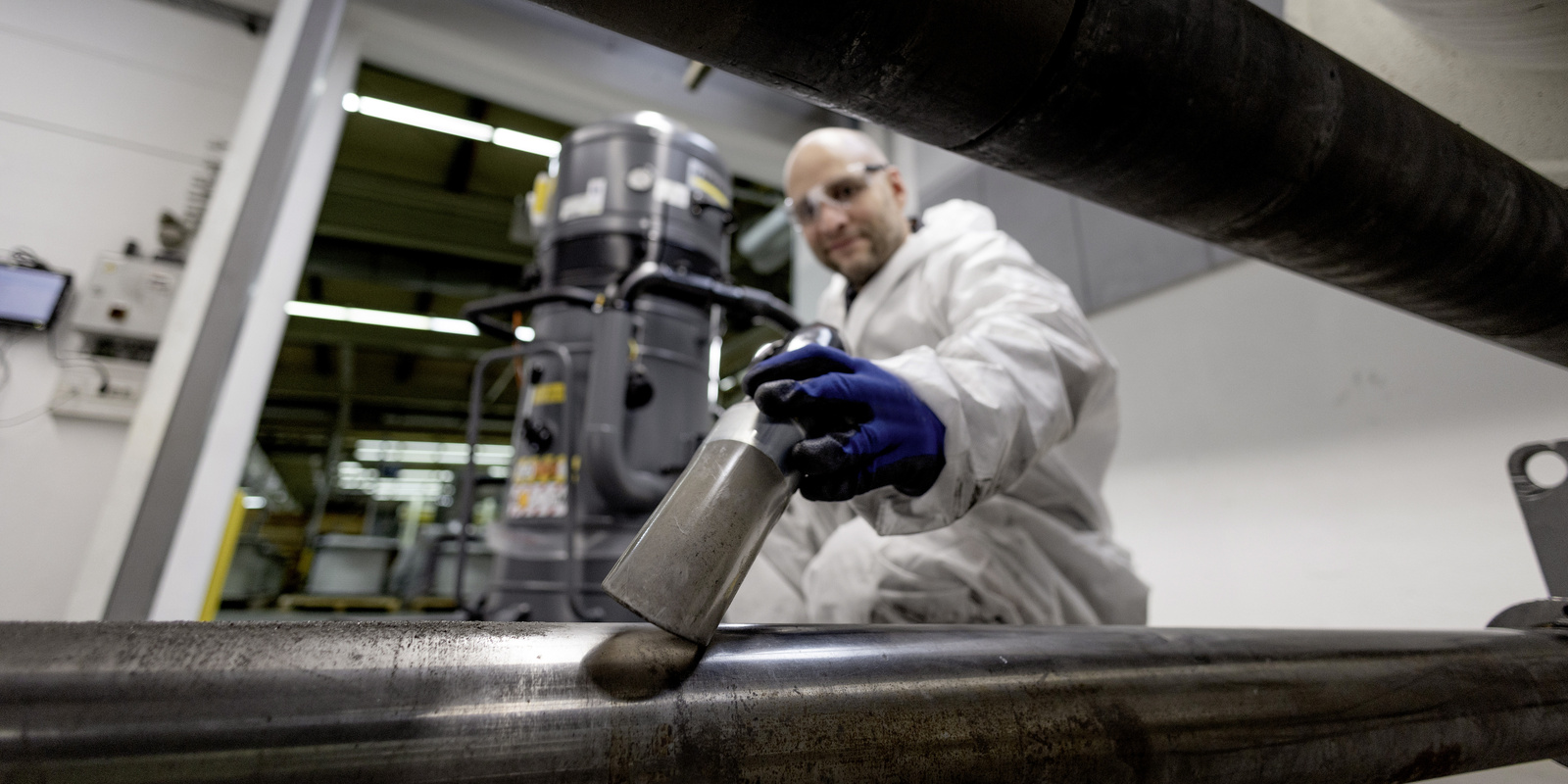
Tip – Vacuum up swarf one type at a time:
If the production processes are cleverly organised, swarf and chips can be vacuumed up one material at a time to achieve higher prices in recycling.
Automotive
People's cars are a matter close to their hearts. Customers are therefore not only looking for highly polished vehicles, they also consider a clean environment to be important – whether purchasing a car, visiting a workshop or at a service station. Achieving a spotless environment involves a wide range of challenging tasks.
Example: dusts in the food industry
Standards such as HACCP must be complied with in the food processing industry. In addition to the usual hygiene requirements, dust, including flour dust, is an important consideration because it can pose a potential explosion risk. ATEX industrial vacuums are mandatory in this environment to prevent risks.
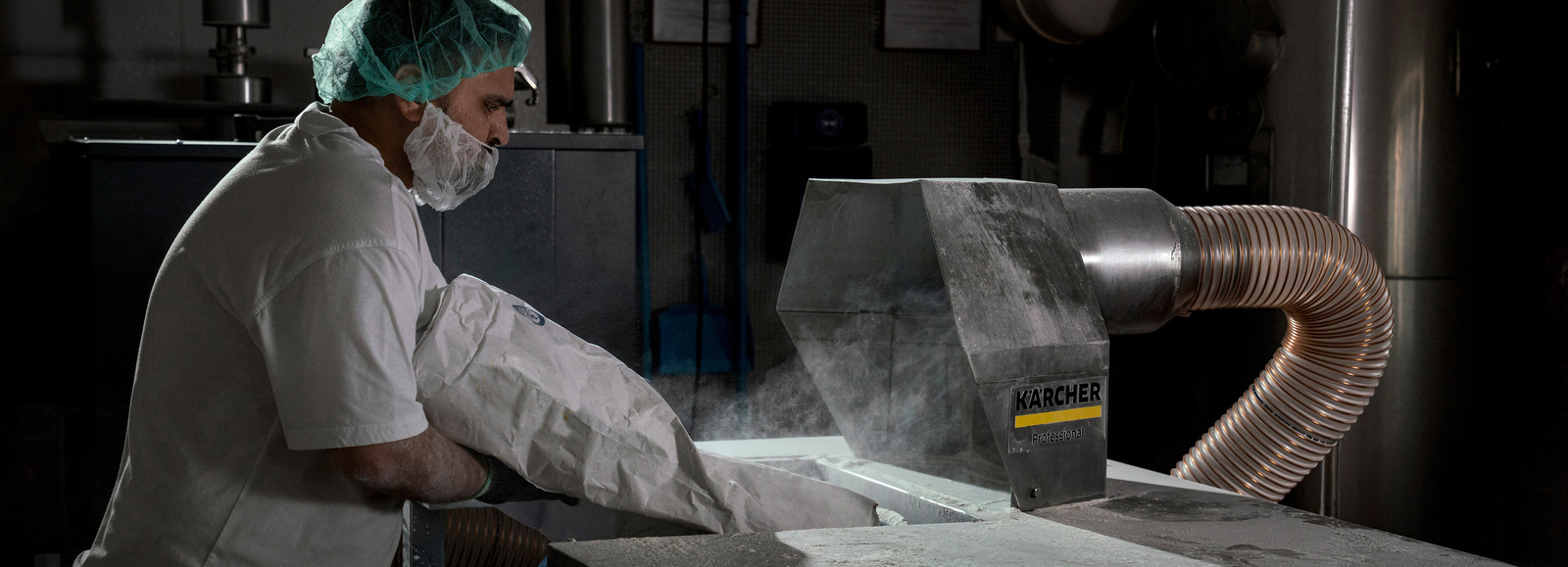
International standards for consumer safety
When it comes to handling food, cleanliness and hygiene are the number one priority for consumer safety and therefore for manufacturers. Standards such as HACCP (Hazard Analysis and Critical Control Points) help to minimise risks. How these are set up and implemented varies depending on the individual circumstances. Production processes are usually designed as closed systems in order to reduce weak points as far as possible, by minimising human intervention and standardising automated processes.
HACCP
You can't buy trust, yet making a purchase does call for a certain amount of trust – and that's exactly why the HACCP concept was developed. Safety – and therefore also cleanliness and reliable cleaning processes – play a major role in the food industry; high standards should ensure that consumers can enjoy products without any concerns. In light of this, the HACCP concept is an important tool for self-monitoring, which can be used to help identify and analyse potential hazards and bring these under control.
Preventing dust explosions with ATEX industrial vacuums
In the food industry, dust is often generated as a side-effect of production, for example, in the manufacture of baked goods when work surfaces are dusted with flour or pieces of dough are portioned up to go in the chiller. As long as the flour is in the bag, it is not a hazard. Depending on the production batch in question, however, more or less fine flour dust is produced, which becomes airborne and spreads everywhere, leading to a high risk of explosion.
For this reason, it is mandatory for large companies to use ATEX industrial vacuums to remove fine dust. According to the definition of explosion risk in ATEX (Atmosphères Explosibles), the European directive on explosion protection, many applications fall under zone 22. This means that a potentially explosive atmosphere occurs either rarely or only briefly during normal operation. Machines must be designed for use in ATEX zones and their electronics must be sealed shut to reliably prevent the ignition of explosive atmospheres.
If an area is not classified as an ATEX zone, but is still very dusty, industrial vacuums that meet the standard DIN EN 14460:2007-07 can be used. That way, any explosion remains inside the machine and poses no danger to the outside.
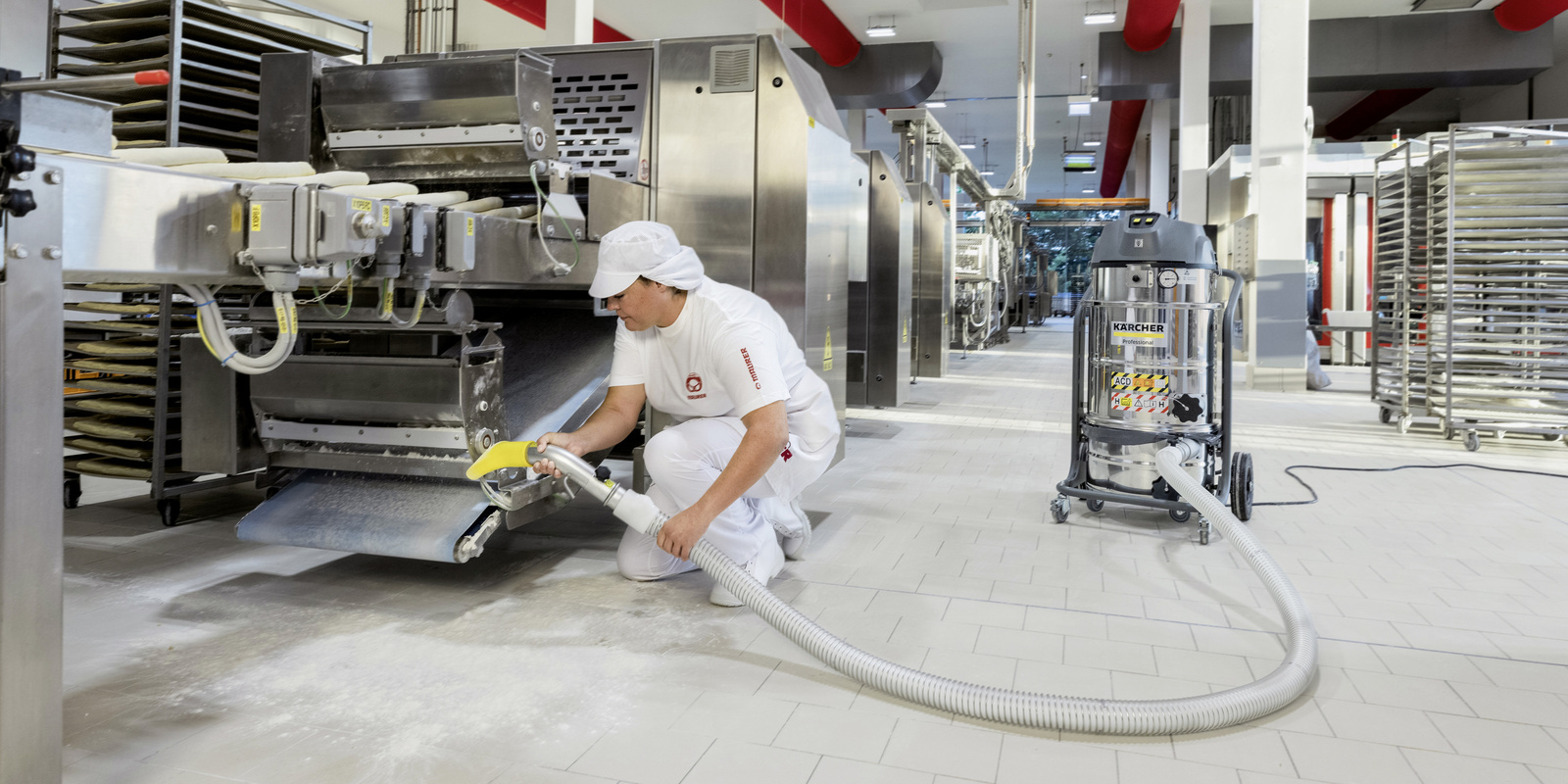
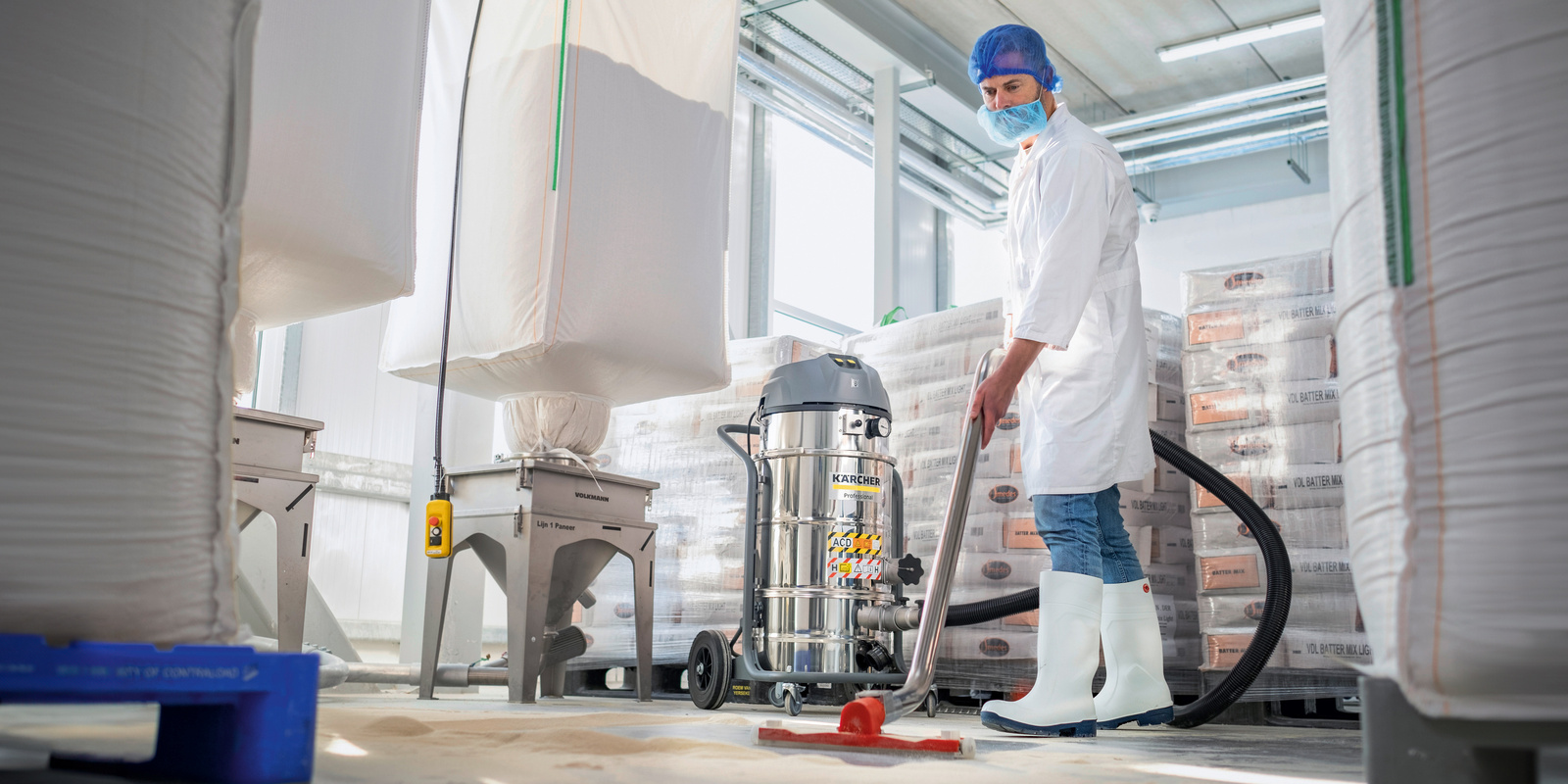
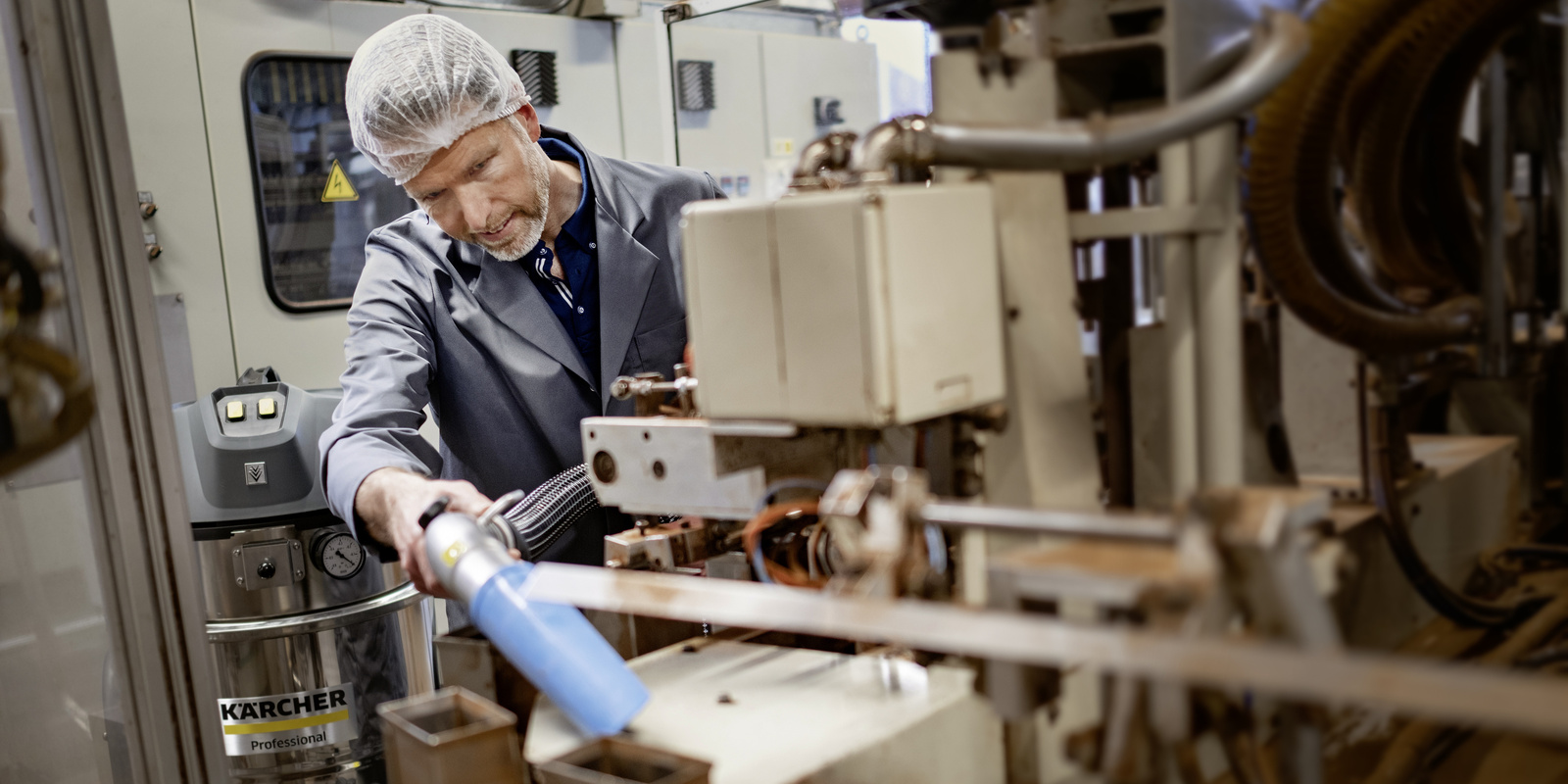
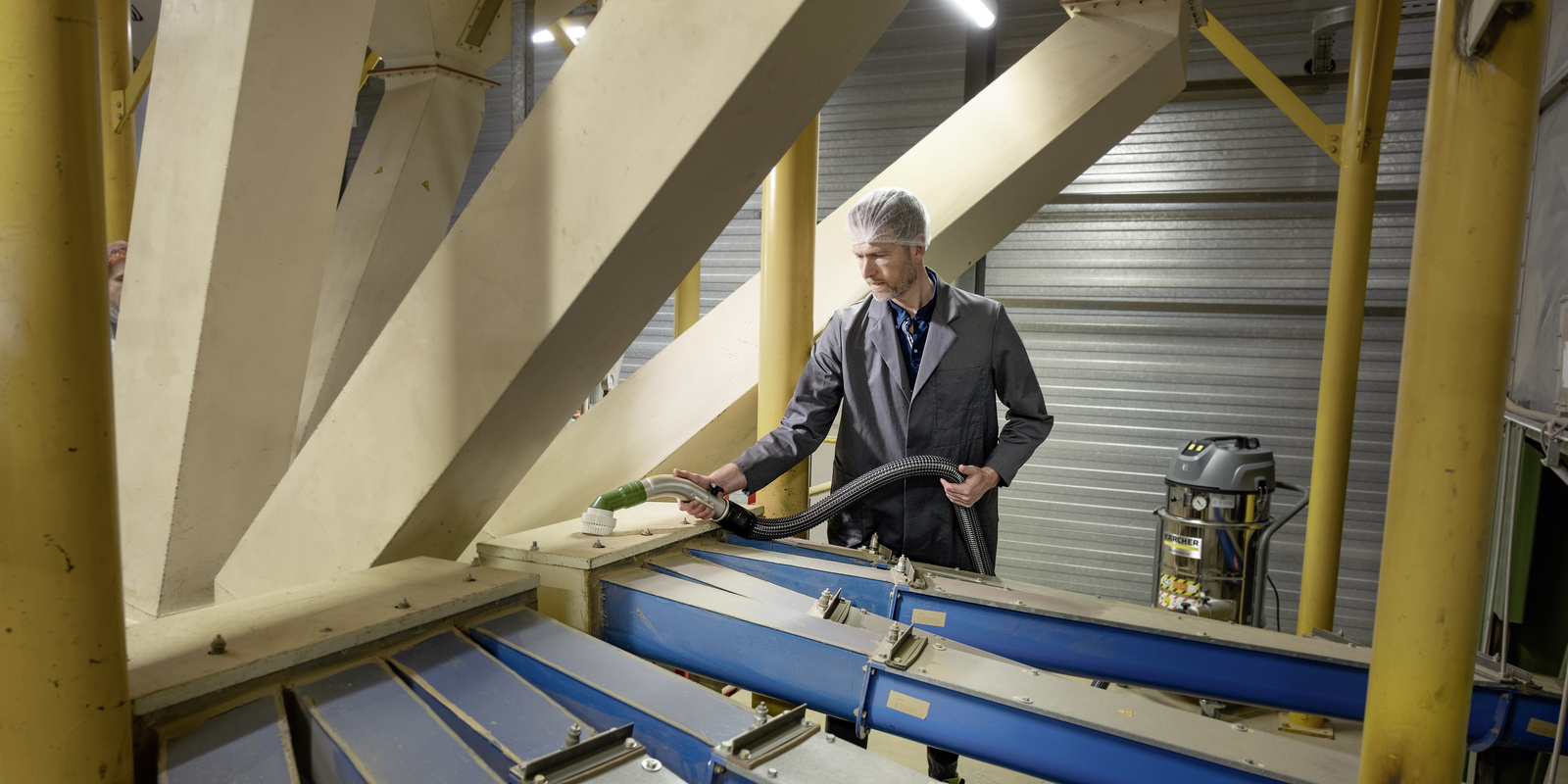
Tip 1 – Protect users with class M filter:
For all vacuum cleaners used in the food industry, ensure that the filter is for dust class M and therefore removes fine dust from the air effectively. To prevent the filter from becoming clogged with flour dust, filters should be subject to automatic cleaning.
Tip 2 – Regular cleaning is crucial:
Removing the fine dust on a weekly or even daily basis reduces the amount, making cleaning faster and more efficient overall. What's more, it stops moisture from getting trapped, which in turn prevents the formation of mould.
Cleaning in the food industry
Hygiene is the number one priority in the food industry and is safeguarded by means of risk prevention and risk assessment systems, such as HACCP. Cleaning is therefore a vital lever for achieving market success and supplying consumers with flawless products. Appropriate measures and processes must be established, depending on whether raw materials or processed products are being manufactured. This also means determining whether a lot of water is to be used – as in meat processing plants – or as little water as possible, as in industrial bakeries.
Example: greasy dirt in the metal industry
In the metal industry, numerous contaminants are produced during the machining process, especially swarf that has been made greasy by cooling lubricants, which industrial vacuums remove efficiently. In the event of accidental soiling, scrubber dryers present a good solution. When cooling lubricants need to be changed, high-pressure cleaners and detergents are used.
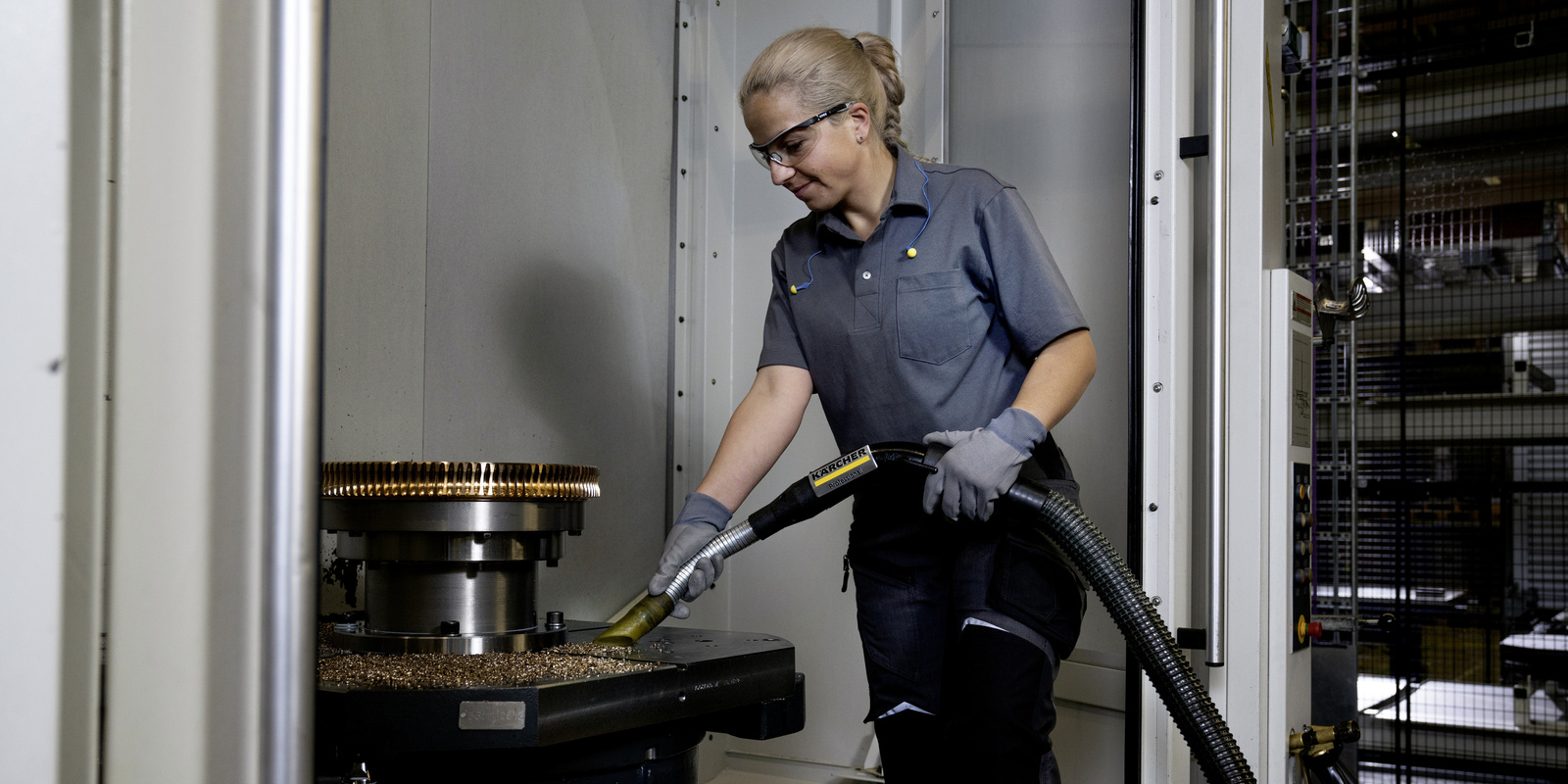
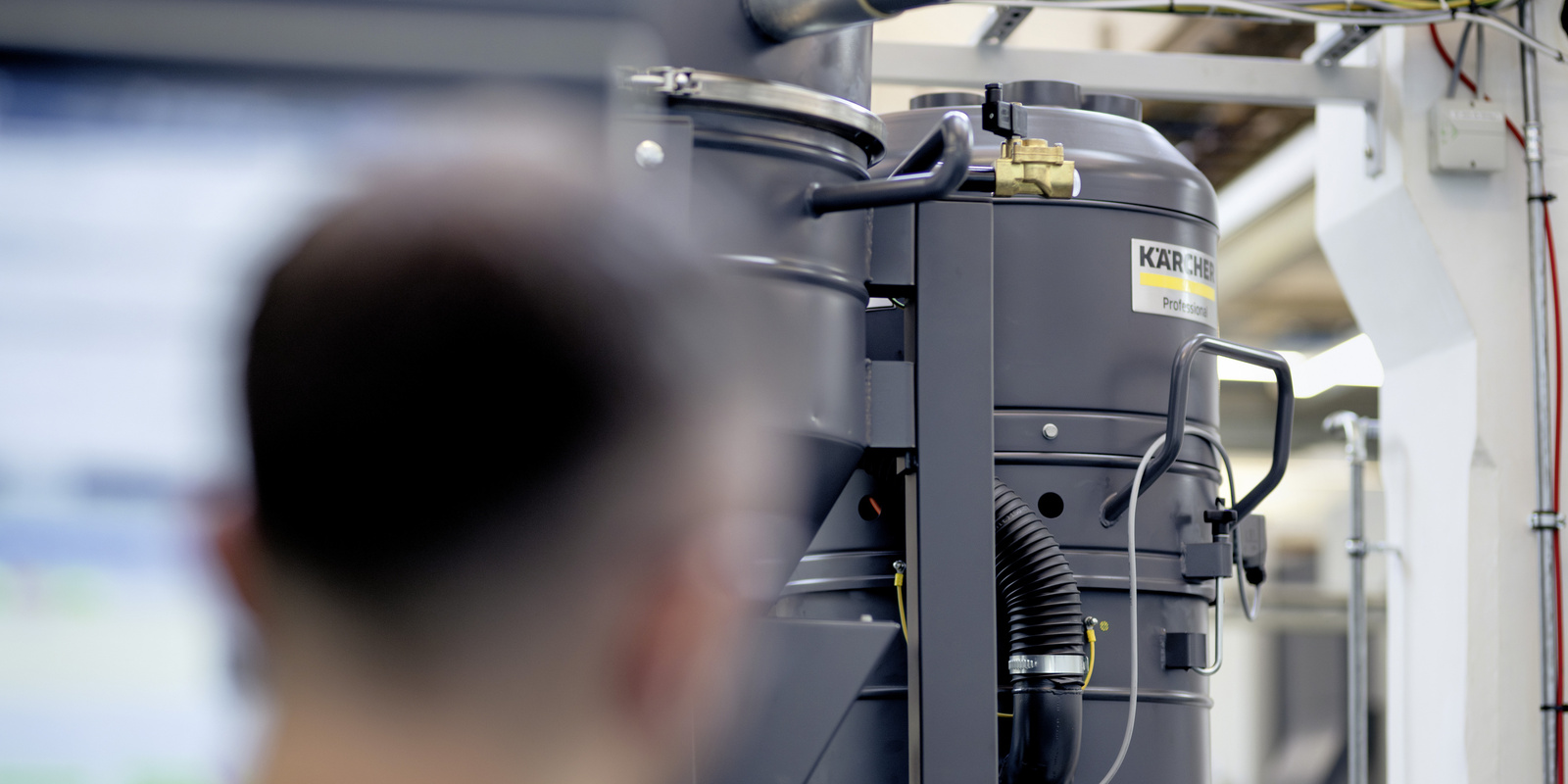
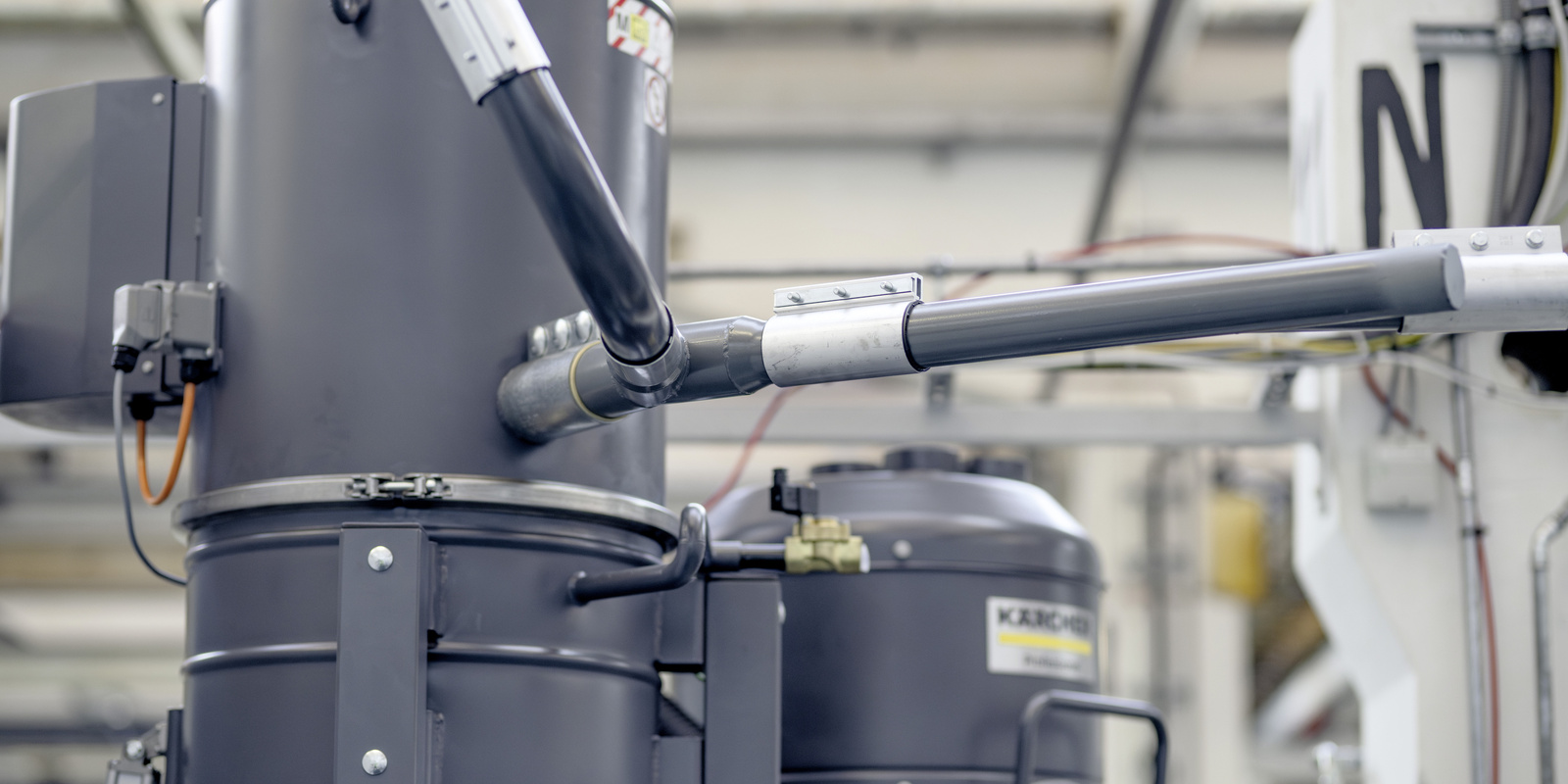
The right vacuum cleaners for production-related dirt
Whether milling, grinding or turning – all metal processing steps generate heat, caused by the friction of metal on metal. To keep processing machines operating at high machining speeds and with precision, they are treated with cooling lubricants, i.e. sticky, greasy fluids. Dirt produced by the machining process, such as greasy swarf, must be removed in order to maintain precision in production. This is where industrial vacuums come in, either as a stationary manually operated setup, consisting of plant, pipework and vacuum cleaner, or as an individual machine that is permanently installed at the machining station.
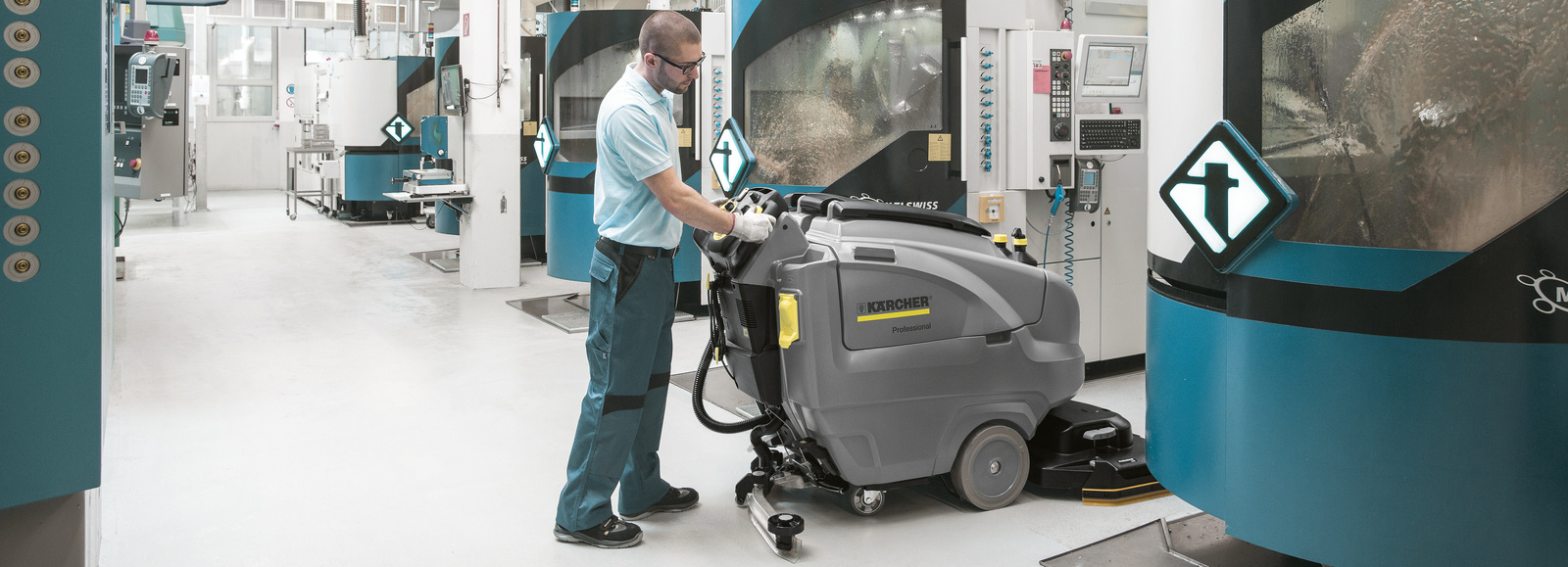
To the rescue: scrubber dryers in response to accidents
To prevent the risk of accidents on floors that have been made slippery by leaks, any spillages are vacuumed up by small, compact scrubber dryers, which can easily be manoeuvred through the tight spaces of the production halls. The use of a grease-dissolving detergent is crucial here, as is very good suction. Models with a brush head have a sweeping function and a sweeper drawer to pick up swarf as well. Models with a disc head are not suitable because swarf can get caught in the disc and leave scratches on the floor.
Replacing cooling lubricant using high pressure
Over time, the quality of the cooling lubricant deteriorates and the fluid needs to be replaced: the old coolant needs to be extracted, residues need to be rinsed off and the lines need to be thoroughly cleaned as well. The cooling lubricant tank can be cleaned using a mobile high-pressure cleaner, i.e. a small machine with a short cup foam lance, in combination with a grease-dissolving detergent. The detergent is then rinsed off. Once cleaned, the tank is then refilled with fresh coolant.
Tip – Hot water cleans cooling lubricant tanks more thoroughly:
Cold water is usually sufficient for cleaning the cooling lubricant tank, although hot water can achieve more thorough results faster.
Cleaning in metal processing
Metal processing is often highly automated, with various machining steps, such as sawing, turning, drilling and milling, being combined with the application of coatings where necessary. The often complex components call for a well-coordinated process in order to achieve the required level of precision and product quality. Efficiency in processes is also important in order to stay within budget and to produce profitably. With this in mind, cleaning is an important factor, since it removes many potential stumbling blocks on the way to the product.
Example: ingrained dirt in the chemical industry
Stationary high-pressure units with movable interior cleaning heads for ingrained deposits are well suited for cleaning containers in the chemical industry. Stubborn dirt in the pipes doesn't stand a chance against ultra high-pressure cleaners or powerful dry ice blasters.
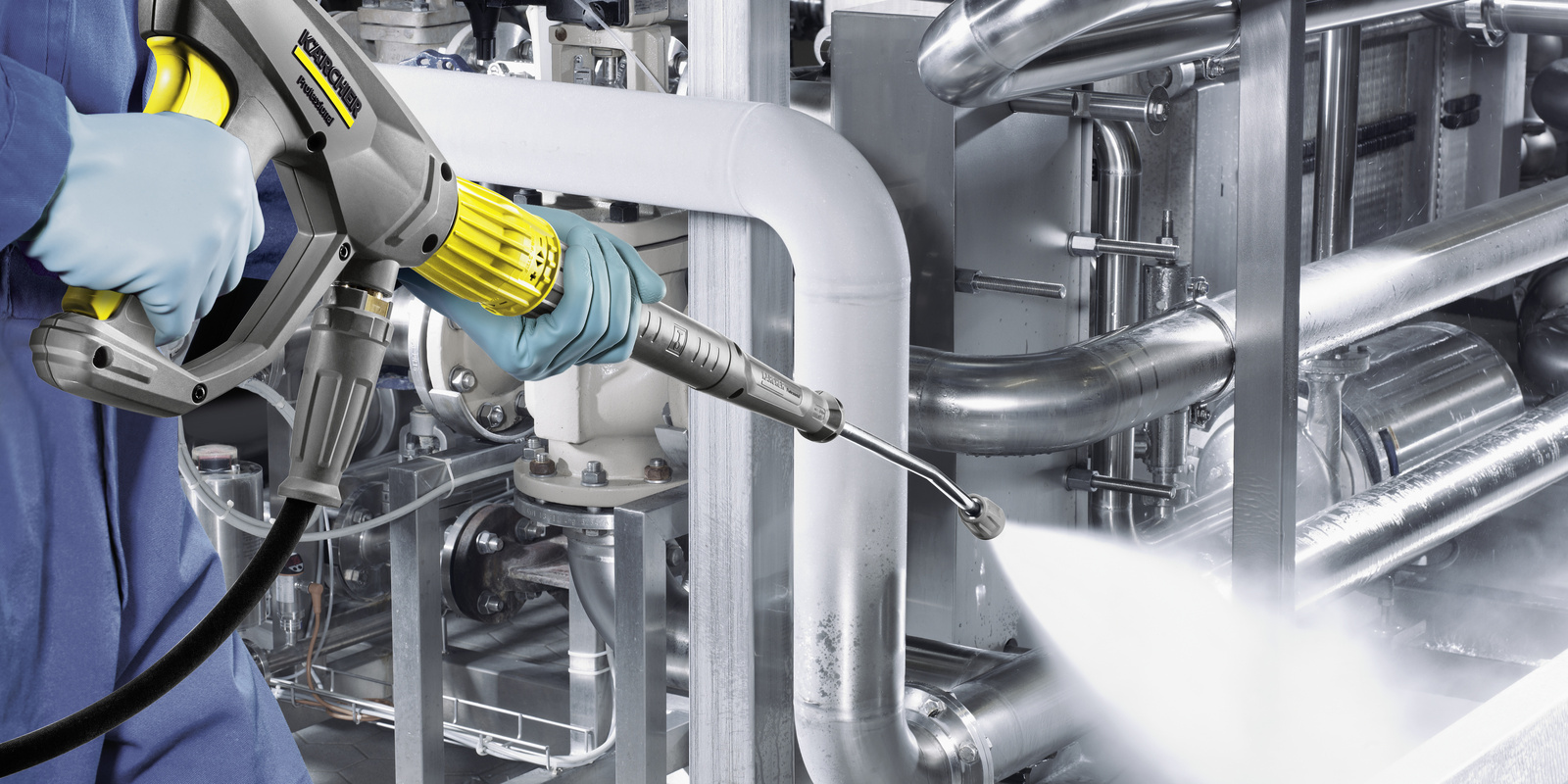
Cleaning containers efficiently with stationary high-pressure units
A central issue in the chemical industry is how to transport and store primary products. Cleaning out containers forms a central focus in this. This also includes cleaning the agitators, primarily using stationary high-pressure units with movable interior cleaning heads. These have a 360° rotating nozzle and are fed through the container to remove stuck-on deposits.

Ultra high-pressure cleaners and dry ice to combat stubborn dirt
During the complex chemical handling process, where primary products are processed into the product, stubborn dirt builds up in pipes or filters of the production equipment, which has to be removed several times a year. Ultra high-pressure cleaners with a pressure of 500 to 1000 bar provide an effective remedy, with the high pressure acting as a cleaning tool and removing the need for detergents. Alternatively, dirt can be removed using a powerful dry ice blaster, which is especially gentle to surfaces. The performance depends on the quantity of compressed air, with which the dry ice hits the surface.
Cleaning in the chemical industry
The chemical industry is under increasing cost pressure, primarily due to fluctuating energy prices. Furthermore, very strict standards and regulations must be adhered to in order to avert risks in the process that could endanger employees, the environment or the general public. In light of this, cleaning is ultimately a driving force behind efficiency, safety and quality, because cleanliness ensures smooth processes, reduces downtimes and assures product quality. Occupational safety can also be better guaranteed in a clean environment, since leaks, for example, can be resolved fast.
Suitable products for your area of application
Find a wide range of technology at lightning speed – with the Kärcher Professional product finder
In no time at all, we'll show you the exact Kärcher Professional machine that best suits your specific cleaning task.