Cleaning in metal processing
Metal processing is often highly automated, with various machining steps, such as sawing, turning, drilling and milling, being combined with the application of coatings where necessary. The often complex components call for a well-coordinated process in order to achieve the required level of precision and product quality. Efficiency in processes is also important in order to stay within budget and to produce profitably. With this in mind, cleaning is an important factor, since it removes many potential stumbling blocks on the way to the product.
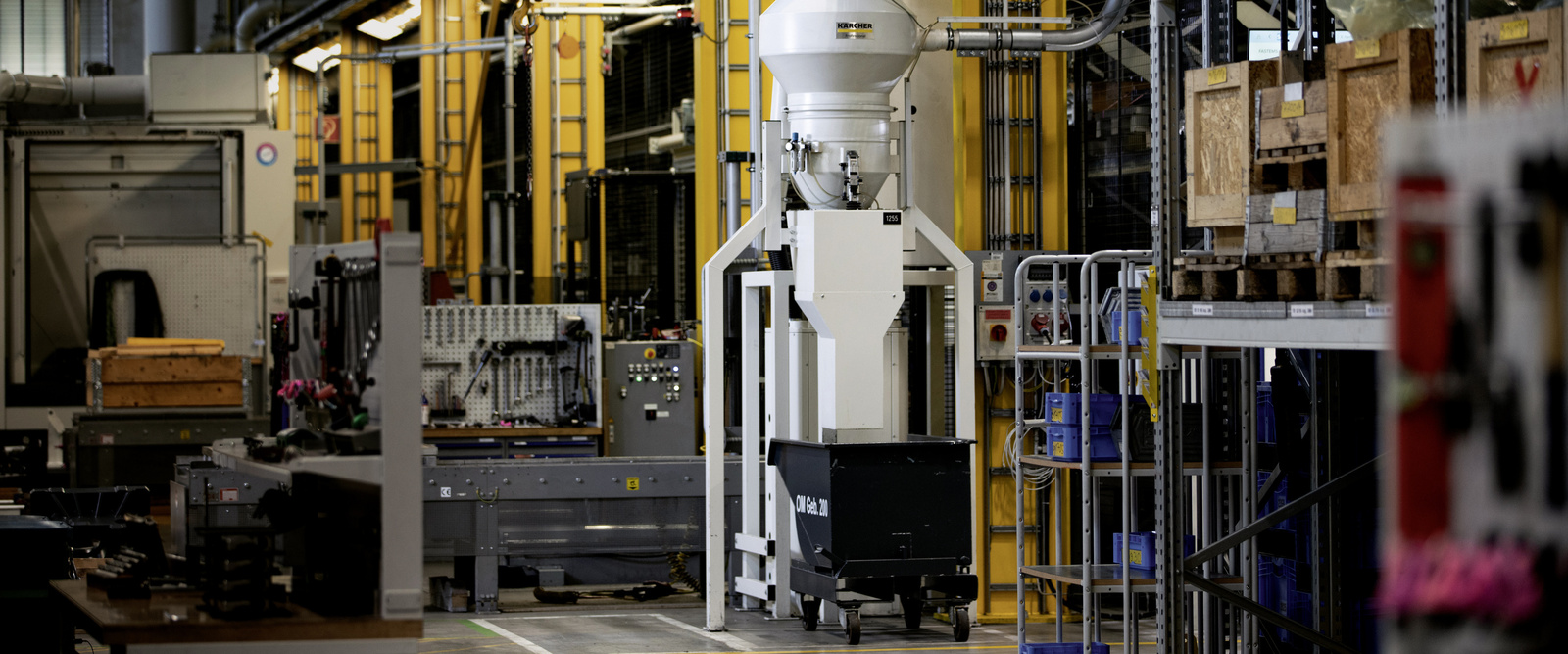
Cleaning in the iron foundry keeps spanners out of the works
For metal casting, blanks are cast in sand moulds and then have to be cleaned ahead of further processing. To that end, they are unpacked, shaken free and degreased using stationary high-pressure units before being coated for transport to the customer, for example. In the manufacturing process itself, dust and sand represent the biggest challenges, because they spread everywhere. Stationary extraction systems integrated in the process, sweepers for cleaning floors and industrial vacuums for elevated areas help to keep this problem in check. This improves overall product quality, because it prevents sand particles from causing scratches or other damage. Occupational safety is also increased, since having dust everywhere puts a great strain on employees.
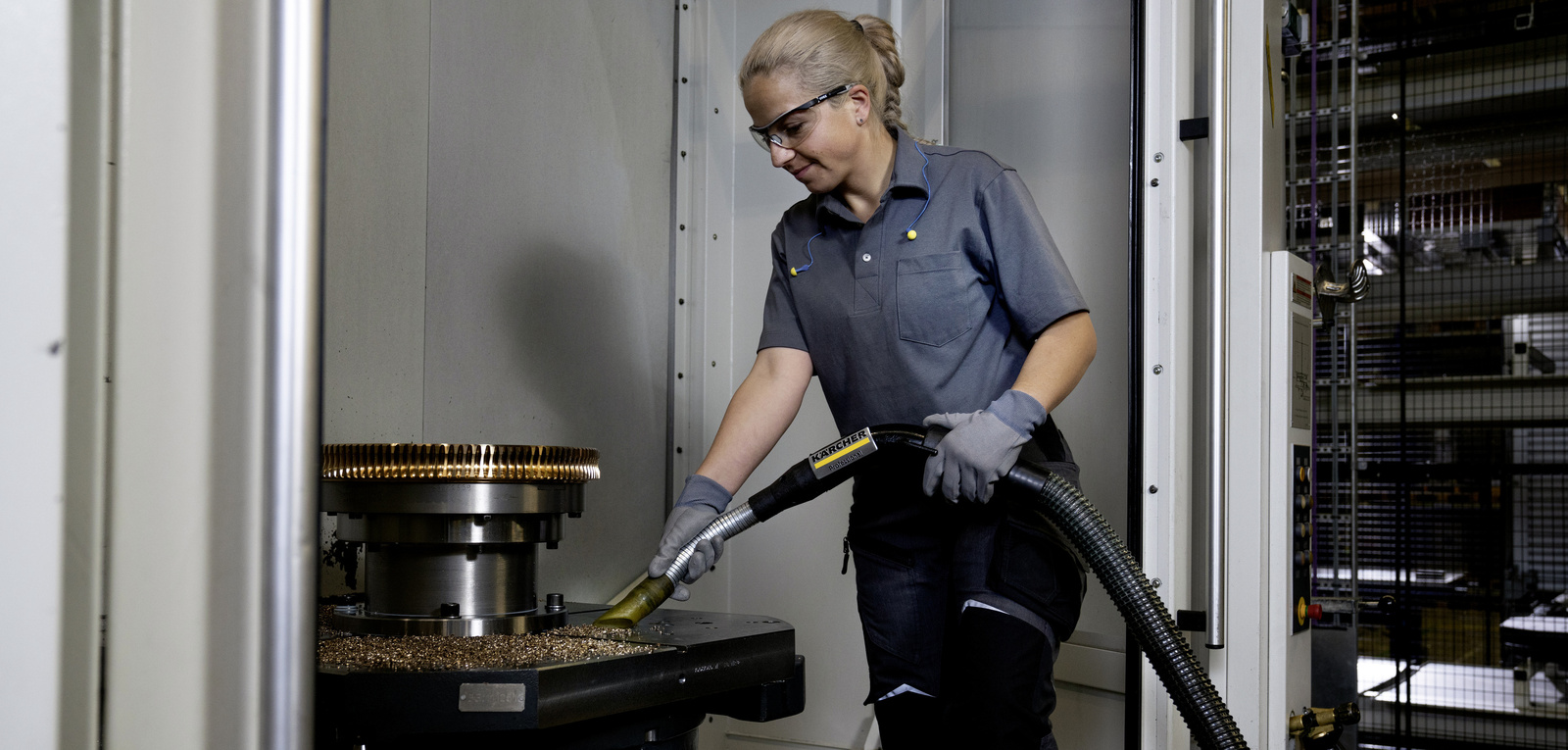
From blank to component with efficiency: cleaning in sheet metal processing
In the production of metal components, the aim is to meet customer specifications with precision, achieve a high yield of faultless parts and establish efficient, safe processes. To keep the press shop clean of punching residues, for example, stationary extraction systems with the necessary pipework or industrial vacuums can be installed as fixed equipment in the workplace. If parts are transported from one station to the next by robot, the gripping tools should be cleaned with a dry ice blaster whenever necessary. Depending on their size, the components themselves can also be cleaned with a dry ice blaster or at a wash bay before they are dispatched.
Protecting investments by keeping machinery and machining centres clean
In order to maintain the value of the infrastructure and to protect investments for the long term, the machining process must be accompanied by cleaning with industrial vacuums. If a cooling lubricant change and major service are due, the machining centres are partially dismantled and cleaned thoroughly using high pressure and detergents, etc. This also ensures machining remains precise, while the new cooling lubricant reduces the health risks for employees.
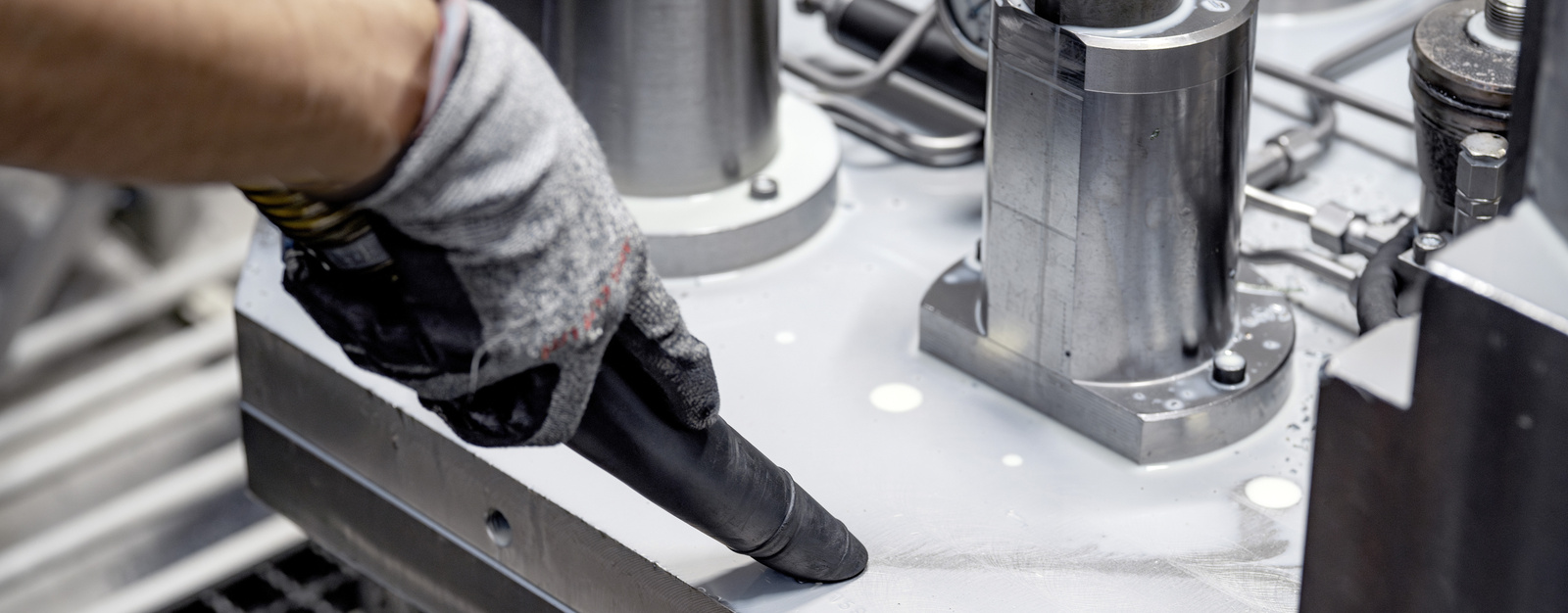