Cleaning transport belts and conveyor belts
Transport belts and conveyor belts are an indispensable part of everyday life in most companies – it is therefore important to maintain them carefully and to clean them regularly. Depending on the specific circumstances of the site, different cleaning solutions are available for this.
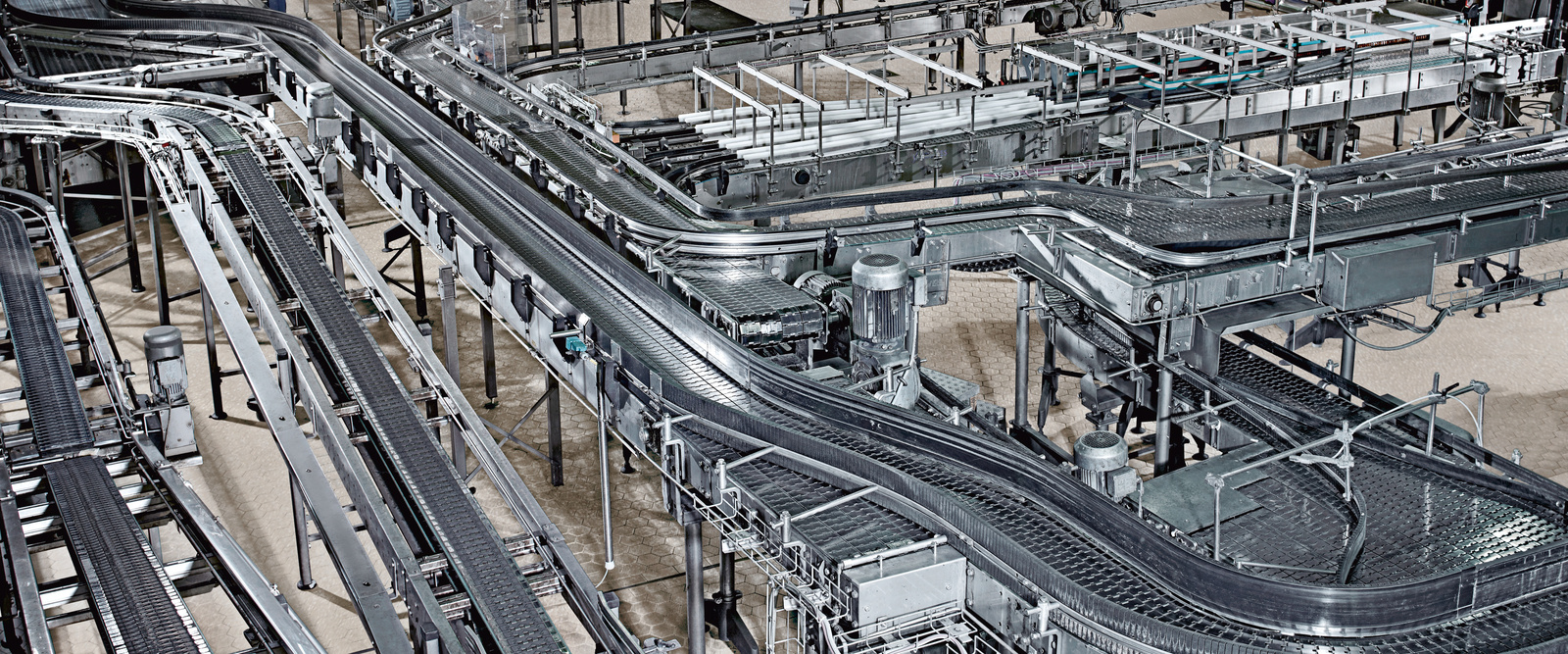
Keep on moving: cleaning to prevent downtime?
The range of applications for transport belts and conveyor belts within a company are wide-ranging – whether operating within the production line, transporting the product to the warehouse or conveying packaged goods for onward transport. Whatever the application, however, they are of immense importance for efficient processes within a company.
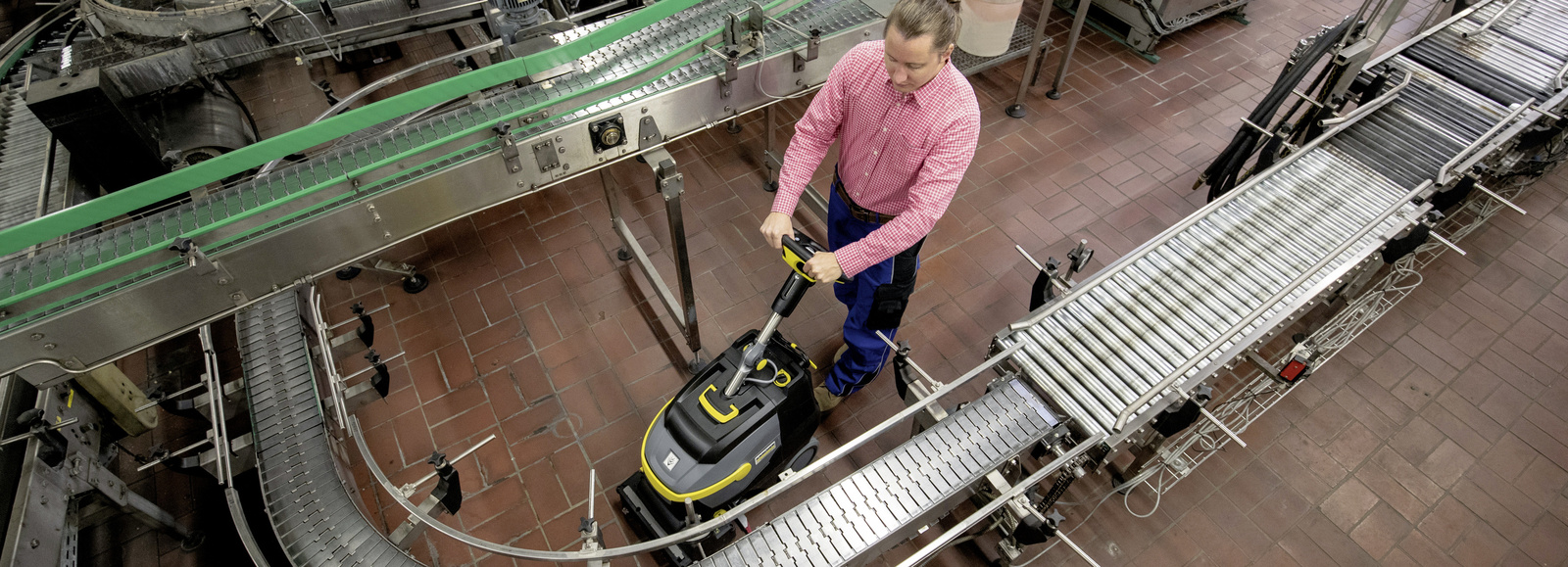
If the belts grind to a halt because they are blocked by dirt or because impurities are interfering with the sensitive electronics, this can have a lasting knock-on effect on production processes. Such complications are costly, which makes it all the more important to implement customised solutions to keep the belts clean – an important area of industrial surface cleaning. Once adapted to the specific circumstances, these solutions help to keep the conveyor belts – and, in turn, production – running smoothly and efficiently.
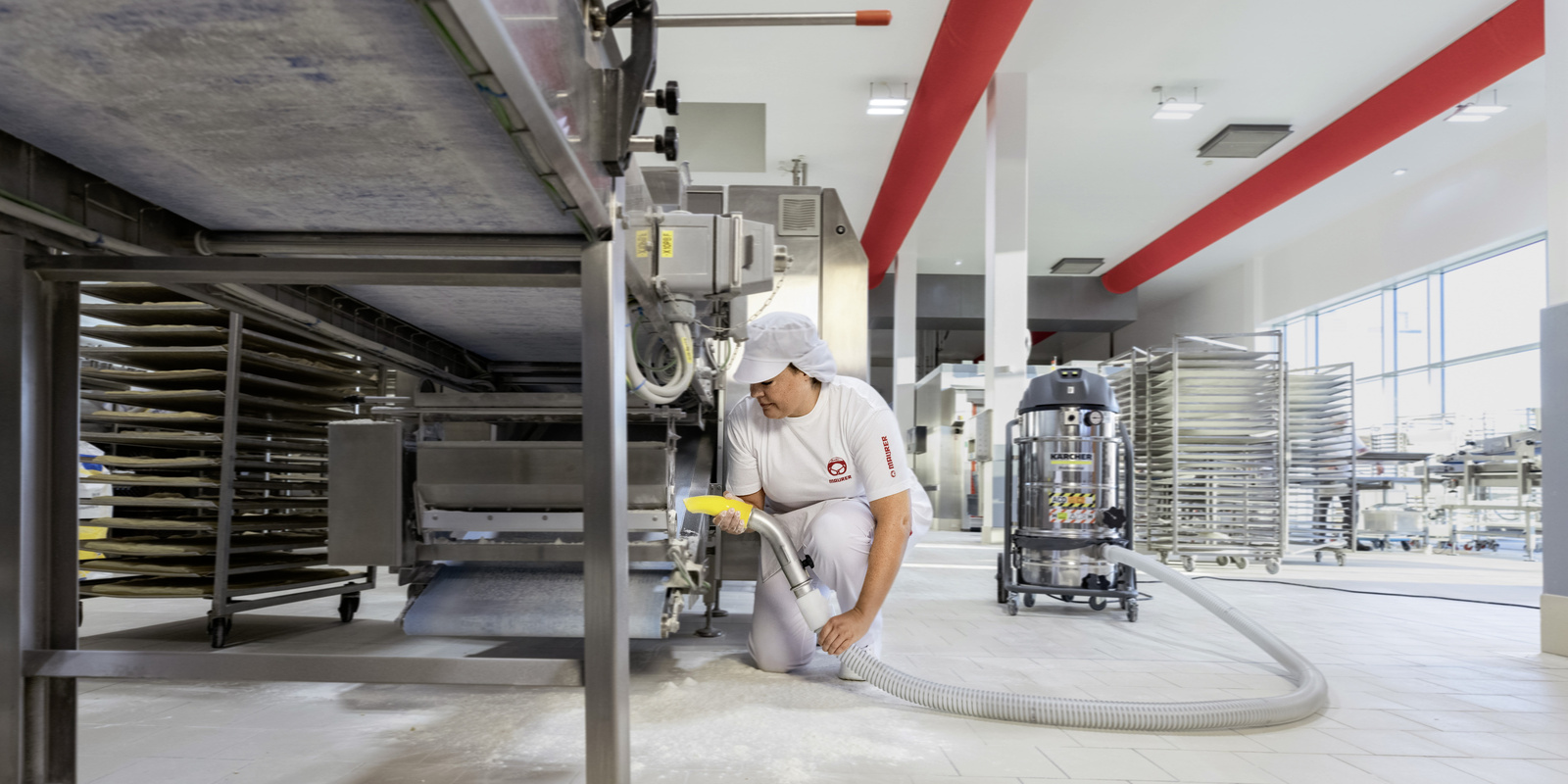
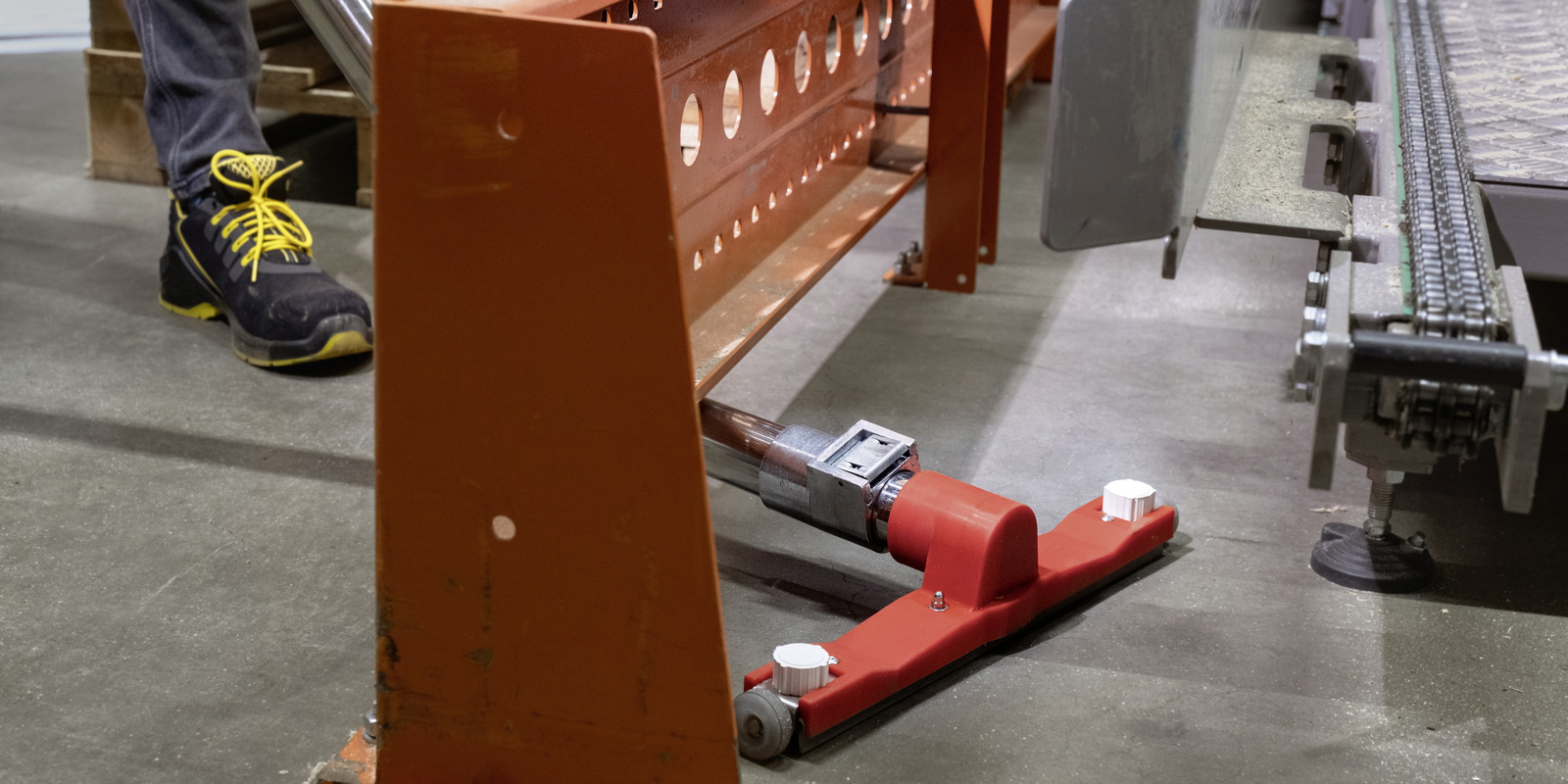
Variable areas of application – different cleaning challenges
Transport belts and conveyor belts are used virtually everywhere within industry. The industry branches in which they are used, the products they carry and the purposes they fulfil are wide-ranging. The types and designs of belt that are used in companies around the world are just as varied.
In industry, a general distinction is made between two types of belt: conveyor belts are robust, often simply constructed and mechanically operated. In many cases, they have no electronics and are used, for example, in the construction and recycling sectors. Transport belts, by contrast, are often networked in industry, embedded deep within the production environment and therefore linked to the surrounding production steps by means of electronics. The latter tend to be more susceptible to faults, not least because of their intricate electronics. This makes it all the more important to implement measures to prevent such faults.
When it comes to the different requirements for maintaining and cleaning transport belts, there are essentially three particularly relevant industrial and economic sectors to differentiate between: the food industry, the automotive/metalworking industries and the logistics sector.
In the food industry, the opportunity for contamination is wide-ranging; from spilt liquids and broken glass to dry residues of baked goods, for example, both on the transport belts themselves and in the immediate vicinity. The focus here is on preventing contamination of the product in order to ensure consumer safety.
In the logistics sector, soiling is generally less varied. The sensitive sensor technology plays a particularly important role here, because this needs to be protected from dirt and, in turn, downtime.
In the automotive and metal processing sectors, transport belts are often impaired by cooling lubricant residues or metal shavings being carried along. Here, the cleanliness of the belts is particularly important for quality assurance and occupational safety.
HACCP
You can't buy trust, yet making a purchase does call for a certain amount of trust – and that's exactly why the HACCP concept was developed. Safety – and therefore also cleanliness and reliable cleaning processes – play a major role in the food industry; high standards should ensure that consumers can enjoy products without any concerns. In light of this, the HACCP concept is an important tool for self-monitoring, which can be used to help identify and analyse potential hazards and bring these under control.
Cleaning in logistics
When it comes to cleaning tasks in transport and logistics, time pressures are a key consideration. After all, the strictly timed processes in goods transport leave windows of time as small as those in the strict timetables of public transport and rail transport. Whether for vehicle cleaning – interior or exterior – or infrastructure maintenance, efficient, carefully considered cleaning technology is required. Specifically, technology that withstands even the harshest of environments.
When it comes to efficiency, customised cleaning processes deliver the best possible results
What all these industries have in common is that the focus is on cleaning in situ – without prior dismantling – in order to keep the effort involved relatively low.
Regular disassembly for cleaning in a separate wash bay brings with it excessive downtime, especially in production environments where high levels of dirt are unavoidable during processing.
In this context, it is also important to differentiate between scheduled cleaning and ad hoc cleaning. Scheduled cleaning, as the term suggests, can be planned for and can therefore be timed to coincide with maintenance shutdowns, for instance. The risk that is prevented or eliminated through scheduled cleaning is calculable.
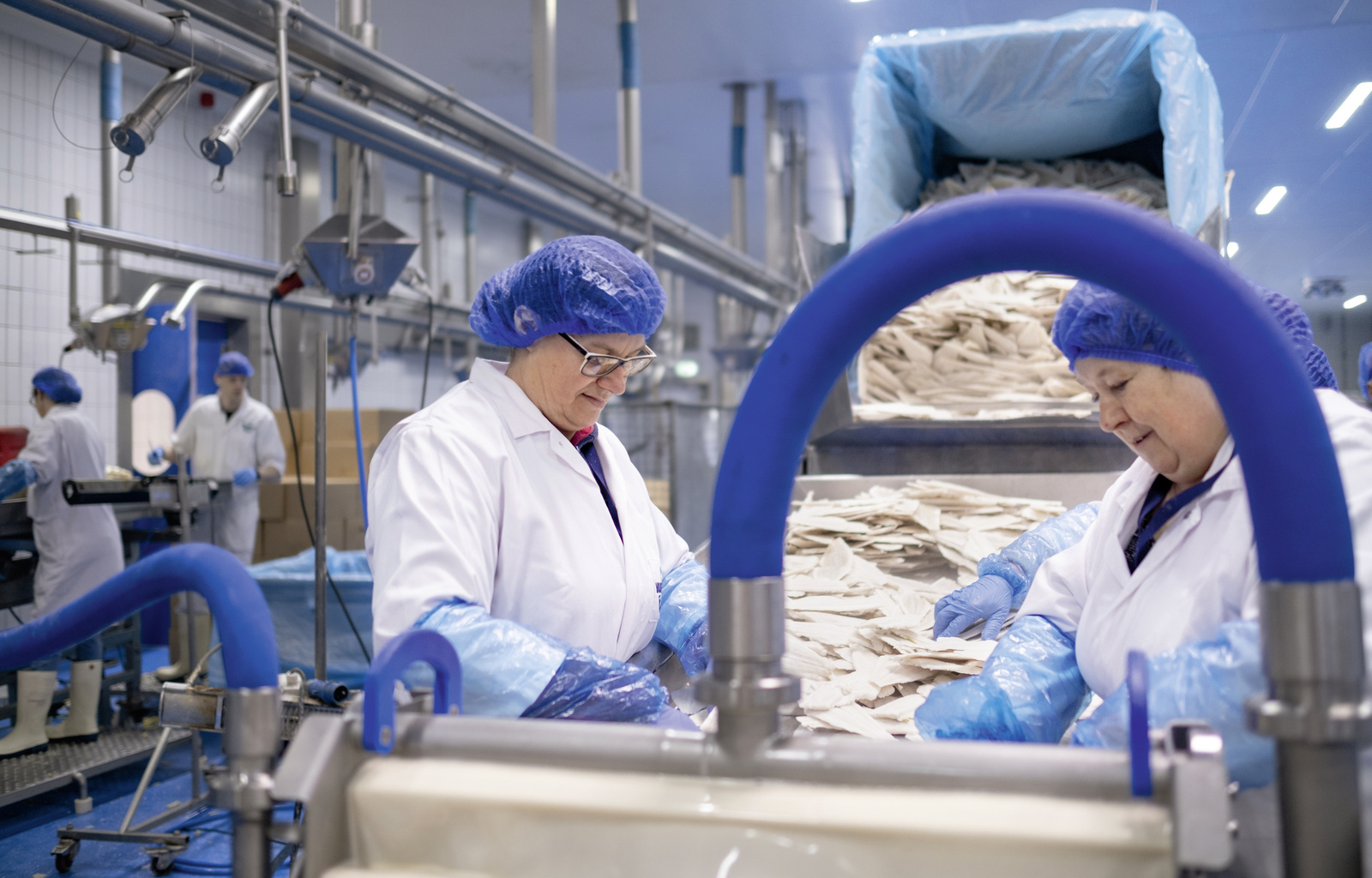
The same cannot be said for ad hoc cleaning: this becomes necessary without forewarning; the impairment caused by the soiling or the associated risk is incalculable. In these scenarios, the response needs to be fast and comprehensive – partly also to prevent the contamination from spreading. The installation of a stationary cleaning system should be considered, especially if the contamination in question occurs regularly – for example, if loose films and labels repeatedly interfere with the sealing mechanism in the wrapping machine. This can have the knock-on effect of further contamination, if parts of the product are escaping from inadequately sealed packaging. If this is the case, using a stationary industrial vacuum can significantly boost efficiency and help to maximise machine availability.
Using automated cleaning machines, which are permanently operational, not only reduces the need for ad hoc cleaning tasks, but also extends the intervals between scheduled cleans, which, in turn, increases productivity. In most cases, stationary extraction systems are incorporated into the design of the production facility. Various extraction lines are laid, running from a central turbine to the individual production lines. This way, the conveyor belt is usually subject to constant extraction – however, a device for manual extraction, powered by the stationary system, is also an option. Stationary extraction systems are particularly suitable for companies with high levels of dust, such as the food, pharmaceutical and metal industries.
Keeping everything moving: clean conveyor belts mean smooth processes
Beyond stationary systems, there are numerous other cleaning solutions that are suitable for use on and around the conveyor belt. To determine which solution is the right one in each case, the specific production environment and cleaning requirements must be taken into account.
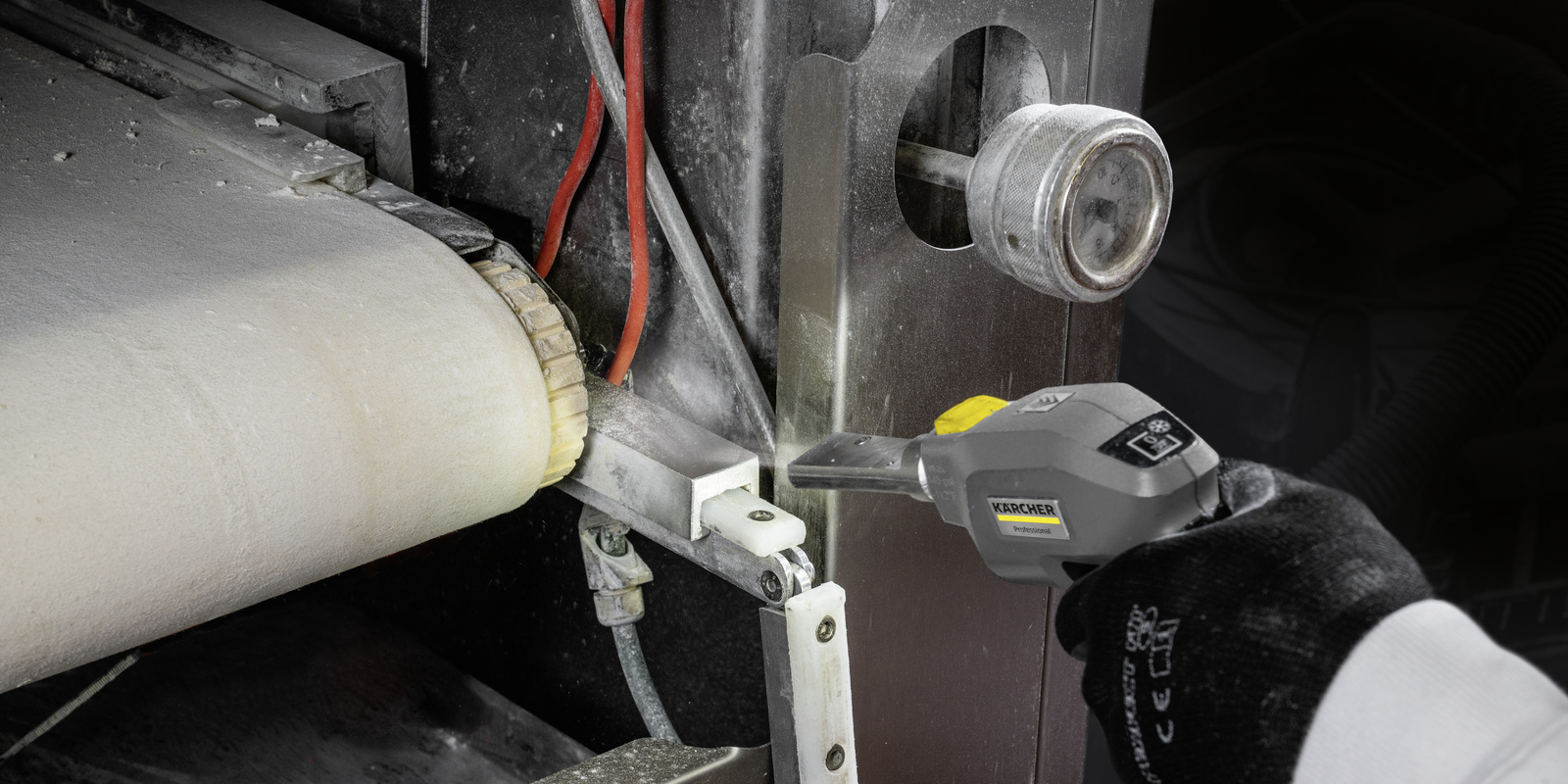
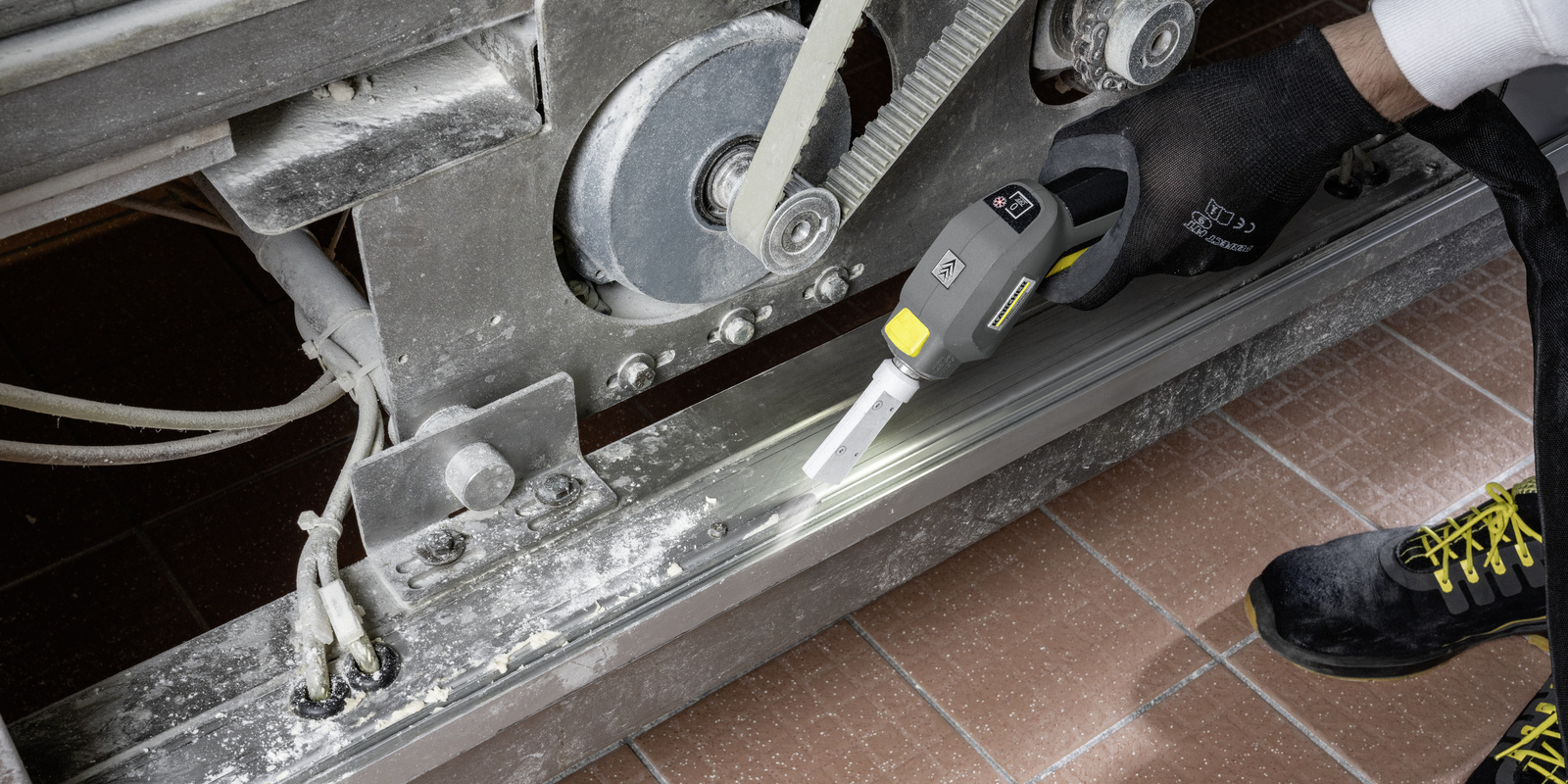
Dry ice is an effective tool for cleaning the belts themselves. With this method, the surface being cleaned is hit by dry ice pellets – at a temperature of -79 °C – travelling at speeds of over 150 m/s. The cold and the impact of the accelerated pellets loosen even ingrained dirt. A particular advantage of this method is that it is barely abrasive; in addition, no blasting agent, dirty water or moisture is left behind after cleaning. Dry ice is a very flexible option when it comes to cleaning transport belts. Depending on the nature of the soiling and the sector in question, the dry ice method can be used on a moving or stationary belt, with or without product. If the belt is heavily soiled, it may be advisable to partially or fully disassemble it. After cleaning with dry ice, the residue of loosened dirt has to be removed. The procedure for doing so varies depending on the nature of the residues and the available space. If the loosened dirt is dry and crumbly or dusty, it is picked up from the floor using a sweeper or vacuum cleaner.
Since the vacuum cleaner – unlike the sweeper – can work in three dimensions, it can also be used to remove dirt residues from gearboxes, trays and elevations. If the dirt is damp or greasy, a scrubber dryer is used – provided the surface is smooth, accessible and secured by means of industrial fastenings. If this is not the case, it is vacuumed or rinsed with a jet of water. In general, dry ice cleaning tends to be used for small areas and for very sticky or highly adhesive soiling. Dry ice can be a particularly useful method if residues have been exposed to a high degree of physical stress (e.g. by means of a freezing or baking process) and therefore adhere particularly strongly. Dry ice cleaning also presents a solution for areas where water and detergents cannot be used due to the potential for product contamination or damage to electronics. This method is applied in numerous sectors, such as the pharmaceutical and automotive industries.
Dry ice blasting in car workshops
Dry ice blasting is an effective particle spray process for removing stubborn dirt coatings from a range of supporting materials. Dry ice cleaning has also proven its worth in automotive workshops or reconditioning shops, especially on complex and delicate surfaces – from upholstery cleaning in cars to cleaning engine compartments and restoration work on classic cars. The main advantage of this technology is that it cleans without leaving any residues, such as waste water, chemicals or spray agent residues.
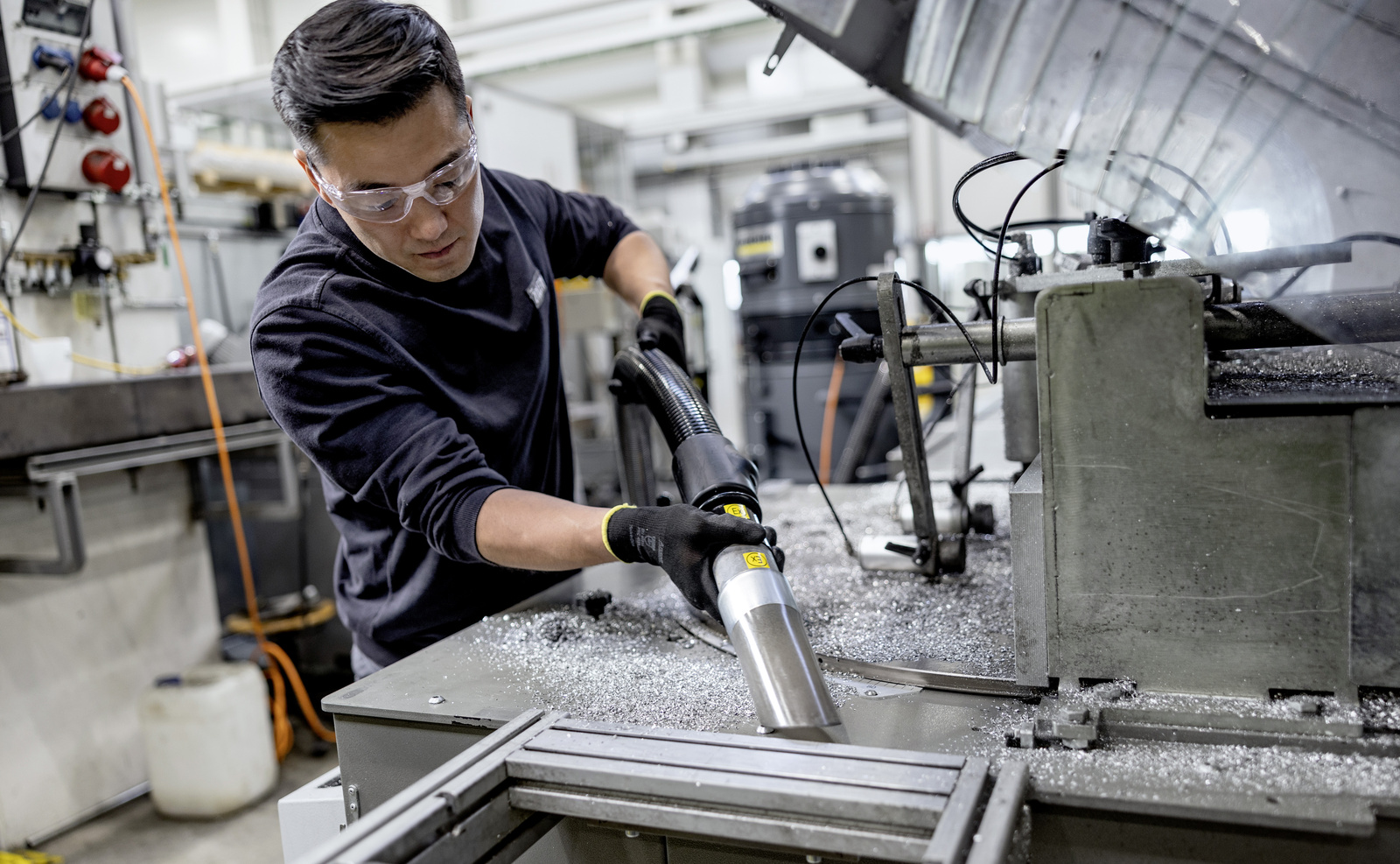
Transport belts, or specifically their surfaces, are often cleaned by hand as well, especially in the food industry. The exact procedure here depends on the individual circumstances – the belt often runs at a slow speed and the dirt is wiped off manually with a cloth. Disposable wipes are generally used for this purpose. In addition to this, any dry residue on the belts can be removed by extraction. A permanently installed extraction unit with an integrated mobile handheld vacuum is often used.
In the automotive sector, for example, the extraction of metal shavings represents an integral part of the cleaning routine. Spot cleaning of acute small stains is also a key cleaning step; extensive cleaning of the belt is rarely necessary.
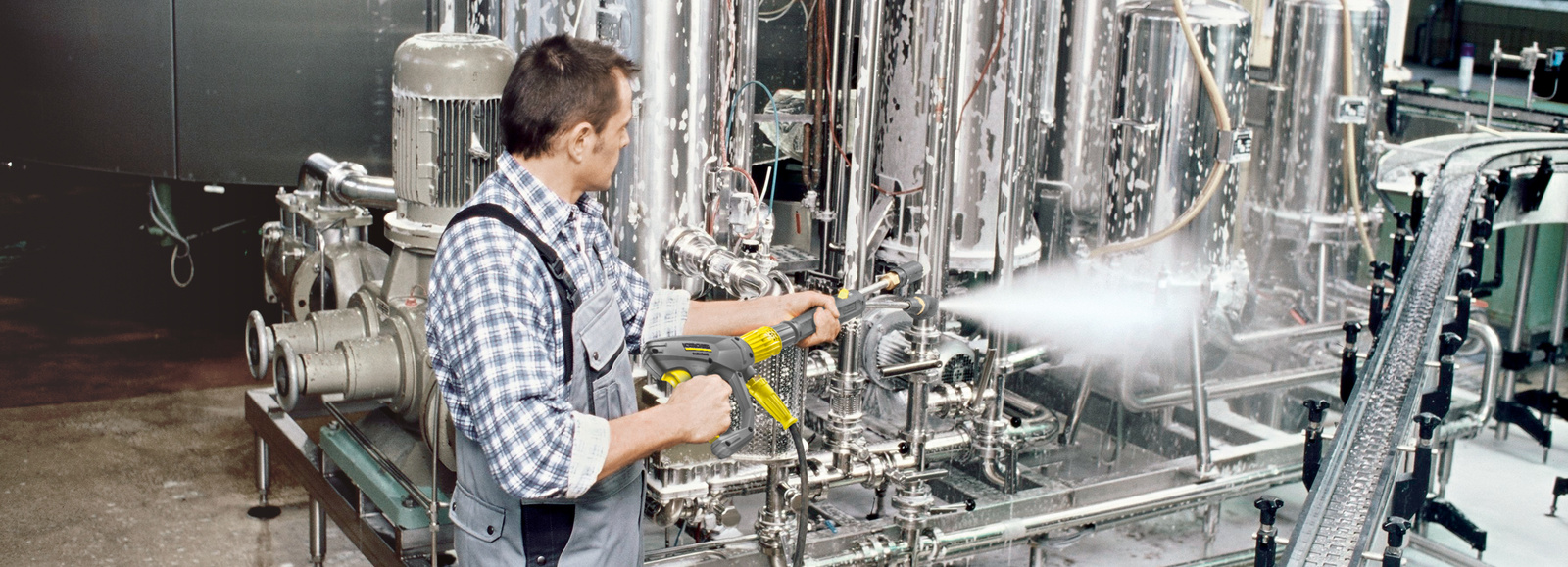
High-pressure cleaning can also be used for cleaning conveyor belts. However, this is not always possible or advisable for every sector. Specifically, belts that move primary products, ores, building materials and wood are often cleaned using high pressure. Cleaning is carried out at regular intervals that vary depending on the product and the level of soiling. Personal protective equipment is required, since high pressure cleaning generally causes spray back.
When cleaning, a basic distinction must be made between dry production areas and areas where wet cleaning is possible.
In the beverage industry, for example, wet cleaning is usually possible, as there are drains everywhere and the filling systems are usually closed. Meat processing plants such as butchers, cutting plants and abattoirs must always be thoroughly wet-cleaned.
In dry production areas, particular care must be taken to ensure that the area is dry again after cleaning, or at most only slightly damp.
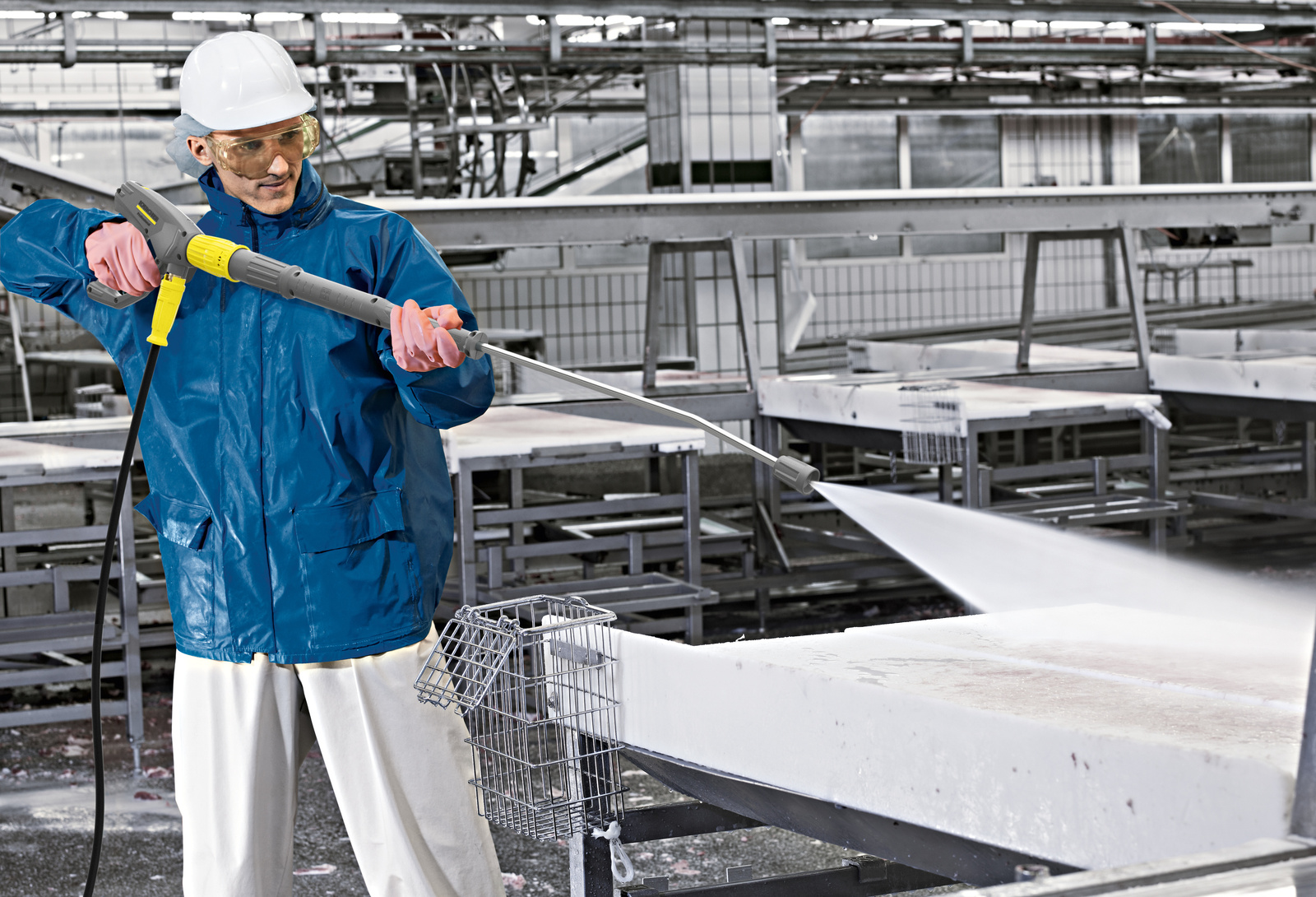
Cleaning in meat processing
In food processing companies such as butcher's shops, extra care and attention should be given to cleaning and disinfection tasks. This applies to work surfaces, tools and machines, as well as floors in production and storage areas and cold storage rooms – because any spread of germs would have harmful consequences. For added convenience, high-pressure cleaners in particular can be used to complete numerous tasks efficiently.
A clean belt alone is not enough
It is not just the belt itself that needs cleaning, but also the floor area beneath it. This represents a major challenge, because the area under the belts is usually difficult to access. Cleaning this floor area is not usually a critical factor in the planning stage, and is therefore often overlooked in the design.
If the environment allows, a high-pressure cleaner combined with a surface cleaner is often a good choice. If, on the other hand, high-pressure cleaning is not possible, as is the case in the automotive sector, for example, cleaning with a scrubber dryer is an option, provided the area under the transport belt is easily accessible and not obstructed. It is important to choose the right accessories – in the automotive industry, for example, attention must be paid to the oil resistance of the equipment used.
Cleaning floor coverings
Whether carpeting in a hotel corridor, cement screed in a production hall or wooden flooring in a school building, there are countless floor coverings that are suitable for different loads and ensure safety through properties such as anti-slip design or studs. Cleaning floor coverings is important in some areas to ensure hygiene, while in other areas the focus is on appearance. In either case, well-maintained floor coverings have a longer service life, meaning that they need to be replaced less frequently. With regular maintenance cleaning, you can even postpone the need for a time-consuming deep clean.
In beverage production, on the other hand, where glass breakage and liquid spillages are frequent occurrences, the appropriate vacuum cleaner should be chosen. For accidents involving smaller quantities of soiling, the mixture of shards of glass and product can be picked up with a wet and dry vacuum cleaner. It is important that the vacuum cleaner selected meets the specifications of the relevant food sector. If large quantities of broken glass need to be cleared, for example in glass production, industrial vacuum cleaners are usually used, since these are capable of collecting heavy vacuumed material in a sturdy container and can be emptied easily.
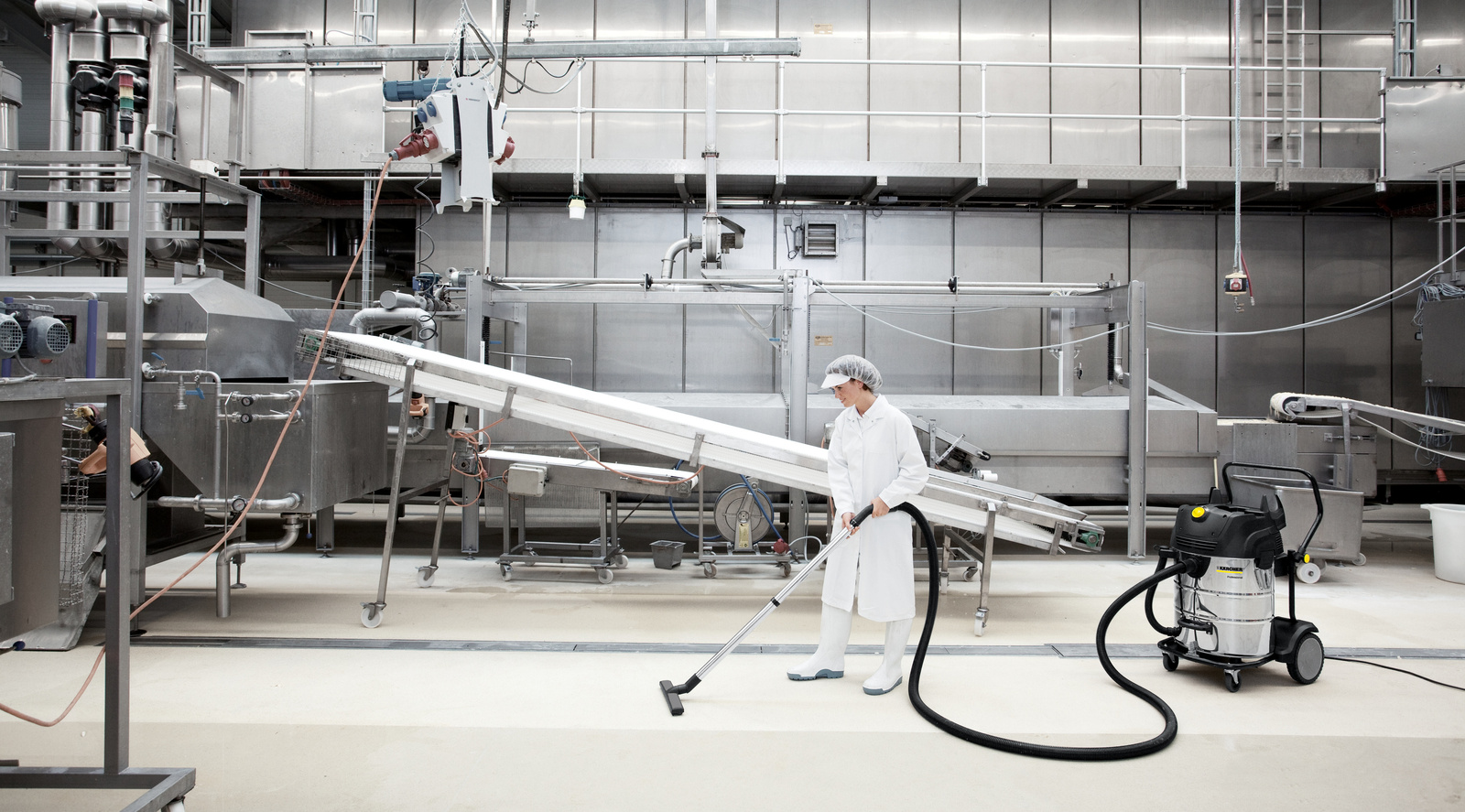
Suitable products for your area of application
Find a wide range of technology at lightning speed – with the Kärcher Professional product finder
In no time at all, we'll show you the exact Kärcher Professional machine that best suits your specific cleaning task.